Important Items in Vibration Diagnostics
1. 기계관리를 위한 계장화 (Instrumentation for Machinery Management)
2. 냉각탑 Fan의 큰 고장 (Catastrophic Failure of a Cooling Tower Fan)
4. 진동 벡터 감시의 중요성 (The Importance of Vibration Vector Monitoring)
5. 축 중심선 자료 감시의 중요성 (The Importance of Monitoring Shaft Centerline Data)
6. 과도상태 자료분석의 중요성 (The Importance of Transient Data Analysis)
1. 기계 관리를 위한 계장화 (Instrumentation for Machinery Management)
1.1 槪要 (Introduction)
Australia의 Incitec 회사에서는 예지정비의 성공적인 도입으로 정비 비용 절감 및 회전체의 수명 연장에 중요한 역할을 하였다. 현재 Incitec 회사에서는 다음과 같이 중요한 왕복동 압축기에 예지정비 기법을 확대, 적용하였다.
Incitec 회사는 암모니아, 화학요소 그리고 화학비료 공장으로 구성되어 있다. 화학요소 공장은 공정에 중요한 두 대의 왕복동 압축기를 가지고 있으며, 2대중 1대 정지시 공장의 생산율이 50%로 감소된다. Incitec 회사는 지속적인 개선책의 일환으로 압축기에 설치된 원래의 “오동작” 진동 스위치를 개선하기로 결정하였다.
2대의 압축기는 기본적으로 동일하고, 2단의 암모니아, 5단의 CO2로 구성되어 있으며 6대의 크랭크 샤프트로 운동하고 있다 (4번째 및 5번째 단은 복합적임. 그림 1-1 참조).
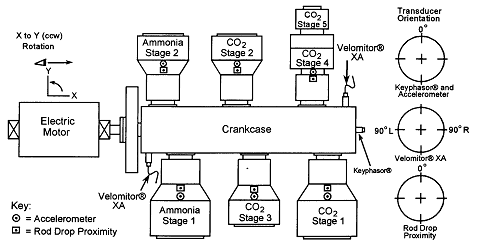
그림 1-1 변환기의 위치 및 회전방향이 표시된 전체 기기 배치도
1.2 Incitec 회사의 要求事項 (Incitec’s Requirements)
Incitec 회사는 중요한 왕복동 압축기를 위해 기존의 예지정비 프로그램에 부합하는 감시와 진단설비 및 기기 관리를 위해 구체적인 자료가 필요했다. 또한 계획정비 기간중 시행한 정비작업이 기계상태를 주관적인 판단보다는 객관적인 판단에 근거한 것인지를 확인하기를 원했다.
감시 및 진단설비는 다음과 같은 기능을 수행할 수 있어야 한다.
• 주 베어링 및 끝단 베어링의 마멸과 같은 크랭크 샤프트와 관련한 결함의 확인.
• 압축기 각단의 감시, 피스톤 이완의 인지 및 갑작스런 피스톤 손상으로부터 보호.
• 각 압축기 단위 Rider Ring 마멸측정.
• 58개의 입구 및 출구측 밸브 감시.
더욱이 정비 작업자는 이 시스템이 특히 실린더 헤드 주위의 기계 정비에 간섭이 되지 않을 것을 강력히 주장하였다.
Incitec 회사는 1995년초 압축기 1대를 개조하기로 결정했으며 개조 작업이 성공할 경우 1996 년에 추가로 2번째 압축기를 개조할 예정이었다.
1.3 解決方案 (Solution)
Incitec 회사는 벤틀리 네바다 회사에 이러한 목적에 부합하는 시스템을 추천할 것을 질의하였으며, 1994년말에서 1995년초까지 벤틀리 네바다 기술진 및 판매진과 발전소 정비 작업자가 공동으로 시스템 설치 및 설계에 대해 면밀히 연구하였다.
① 속도계 XA Sensor를 이용한 크랭크 샤프트 결함 확인
압축기 샤프트 및 베어링 결함들은 수평면에서 측정한 크랭크 케이스 진동값으로 확인된다. Incitec 회사는 각 크랭크 케이스 끝단에 XA(Extended Application) Sensor를 하나씩 설치하였다. 둘 다 원래 설치된 오기능 검출기에 인접하여 크랭크 케이스 중심선에 수평으로 설치하였다.
XA Sensor의 4.5 ㎐~2 kHz의 주파수 응답은 330 rpm으로 회전하는 크랭크 샤프트에서 발생하는 진동측정에 적합하다. XA Sensor는 설치하기 쉽고 어떠한 기후 조건에도 견딜 수 있는 압전 속도 Sensor이다.
XA Sensor로부터의 신호는 벤틀리 네바다 3300/55 Dual Velocity Monitor에 의해 처리된다. 3300 감시설비는 벤틀리 네바다의 표준장비로서 현장에서 프로그램이 가능하고 많은 안전성을 가지고 있다. 크랭크 샤프트 진동을 연속 감시하는 3300/55 설비는 경보음, 기기보호를 위한 계전기 및 진단장비 연결용 버퍼 출력단자들이 있다.
② 가속도계로 각 압축기 단을 감시.
각 단락에서의 문제점을 확인할 수 있는 진동 정보는 6개의 가속도계에 의해 얻어진다. 가속도계는 Crossband Slipper Guides에 실린더를 연결하는 Transition Section에 수직으로 설치되었다 (그림 1-2 참조).
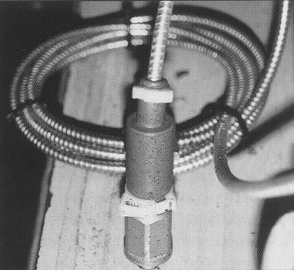
그림 1-2 수직으로 설치된 가속도계
Incitec 회사는 광대역 주파수 응답(10 ㎐~20 kHz)을 가져야 피스톤 로드 이완 및 노킹과 관련한 충격에 의해 발생되는 고주파 신호를 완전히 측정할 수 있기 때문에 벤틀리 네바다 23732 가속도계를 선정하였다. 4번째, 5번째 복합단 CO2 실린더는 1개의 가속도계로 감시되기 때문에 7개의 단을 감시하는데 단지 6개의 가속도계만 필요하였다. 가속도계는 3대의 3300/25 Dual Acceleration Monitor에 연결되었다.
③ 로드 낙하측정과 Rider Ring 마멸 확인
로드 낙하측정은 Rider Ring을 가지고 있는 모든단(5번째, CO2단은 제외)에서 이루어진다. 각각의 실린더에 11 ㎜ Proximity Probe가 Crosshead Oil Wiper Stuffing Box 상에 수직으로 설치되어 있어 여기서 피스톤 로드의 상대 위치를 측정한다. Keyphasor 변환기는 크랭크 샤프트의 Notch를 감시한다. 로드 낙하 및 Keyphasor 변환기로부터의 신호는 로드 낙하 감시기에 의해 처리된다.
로드 낙하 변환기는 고정된 탐촉자 및 움직이는 피스톤 로드 사이의 거리를 측정하는 Proximity Probe이다 (그림 1-3 참조). 이 측정거리는 Rider Ring의 마멸에 따라 변한다. 로드낙하 감시기는 탐촉자와 피스톤 로드의 거리라기 보다는 Rider Ring 의 실제 마멸량을 나타낸다. Keyphasor 신호는 로드낙하 측정을 위한 피스톤 행정중 가장 좋은 지점을 확인하는데 사용한다.
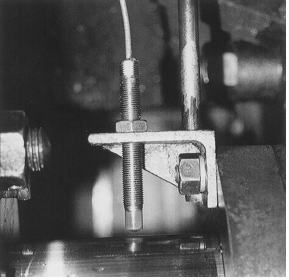
그림 1-3 로드낙하 탐촉자 설치
④ 온도측정을 통한 밸브상태 감시
밸브상태는 58개의 각각의 흡입측과 배기측 밸브 주위의 가스 온도에 의해 지시된다. 각 밸브 주위에 돌출된 열전대는 가스 온도를 측정한다. 각각의 열전대는 스테인레스 스틸 나사 중심부 구멍을 통해 설치되어 있다. 나사 및 열전대 뭉치는 각각 밸브 커버의 잭 나사 위치에 설치되어 있다 (그림 1-4 참조).
58개의 열전대는 2대의 왕복동 압축기 밸브 온도 감시기(3300/75)에 연결되어 있다. 각각의 감시기는 열전대 또는 열저항 온도계 (RTD)로부터 신호를 32개까지 감시할 수 있다. 각각의 열전대는 모듈변환기(TIM : Transducer Interface Module)에 부착되어 있다. 열전대는 32개의 모듈변환기까지 5심 케이블을 통해 연결되어 있으며, 온도 감시기는 계속해서 모듈 변환기를 조사하고 있는데, 32개의 모듈 변환기 조사하는데 약 5초 걸린다.
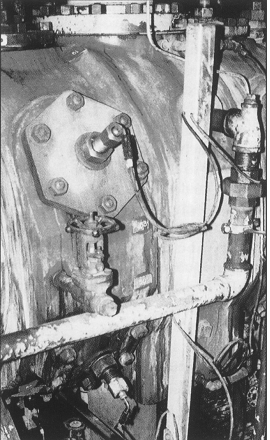
그림 1-4 밸브 커버 및 잭나사에 설치된 열전대 모습
1.4 補修 容易性 (Maintainability)
Incitec 회사는 압축기 정비에 간섭을 일으키지 않는 왕복동 압축기 감시설비를 원했다. 조심해서 설치한 결과 XA 속도 감시기, 23732 가속도계 및 로드 낙하 탐촉자는 압축기를 유지 정비하는데 간섭을 주지 않았다. 그러나 58개의 열전대는 새로운 설치방법이 필요했다. 각각의 열전도계는 Quick-Release 방식으로 연결되도록 하여 정비작업이 필요할 때 재빨리 연결을 해제할 수 있었다.
실린더 측면을 따라 신호선을 보내는 스틸 덕트는 접는 방식으로 고안되었다. 대규모 정비가 필요할 때 열전대 연결을 신속하게 해제하여 같이 묶어서 스틸 덕트로 접어 바닥 그레이팅 아래로 내려놓을 수 있다. 이 새로운 방법은 정비시 짧은 시간 내에 실린더로부터 모든 계측장비를 제거하기 쉬우며, 기계 정비는 제약없이 접근 가능하다.
1.5 온라인 診斷 시스템 (Online Diagnostic System)
Incitec 회사는 벤틀리 네바다 TDM 2(Transient Data Manager) 온라인 진단 시스템에 의해 중요한 압축기를 성공적으로 관리하고 있다. TDM 2는 정상상태 및 과도상태 경보음이 발생했을 때 또한 미리 설정된 주기에 따라 자동적으로 자료를 수집하고 저장한다. TDM 2 는 신속하고 정확하게 기계진단 결과를 여러 가지 형태로 그래프를 그린다. Incitec 회사는 진동 자료를 추적하고 기계의 경보음이 발생했을 때 자료 수집 능력에 따라 왕복동 기계 관리가 성공적으로 수행될 것으로 확신했다.
따라서 Incitec 회사는 벤틀리 네바다의 DDI(Dynamic Data Interface) 및 SDI (Serial Data Interface)를 포함한 3300 감시설비를 설치하였다. DDI는 진동경향의 편집 및 경보음이 발생하였을 때 자료 수집하는 TDM 2와 감시설비 간의 자료를 전송한다. SDI는 감시설비 자료를 발전소 분배제어계통(Distributed Control System)에 보내고 따라서 운전원은 진동 및 온도자료를 감시한다.
1.6 機械管理를 위한 計裝化 (Instrumented for Machinery Management)
Incitec의 새로운 감시설비는 현재 화학요소 발전소 운전관리에 중요한 도구이다. 감시설비는 큰 사고로부터 기계를 보호한다. TDM 2 온라인 진단설비는 기계의 수명 연장, 정비기간의 단축 및 비용절감 등으로 기계를 관리하는데 도움을 준다. Incitec 회사는 현재 화학요소 공장의 다른 중요한 왕복동 압축기에도 개조를 계획하고 있다.
2. 냉각탑 팬의 큰 고장 (Catastrophic Failure of a Cooling Tower Fan)
Titus 발전소는 3개의 석탄 연소 증기발생 유니트가 있으며, 총 240 ㎿의 전력을 생산해 내는데 최근에 냉각탑 Fan이 크게 파손되어 그들의 수동식 휴대용 진동 자료 수집 프로그램의 신뢰성을 제고하게 되었다.
Titus 발전소는 연속적이며 휴대용 자료 수집기인 Bently Nevada의 Snapshot 시스템을 사용하고 있으며 하나의 증기터빈에는 연속적인 3300 감시 시스템이 설치되어 있고, 다른 2개의 유니트에도 3300 시스템을 곧 설치할 계획을 갖고 있었다. Titus 발전소측은 1980년대 중반부터 다른 중요기계에는 수동으로 자료를 수집하는 휴대용 Snapshot 시스템을 사용해 왔다. Titus 발전소는 Snapshot의 기능에 만족해 하지만 수동 자료 수집에 대한 한계를 잘 알고 있었다. 자료 양은 훈련된 인원의 활용성 때문에 제한을 받게 되고, 자료의 질은 자료 수집기를 작동하는 기술자들의 숙련도에 달려 있다.
2.1 冷却塔 (The Cooling Tower)
유인 통풍 냉각탑은 기계적인 주요 문제점을 안고 있었다. 냉각탑은 대형 쌍곡선 형 Shell을 가진 콘크리트 구조물로 높이가 45m 이다. Shell 내부에 8개의 전동기 구동 Fan이 있어 탑을 통해 공기를 보내준다. 각 Fan과 기어박스는 Fan Stack 내부에 위치해 있고 Stack 외부에 전동기가 장착되어 있으며, 길고 수평인 구동축은 각 Fan Stack을 지나 감속기 기어와 직각으로 물려있는 각각의 전동기와 연결되어 있고, 각 Fan은 기어 박스로부터 수직으로 나와있는 축에 직접 연결되어 있다. Fan 전동기는 Snapshot을 사용해서 한 달에 한 번씩 운전상태를 측정하고 있다. 각각의 Fan Stack 내부에 위치해 있는 Fan과 기어 감속기는 점검자들이 접근할 수 없는 위치이므로 운전상태를 수집할 수 없었다.
냉각탑의 특성상 휴대용 자료 수집기를 가지고 측정하는데 많은 어려움을 가지고 있다. Fan 전동기의 자료를 수집할 때는 방진마스크를 쓰고 냉각탑 구조물로 들어가야 하고 냉각 과정중의 증발로 인해 생기는 짙은 안개 때문에 때때로 1m 앞도 분간할 수 없게 된다. 동절기에는 Fan Stack과 Shell 사이의 통로에 얼음이 생기기도 하여 Titus 발전소의 책임자는 안전을 위해 Tower 상태에 따라 정기적으로 계획된 수동 자료 수집을 종종 며칠동안 연기시키기도 했다. 또한 인력 부족으로 인하여 더 많은 시간이 연기되기도 하였다.
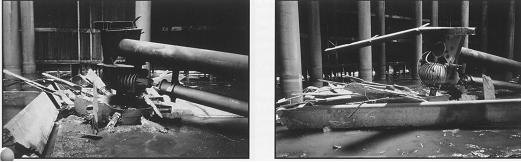
그림 1-5 파괴된 냉각탑 Fan과 기어 감속기
Titus 발전소는 Fan을 고진동으로부터 보호하기 위하여 기계적 진동 스위치를 사용했다. 스위치는 전동기 가까이에 설치되어 있고, 자동정지를 위해 제어 회로에 전기적으로 연결되어 있다. 발전소 담당자들은 진동 스위치 사용에 2가지의 문제점을 인식했다. 하나는 스위치가 감속기와 Fan을 직접 감시할 수 있는 위치에 없다는 것이다. 스위치는 각 Fan 전동기에 설치되어 있고, 각 기어 감속기와 Fan으로부터 몇 미터 떨어져 있다. 이러한 설치 위치 때문에 Fan의 실질적인 운전상태에 따른 스위치의 작동이 불가능하여 큰 사고를 일으키기도 한다. 또 다른 하나는 스위치의 신뢰성이다. 냉각탑의 주변 환경이 나쁠 때는 스위치의 내부 메커니즘에 손상을 주어 진동 스위치 작동에 대한 Fan의 정지가 불가능하게 된다. 또한 진동 감지 요소가 정확히 동작하는지를 확인할 수 있는 방법이 없다.
최근 몇 달동안 볼트의 풀림, 전동기 베어링의 문제, 분할 Hub와 축의 휨 현상 등으로 인해 발생된 진동의 증가를 적어도 3번 정도 감지하지 못했다. 이러한 문제점들로 인해 중대한 사고를 방지하기 위해 발전소 구성원들은 냉각탑의 휴대용 자료 수집 프로그램에 추가 측정을 보완했다.
1992년 1월 발전소의 냉각탑 외부에서 일하고 있던 작업자들이 큰 소음을 듣고 운전부서에 연락하였다. 운전원들이 확인한 결과 냉각탑 Fan과 전동기, 기어박스가 지지대로부터 완전히 떨어져 나가있는 상태였고 Fan 조립체 전체가 Tower Deck 아래의 20m 웅덩이로 떨어져 있었다. 전동기를 지지하던 통로부분은 떨어져 나갔고, Gaping Hole만 남겨진 상태였다.
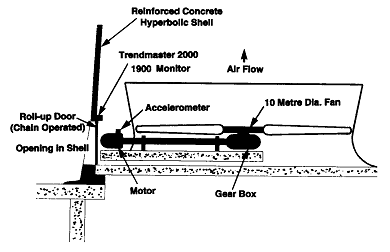
그림 1-6 Fan이 설치된 냉각탑의 단면도
2.2 問題點 分析 (Problem Analysis)
조사자들은 하나의 Fan Blade가 완전히 떨어져나가 심한 불평형 상태가 되었을 때 손상이 시작되었다고 판단했다. Fan의 진동 스위치가 Fan을 정지시키지 못했고 불평형 힘이 결국에는 냉각탑 전체를 파괴시켜 버린 것이다. 조사결과 스위치가 동작하지 못한 것은 케이싱내로 들어간 습기에 의한 부식 때문이었다. 이로 인해 진동 스위치가 불평형된 Fan에 의한 진동에 대응하지 못했다.
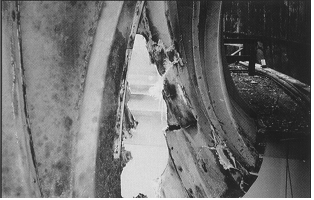
그림 1-7 전동기가 위치했던 Gaping Hole을 보여주는 Fan Stack
Titus 발전소의 감독부서와 정비 담당자로 구성된 조사팀은 조사후 유사 사고가 재발하지 않도록 다음의 3가지 방안을 제시했다.
(1) Fan 보호용 진동 스위치와 수동으로 자료를 수집하기 위해 Snapshot를 계속 사용한다. 자료의 수집 주기를 줄이고 정기적으로 진동 스위치를 시험한다.
장 점 : 초기 Hardware 비용을 최소로 할 수 있다.
단 점 : 진동값을 수집하고 진동 스위치를 시험하기 위해 전보다 기술자들이 자주 탑으로 들어가야 하므로 비효율적이며, 이 경우에도 중요한 진동 정보를 놓칠 수 있다.
(2) Fan에 영구적인 변환기를 설치하고 감시기에 연결해서 정확히 동작하는지를 계속해서 점검한다. 고진동이 감시되면 감시기가 자동으로 Fan을 정지시키도록 한다.
장 점 : 기본적이고 신뢰성 있는 보호체계로서 Fan의 심각한 손상을 막아준다.
단 점 : 초기 Hardware 비용이 많다. 기술자가 탑에 들어가지 않으면 진동을 분석하고 판독하는데 자료를 이용할 수 없다. 이 또한 비효율적이며 인력 낭비이다.
3) 영구적인 변환기와 감시기, Online Trending과 진단 시스템을 설치한다.
장 점 : Fan이 보호되고 진동 정보가 자동으로 수집되어 계속해서 진동 경향을 판단하고 진단할 수 있다. 이것은 초기 단계에서 Fan의 문제점을 진단할 수 있고 기술자들은 자료 수집을 위해 탑내에 들어가지 않아도 된다.
단 점 : 초기 감시 시스템의 자료 수집 Hardware 비용이 가장 크다. 일부 Online 진단 장치를 효과적으로 사용하는데 상당한 훈련이 필요하다.
2.3 實行 方案 (Implemented Solution)
조사팀은 Fan의 손상과 최근의 또 다른 냉각탑 Fan의 문제로 인해 Titus 발전소는 $ 300,000 이상의 비용이 들었다는 것을 알았고, 이러한 비용으로 미루어 볼 때 앞의 2번째와 3번째 안의 채택에는 크나큰 무리가 없음을 알았다. 계속된 연구와 비용 분석후에 장기적인 안목에서 3번째 안이 채택되었다.
조사팀은 다양한 Online Monitoring과 진단 장치에 대해 연구했고 시스템의 초기 Hardware와 설치 비용을 비교했으며, 또 그 시스템을 운용하는데 필요한 훈련량도 비교했다. 그들은 Titus 발전소가 진보적인 예방정비 프로그램을 계획하고 있었기 때문에 시스템을 얼마나 쉽게 확대 적용할 수 있는가를 조사했다. 조사팀은 저가인 89129 가속도계와 1900 Series 모니터와 함께 Online Trendmaster 2000 시스템을 사용하기로 결정했다. 그 시스템은 1994년 초에 8개의 냉각탑 Fan에 설치되었다 (그림 1-8).
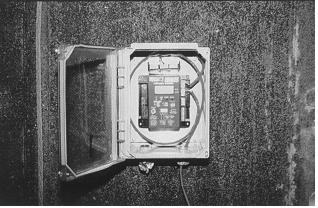
그림 1-8 냉각탑의 외벽에 설치된 전천후형 케이싱 내에 있는
Trendmaster 2000 TIM과 1900 Series 감시기
Trendmaster 2000은 컴퓨터를 기초로한 Online System으로 운전 및 경향 자료를 시스템에서 매 Point마다 수집한다. 또한 경제적 비용으로 설치, 사용, 확장할 수 있게 설계되었고, 쉽게 설치할 수 있는 저렴한 가격의 구성품들을 사용한다. 이것은 독특한 Multi-drop 구성으로 하나의 케이블에 256 Point까지 설치할 수 있다. 데이터를 얻는 컴퓨터는 총 2048 Point를 가지는 8 개의 케이블로 되어 있다. 하나의 전송기에 각각 연결되어 있는 시스템들과 비교해볼 때 Trendmaster 2000은 설치 비용이 훨씬 적게 든다. 확장시키는 방법은 새로운 전송기를 현재 있는 케이블에 연결시키거나 새로운 위치에 케이블을 증설하면 된다. Trendmaster 2000의 운용체계 Software를 사용하는데는 그다지 많은 훈련이 필요하지는 않다.
89129 진동 가속도계는 비용면에서 속도 변환기와 거의 비슷하고 기계적으로 동일한 Micro-machined Silicon Sensor를 사용한다. Bently Nevada의 1900 Series 모니터는 비용이 경제적이며 Single Channel이며, 기본적이고 일반적인 기계류의 지속적인 Monitor에 사용된다. Titus 발전소가 선택한 1900 Series 모니터는 Trendmaster 2000 Interface가 내장되어 있다.
각 냉각탑 Fan은 2개의 영구적인 진동 가속도계를 가지고 있으며, 하나는 감시기에 하나는 기어 감속기에 설치되어 있다. 각 기어 감속기에 설치한 가속도계는 1900 Series 감시기에 연결되어 고진동시 Fan을 정지시키도록 되어있다. 1900 Series 감시기 8개 모두가 하나의 Trendmaster 2000 신호 케이블에 직접 연결되어 있다. 이 케이블은 각각의 Fan 전동기를 통해서 8개의 Transducer Interface Modules(TIM) 통해서 각각의 Fan 전동기에 있는 진동 가속도계에 연결되어 있다. 하나의 케이블이 냉각탑에서 Engineering Room으로 연결되어 있고, 이곳에서 Online Trendmaster 2000 시스템 컴퓨터에 연결되어 있다. 각 Fan의 1900 Series 모니터와 TIM은 전천후형 NEMA 4 Housing에 함께 설치되어 있다. 전천후형의 각 Housing은 Fan 감시기 가까이의 냉각탑 벽에 설치되어 있다.
2.4 向後計劃 (Future Plans)
Titus 발전소는 Trendmaster 2000 시스템을 보일러 급수펌프, F.D Fan, I.D Fan에 확대 설치할 계획을 가지고 있으며, 이렇게 추가로 설치된 것은 보호프로그램 역할뿐만 아니라 기계적 문제가 발생할 때 사전에 인식할 수 있는 예방정비 프로그램의 역할을 하게 된다. 초기에 문제점을 발견하면 Titus 발전소나 그 고객 모두에게 비용을 절감할 수 있게 된다.
2.5 要約 (Summary)
휴대용 자료 수집기나 기계적 진동 스위치로는 냉각탑 Fan을 신뢰성 있게 운전할 수 없으므로 “Shut-Down” 기능을 가지며 영구적인 모니터와 Online 진단 및 경향을 판단하는 연속적인 감시 시스템이 냉각탑 Fan을 안정적으로 운전할 수 있는 최선의 선택이다. 냉각탑이 설계 성능 한계점에 이르러서 운전되고 그로 인해 냉각능력 손실이 전력생산 능력에 영향을 미칠 때 Trendmaster 2000 시스템은 한층더 신뢰될 수 있다.
3. 원격 진동 진단 시스템 (The Application of a Remote Vibration Diagnostic System for Rotating Machinery of a Power Plant)
3.1 槪 要 (Introduction)
발전설비를 포함한 자본 집약 산업에서의 세계적인 기술 추세는 Net-Work 기능을 구축하여 현장 기계의 운전 상태의 감시, 추적 관리 및 진단을 통해 기계의 사전 정비를 실시하여 비용을 최소로 절감하고, 자원을 최대한 활용하고, 노동 생산성을 증가하고, 설비의 신뢰성 향상과 가동시간을 증가시키기 위한 노력을 계속하고 있다.
이러한 세계적인 추세에 발맞추어 한국전력공사는 공사가 보유하고 있는 광통신망을 이용하여 발전소 주요 회전기계의 진동 상태를 한전 본사 진동 전문가들도 Online Real Time 분석이 가능하도록 1996. 12. 31일부터 회전기계 원격진단 Network의 구축이 완료되어 운영중에 있으며, 그 동안 프로그램 운영기술 향상과 진동 기술에 대한 저변 확대를 위해 원격진단용 프로그램 운영 지침서 번역 및 운영 기술을 전파하였으며 Network이 구축된 Unit를 대상으로 본사 진동 전문가들이 현장 출장을 가지 않고도 회전기계의 진동상태 감시, 분석 및 대책을 수립하는 등 직접 기술지원하므로서 최근 어려운 전력 수급 상황에도 불구하고 신속하게 발전소 주요 회전기계의 신뢰성을 향상시켜 전력 수급 위기 상황을 슬기롭게 극복하는데 크게 기여하고 있다.
3.2 遠隔 振動 診斷 시스템 (Remote Vibration Diagnostic System)
1) 진단 시스템의 제원
• 진동 분석 및 진단 Program Name : DM(Data Manager) 2000
※ 특징(TDM2 비교)
∙ 원격통신 : Modem 방식 → Network 방식
∙ DCS(Distributed Control System) 데이터 공유 가능 : 480 Point
∙ Network 사용자수 : 10 → 255 Users
∙ 진동 Trend 상호 비교 가능 : 8 Points
• Network 구축 완료일 : 1996. 12. 31(1단계)
• Network 구축 발전소 : 23개 사업소 59 Unit(’98. 4 현재)
• 대상기기 : 터빈/발전기, BFP-T, BFP-M, CWP, FAN 류
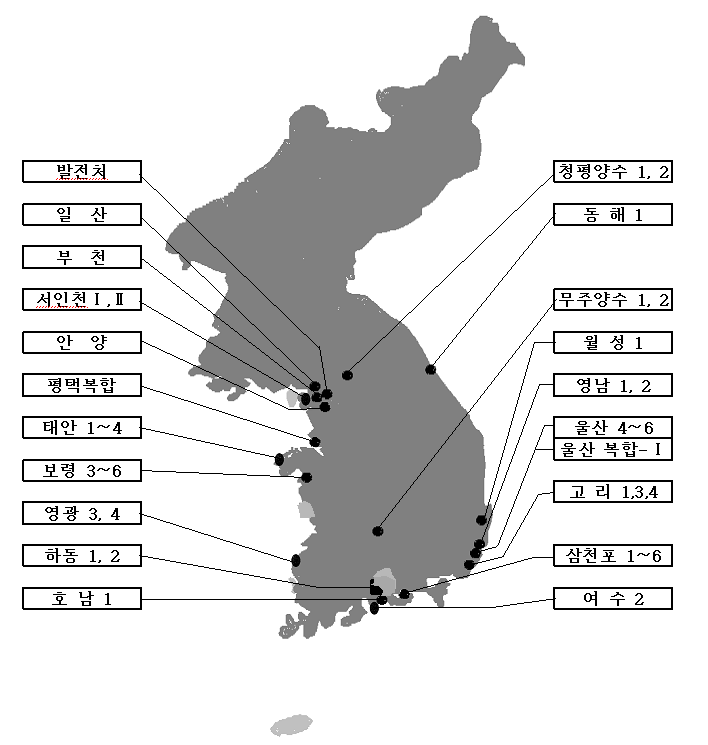
그림 1-9 원격 진동 진단 설비 구축 현황 (‘98. 12월 현재)
3) 원격 진단 시스템 하드웨어 구성
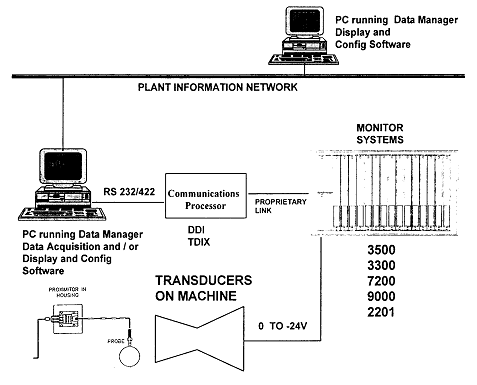
그림 1-10 원격 진단 시스템 하드웨어 구성
3.3 泰安 2號基 發電機 베어링 振動 上昇 原因 糾明 및 對策 樹立(事例 1)
(Case 1 : Cause and Answer High Vibration in Taean #2 Unit Generator Bearing)
1) 운전 현황
‘95. 10 상업 운전 이후 발전기측 #7 베어링 축진동이 75 ㎛이하로 운전되어 오다가 ‘97년 3월 2일 주말정지 기동후 #7, 8 베어링 축진동이 20 ㎛ 정도 상승하였으며 그 이후 #7 베어링 축진동이 점진적으로 상승하여 ’97. 3. 15에는 150 ㎛까지 상승(그림 1-11 참조)하여 원격 진단을 실시한 후 진동 상승의 원인과 대책을 수립하여 현장 기술지원함.
일자베어링 | 97. 2. 28 | 97. 3. 2 | 97. 3. 11 | 97. 3. 13 | 97. 3. 15 | 비 고 |
#7 | 75 | 95 | 125 | 132 | 150 | 단위 : ㎛X-abs |
#8 | 48 | 65 | 92 | 97 | 97 |
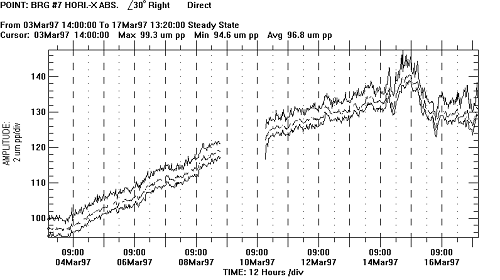
그림 1-11 #7 베어링의 진동 Trend
2) 원인 검토
• Misalignment
발전기 전후측 베어링 메탈 Temp. 온도차가 9℃로 크게 나타나고, 특히 그림 1-12와 같이 #7 베어링에서의 Orbit이 큰 타원형인 것으로 보아 C-Coupling에서 Rim 및 Face Misalignment가 큰 것으로 판단됨.
베어링 | #5 베어링 | #6 베어링 | #7 베어링 | #8 베어링 | 비 고 |
베어링 온도(℃) | 87 | 88 | 80 | 89 | 500 ㎿(’97. 3. 8) |
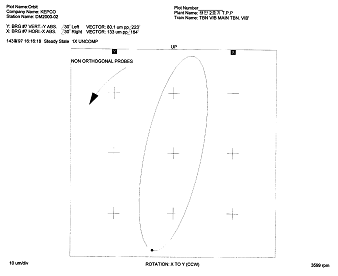
그림 1-12 #7 베어링에서의 Orbit
• 베어링 조립 상태 불안정
상대 및 절대 진동 위상차는 적으나 진동값 차가 62 ㎛로 진동값 차가 10 ㎛이하인 타 베어링에 비해 크게 나타남.
• 발전기 내의 수소 운전 온도가 33℃로 다소 낮게 운전됨.
(운전 범위 : 30~46℃)
3) 대책 수립
가) 임시대책
운전중 부하 감발과 발전기 수소 온도 상향 조정으로 “C-Coupling”의 축정렬 상태를 개선하여 발전기 베어링 부하 안배를 보다 균등하게 함으로써 점진적인 진동 상승 현상이 멈추어 진동이 130 ㎛에서 안정되었고 1개월 후면 계획예방정비 시행 예정이므로 계속 운전할 것을 권고하였음.
나) 근본대책
• 터빈/발전기 축계 축정렬 조정.
• 발전기 베어링 정밀 점검(Pinch Clearance 및 Ball Seat Contact 개선)
• 발전기 Foot/Base간 선형 접촉 상태 개선.
• 터빈/발전기간 Centerline Key 정밀 점검.
(4) 계획예방정비후 진동 상태
• Rotor Alignment 교정(단위 : 1/100 ㎜)
– 설계치
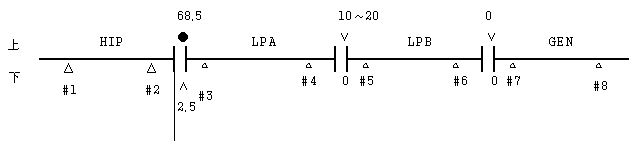
– ‘97 분해시
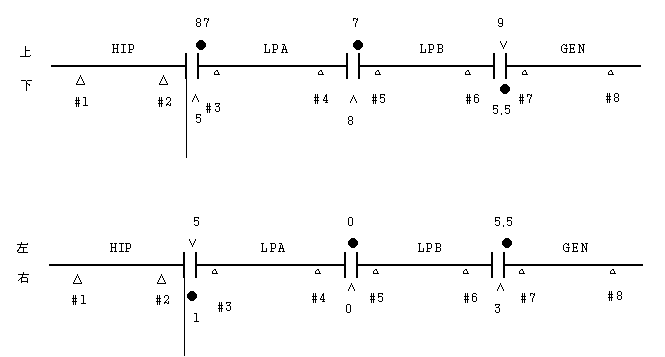
– ‘97 조립시
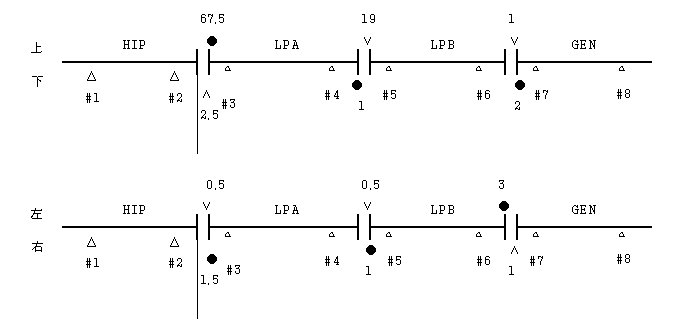
※ 분해시 A, B, C 커플링 모두에서 Alignment 상태가 불량하여 조정 조립하였음.
• 베어링 조립 상태 개선
#7 하부 베어링 Ball Seat Contact 개선(10 → 90%)
• 기동후 진동 및 베어링 부하 분담 상태
– 진동 개선 : #7, 8 베어링 진동이 152 → 46 ㎛
베어링부 하 | #7 베어링 | #8 베어링 | 비 고 |
O/H전 500 ㎿(’97. 4. 11) | 152 ㎛ | 98 ㎛ | X-absShaft |
O/H후 500 ㎿(’97. 6. 9) | 46 ㎛ | 47 ㎛ |
– 베어링 부하 분담 상태 개선 : 계획예방정비전에 비해 #3, 4 베어링 및 #7, 8 베어링에서의 부하 분담이 평균화 됨.
부하 | BEARING METAL TEMP | 비 고 | ||||||||
#1 | #2 | #3 | #4 | #5 | #6 | #7 | #8 | #9 | ||
1997.4.11 17:20500 ㎿ | 92 | 93 | 99 | 89 | 87 | 88 | 80 | 89 | 63 | O/H전 |
1997.6.9 10:00500 ㎿ | 95 | 99 | 92 | 90 | 88 | 87 | 82 | 86 | 63 | O/H후 |
3.4 嶺南 2號基 터빈 起動時 高振動 發生 原因 糾明 및 對策 樹立(事例 2)
(Case 2 : Cause and Answer of High Vibration in Young Nam Unit HIP Turbine Bearing during Start-up)
1) 운전 현황
영남 2호기 터빈은 ‘95. 11~’97. 4월까지 전 베어링의 진동치가 최대 53 ㎛ 이하로 양호하게 운전(그림 1-13 참조)되었으나 최근 4차례의 기동 및 정지시 HIP 터빈 베어링 진동이 상승된바 있으며 특이 사항은 다음과 같다.
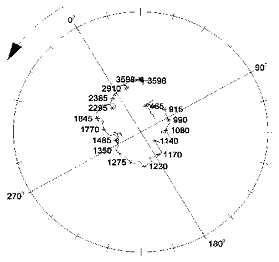
그림 1-13 정상 기동시의 #2 베어링 Polar Plot (Full Scale : 50 ㎛)
• ‘97. 4. 14 06 : 40 터빈 Rolling후 계통병입 준비중 보일러수 순환펌프 정지로 인해 터빈 정지중 1750 rpm 부근에서 #2 베어링 진동이 200 ㎛ 이상으로 급상승함 (그림 1-14).
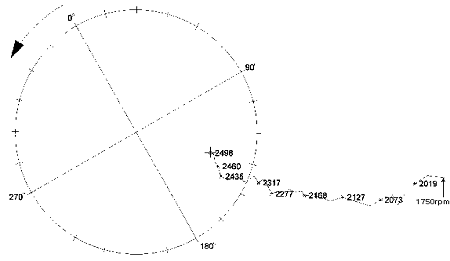
그림 1-14 정지시 #2 베어링 진동이 임계속도 부근(1750 rpm)에서 200 ㎛까지 상승함.
• ‘97. 4. 20 17 : 35 터빈 승속중 1758 rpm에서 DEHC Speed Control 시스템 제어 불량으로 2분간 Holding되자 #2 베어링 진동이 55 ㎛에서 200 ㎛까지 상승하였으며, 정지후 재기동하였어도 진동이 계속 증가하였음 (그림 1-15).
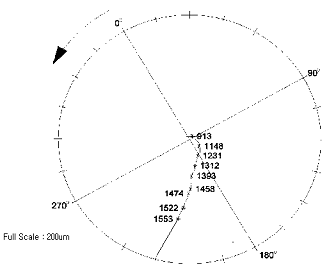
그림 1-15 기동시 #2 베어링 진동이 임계속도 부근(1758 rpm)에서 200 ㎛까지 상승함.
(2) 원인 검토
DM 2000 시스템은 기동, 정지시 또는 정상 운전중 진동 상승에 의한 경보 취명시 데이터가 자동 수집되는 기능이 있다. 기동, 정지시 1차 임계속도 또는 그 이하 속도에서 Rubbing 발생시에는 국부적인 High Spot가 발생되고 새로운 High Spot 발생없이(즉, 위상각 변화없음) 1× 진동 진폭이 크게 상승한다. 1차 임계속도 이상에서 Rubbing 발생시에는 새로운 High Spot가 계속 발생하고(즉, 위상각이 계속적으로 변함) 1× 진동 진폭 상승폭이 크지 않다.
영남 2호기의 경우 기동 또는 정지시 진동 급상승으로 인해 자동 수집된 Transient Data중 Polar Plot 및 Bode Plot 자료 검토시 1차 임계속도(1700~1800 rpm : 그림 1-16 참조) 부근에서, 그림 1-14, 1-15에서와 같이 1× 성분 진동이 위상각 변화없이 급상승하는 것으로 보아 Rubbing에 의한 진동 상승임을 판단할 수 있으며, Rubbing 발생 원인을 파악하기 위해 운전변수 자료를 요청하여 검토한 결과 터빈 Water Induction 관리 기준인 HIP 터빈 케이싱 상하 온도차 증가에 대한 경보 회로(30℃)가 구축되어 있지 않았다.
HIP 터빈 케이싱 상하 온도차가 그림 1-17 및 1-18과 같이 72~75℃로 경보치를 초과한 상태로 기동하여 케이싱 팽창이 불균일한 상태에서 임계속도 부근에서 장시간 운전으로 인한 Rubbing 발생이 그 원인임.
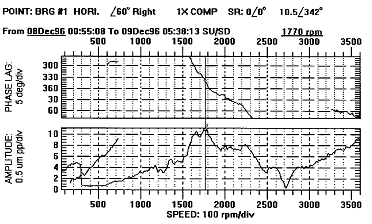
그림 1-16 HIP 터빈 #1 베어링 임계속도 : 1700~1800 rpm 부근
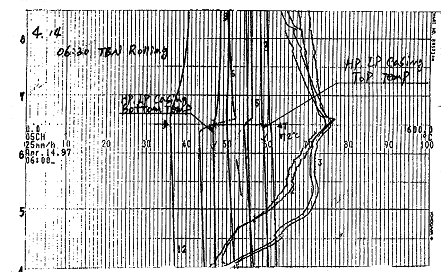
그림 1-17 ‘97. 4. 14 06:40 기동시 HIP 터빈 상․하부 케이싱 온도차 Chart (72 ℃)
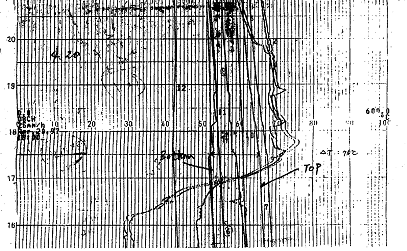
그림 1-18 ‘97. 4. 20 17 : 35 기동시 HIP 터빈 상․하부 케이싱 온도차 Chart (75 ℃)
3) 대책
○ Water Induction 관리 기준인 HIP 상, 하 케이싱 온도차 상승에 대한 경보 회로를 구축(30℃)하고 케이싱 온도차가 30℃ 이내에서 기동.
○ HIP 및 LP1 로터의 임계속도가 1700~1800 rpm 부근에서 나타나고 있으므로 기동시 DEHC Speed Target를 1600 rpm → 1300 rpm으로 프로그램 변경하고 임계속도 부근에서 승속율을 Fast Mode로 운전.
○ 기동 또는 정지시 이상 진동이 발생하면 DM 2000 프로그램 Bode 및 Polar Plot를 통해 진동 원인 분석한 후 Rubbing임이 확인(1차 임계속도 이하에서 위상각 변화가 없이 1× 진동이 증가)되면 감속후 바로 재 기동하면 진동이 감소하지 않으므로 터닝 기어를 최소한 2시간 이상 운전하여 Rubbing에 의한 로터 Thermal Bow 현상을 제거한 후 재기동함이 바람직함.
4. 진동 벡터 증가의 중요성 (The Importance of Vibration Vector Monitoring)
이 사례는 열병합 발전 플랜트의 터빈․발전기에 관한 것이다. 1기의 증기 터빈은 100 ㎿의 전기를 생산하고 2기의 가스 터빈은 각각 70 ㎿의 전기를 생산한다. 가스 터빈에 의해 발생한 남은 열은 증기 터빈용 증기를 생산한다 (그림 1-19).
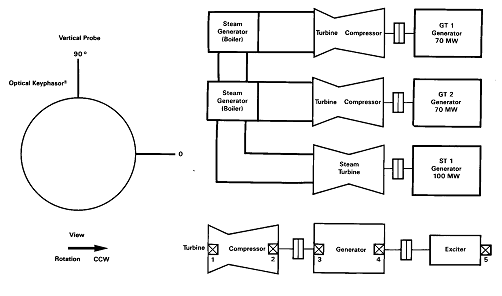
그림 1-19 복합 사이클의 전기 발전기기의 배열
이 가스터빈은 각 레디얼 베어링에 수직으로 설치된 벤틀리 네바다의 Dual Probe Transducer가 장착되어 있다. 이 진동감시 시스템은 축의 절대 움직임(Dual Probe 모니터에서 축의 상대 움직임과 베어링 하우징의 움직임의 벡터 합)을 나타낸다.
몇 달 동안 가스 터빈 Train중 하나가 진동문제로 골칫거리 이었다. 이 글은 문제에 대해 성공적인 검출과 해결을 가져온 상세한 분석을 정리한 것이다.
발전기와 여자기는 1년이 넘도록 진동 문제를 겪어 왔다. 진동 변화와 결부된 발란싱 문제로 철저한 기계 검사를 하였으나 주목할 만한 문제가 발견되지 않아 기계는 다시 조립되었다. 또한 궁극적으로 만족할 만한 발란싱 조건이 얻어진다 할지라도 여자기를 발란싱하는 것은 어렵다는 것이 판명되었다. 이 당시에 장비 제작자(Original Equipment Manufacturer: OEM)는 이 기기에 대한 일차적인 책임을 가지고 있었다.
아직 문제가 존재한다고 의심되기 때문에 사용자는 기계의 철저한 진동 분석을 하기 위하여 벤틀리 네바다의 기기 진단 서비스(Machinery Diagnostic Service)를 요청했다. 초기 진단결과 기계에 아무 이상도 발견하지 못했다. 그러나 아직 문제가 감지되고 있기 때문에 벡터 모니터링 프로그램 사용을 권고했다. 사용자에게 1× 진동 진폭과 위상을 주기적으로 기록하도록 하였다. 이것은 모니터와 연결된 벤틀리 네바다 디지털 벡터를 사용하여 정비요원들에 의해 수행되었다.
그후 몇 달 동안 일련의 실질적인 벡터 이동이 있었다. 여자기가 진동 변화를 보여줄 때 발전기 내측 베어링과 가스 터빈 압축기 베어링에 유사한 벡터 이동이 있었다. 발전기 외측 베어링과 가스 터빈의 고열 끝단에서는 작은 변화만 있었다.
처음에 진동 벡터 이동은 설명이 불가능 하고 예측 불가능한 것으로 보였다. 그러나 진동 특성의 패턴이 분명해 지기 시작했다. 우리는 몇 달후 새로운 문제(라 추정되는)를 개선하기 위하여 이전에 설치된 발란싱 웨이트를 제거했을 때 2가지 눈에 띠는 운전 모드를 알아냈다. 설명하기 위하여 2가지 모드를 모드 A와 모드 B로 언급한다.
모드 A에서 모드 B로의 벡터 변화 상태를 보면 거의 크기는 같고 방향은 반대였다. 그림 1-20과 1-21은 전형적인 벡터 형태도이며 이와 관련된 모드 A와 모드 B에 대한 축의 Mode Shape이다.
이 벡터 그림에서 전체(Overall) 진동 변화는 실제 진동 벡터(진폭과 위상각) 이동에 비하여 아주 작다. 이것은 특히 전체 진동 진폭이 아주 작은 변화를 보였을때 상당한 진동 이동이 발생한 여자기와 발전기의 내측 베어링에 있어 특히 뚜렷했다. 특별히 여자기의 모드 A와 모드 B 사이의 전체 진폭 차이가 1 mil 보다 훨씬 적었다. 그러나 진폭의 실제 벡터 변화는 대략 8 mils 였다.
이 설비는 단지 전체 진동 진폭에 의지하기 때문에 운전원은 모니터 값에서(있더라도) 단지 작은 변화만 눈치 챌 수 있었을 것이다. 결과적으로 실질적인 문제의 심각성은 눈치챌 수 없었을 것이다.
우리는 각기 모드에서 운전하고 있을 때 완벽한 진동 분석을 하게 되었다. 이 테스트의 막바지 과정에서 발전기의 전부하 차단 시험을 실행함으로써 모드 이동의 실질적인 결과가 얻어졌다. 기동 및 정지시의 데이터의 결과는 그림 1-22의 도면에 나타내었다. 여기서 우리가 즉시 알아낸 사실 중 한가지 지적할 만한 것은 진동 진폭의 이동은 Full Speed에서 발생하지 않았으며, 기계 손상이 2000 rpm 아래에서 발생했다는 것이다.
진동 데이터는 여러 단계의 부하와 오일 온도에서 수집됐으나 중요한 변화는 보지 못했다. 단지 2000 rpm이하의 운전에서만 진동 이동이 있었다. 우리는 1×와 2×의 과도상태 데이터, Slow Roll 정보, 특별히 축 균열 가능성에 주의하면서 정상상태의 데이터를 분석했다. 이 데이터를 분석한 결과 축균열의 증거는 전혀 없음을 나타냈다.
이쯤에서 모든 사람들은 이 문제가 심각할 수도 있기 때문에 기계적인 점검을 위하여 정지하여야 한다는데 동의했다. 전번 여자기의 점검시에 좀체 가시지 않는 불확실성이 있었는데, 특히 여자기는 아직도 고장 원인의 첫째 순위라고 생각했기 때문이었다. 그러나 터빈과 발전기의 전체를 점검하는 데는 많은 비용이 들기 때문에 사용자는 가장 문제가 되는 영역으로 문제를 좁혀 초점을 맞춘 점검 절차를 요구했다.
진동 이동의 원인을 찾아내기 위하여 모든 유효한 기계 정보를 수집하였다. 이의 관련 구성원은 발전기의 전기적인 고장에 대해 상당한 의견을 개진했다. 그러나 축 Mode Shape와 2가지 운전의 기계 모드의 반복성 때문에 우리는 여자기나 발전기의 일차 원인으로 전기적인 원인은 제외했다.
모드 A와 모드 B 사이의 1× 진동 벡터가 거의 정확하게 반복되기 때문에 이것은 하나의 기기 운전 모드에서 다른 모드로 변화시킬 수 있는 교번하는 큰 힘에서 올 수 있다고 가정했다. 우리는 이 정보를 토대로 진동 이동은 기계적인 불평형에 의해 초래될 수 있다고 가정했다.
터빈은 몇 가지 이유로 원인 규명 대상에서 제외되었다. 첫째로 가스 터빈의 압축기 부분에서 발생하는 어떤 질량 이동은 터빈 진동에 실질적인 영향을 줄 수 있는데 이것이 발생하지 않았다. 둘째로 터빈에 취부된 발란스 웨이트는 일반적으로 압축기에는 많은 영향을 주었으나 발전기와 여자기에는 거의 영향을 주지 않았다. 또한 우리가 비슷하게 설계되고 건설된 가스 터빈에서 불평형의 큰 변화를 관찰할 때 이러한 변화는 정지시의 과도상태에서 뚜렷하게 나타났다. 이러한 이유가 결론적이지는 않지만 가스 터빈은 고려대상에서 제외시키는 게 적절하다고 느꼈다.
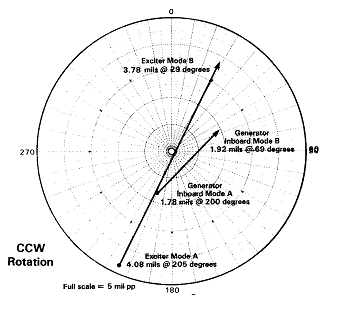
그림 1-20 모드 A와 모드 B에서 여자기와 발전기 내측 베어링의 진동 벡터
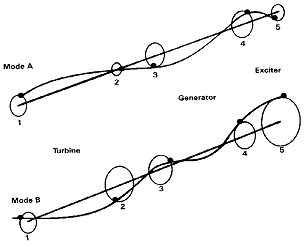
그림 1-21 Mode Shape
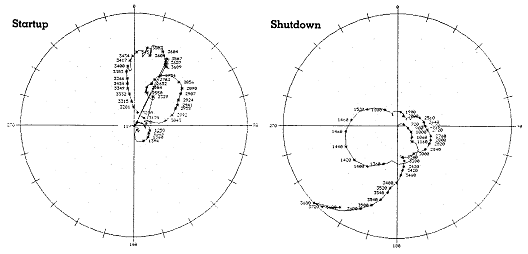
그림 1-22 기동, 정지중 여자기 #5 베어링의 Polar Plot. Full Scale
5 mils pp, 1× Filtered Comp., 반시계 회전 방향
그래서 관심은 질량 이동이 발생하는 발전기와 여자기 부분의 기계적 불평형의 가능성에 모아졌다. 과거 이 기계에 발란스 웨이트들이 부착되었고 각 발란스 과정에 대한 진동 응답이 잘 보고서화 되었기 때문에 우리는 이전의 각 발란스 과정의 영향과 이 기계에서 관찰된 데이터를 비교할 수 있었다.
여자기에 웨이트 부착에 의한 영향은 이 문제에서 보고서화 된 진동 이동과 비슷하지 않았다. 그리하여 여자기에서 가장 큰 진동 진폭이 발생하고 있었음에도 진동의 주요 원인에서는 제외되었다.
발전기에 대한 발란스 웨이트의 효과 벡터 데이터는 없었다. 그러나 제작자는 비슷한 기계에 대한 데이터를 제공했다. 그림 1-23의 그래픽은 이 기계에서 우리가 보았던 제시된 발전기 웨이트 효과와 상당히 유사함을 보여주고 있다. 이 정보로 발전기의 한쪽 끝이나 다른 쪽에서 원인 파악을 하게끔 점검범위가 좁혀졌다. 또한 이로 인해 비슷한 결과를 나타낼 수 있는 보정 웨이트의 계산을 할 수 있게 되었다.
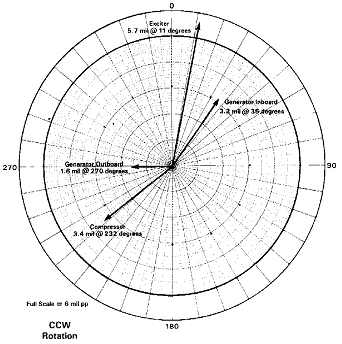
그림 1-23 발란싱 웨이트에 기인한 벡터이동
모달 이론과 유효한 과도상태 데이터를 사용함으로써 이 원인 파악이 발전기의 내측으로 더욱 더 좁혀졌다. 발전기는 2번째 공진 속도 가까이에서 운전되었기 때문에 이 Mode Shape는 2번째 모드 응답과 거의 비슷했다. 모달 분석으로 다른 모드와는 무관하게 축의 각 모드에 영향을 주는 웨이트 위치를 선택하게 되었다. 이러한 모드의 분석은 넓게는 일련의 다면 기계 발란싱에 사용되고 웨이트 교정 기술과 함께 사용된다.
이러한 분석 기법을 사용하여 실제 관찰된 축의 응답을 재현하는 이론적인 모달 교정 웨이트를 결정했다. 이 경우에 대칭인 발전기 축의 한쪽 끝에서의 웨이트의 취부는 첫 번째와 두 번째 발란스 Mode Shape 모두에 영향을 미칠 수 있다. 우리는 발전기 양쪽 끝에서 첫 번째와 두 번째 모드 응답의 위상 관계를 비교함으로써 각 모드에 미치는 영향을 예측했다. 이 결과 불평형의 원인으로 발전기의 내측 끝쪽을 지적하게 됐다. 이 데이터로부터 우리는 또한 각도위치가 잘못된 것을 예측했다. 이 시점에서 발전기 축은 철저한 기계 점검을 위해 공장으로 보내졌다.
이 점검 기간 동안에 제작자는 발전기(그림 1-24)의 내측끝의 권선 끝에 위치한 원주형 Spacing Block이 풀려진 것을 발견하였다. 이 블록은 리테이닝링(Retaining Ring: 보통 검사하는 동안에 제거되지 않음) 아래에 위치하고 있고 무게는 대략 1.6 ㎏ 정도였다.
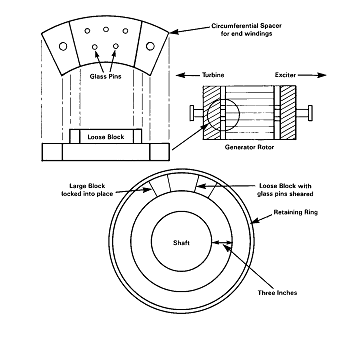
그림 1-24 기계 점검시 발견된 풀려진 스페이싱 블록의 상세도
권선과 저널 사이에 위치하고 있는 리테이닝 링은 블록이 축에서 빠지지 않도록 유지시켜 주나 이 블록은 축의 중앙으로 총 75 ㎜ 만큼 30도 원주 내에서 움직일 수 있다. 축이 정격 속도에 있을 때는 이 블록은 원심력에 의해 새로운 위치로 자리 잡는다. 터닝 기어 운전시에는 원심력이 무시할 정도로 작기 때문에 이 블록이 자유롭게 움직여서 새로운 위치로 스스로 이동한다.
이는 기계적 이동은 힘이 최대가 되는 높은 속도에서 보다 낮은 속도에서 발생하는 것을 설명해 준다. 이 움직이는 블록의 각도 위치와 계산된 원심력은 예측 된 값과 거의 비슷했다. 이러한 결함을 점검하지 않고 방치하여 놓으므로써 이 블록은 결국 권선 아래로 움직였고 따라서 문제를 초래 할 만큼 커다란 힘을 발생시켰다. 이 경우 다행이도 고장이 기계에 어떤 손상을 입히기 전에 발견되어 고쳐졌다.
이 사례가 진동 분석의 일반적인 진단 능력을 묘사하고 있지만 진동 벡터 측정(진폭과 위상)이 심각한 기계 문제를 발견하는 데 중요한 역할을 했다는 것을 주목해야 한다. 이 프로젝트 과정 동안 제어반 운전원들은 여러 번 있어온 진동의 심각한 변화를 눈치 채지 못했을 것이다 (단지 진동 모니터의 전체 진폭만을 보았을 것이다). 그러나 같은 기간동안 주기적인 벡터 측정을 행하고 관찰한 정비 관계자들은 이 변화를 볼 수 있었다. 이 것은 진폭이 거의 변화가 없는 상태에서 위상 변화에 의해 진동에 커다란 변화가 있었던 한 예이다. 이 문제는 단지 진동 진폭만을 보는 것으로는 알아 낼 수 없었던 것이다.
이 진동 사례에 있어 벡터 모니터링은 설비 관계자들에 의해 수동으로 행해졌는데, 주기적으로 정비 요원들은 모니터 시스템에 디지털 벡터 필터 장비를 연결하여 수작업으로 1× 진폭과 위상 값을 기록할 수 있었다.
더 쉽고 더욱 신뢰성 있는 방법은 벡터 모니터를 사용하는 것이다. 벤틀리 네바다 3300/60 벡터 모니터는 진동 진폭과 위상 혹은 어느 한 쪽 값이 미리 결정된 영역(허용 영역: Acceptance Region 이라 불림)의 한도를 넘는 것은 경보하여 회전 기기를 항상 보호하여 준다.
벡터 모니터링은 특히 불안정한 발란스 이력을 갖고 있는 기계와 축에 균열이 가기 쉽다고 증명된 모든 중요 기기에 응용할 수 있는 하나의 기술이다.
5. 축 중심선 감시의 중요성 (The Importance of Monitoring Shaft Centerline Data)
다음은 축 중심선 자료의 기본 원리와 최근 주요 공정기계의 시운전 기술지원시 경험한 사례에 대하여 기술하고자 한다. 이 사례는 최초 기동시의 심각한 Misalignment에 초점이 맞춰졌으나, 추후 베어링 리테이닝 스크류의 이완에 의한 것으로 밝혀졌다. 이 내용은 축 중심선 자료가 복잡한 기계의 오기능에 관한 추가 정보를 제공하기 때문에 진단 과정의 중요한 부분임을 설명하고 있다.
5.1 紹介 (Introduction)
1×, 2× Bode 및 Polar Plot은 가장 유용한 기계진단 자료이다. 이들 자료는 속도 변화에 따른 기계의 진폭/위상각 응답을 보여준다. 실제로 이러한 형태의 자료 표시는 널리 보급되어 있고 기계 진단용으로 관찰하는데 최상의 그림이기 때문에 산업계의 표준으로 인정받고 있다. 그러나, 또 다른 자료 표시 형태인 “축 중심선”은 일반적으로 빠트리고 본다.
많은 기계 진단 기술자는 축 반경 위치 정보의 가치를 오랫동안 인정하여 왔다. Preload의 존재 유무는 베어링 간극 내에서 축 중심선의 평균 반경 위치를 관찰함으로써 빨리 알 수 있다. 축 중심선 위치는 방전에 따른 베어링 베비트 손상 또는 장기간 사용에 따른 베어링 마멸의 결과로 변할 수 있다.
“회전기계에서 축 중심선의 감시로 변화하는 기계 상태에 대한 중요하고 분명한 정보를 얻을 수 있다.” 이러한 개념이 다음 사례에서 기술되었는데 여기서 축 중심선 자료는 기계의 오기능을 해결하는데 중요한 성분이 되고 있다. 그러나 먼저 축 중심선의 감시 및 진단에 관한 이론적인 견해를 분명히 하기 위하여 간단하게 언급하고자 한다.
5.2 軸 中心線의 理論 (Shaft Centerline Theory)
비접촉식 와전류 변환기와 Proximitor로 반경 방향 축의 이동을 감시할 때 변환기 시스템은 다음의 신호 성분을 제공한다.
① AC신호 : 픽업 장착부에 대한 상대적인 축의 동적인 움직임(Vibration).
② DC신호 : 픽업 장착부에 대한 상대적인 축의 평균 반경방향 위치(Gap).
대개, 동적인 신호는 반경방향 진동감시기로 감시되며, ㎛ 또는 mils Peak to Peak 단위로 표시된다. 그러나, 신호의 DC 성분은 대개 잘 사용하지 않고 있다. Axial Position Probe가 축방향 움직임을 감시하듯, 반경방향 Proximity Probe는 베어링 내에서의 반경방향 축위치를 측정하는데 사용될 수 있음을 알아야 한다.
축중심선 감시에 사용되는 2개의 Proximity Probe는 각 베어링에서 서로 90˚(XY)되도록 설치되고, 여기서 필요한 DC성분을 제공한다. 두 신호의 조합과 이미 알고 있는 베어링 반경 간극을 비교하면, 베어링 간극내에서의 축 중심위치를 구하는 충분한 정보를 얻게된다.
보다 정확한 축 중심선 자료를 수집하기 위해서는, 초기 정지시의 Gap Voltage 기준이 필요하다. 이 기준은 로터 정지시 또는 터닝기어 운전시 수집된다. 이때, 로터는 베어링 하단부에 위치하게 된다. 따라서 이후의 모든 Gap Voltage 측정은 초기 시작지점이 기준이 된다. 기동시 속도가 증가함에 따라, 변환기로부터의 Gap Voltage 변화량은 베어링내에서의 평균 축 이동거리를 나타낸다. 따라서, 정격속도에서 베어링내에서의 축 위치를 쉽게 알 수 있다.
베어링내에서의 축 위치를 분석하면, 다음과 같은 여러 가지 중요한 매개변수에 관한 정보를 알 수 있다.
① 커플링과 베어링의 정렬상태
② 로터의 예압
③ 유막 두께
④ 베어링 마멸
⑤ 양태각(Attitude Angle) α
양태각은 로터에 작용하는 정적 하중(중력 또는 유체력: 그 방향은 정확히 알려져 있지 않음)방향과 베어링의 기하학적 중심점과 축의 중심선을 연결하는 선사이의 각도로 정의된다.
정확한 베어링 간극과 정지시의 Gap Volt 기준값을 주의 깊게 구하면, 양태각은 축 중심선 자료로 쉽게 얻을 수 있다. 일반적으로, 축의 양태각을 평가하므로써 특정기계의 안정성 한계(Stability Margin)를 알 수 있다. 기계의 축정렬이 정확하고 축 중심선 측정용 매개 변수들을 관찰했을 때 양태각이 90˚에 이른다는 것은 시스템이 불안정한 상태임을 나타낸다. 그림 1-25 (정상), 그림 1-26 (비정상)을 참고하라.
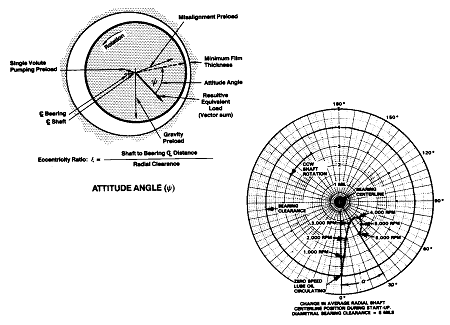
그림 1-25 축의 양태각 정의(상). 축의 반경방향 평균 중심선 위치가
기동시 어떻게 변화하는가의 한 예(하).
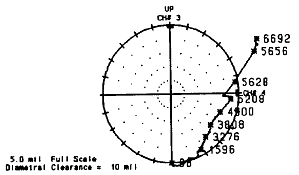
그림 1-26 6,692 rpm에서 베어링 간극을 초과하여 과도한 축의 움직임을 보여주는 축 중심선 자료.
이 그림은 또한 기동시부터 로터의 전체 이동량을 보여주며,
이때의 양태각은 수직 방향으로부터 약 130˚이다.
일반적으로 시계방향으로 회전하는 기계의 베어링내에서 이상적인 축 위치는 수직방향으로부터 측정시 20~60˚의 양태각(α)을 가지며 좌측 하단부 4분면에 있다. 마찬가지로 반시계 방향으로 회전하는 기계는 양태각은 같고 우측 하단부 4분면에 있다. 관찰하는 규칙은 항상 구동기(전동기/터빈)에서 종동기(발전기/압축기)를 향하여 바라보는 것으로 한다.
5.3 事例 (Case History)
문제의 기계는 6단의 증기터빈과 기어 커플링을 통해 구동하는 7단의 원심 압축기로 구성되어 있다. 주된 운전속도는 7100 rpm 근방이다. 공정제품은 오일정제 계통에서 냉매로 사용되는 Propane이다.
계획정비 기간동안 완전 분해 및 점검 작업이 수행되었다. 전 저널 베어링의 교체, 압축기 로터의 재가공, 터빈 로터의 재 제작 작업이 수행되었다. 재조립시의 축 정렬은 이전 정지시의 Hot, Cold 축정렬 자료를 이용하여 자체인력에 의해 수행되었다.
초기 기동시 1× Bode 및 Polar Plot에서 시스템의 잔류 불평형은 거의 없음을 보여주었다. 실제로 1차 공진 통과시 최고 진동은 51 ㎛ pp를 약간 넘었다. 모든 지시치로 보아, 기계의 운전 상태는 정상으로 보였다. Orbit 및 스펙트럼 자료에서도 이상점이 발견되지 않았다. 그러나 시간이 경과한후, 정상 상태에서 터빈 양 베어링에서 작은 진폭 및 위상 변화가 갑자기 발생하였다. 이때, 압축기 베어링에서는 변화가 발견되지 않았다. 축 중심선자료 검토결과, 무언가 심하게 나빠진 것으로 나타났다. 그림 1-26에서 터빈 내측 베어링에서의 축 위치가 운전속도에서 51 ㎛정도 베어링 간극을 초과 하였다.
공장자체 기록에 의하면 이 기계의 축 정렬은 이전의 정지기간중 다이얼 게이지를 장착한 Essinger Bar를 사용하여 수집된 Hot, Cold 값을 이용하여 추정하였다. 기계의 진동감시는 계속되었으며, 압축기의 어떤 부하 범위를 넘어서자 변화가 발생하였다. 이 변화는 양쪽 터빈 베어링에서 반경방향 진동이 높은 것으로 나타났고 이따금 Trip되어 전력계통으로부터 분리되었다.
초기 기동시 발생한 격심한 압축기 서징 현상이 이러한 갑작스러운 진동 위상 변화에 영향을 미쳤으리라 추정되었다. 분석결과 압축기 서징 발생시 터빈 로터의 Preload의 변화 때문에, 축정렬상태가 의심스러웠다.
축정렬 점검을 위하여 기계를 정지하고자 준비중일 때 제작도면 특히, 터빈 내측 베어링 도면을 검토한 결과 베어링 리테이닝 조정나사(Setscrew)를 의심하게 되었다. 조정나사가 느슨해지면 상부 베어링에서의 구속력이 없어지므로, 로터가 베어링 간극을 초과하여 이동될 수 있다.
이 조정나사는 내측 베어링 Carrier 상부에 있고(그림 1-27), 상부 Carrier를 잡아주는 단일 부품이다. 조정나사의 OEM 권고 조임치는 27 N․m이다. 조정나사는 베어링 하우징 외부 커버를 제거하면 운전중에도 접근 가능하다. 정지에 앞서 점검결과 조정나사의 이완이 발견되었다.
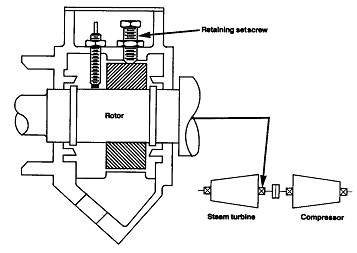
그림 1-27 터빈 내측 베어링과 베어링 리테이닝 조정나사 위치를 나타내는 도면
공장 책임자는 먼저 정상속도로 운전중 조정나사를 조이기로 결정하였다. 조정나사를 조이자 축 중심선 위치가 베어링 간극내로 바로 복귀된 것을 그림 1-28에서 분명히 보여주고 있다.
이러한 조치로 로터의 Preload를 크게 증가시켰고, 양쪽터빈 베어링에서의 1× 진폭 및 위상의 변화와 더불어 Orbit에 주로 영향을 미쳤으나 압축기는 영향을 받지 않았다.
마침내 기계를 정지한후 점검결과, 터빈 압축기의 축정렬 상태는 수직방향으로 크게 불량했다. 그림 1-28 하단부의 축 중심선 자료를 보면, 축위치가 내측 베어링에서는 여전히 높다는 것이 분명하다. 터빈 축정렬 수치는 최근의 Hot Alignment 기록치를 기준으로 재계산 되었으며, 최종 Cold Alignment 기록치로부터 Thermal Growth 값이 산출되었다. 실제 수정 Alignment는 축중심선 자료를 추가로 참고하여 터빈을 이동하여 시행하였다.
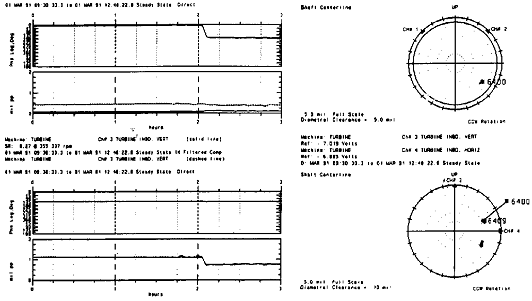
그림 1-28 1× 진폭 및 위상각변화(좌)와 조정나사 조임후 축 중심선 자료의 변화
HOR : 터빈 케이싱 79 ㎛ 우측이동 → 로터가 중심으로 이동
VER : 터빈 케이싱 229 ㎛ 상부이동 → 로터가 베어링하부로 이동
시계 반대방향으로 회전하는 수평 기계이므로, 이상적인 축위치는 20~60˚의 양태각을 가지고 우측 하단부 4분면에 있게 됨을 기억하라.
베어링 점검결과 터빈 내측의 상․하부 베어링 쉘의 손상이 발견되었다. 상부 베어링 쉘은 그림 1-26, 1-28에서 보여준 축위치와 똑같은 위치에서 마멸되었다 (그림 1-29 참고). 양 쉘은 교체되고, 플라스틱 게이지로 간극점검결과 254 ㎛로 측정되었다.
통상적인 축정렬기법과 함께 축중심선 자료를 이용하여, 보다 높은 정도의 신뢰성을 가지고 축정렬 작업이 수행되었다. 그림 1-30에서 운전속도에서의 베어링내에서 최종 축위치를 보여준다. 이러한 교정 작업후 더 이상의 문제점 없이 운전되었다.
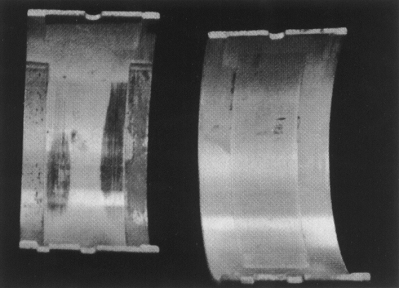
그림 1-29 축의 Misalignment와 조정나사 이완에 의한
마멸상태를 보여주는 터빈 내측 베어링
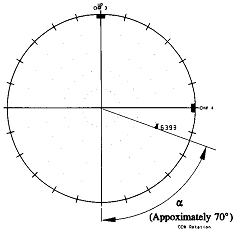
그림 1-30 터빈 내측 베어링에서 최종 운전속도 위치.
양태각은 130˚에서 약 70˚로 감소되었다.
5.4 結論 (Conclusion)
축중심선 자료를 감시함으로, 1× Bode 및 Polar Plot 만을 이용하는 것보다는 기계 오기능에 관하여 직접 초점을 맞출 수 있었고 해결책을 빨리 구할 수 있었다. 축 중심선 자료 없이는 문제점이 여전히 감지되지 않았고, 결과적으로 불필요한 정지 및 관련 비용이 증가하게 되었을 것이다.
6. 과도 상태 데이터 분석의 중요성 (The Importance of Transient Data Analysis)
진동 데이터는 기계가 일정 속도와 부하로 운전될 때나 변화되는 도중에도 얻을 수 있다. 각각의 데이터는 기계의 상태를 파악하는데 중요하다. 일정한 운전 상태에서 얻는 정상상태 데이터는 대부분의 기계 장치의 예방정비 프로그램에 필수적이다. 그러나 이러한 프로그램들은 기동 및 정지과정에서 즉 과도상태에서의 중요한 데이터를 얻지 못한다. 이 장에서의 정비 사례들은 과도상태 데이터가 실제 기계의 문제점을 해결하는데 얼마나 도움이 되는지를 보여준다.
6.1 過渡한 平均 軸 中心線의 位置變化 (Excessive Shaft Average Centerline Position Change)
발전소 운전원들은 출력 1150 ㎿의 증기터빈 발전기에서 과도한 진동현상에 관심을 갖게되었다. 이 터빈과 발전기는 원래 1985년에 시운전되었다. 첫 5년간의 운전 중에 기계 정비는 주로 터빈의 발란싱과 여자기의 축정렬이었다. 그러나 기계가 기동과 정지운전중 어떤 부하의 범위를 통과할 때 고압터빈에서 심한 진동이 발생하였다. 기동 운전중 취한 평균 축 중심선 데이터는 이 문제를 해결하는데 도움을 주었다.
증기터빈은 4단이고, Double Flow방식으로 설계되었고 1대의 고압터빈과 3대의 저압 복수터빈으로 구성되었다. 증기터빈과 발전기는 강성 커플링으로 연결되었다. 발전기는 4극이고, 회전수는 1800 rpm이며, 여자기가 설치되어있다. 11개 베어링의 각각에는 XY 방향으로 설치된 한 쌍의 Dual Probe 변환기가 설치되어 있다 (그림 1-31).
Dual Probe 변환기가 측정하는 것은 절대 축 이동 즉 자유공간에 대한 축의 절대 이동량이다. 그건 두 개의 변환기로 구성된다. 즉 케이싱이나 기초의 절대진동을 측정하는 한 개의 Seismoprobe 속도센서와 베어링 하우징에 대한 축의 상대 운동을 측정하는 한 개의 Proximity 검출기 이다. Keyphasor 검출기는 위상 기준을 제공하기 위해 터빈 축상에 설치되었다.
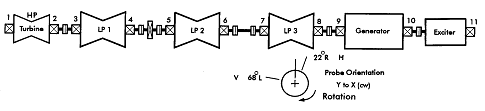
그림 1-31 1150 ㎿ Steam Turbine-generator Machine Train
기계진단(MDS) 그룹은 1990년 10월에 이 기계를 분석했다. 발전소 관계자는 기동 중에 고압터빈이 공진속도 지역을 통과하면서 진동을 일으키고 기초를 흔든다고 하였다. 10월 15일 아침에 2시간에 걸쳐 터빈과 발전기가 계통병입 속도인 1800 rpm에 도달되었다. 기계진단 그룹은 기동 중에 과도상태 데이터를 취하기 위해 108 데이터 수집 계측장비 일체와 ADRE 3 시스템을 사용했다. 10월 15일에서 18일에 걸쳐 부하를 1150 ㎿(전부하)로 올렸다. 한편 고압 터빈 측의 #1과 #2 베어링에서 과도상태 데이터를 취했고, 다음사항을 확인했다.
• 고압터빈 발란싱 상태는 문제가 없다. 무부하, 정격속도 및 전 부하에서 1× 진동진폭은 양 베어링에서 25 ㎛ p-p 이하이다 (그림 1-32a 및 1-32b).
• #1베어링에서의 동기 증폭 계수(QS)는 #7 베어링보다 더 크며(그림 1-32a와 1-32b에서 QS값은 비례법에 의해 계산된다), 그것은 비정상적으로 높다. QS값은 불평형 힘에 기인하여 로터의 고유 진동수에서 발생하는 진동진폭을 계산하는데 필요하다. QS값은 약 10인데 그 값은 시스템이 공진 상태에서 고진동을 일으킬 수 있는 것을 나타낸다.
• 그림 1-33은 2개의 평균 축 중심선 곡선이다. 평균 축 중심선 곡선은 시간대별 평균 로터의 위치를 나타낸다. 이 곡선에서 점선 원은 베어링의 반경방향 간극이 20 mils(500 ㎛) 임을 나타낸다. 그림 1-33은 운전속도에서 #2 베어링이 0.4의 편심율과 120˚의 로터 위치각(수직 하부기준)을 가지는 것을 보여 준다. 그러므로 #1과 #2 베어링에서 로터의 중심선은 베어링의 좌측상부의 사분면에 위치한다. 유막 베어링을 가진 기계에서 이와 같이 로터는 속도가 증가함에 따라서 통상적으로 Oil Wedge 위로 올라간다. 비정상적인 부하가 없는 상태에서 Y방향에서 X 방향(시계방향)으로 회전하는 축은 보통 20˚와 50˚사이(수직 하부가 기준)의 위치각을 가지며 그 베어링의 좌측하부의 사분면에 위치하게 될 것이다.
• 그림 1-33은 또한 부하(증기유량)증가에 따라 #1과 #2 베어링에서의 로터의 위치가 극적으로 변화하는걸 보여준다. 10월 15일 오전 9시 직후에 부하는 증가되었고, #1 베어링에서 오른쪽 위로 들렸는데 그 위치는 오른쪽으로 11.5 mils(292 ㎛), Zero 속도 (베어링의 하부)에서 위로 34 mils(864 ㎛)였다. 이것은 850 ㎿출력에서의 위치와 일치하였다. 부하가 더욱 증가함에 따라 로터는 왼쪽 아래로 움직여 최종위치인 왼쪽으로 4 mils(100 ㎛) 그리고 기준위치 위로 21 mils(530 ㎛)에 위치하게 되었다.
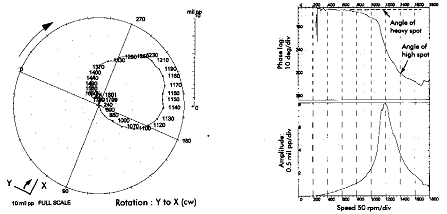
그림 1-32 베어링 간극이 적절히 설정 되기전 #1 베어링 수직 변환기에서의 1× 과도응답.
(a) Polar, (b) Bode Plot
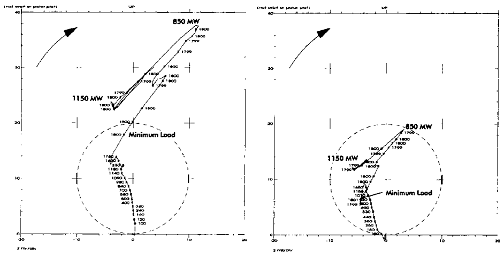
그림 1-33 베어링 간극이 적절히 설정되기전 #1, #2 베어링에서 평균 축 중심선이 변화한다.
진단그룹은 고압터빈 입구밸브의 Sequence를 조사하였다. 증기는 상부 및 하부 밸브 Rack을 통과하여 터빈으로 들어간다. Zero부터 850 ㎿의 부하상태에서는 하부 밸브 Rack이 열려 하부로부터 증기가 유입되어 로터를 들어올린다. 850 ㎿이상의 부하에서는 상부의 밸브 Rack이 열리기 시작하여 로터의 상부로부터 증기가 유입되어 로터는 위로부터 힘을 받는다. 그림 1-33에서 축이 #1 베어링과 #2 베어링에서 같은 방향으로 움직임을 보여준다. 그러나 #2 베어링에서 축은 베어링 간극내에서 이동하고 있으나 #1 베어링에서 축은 베어링 간극 바깥으로 벗어나 이동하고 있다. #1 베어링의 동기 증폭 계수가 정상보다 더높고, #1 베어링에서의 축 중심선이 비정상적인 움직임을 보여주었기 때문에 다음 사항을 의심하게 되었다.
• #1 베어링에서의 내부간극이 과도하지 않은지
• #1 베어링이 페데스탈에서 풀려, 적절히 고정되지 않았는지
• 상기 두 가지의 복합효과
전부하의 진동준위는 허용치 이내였다. 그러므로 운전원들은 #1 베어링을 점검하기 위해 다음 계획 정지시까지 기다리기로 결정했다. 나중에 #1 베어링을 검사하였을 때 발전소 정비요원은 과도한 간극이 있었음을 발견했다. #1 베어링은 4개의 패드조각으로된 틸팅 패드 베어링으로, 베어링의 내부간극을 적절히 맞추기 위해 두개의 상부패드의 Shim 조정이 필요했다. 이 베어링은 1985년 최종 조립시 Shim 조정을 하지 않고 그냥 넘겨버린 것이다.
#1 베어링의 간극을 적절히 조정한 후 1991년 5월에 재기동하였다. 기동 데이터로부터 작성된 Polar 및 Bode선도가 보여주듯 로터가 1200 rpm의 임계속도를 통과할 때 1×의 최대진폭은 4 mils(100 ㎛)pp을 초과하지 않았다. 같은 데이터로 만들어진 평균 축 중심선도는 #1과 #2 베어링에서의 평균 축 중심선이 전 속도와 부하범위에 걸쳐 각 선도의 왼쪽 하단 사분면에 머무른 것을 보여주고 있다 (그림 1-35). #1 베어링에서의 과도한 간극은 로터 베어링 시스템의 동적 강성을 감소시켰다. 공진 상태에서 동적 강성은 로터의 응답을 제한 즉 로터의 움직임을 제한시킨다. #1 베어링에서의 감쇠효과의 감소로 공진 상태에서 로터 진동이 다른 때보다 훨씬 커졌다. 이 무거운 로터는 발란싱이 잘되어서 공진 상태 이상에서의 진동은 허용치이내였다.
그림 1-32와 1-34에서 처럼 #1 베어링의 Shim조정 전후에 얻어진 데이터로부터 작성된 Polar 및 Bode선도를 비교하는 것은 흥미있는 일이다. 진동의 진폭은 감소하였지만 공진 주파수는 증가하였다. #1 베어링이 페데스탈 내에서 이완되었을 때 공진 주파수는 1190 rpm이었다. #1 베어링이 적절히 Shim 조정된 후 공진 주파수가 1240 rpm으로 상향 이동된 것으로 증명되듯이 기계적 강성은 증가했다.
평균 축 중심선도는 어떤 환경에서는 매우 유용하게 사용될 수 있다. 이 예에서 베어링 내에서 축 평균위치의 2차원 표시는 이 기계의 문제점이 #1 베어링에 있었음을 분명히 하고있다.
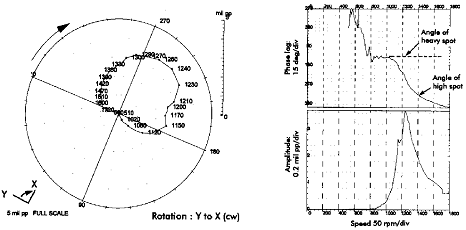
그림 1-34 베어링 간극이 적절히 조정된 후 #1 베어링 수직변환기에서의 과도상태 1× 응답.
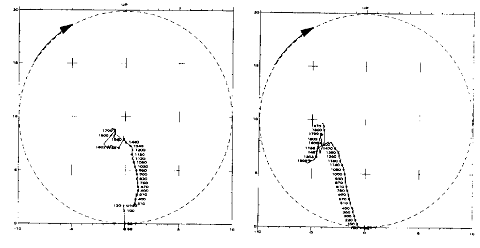
그림 1-35 베어링 간극이 적절히 조정된 후 평균 축 중심선 위치가 #1 및 #2 베어링에서 변화했다.
6.2 高次數의 過渡狀態 데이터는 軸龜裂을 확인하는데 도움을 준다. (Higher-Order Transient Data Helps Identify a Shaft Crack)
어느 원자력 발전소에서 1989년, 1990년, 1991년에 주 냉각재 펌프의 심각한 축균열이 발생하였다. Bently Nevada의 MDS는 여러 형태의 기계 데이터를 검토한 후 이 축균열을 확인하였다. 사용한 데이터의 일부는 회전속도 5배의 고조파로부터 취한 과도상태 데이터였다. 어떤 기계가 축균열이 있는지를 정확히 파악하기 위해서는 여러 가지의 많은 데이터를 필요로 한다. 과도상태 데이터는 중요하지만 그것이 필요한 유일한 데이터는 아니다. 요구되는 데이터들 중에는
• 전체 진동진폭의 경향 이력
• 1× 허용영역 데이터와 Slow Roll 데이터. 로터에 균열이 발생하면 로터는 휘고 1× 응답이 변한다.
• 2× 허용영역 데이터. 횡방향 균열이 성장함에 따라 축의 강성은 균열면에서 비대칭이 된다. 축의 비대칭으로 로터는 심한 반경방향 부하가 있게되어 2× 응답을 발생한다.
• 과도상태의 데이터 선도에서 보여주는 것처럼 고유 진동수와 그들 진동수의 어떤 변화. 횡방향 균열은 축의 강성을 줄여, 고유 진동수들을 낮춘다. 주어진 로터 모드에 대하여 균열이 로터의 최대 처짐점에 더욱 근접할수록 고유 진동수가 더욱 낮아진다.
• 상태가 좋은 로터의 모델. 이것은 로터의 모드 형태를 평가하고 균열이 어떻게 고유 진동수를 변화시키는지를 예견하는데 도움을 준다.
이 내용은 과도상태 데이터 분석에 초점을 맞추고 있기 때문에 고차수인 5× Polar 및 Bode 선도에서 축균열이 어떻게 분명 하였는가에 대해서만 설명을 하겠다. 여기서 제시된 데이터는 1989년과 1990년에 발생한 균열된 축으로부터 취해진 것이다.
주 냉각재 펌프는 7,940 HP의 전동기로 구동되는 대형 수직펌프이다 (그림 1-36). 정격 펌프속도는 1790 rpm이고, 공칭유량은 150,000~170,000 ℓ/min(40,000~45,000 gpm)이다. 펌프 임펠러는 5개의 날개를 가졌다.
균열이 발생한 축의 현상에 대한 기계를 분석함에 있어 1× 과도상태 응답으로 로터의 정상운전속도 이내에서 일어나는 공진의 변화를 알아낼 수 있다. 이 펌프의 1차 공진 주파수는 주로 전동기의 병진운동 응답 때문에 1800 rpm보다 조금 높았다. 이 모드에서 최대 변화량은 전동기 축의 중간 Span에서 나타났고, 반면 커플링으로부터 펌프 임펠러까지에서 1× 진동은 거의 발생하지 않았다. 이 펌프의 2차 공진 주파수는 3100~3,200 rpm이었으며 이건 펌프축의 응답이다. 최대 변화량은 펌프 임펠러에서 나타나는데, 전동기 상부로부터 펌프 커플링까지의 부분에서는 거의 나타나지 않았다.

그림 1-36 냉각재 펌프
이 두 공진 모드 형태에서 펌프 로터의 횡방향 균열은 1차 공진에는 영향을 미치지 않지만 2차 공진 주파수에는 심각한 영향을 미친다는 것을 암시했다. 고차수의 과도상태 분석의 원리는 회전하는 축은 회전속도의 정수 배에서 가진 함수를 창출해낼 수 있다는 것이다. 그러므로 이 기계에서 축의 회전속도가 1550 rpm을 통과할 때 2×의 가진 함수는 3100 cpm을 통과한다. 이 펌프에서 2차 공진에 대한 최대 변화량이 임펠러에서 나타남을 기억하라. 5개 날개의 임펠러는 5배의 축회전속도에서 고유 가진함수를 창출하도록 시스템의 수력학과 상호작용을 한다. 만일 330 rpm에서 1800 rpm까지 5× 임펠러 날개의 통과 주파수를 추적했더라면 1650 rpm에서 9000 cpm까지의 펌프 로터의 응답을 관찰할 수 있었을 것이다.
상태가 좋은 펌프는 3100 cpm과 3200 cpm사이에서 2차 공진 주파수를 가졌다. 전형적인 펌프로부터 취한 5× 응답 Polar 및 Bode선도인 그림 1-37a와 1-37b는 이것을 보여준다. 1989년에 균열이 발생된 펌프 축으로부터 취한 동일한 선도형태에서 2차 공진피크가 5 mils(125 ㎛)pp이상의 5× 진동진폭과 함께 2540 cpm아래로 이동했음을 보여준다 (그림 1-38a와 1-38b).
마찬가지로 1990년에 균열이 발생된 펌프 축은 2차 공진 주파수가 2955 cpm으로 낮아졌다 (그림 1-39a와 1-39b).
이것은 사용한 축이 균열되었음을 결정하는데 이용한 유일한 데이터는 아니었지만 고차수인 이 5× 응답선도는 매우 중요하였음이 명백하다.
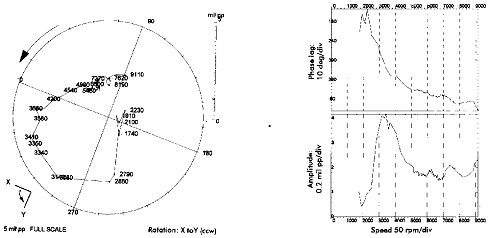
그림 1-37 축 균열이 없는 전형적인 냉각제 펌프의 5× 과도상태의 공진.
2차 공진 주파수는 3140 cpm에 발생한다.
(a) Polar, (b) Bode
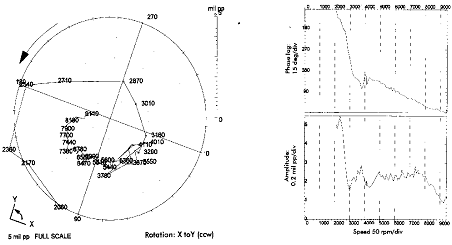
그림 1-38 균열된 축을 가진 냉각제 펌프의 5× 과도상태의 공진.
2차 공진 주파수는 2540 cpm에서 발생한다.
(a) Polar, (b) Bode
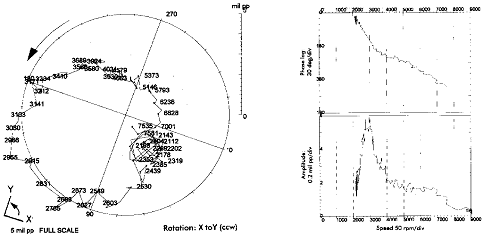
그림 1-39 균열된 축을 가진 냉각제 펌프의 5× 과도상태의 공진.
2차 공진 주파수는 2955 cpm에서 발생한다.
(a) Polar, (b) Bode
6.3 結論 (Conclusion)
대부분 기기의 예방정비 프로그램들은 정상상태에서의 데이터이며 과도상태 데이터를 사용하지 않는다. 이것은 불행한 일이다. 왜냐하면 과도상태 데이터는 정확한 기계의 검사를 위해 필수적이기 때문이다. 여기에서 설명한 사례들에서 과도상태 데이터 분석의 진가를 납득하기를 바란다.