Flow-Induced Vibration Problems
1. 발전기에서의 Oil Whip을 진단하는데 있어 유용한 기준자료 (Baseline Data Useful in Diagnosing Oil Whip in a Generator)
2. 유도 전동기에서의 정확히 50%의 차동기 진동 (Exact 50% Subsychronous Vibration on Induction Motor)
3. 설계상 문제로 인한 Oil Whirl (Oil Whirl Caused by Design Problem)
4. 증기터빈에서 증기에 의한 Whip의 진단 (Diagnosing Steam-Induced Whip on a Steam Turbine)
5. 불안정성 발생 위치의 규명 (Defining the Source Location of Instability)
7. 보일러 급수펌프의 수력 강제진동 (Hydraulic Force Vibration in a Boiler Feed Pump)
8. 냉각수 펌프내에서 케비테이션 진단 (Cavitation Diagnosis within a Chilled Water Pump)
1. 발전기에서의 Oil Whip 진단 (Baseline Data Useful in Diagnosing Oil Whip in a Generator)
Bently Nevada사의 기계진단 서비스팀(MDS)은 150 ㎿의 화력발전소의 발전기 양끝의 베어링에서의 고진동을 조사해 달라는 의뢰를 받았다.
발전기의 내․외측 베어링으로부터의 Unfiltered 및 Filtered 1× 진동신호가 축의 Orbit 및 Timebase 형태로 그려졌다.
그림 7-1에는 내측 베어링에서의 전체 진동신호 및 1× 진동신호가 축의 Orbit 및 Timebase 형태로 나타나 있다. 외측 베어링도 유사한 진동신호를 나타냈다. 전체 진동의 Time Base Plot은 진동 사이클당 하나 이상의 Keyphasor 표시를 보여 주는데 이것은 회전당 한번(1×) 보다 적은 진동주파수가 존재한다는 것을 나타낸다.
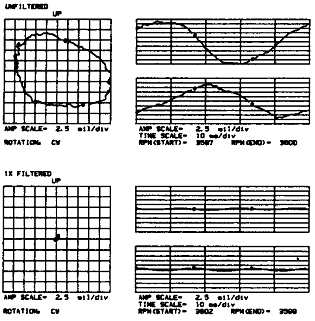
그림 7-1 1× 보다 적은 진동주파수를 지시하는 여러 개의 Keyphasor Mark를 보여주는
Orbit 및 Timebase Plot
진동 크기는 베어링의 전체 간극에 가까울 정도로 매우 높게 나타났으며, 진동주파수는 대략 1,300 cpm(회전축의 속도는 3,600 rpm)의 차동기 주파수가 주성분이었다. 기계가 병해되고 속도가 3,200 rpm까지 감속될 때를 나타낸 그림 7-2의 스펙트럼 Cascade Plot에서 이 일정 주파수를 관찰할 수 있다. 차동기 진동은 축의 속도가 3,400 rpm으로 감소됨에 따라서 사라졌다.
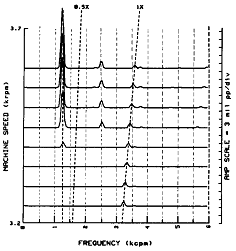
그림 7-2 감속시 회전속도가 3,400 rpm에 접근함에 따라 차동기 진동성분이 없어짐을 보여주는
Cascade Plot
상기의 정보가 MDS 사무실에 통보되었다. 약 1년전 그 회사가 Bently Nevada사의 터빈 감시장치(Turbine Supervisory Instrumentation, TSI)시스템으로 설비개선을 할 때, MDS는 그 회사로부터 기계 기동시의 기준 데이터를 연구해 달라는 주문을 받았다. TSI 시스템은 기계의 7개의 베어링을 각기 관찰하는 한 쌍의 XY Proximity Probe를 포함하고 있다.
기준 데이터는 발전기에서의 문제를 진단하는데 매우 유용하였다. 그림 7-3과 7-4는 발전기 내측 베어링에서의 Proximity Probe 신호중의 하나에 대한 기준 데이터의 연구로 부터 나온 Polar Plot과 Bode Plot이다. 이들 Plot은 Runout 보상이 이루어졌다. 즉 이들 Plot상의 각 점에서 Slow-Roll Residual Synchronous Runout Vector가 제거된 것이다.
그림 7-3과 7-4는 발전기 회전체/베어링 시스템이 2차 공진(임계속도)이상에서 운전중인 것을 보여준다. 이 시스템의 1차 공진은 1,300 cpm 바로 밑, 그리고 2차 공진은 2,800 cpm 근처이다.
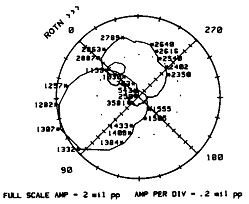
그림 7-3 운전속도가 2차 공진(임계속도) 이상임을 보여주는 Polar Plot.
그림 7-2의 차동기 진동주파수는 1차 임계속도와 일치한다 (기준 데이터).
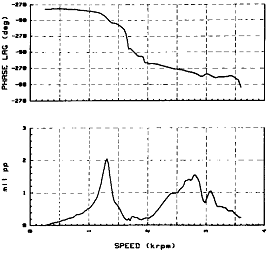
그림 7-4 상대적으로 높은 동기 증폭계수를 보여주는 Bode Plot.
이것은 계의 감쇠가 작다는 것을 나타냄 (기준 데이터).
1차 임계속도는 대략 9.4의 동기증폭계수로 약간 감쇠되어 있다. 이 증폭계수는 American Petroleum Institute(API)방법 또는 임계속도에서의 진폭을 임계속도가 지난 속도에서의 진폭으로 나누는, 전통적 방법에 의해 계산된 것이다. 기준 데이터 연구시는 차동기 진동성분은 없었다.
기준 데이터 연구정보와 가장 최근의 진동정보를 비교하여 볼 때, 기계가 ‘Oil Whip’ 상태에서와 같이, 1차 임계속도(Cylindrical Mode)와 같은 주파수에서 진동을 일으킨다는 것이 명백하였다. 이러한 분석이 1시간 내에 전화로 발전소장에게 통보되었고 기계는 손상없이 정지되었다.
정지중, Proximity Probe의 DC Gap Voltage 변화는 베어링 내에서 축의 위치가 수평중심보다 높다는 것을 지시하였다. 이러한 지시는 베어링에 부하가 적게 걸린다는 것을 의미한다. 조사결과 베어링 간극이 상한치에 근접하여 Oil Whip 불안정성을 야기한 것으로 나타났다.
기계 제작사의 Service 대표자는 유효 베어링 길이를 줄여(L/D비를 줄임) 베어링 단위 면적당 부하를 증가시키기 위해 발전기 베어링의 양단의 Babbitt를 1 inch 제거할 것을 권고하였다. 이 수정은 성공적이었다.
기준 데이터 연구는 다채널 F.M Tape Recorder와 컴퓨터화된 고속 데이터 정리의 이용으로 인해 경제적이었다. 과도상태에서 얻어진 Polar, Bode 및 Cascade Spectrum Plot과 정상상태하에서 얻어진 Orbit, Timebase, Spectrum Plot이 16시간의 작업시간동안 터빈에 있는 14개의 Probe에서 얻어졌다.
시간을 절약하기 위해 재생하는 동안의 Tape 속도가 실제 기동기간의 것보다 빨랐고, ADRE 2 Software는 주파수 교정을 수행하였다. 신호는 또한 진단장비에 적합하도록 증폭되었으며 Software는 다시 진폭 Scaling을 수행하였다.
Vector 보상은 Software를 통해 단 몇 초 이내에 이루어졌다. 그림 7-3과 7-4의 승속시 데이터는 기록속도의 4배의 테이프 재생속도로부터 산출되었다.
2. 유도 전동기 0.5X 차동기 진동 (Exact 50% Subsynchronous Vibration on Induction Motor)
이 사례에서는 대형 유도 전동기에 관한 기준자료를 구할 수 없었던 경우이다. Orbit과 Timebase Plot(그림 7-5)과 Spectrum Plot(그림 7-6)에 나타난 바와 같이, 상대축 진동은 높은 값에 이르렀다.
주된 주파수는 그림 7-5에서 Orbit 및 Timebase 신호상의 2개의 정지상태의 Keyphasor 표시로 금방 알 수 있듯이 이런 현상을 “Phase Locked”라 하며, 그림 7-5에 나타난 바와 같이 Orbit의 Loop를 이루고 있다. 이런 현상의 가장 주된 원인은 경미한 Rub 또는 과도하게 이완되었거나 간극이 너무 커진 베어링 때문이다.
높은 진동의 원인을 검증하고, 이에 따른 기계의 정지에 대한 권고를 뒷받침하기 위해서는 회전속도의 1/2과 같거나 작은 주파수라던가 또는 공진(임계속도)이 있었다는 것을 증명하는 것이 필수적이었다.
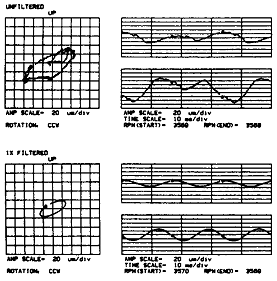
그림 7-5 Orbit과 Timebase Plot은 2개의 “Locked” Keyphasor 표시를 보여주며,
Orbit은 축 회전속도 진동주파수의 정확히 1/2(1/2×)를 나타내는 Inside Loop를 보여준다.
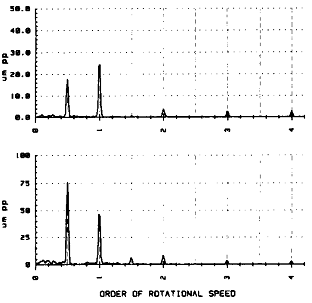
그림 7-6 스펙트럼 Plot은 1/2× 진동주파수를 나타내는 Orbit/Timebase 데이터(그림 7-5)와 일치한다.
기계는 정지되었으며, 정지과정이 기록되었다. 정지중의 기록은 현장에서 천천히 재생되었으며, 신호는 DVF 2, 오실로스코프 및 스펙트럼 분석기에서 관찰되었다.
관찰결과 공진(임계속도)이 회전속도의 1/2에 가깝다는 것이 나타났다. Tape에 기록된 데이터를 Polar Plot과 Bode Plot(그림 7-7과 7-8)에 정리하였다. 이들 Plot은 임계속도가 회전속도의 1/2에서 존재한다는 것을 보여주었다.
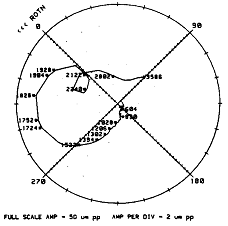
그림 7-7 회전속도가 1차 공진(임계속도) 이상이며, 공진이 회전속도의 1/2에서 발생함을
보여주는 Polar Plot (정지시의 데이터).
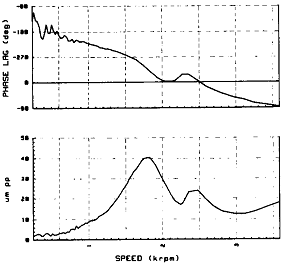
그림 7-8 1차 공진(임계속도)이 축 회전속도의 1/2이라는 것을 확인시켜 주는
Bode Plot (정지시의 데이터).
1차 임계속도가 정확히 회전속도의 1/2배일때, 이 현상은 회전속도의 정확히 1/2배에서 공진조건을 만든다. 이 상태가 차동기 주파수에서 정방향 세차운동(Forward Precession)의 특성이 있으므로 Rub에 의한 것이 아니라는 것을 이 Orbit Plot이 제시하고 있다.
Oil Whip과 비교하여 볼 때, 회전속도의 1/2에서의 공진의 양상은 가진을 일으키기 쉬우나, 그 최종결과는 축이 1차 굽힘 모드로 진동한다는 것이다.
그 유도 전동기는 180˚(Babbitt의 반) 원통형 슬리브 베어링을 사용하고 있었다. 이 베어링은 간극이 과도하게 크다는 사실이 조사되었다.
이 조사에서, 기계에 대한 진단과 권고사항이 컴퓨터를 통한 분석이 이루어지기 전에 제시되었다. 그러나, 컴퓨터에 의한 분석이 베어링을 조사하는 동안 수행되었다. 컴퓨터를 이용한 분석은 진단사항을 확증하고, 베어링 간극을 줄이는 것이 문제에 대한 정확한 해결책이라는 것을 검증하는데 필수적이었다.
3. 설계 문제로 인한 Oil Whirl (Oil Whirl Caused by Design Problem)
이 Turbo-expander는 44,000 rpm 근처의 회전속도로 운전되는 매우 작은 4.5 ㎏의 회전축을 가지고 있다. 회전축의 고속으로 인한 열의 제거를 위해 베어링을 통해 많은 윤활유 흐름이 필요로 하게 되었다. 3개의 나선형 홈이 베어링에서의 많은 윤활유 흐름을 용이하게 하기 위해 파여 있었다. 불행하게도, 이러한 베어링설계는 윤활유의 원주방향 흐름(소용돌이)을 유발하여, Oil Whirl에 의한 불안정성을 야기 시켰다.
이 새 기계를 기동하던중, 압축기와 터빈 사이의 축의 양끝에 설치한 Probe로부터 높은 진동이 관찰되었다. 컴퓨터를 이용한 해석결과 그림 7-9~7-11에 나타난 바와 같이 낮은 속도에서부터 정격속도까지 사이에서 가장 두드러진 주파수 성분은 축의 회전속도 주파수의 43%이었음이 나타났다.
Spectrum Cascade Plot(그림 7-11)은 기계가 높은 속도에 도달했을 때, Whirl 성분이 감소함에 따라, 잔류 불평형에 의해 야기된 1× 동기성분이 증가하여 탁월하게 되었다. 불평형에 의한 Oil Whirl의 억제는 특별한 것이 아니라는 사실이 논문에서 발표되었다.
이 Turbo-expander는 그림 7-12에 나타난 바와 같이 1차 공진(임계속도) 이하에서 운전되었다. 그러나, 약간의 위상변화는 시스템이 공진에 접근함에 따라 불평형을 증폭시킨 것을 나타낸 것이었다.
Oil Whirl의 진단은 회전체 역학을 연구하는 사람들의 관점에서 보면 간단한 것이었다. 그러나 기계 제작자에게 문제점을 납득시키기 위해 증빙서류가 필요하였다.
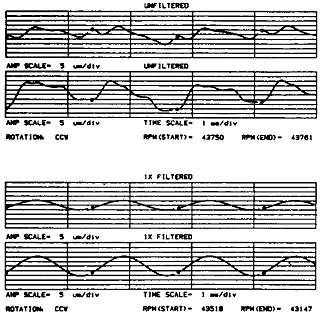
그림 7-9 1× 이하의 진동주파수를 나타내는 여러 개의 Keyphasor 표시를 보여주는 Timebase Plot.
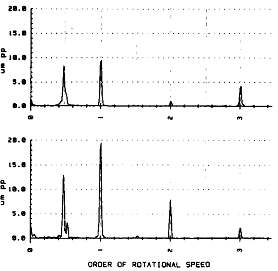
그림 7-10 1/2× 보다 약간 낮은 진동주파수의 존재를 확증하는 스펙트럼 Plot.
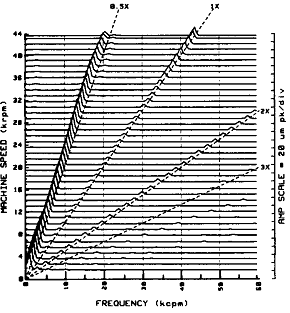
그림 7-11 기계가 정격 회전속도에 접근할때 1× 잔류 불평형 진동의 증가로 인해
0.43× 진동 진폭의 감소를 나타내는 Cascade Plot.
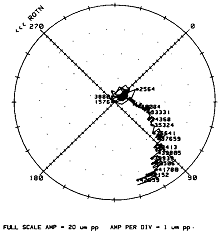
그림 7-12 기계가 정격속도에 이르렀을 때 위상변화는 공진에의 접근과 이로 인한
1× 불평형 응답의 증폭을 나타내는 Polar Plot.
기계의 가동중지로 인한 생산손실은 사업자에게 많은 금전상의 손실이므로, 문제를 빨리 해결하는 것이 요구되었다. 그림 7-11에 나타난 데이터는 기계제작자의 Service 대표자가 입회한 상태에서 MDS 사무실에서 정리되었다.
제작자는 베어링에서 나선형 홈대신 축방향의 직선 홈을 가공함으로써 문제를 해결하였다. (서로 반대방향으로의 나선형 홈들이 아마도 가장 좋은 해결책일 것이다). 그림 7-13의 Spectrum Cascade Plot은 새로운 베어링이 설치된 후 작성된 것인데 Oil Whirl이 제거된 것을 보여준다. 운전중인 유사한 설계의 여러 개의 다른 Turbo Expander도 유사한 경험을 갖고 있으나 진단이 이루어지지 않았다. 이들 기계에 축방향의 직선 홈을 가진 베어링이 설치되었더라면 문제는 해결되었을 것이다.
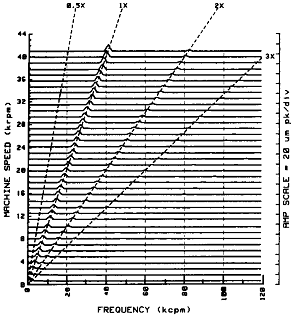
그림 7-13 베어링에 대한 수정이 좋은 해결책이었다는 사실을 증명하는
Oil Whirl 진동주파수의 사라짐을 보여주는 Cascade Plot.
4. 증기에 의한 Whip (Diagnosing Steam-Induced Whip on a Steam Turbine)
이 사례에 나타난 데이터는 이 프로젝트로부터 취한 데이터의 일부분이다. 이 정보의 양, 그 자체는 컴퓨터의 절대적인 도움으로 얻어진 것이다. 이 Plot들은 기계의 폭 넓은 분석으로부터 얻어질 수 있는 정보의 범위를 보여주고 있다.
Overspeed Trip 이 되었을 때, 이 압축기상의 터빈 구동부인 축의 상대 진동은 150μm p-p까지 상승하였다. 진동은 1차 공진 주파수로 차동기이었는데 이것은 Whip 상태에 있음을 나타낸다.
처음에는 구동기구(Driving Mechanism)가 베어링에서 있었는지, 아니면 Seal 또는 터빈의 다른 증기영역에서 있었는지 불명확하였다. 압축기로부터 분리되었을때 터빈의 불안정성을 크게 줄이기 위해 베어링이 수정되었다.
그러나, 터빈이 압축기와 결합되었을 때는 진동의 크기는 증기유량의 증가를 포함하는 어떤 운전조건의 변화에도 매우 민감하다는 사실이 명확하게 드러났다.
나타낸 데이터는 결합된 기계의 기동시와 2일전 터빈이 압축기에서 분리되었을때 정지시의 자료이다. 그림 7-14는 승속중 조속기 끝부분에 위치한 Outboard Proximity Probe 중 한 개로부터 얻어진 Spectrum Cascade Plot이다. 이 Plot은 그림 7-14에서 볼 수 있는 바와 같이 불안정의 시작이 매우 빠르고 그때의 주파수는 1차 공진(임계속도)인 대략 3,500 cpm과 같음을 보여주고 있다.
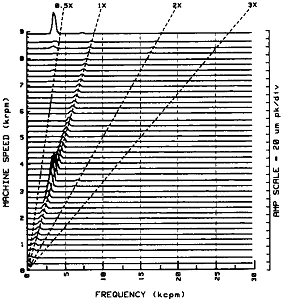
그림 7-14 승속시 차동기 진동이 매우 빨리 시작됨을 보여주는 Cascade Plot.
차동기 주파수는 1차 공진(임계속도)에 근접하여 일치한다 (결합상태의 경우).
그림 7-15와 7-16은 이 운전과정중 최대속도에서의 Orbit/Timebase Plot과 Spectrum Plot이다. Orbit을 컴퓨터를 통해 나타내는 것은 특히 유용하다. Plot 상의 Keyphasor 표시는 Orbit 이나 진동 사이클당 2회의 축 회전보다 약간 큰 것을 보여주는데, 이것을 오실로스코프상에서 실시간으로 관찰하기는 매우 어렵다.
Timebase Plot에서 Keyphasor 규약은 시간축 상에서 즉 왼쪽에서 오른쪽으로 “Bright Spot 앞에 Blank Space”가 있도록 나타낸다. 이 규약을 Orbit에서 적용해보면 반시계방향의 세차운동을 하는데 이것을 정방향 세차운동(Forward Precession)이라 한다. 즉, 축의 회전방향과 같은 방향으로의 세차운동이다.
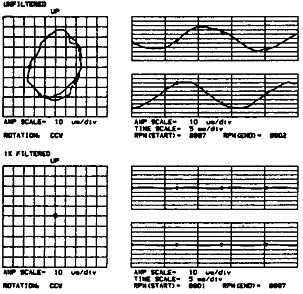
그림 7-15 진동 주파수가 1/2×보다 작음을 나타내는, 진동 사이클당 2개 이상의
Keyphasor 표시를 보여주는 Orbit/Timebase Plot.
Timebase Plot상의 Keyphasor 표시의 Blank/Bright Sequence는
Orbit Plot으로 전환되었을 때 축의 정방향 세차운동을 나타낸다.
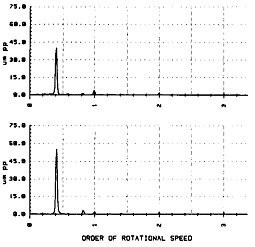
그림 7-16 우세한 진동 주파수가 1/2× 근처에서라는 것을 확증시키는 Spectrum Plot.
세차운동의 방향은 이 경우에서와 같이 공진이 불안정성에 의해 가진 되었는지, 아니면 Rub에 의해 가진 되었는지를 구분하는데 있어 중요할 수 있다. Rub는 역방향 세차운동(Backward Precession)을 일으킨다.
그림 7-17과 7-18은 같은 승속과정에 대한 Polar Plot과 Bode Plot이다. 이들 Plot에서 4.4μm의 Slow Roll Runout Vector가 공제(보상)되었다. 이 작은 양의 Runout은 축 표면의 상태가 매우 좋다는 것을 나타낸다. 보상된, 운전속도에서의 1× 진폭은 매우 작았는데(대략 5μm) 이것은 질 높은 Balance Quality임을 보여주는 것이다.
기동시, 기계는 2,000 rpm까지 너무 빨리 승속되었다. 그 다음, 500 rpm까지 속도를 내린 후 적당한 Slow-roll Time동안 유지되었다. 이런 기동형태는 축에 일시적인 잔류 휨(Residual Bow)과 이에 따른 불평형을 일으켰다. 기동시 얻어진 그림 7-17과 7-18, 그리고 정지시 얻어진 그림 7-19와 7-20의 저속에서의 데이터를 비교하여 보면 일시적 잔류 휨에 의한 기계의 응답을 알 수 있다. 대략 3,500 cpm 근처에서 1차 공진(임계속도)이 매우 명확하다. 기계가 결합된 상태에서의 진동 Plot과 분리된 상태에서의 진동 Plot은 단일 모드, 단일 자유도의 시스템의 응답으로 거의 교과서적인 형태로 나타나 있다.
그러나 이들 Plot 상에서 혼란을 주는 정보사항은 공진의 동기 증폭계수이다. 10의 값을 계산하기 위해 API 계산법이 사용되었는데, 이 10의 값은 회전체/베어링/지지 구조물의 감쇠가 매우 작다는 것을 암시한다. 감쇠가 작은 시스템에서는 증기의 원주방향 흐름에 의해 야기된 접선력(Tangential Force)을 받을 때 축은 불안정해지게 된다.
축과 지지물의 중량과 강성의 증가를 포함한 주요한 설계변경으로 결국 증기에 의한 Whip 문제를 해결하였다.
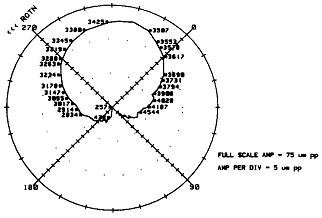
그림 7-17 운전속도가 1차 공진(임계속도) 이상이라는 사실과 공진이 높은
동기 증폭 계수를 갖는다는 것을 보여주는 Polar Plot (승속시의 데이터).
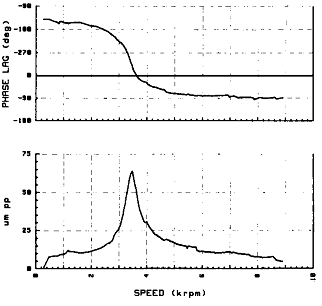
그림 7-18 회전축/베어링/지지 구조물이 약간 감쇠 되었다는 것을 나타내는
높은 동기 증폭계수를 보여주는 Bode Plot.
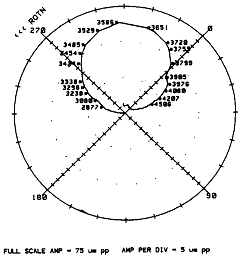
그림 7-19 축이 낮은 회전속도에서 승속하는 동안(그림 7-17) 관찰된 상당히 높은 1× 진동진폭이
나타나지 않음을 보여주는 정지시의 Polar Plot. 낮은 속도에서 승속시의 높은 1× 성분은
축의 일시적 잔여 휨을 야기하는 매우 빠른 가속의 결과였다.
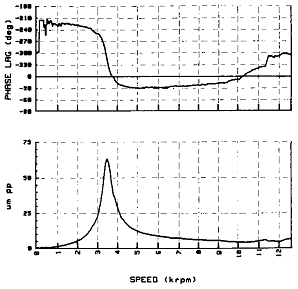
그림 7-20 낮은 회전속도에서 승속하는 동안(그림 7-18) 관찰된 상당히 높은 1× 진동진폭이
나타나지 않음과 높은 동기증폭계수를 보여주는 정지시의 Bode Plot.
5. 불안정성 발생 위치의 규명 (Defining the Source Location of Instability)
여기서는 회전기계의 로터에서 생기는 불안정성의 출처를 알아내는 방법을 정립하기 위하여, 유체 유도 불안정의 연산식을 직접 이용하는 방법에 대해 논하고자 한다. 이 새로운 회전기계 진단 기법을 현장에서 사용한 몇 가지 실례와 함께 기본적인 방정식도 언급한다.
우리 연구진의 최근의 발견으로 회전기계에서의 유체에 의한 불안정의 가능한 출처를 알아낼 수 있는 새로운 방법을 알게 되었다. 이것은 단순히 기계의 한쪽 끝에서 다른 쪽 끝까지 Rotor Whirl이나 Whip 진동의 상대 위상각(시간차)을 관찰해보면 된다. 일반적으로 이것은 어떤 기계의 반대편 양끝에 수직 또는 수평으로 설치된 변환기로 Whirl이나 Whip 진동의 위상각 차이를 관찰하여 알 수 있다. 이 위상각의 차이는 불안정이 발생되는 주파수(Whirl이나 Whip 진동 주파수만 Filtering하여)에서 측정되어야 한다. 이러한 측정은 Bently Nevada의 스펙트럼 분석기인 DVF 3 변환 함수 기능을 이용하거나, 오실로스코프의 변환기 신호로부터 표시되는 Timebase 또는 Orbit을 이용할 수 있다.
간단하게도 Whirl이나 Whip 진동이 일어나고 있는 기계의 한쪽 끝이 시간상(위상각상)으로 가장 빠르다면 Whirl/Whip 불안정성의 주발생원은 거의 이곳이 된다. 이는 Whirl이나 Whip 발생원의 에너지가 로터 시스템의 나머지 부분에서의 감쇠에 의해 점점 없어지기 때문이다. 동력학적 강성으로 표시하면 감쇠 성분의 일반적인 특성은 + jD(여기서 j = 이며, D는 감쇠를 나타냄)이다. +j는 각도가 90˚ 앞서 있는 것을 나타낸다. 축의 운동은 동력학적인 힘을 동력학적 강성으로 나눈 것과 같기 때문에 이러한 운동은 시간적으로 지연되며 따라서 위상각도 지연된다.
Seal이나 베어링(또는 기타 유체에 의해 위치가 정해지는 로터)에서 Fluid Wedge의 지지 강성은 일반적으로 Kyx와 Kxy로 이름 붙이고, 교차강성(Cross Stiffness)이라고 부르며, 이것은 감쇠 D, 회전속도 Ω, 유체의 평균 원주속도비 λ와 직접적인 관련이 있다. 특히 우리는 이 Wedge 지지 강성 성분을 -jλΩD라고 부른다. -j는 근본적으로 음의 방향(이것은 감쇠항의 반대방향이다.)인 Quadrature 강성항 때문이다.
만일 반경방향으로 정적 외력이 회전축에 가해지면, 축은 가해지는 힘의 벡터 방향과 동일 선상으로 움직이는 것이 아니라, 약간 편심되게 베어링이나 Seal내에서 회전하는 방향을 따라 옆으로 크게 움직인다. 이것이 바로 간단한(그리고 때로는 억제되지 않는) Servomechanism으로 표현되는 로터 시스템이 가해지는 정적 부하를 지지하기 위하여 Fluid Wedge를 형성하는 방식이며, 회전방향으로의 움직임은 각도 상으로 앞서게 된다. 따라서 가해지는 외력 값이 시스템의 강성에 움직임량을 곱한 값과 같아질 때는 강성항은 동일한 각도로 지연되어야 한다. 그러므로 Oil Wedge 지지항인 교차 강성(Cross Stiffness)은 자연히 음의 방향이 된다. 그림 7-21은 일정 회전속도와 교란 주파수에서의 직접적인 동력학적 강성과 Quadrature 동력학적 강성을 보여주는 전형적인 그림이다.
Whirl이나 Whip에 의해 생기는 힘을 결정하기 위한 다음 단계는 기계적인 강성은 보통 수동적(Passive)이지만, Wedge 지지항(이 에너지는 축의 회전에 의해 생긴다)은 능동적(Active)이라는 사실을 상기하는 것이다. 제어 이론 용어에서 -jλΩD와 움직임량을 곱한 값은 정확히 시스템의 Feedback Force를 의미한다(여기서 j는 교차 축방향을 나타낸다). Whirl이나 Whip 상태가 발생되면 Whirl이나 Whip의 실제적인 힘인 Fow는 Wedge 지지강성 D에 Whirl이나 Whip의 Orbit 반경인 Z를 곱한 값의 크기이다. 즉 Fow =λΩDZ가 된다. 강성의 비선형 부분은 각각의 λ비, 불안정원(Instability Source)에서의 감쇠항 D, 회전속도 Ω에 대한 z의 크기를 결정한다.
그림 7-22에서 간단한 로터 시스템에 가해진 이러한 힘 Fow에 대해 로터의 길이 방향을 따라 Whirl/Whip 성분의 상대 위상각 관계를 보여준다. 베어링에서의 움직임은 불안정 발생원에서의 움직임보다 Arctan 만큼 지연된다는 사실을 주목하라. 여기서 ω는 Whirl 또는 Whip 주파수이고, DB는 유막의 반경방향 감쇠, KS는 축의 강성, KB는 유막의 반경방향 강성이다. 좀더 복잡한 모든 시스템에서도 이와 똑같은 기본적인 특성을 가지고 있다.
발생원으로부터 멀어질수록 지연각이 증가하는 Whirl이나 Whip의 위상 지연을 관찰하는 방법은 연구실에서의 수많은 실험으로 확증되었다. 불안정성의 발생위치를 알아내기 위해, 이전에 기록된 수많은 불안정성의 경험사례들을 검토하였다. 그 결과는 다음 단락에서 설명될 것이다.
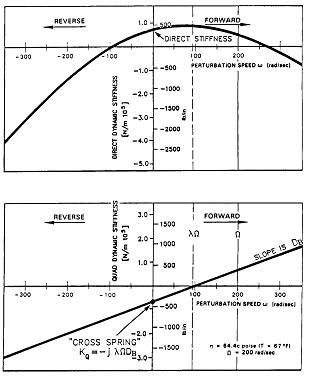
그림 7-21 Seal이나 베어링 유막의 동력학적 강성 대 정방향과 역방향 교란 주파수의 전형적인 그래프.
직접적인 동력학적 강성은 정적 반경방향 강성과 관성항을 포함하고 있고, Quadrature 동력학적 강성은
반경방향 감쇠와 Cross Spring항(축의 감쇠는 무시됨)을 포함하고 있다.
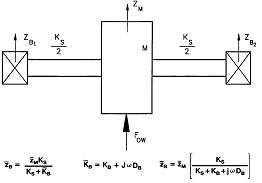
그림 7-22 Two-bearing Rotor Model
5.1 事例 1 (Case History 1)
150 ㎿의 전력을 생산하는 고압 터빈에서 높은 정방향의 차동기 진동(1× 이하 성분)이 발생하였다. 부하의 증가에 따라 그 차동기 진동의 크기와 주파수도 증가하고 있었으며, 이는 Steam Whip으로 확인되었다. 기동시 관찰한 결과 다음과 같은 사항들을 알게 되었다. 1차 공진(임계속도)은 1,470 rpm에서 일어나고 있었는데, 이 앞의 기록치를 보면 이 점이 1,750 rpm이었다. 1,470 rpm에서의 1× 진동치는 약 305 ㎛ p-p였으며, 이 또한 이전의 값보다 높은 값이었다. 가장 중요하다고도 할 수 있는 데이터는 축 중심선 위치 데이터에서 발견하였는데, 베어링 저널 근처에 설치되어 있는 Proximity 변환기의 데이터로 볼 때 베어링 내에서의 축의 위치 변화가 너무 컸던 것이었다. 그 변위량으로 볼 때 반경 방향 간극이 크게 증가했음을 알 수 있었다. 베어링 간극 증가로 그 베어링의 직접 동적 강성 특성(Direct Dynamic Stiffness Property)을 낮추는 효과를 가져 왔다. 1차 공진주파수가 1,750 cpm에서 1,470 cpm으로 줄어든 것은 바로 이 때문이며, 축도 불안정한 힘(Perturbation Force)들에 대항할 수 있는 안정성 여유가 매우 적은 위치에 있게 된다.
동기속도(3600 rpm)에서 50 ㎿까지는 주진동이 동기주파수인 3600 cpm에서 일어났다. 부하가 50 ㎿를 넘어서자 1,200 cpm에서부터 차동기 진동을 보이기 시작하였다. 부하를 증가함에 따라 차동기 진동의 주파수도 따라서 증가하였다. 이러한 상황은 Steam Whip 상태라고 판단되었다 (그림 7-23).
풀어야 할 마지막 의문은 그 진동의 근원에 관한 것이었다. 그 기계의 양 끝단 중 어느 쪽이 그 진동의 주원인 제공자인가를 알아보기 위하여 차동기 주파수에 대한 전달함수를 조사하였다. #1, #2 베어링에서의 위상차는 +30˚이었다. 이는 Steam Whip의 근원이 조속기의 반대쪽인 #2 베어링에 가까웠음을 분명하게 나타낸 것이다.
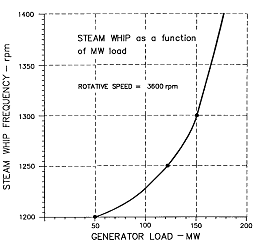
그림 7-23 Steam Whip 주파수 대 출력
5.2 事例 2 (Case History 2)
한 가스압축기의 고압측 압축기에서 차동기 유체불안정 진동이 발생한 일이 있었다. 현장 기술자들이 이 기계의 안정성을 회복시키기 위하여 수많은 일회용 조치들을 시행했었다. 이 불안정의 근원은 공기역학적 Whip에서 기인하는 것이었다. 최근에 그 당시 진동 데이터를 기록한 테이프를 다시 조사하게 되었다. 그래서 입구측과 출구측의 전달 함수를 비교 분석하는 작업을 수행하였다.
입구측과 출구측의 차동기주파수에 대한 위상차가 Whip 초기 발생 시인 0˚에서 Whip 진동이 심할 때는 +82˚까지 변하고 있었다. 이는 그 불안정이 그 압축기의 출구측에서 유도되었음을 분명하게 나타내었다. 정방향 Whip의 비는 저진동시 4000 rpm에서, 고진동시 6000 rpm까지 변하였다. 운전속도에 대한 백분율로 보면, 저진동시 45%, 중간 정도의 진동에서는 40%까지 내려갔다가 고진동/고회전 영역에서는 50%가 넘었다. 분해를 해 보니 가운데 Seal의 반경 방향 틈새가 3,810 ㎛이었고 베어링 근처에서의 축의 움직임이 190 ㎛ p-p였다. 그 당시에 이러한 정보가 있었다면 공기역학적 Whip에 대한 원인과 해결책이 보다 쉽게 나올 수도 있었을 것이다.
현재 이것과 같은 압축기열의 저압 압축기에서 높은 정방향 차동기 진동이 발생하고 있다. 이러한 불안정은 압축기가 10,600 rpm 이상으로 운전될 때 뚜렷하게 나타난다. 또, 이 기계의 정상운전속도는 11,300 rpm이며, 차동기 진동은 운전속도의 0.475× 주파수에서 발생하고 있다. 전달 함수를 분석한 결과 이 기계를 가로질러 +65˚의 위상차가 있음을 알았다. 이러한 위상차는 압축기의 입구측이 불안정 메커니즘의 근원에 가까웠음을 나타내었다. 그 압축기는 틸팅패드 베어링을 장착하고 있었다. 이러한 베어링은 고속압축기에 사용되는 경우가 많은 구조로써 베어링 내에서 발생하는 Whirl/Whip과 같은 메커니즘을 방지하여 줄 것이다. 따라서 유체불안정이 발생 가능한 근원은 입구측에 있는 Dynamic Seal을 조사해 보면 알 수 있을 것이다. 적절한 해결책이라면 그 같은 Seal에 현대식 Anti-swirling용 Seal을 채용하는 것이다.
5.3 事例 3 (Case History 3)
한 시멘트 공장내 가스터빈 구동 발전기는 기동시에 차동기 진동이 발생하였다. 차동기 진동은 가스터빈이 9,300 rpm에 도달하였을 때 발생하였다. 가스터빈의 통상적인 운전속도는 11,040 rpm이다. 차동기 진동 성분은 0.5×이었고, 시간이 경과하고 운전 온도가 상승함에 따라 그 크기는 감소하였으며, 진동발생 근원 규명을 위해 전달함수 분석을 실시하였다.
시험 결과는 흥미있는 것이었는데, 유체불안정이 처음 발생하였을 때, 초기 조사에서 가스터빈 입구 베어링이 유체불안정 발생원에 보다 가까운 곳으로 나타났다. 그러나, 부하와 온도가 상승함에 따라, 출구측 베어링이 불안정 원인에 더 가까운 곳으로 나타났다. 이 기간 중 가장 변화가 컸던 운전변수는 온도였다. 기계의 각 금속부위가 운전온도에 충분히 가까워지자 베어링 간극 또한 운전조건에 가까워졌다. 불안정 발생원이 입구측에서 출구측으로 바뀌는 것은 베어링 간극과 연관이 있을 것으로 생각되었다. 이후 기계적인 점검을 한 결과 베어링 간극이 설계치를 초과하고 있음이 판명되었다.
5.4 事例 4 (Case History 4)
160 ㎿ 발전기에서 기동시에 차동기 진동이 발생하였다. 3,000 rpm에서 불안정이 일어났는데, 차동기 진동 성분 주파수는 1,056 rpm이었다. 이러한 주파수는 발전기의 1차 공진점과 같은 것이었고, 발전기의 회전속도가 3,600 rpm으로 상승하였을 때에도, 불안정 주파수는 일정량 잔존하고 있었다. 이러한 형태는 이 것이 Oil Whip 유체불안정임을 암시하는 것이다. 계통에 병입하여 출력을 점차적으로 증가시켜도 발전기에는 여전히 불안정한 성분이 남아 있었다. 이러한 기간동안 윤활유 공급온도와 차동기 진동 성분의 감소 크기 사이에는 어떤 상관관계가 있음을 알았다. 3,600 rpm에 도달했을 때 윤활유 공급온도는 28˚C였고, 점차 윤활유 온도가 상승하여 46˚C에 이르자 불안정은 사라졌다. 이러한 상호관계가 몇 번에 걸쳐 확인되자, 기동 운전절차에 윤활유를 46˚C로 예열하도록 수정하였다.
공급 윤활유 온도는 유체역학적 베어링의 안정에 영향을 미치는 중요한 변수의 하나이다. 온도는 윤활유의 점도관계를 결정하며, 이는 다시 말하면, 윤활유의 Damping 특성에 영향을 끼친다는 것이다. 또한, 이것은 베어링의 기하학적 중심에서의 로터의 상대적 위치에도 영향을 주고 있다. 편심율이 높은 로터는 베어링 중심선과 로터 중심선이 일치하는 베어링보다 본질적으로 더 안정하다. 기계 구성도는 그림 7-24에 나타내었다. 각 기계의 구성 부품들 간의 시간/위상지연 상태를 알기 위하여 감쇠항의 영향과 불안정 근원의 관계를 실증하려고 5개 베어링 전체에 대한 전달함수 분석을 실시하였다. 그림 7-25와 7-26에서 이러한 전달 함수 분석을 보여주고 있다.
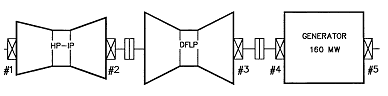
그림 7-24 기계 구성도
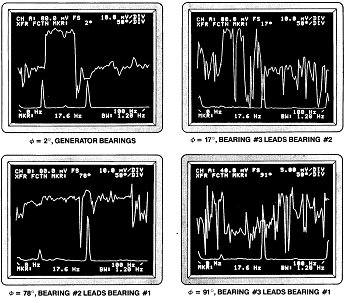
그림 7-25 #1~5 베어링의 Whip 진동 진단을 위한 전달함수 분석
(ΔΦ는 상대위상임).
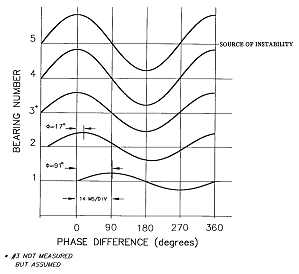
그림 7-26 그림 7-25를 간략화한 데이터. 기계의 Timebase 전달 함수
문제가 있는 기계에서 Whirl및 Whip진동의 시간/위상차를 알기 위하여 전달함수 기법을 이용하는 것은 불안정 발생원의 위치 해석에 있어 강력하고 새로운 기법임이 확인되고 있다. 불안정 현상이 가장 있을법한 근원을 정확하게 규명함으로써, 문제가 있는 부분에 중점을 둔 정비 및 교정조치가 가능해진다. 뿐만 아니라 이런 새로운 기술정보는 시험 및 설계 기술자들도 유용하게 사용할 수 있는데, 베어링 및 밀봉장치의 동적 강성과 유체취급 기계류의 동적 특성에 영향을 끼치는 유체/고체 상호작용의 이해를 보다 증진시킬 수 있기 때문이다.
6. 스톨영역 (Stall Zone)
Bently Nevada의 기계진단팀(MDS)은 최근 Gas Injection Process 프로젝트의 한 부분인 바렐 타입 다단 저압 압축기의 성능 시험에 대한 진동 진단 계약을 체결하여 API 기준과 계약자의 제원에 따라 시험을 수행하였다.
이들 압축기는 8단으로 구성되었고 입구 안내 베인과 디퓨져를 개량하여 가스터빈용 고압, 저압 압축기 모듈로 설계되었으며 Squeeze-Film 댐핑 베어링이 압축기 각단을 지지한다.
저압 압축기의 시험에서 정격(설계)부하보다 낮은 부하에서 차동기 진동 성분이 나타났는데 처음에는 차동기 진동의 가진원으로 베어링 유체에 의한 불안정성 Whirl 및 Whip)이 아닌 것으로 생각했다. 모든 상(Phase)에 대해 베어링 및 Seal Oil의 온도와 압력을 조정해 가며 시험한 결과 불일치되는 것은 없었으나, 현저한 차동기 진동이 베어링 유체의 Whirl 및 Whip의 전형적인 주파수인 0.35× 및 0.48× 주파수보다 낮은 저주파수에서 발생되었기 때문에 공기역학적 인자를 고려해야 했다.
진동 자료를 얻기 위하여 압축기 입구 및 출구 베어링에 레디얼 Probe와 입구측에 Thrust Probe를 설치하였고, 또한 진동 분석에 더 많은 도움을 얻기 위해 압축기 1단부터 7단까지 가스 입구 Loop와 출구 Spool에 특별한 압력 계측기를 설치하여 각단과 입구 Loop에서 실시간 압력 변화를 조사하였다 (그림 7-27).
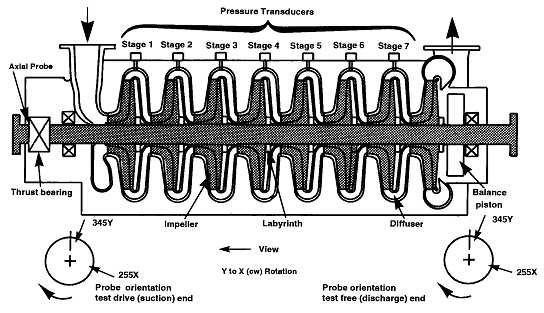
그림 7-27 압축기 단면도 및 Probe 설치 위치
1992년에 실시한 공장 성능 시험에서는 아무 이상이 없었으나 현장 성능 시험에서는 저압 압축기에서 불안정성 문제가 발생하였다. 원심 압축기의 유동 불안정에 대한 메커니즘은 일반적으로 공급받는 전력의 함수이며, 이것은 가스밀도, 몰 중량, 작용압력, 입․출구의 압력차와 관련이 있고 압축기에서 이러한 유동 불안정을 Surge 또는 Stall이라 부른다.
다음의 유체 동역학적 현상은 압축기 입구 공기량이 줄어들 때 발생할 수 있으며 아래와 같이 정의한다.
• Local Stall
임펠러 또는 디퓨져에서의 유동 분리(Flow Separation)를 말한다.
• Stage Stall
임펠러내의 한 지점에서 Local Stall이 증가할 때 역류가 발생하는 현상으로 전체적인 흐름은 압축되는 방향으로 흐른다.
• Stall Zone
원심 압축기에서 Stall의 징후가 명백하고 유동 교란이 일어나는 임펠러 또는 디퓨져 지역을 말한다.
• Surge
주기적인 유동 진동 및 압력 변동을 말하며 이러한 유동 진동이 역류를 유발시키 게 되면 이것을 Deep Surge라 한다. 또한 안내 날개 사이의 공간에 가스가 충분히 채워지지 않는 것을 Extreme Stall이라고도 한다. Surge는 축 방향으로 전파되어 나간다.
• Rotating Stall
Propagating Stall Zone이라고도 한다 (그림 7-28). Large Stall Zone으로 이루어지고 아주 낮은 Rotor Speed에서 원주 방향으로 전파되어 나가며, Stall Zone의 수와 전파율은 상당히 변화된다.

그림 7-28 Rotating Stall의 예
Stall과 Surge 현상은 압축기에 있어서 매우 위험한 것이다. 그 이유는
• Streamline Degradation으로부터 발생하는 로터 진동은 단락 사이의 레비린스 패킹을 손상시킬 수 있다.
• 유동 역류는 임펠러 베인 입구에서 계속적인 온도의 상승(토출 수두 저하)을 초래 할 수 있다.
• 입․출구 사이의 압력 변화는 추력의 변화를 가져오며, 따라서 추력 베어링의 손상을 초래할 수 있다.
• 갑작스런 부하와 속도의 변화를 일으킬 수 있다. 이것은 결정적으로 임펠러 및 다른 부속품에 영향을 미친다.
Stall의 징후와 진동 응답의 추적
이 압축기에서 경험한 공기역학적 Stall 현상을 정의하기 위해 운전 속도에서의 압력 변동과 Stall Zone에서의 압력 변화를 비교하였다.
다른 운전 속도에서의 압축기 토출량을 비교할 수 있는 비유량계수(Specific Flow Coefficient) Q/N(Gas Flow Rate/Operating Speed)값과 관련해서 Stall이 처음 일어났던 단을 조사하였으며, 또한 이 Stall이 단 전체에 퍼져 나가는데 걸리는 시간과 단에서의 압력변화의 크기 및 이에 대응하는 진폭을 조사하였다.
진동 응답과 압력 계측 정보를 기록한 후 108 Data Acquisition Instrument(108 DAIU)로 처리하였고 진동 진단 Software인 ADRE로 Diagnostic Plots를 만들었으며 Windows용 ADRE는 Microsoft Windows하에서 구동되는 강력한 진동 진단 소프트웨어다. 그림 7-29~7-32는 제4단에서의 Stall을 보여주는 Time-mapped Spectrum Waterfall이다. 이 4단은 압력차가 증가한 맨 처음 단이며, 이것은 횡진동 응답 Plot에서 관찰된 차동기 가진과 밀접한 관계가 있다.
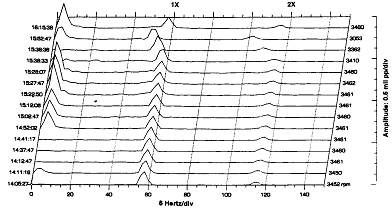
그림 7-29 출구측(Free End) 수평 방향 Probe에서의 Spectrum Waterfall Plot.
Stall 및 4 ㎐ 차동기 진동 성분의 징후가 현저하게 나타남 (운전 속도=57.7 ㎐)
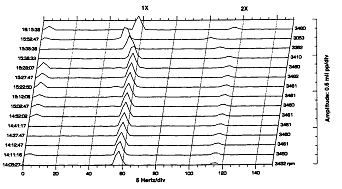
그림 7-30 구동측 수평 방향 Probe에서의 Spectrum Waterfall Plot. Stall 및
4 ㎐ 차동기 진동 성분 출현 징후가 있음 (운전 속도=57.7 ㎐)
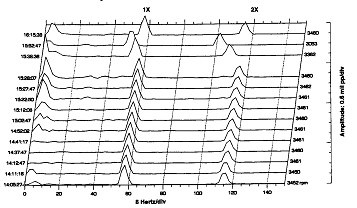
그림 7-31 Thrust probe에서의 Spectrum Waterfall Plot. Stall의 징후와 4 ㎐
차동기 진동 성분이 현저하게 나타남.(운전 속도 = 57.7 ㎐)
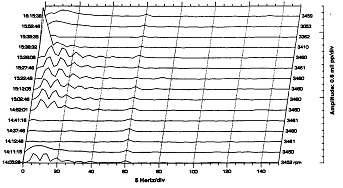
그림 7-32 4단 압력 변환기에서 Stall의 징후가 나타난다.
또한 압력과 진동응답 추적에서는 4단에서 Stall이 발생한 직후 6단과 3단에서 동시에 나타났고, 잇따라서 5, 7, 2, 1단 순으로 발생하였으며 Q/N값의 감소와 함께 대부분의 내측 단에서 첫 Stall이 나타났다. 여기서 흥미있는 것은 3, 4, 6단은 동일하게 설계되었고 Stall 징후를 일으키는 첫 단이라는 것이다.
가장 큰 압력변동은 6단에서 0.26~1.0 bar까지 거의 4배 증가하였고 그 외 다른 단에서는 3 : 1 정도의 증가를 나타내었는데 이러한 압력 변화는 기계적 안정에 큰 영향을 미치기 때문에 매우 중요하다. 그것은 운전속도 주파수(57.7 ㎐)의 7%(4 ㎐) 근처에서 차동기 진동을 야기 시키며 특히 출구측(Free End)에서 진폭이 크게 된다.
여러 단에서 Stall이 심하게 나타날 때는 4 ㎐에서의 진폭은 38 ㎛까지 크게 되는데 이것은 운전속도(1×)에서 보다 거의 3배이상 큰 값이다. 이 압축기는 내부 간극이 매우 작아 44~51 ㎛의 진동은 래비린스 밀봉장치를 손상시킬 수 있기 때문에 시험중 진동이 매우 높게 나타나는 것을 보고 즉시 압축기를 정지시켰다. Drive End Vibration은 체결효과(Coupling Effect)로 인하여 진동이 낮아지고 Drive End Stages는 Stall에 덜 영향을 받는 것으로 나타났다. 이것은 아마도 Balance Piston의 안정효과 때문인 것 같다. 이러한 현상은 Hydrocarbon(High Horsepower and High Pressure)시험 중에는 현저하게 나타나진 않았으며, 저압 압축기는 터빈/압축기 모듈로 연결되어 있다.
Stall이 발생하는 동안에 한단 또는 그 이상의 단에서 압력이 점진적으로 증가하는 것으로 나타났다. 따라서 로터의 안정성은 임펠러와 디퓨져의 공기역학적 환경과 베어링, 축, 다이아프램의 강성관계에 지배를 받는다. 입구가스 유동 조건의 조절이나 또는 압축기 내부 요소의 설계 변경은 이들 두 인자의 선택에 따라 압축기 성능에 큰 영향을 미친다. 사실 차동기 진동은 설계 변경에 매우 민감한 것으로 나타났는데 이것은 후에 압축기 내부 요소를 설계 변경 해봄으로서 사실로 입증되었으며, 입구 안내 베인, 밸런스 피스톤 형상, 디퓨져, 래비린스의 개선은 진동응답의 변화를 야기 시킨다. Stall의 전형적인 저주파수 진동 외에 여러 설계 형태의 분석을 통해 2800 cpm 부근에서 로터의 첫 공진을 재가진하는 다른 차동기 진동 요소가 있는 것을 알았다.
Stall이 발생될 때의 Orbit 및 Timebase Plot에서는 어떤 흥미로운 현상을 보여준다 (그림 7-33, 7-34). 이 Plot는 시계 방향의 축회전과 No Stall에서 Surge 발생까지의 진동과정을 나타내고 있다. 이 Plot에서 유니트가 불안정할 때 격렬한 반응이 나타난 것을 알 수 있으며, 가스 압력 증가와 갑작스런 로터의 증․감속에 따라 맥동 영향이 Stall과 Surge에서 명백하게 나타나 있는 것을 볼 수 있다. 출구측 수평방향 Probe에 나타난 진동진폭은 정상상태에서 Surge상태에 이르기까지 20 ㎛에서 40 ㎛까지 증가하였고, 구동측 수평방향 Probe에서는 단지 21 ㎛에서 25 ㎛로 증가하였다. Stall 증상은 사용자가 규정한 제한치인 전체 진동 29.7 ㎛ p-p보다 더 큰 진폭에서 설계 유량점 아래에서 잘 일어나므로 이 유니트는 부적합한 것이다. 임펠러 설계에서 충분히 발달한 Stall 상태로 수행한 여러 번의 시험에서 3:1의 단락 압력 변화비는 Free End Radial Probe에서 전체 진동의 2:1 증가와 일치하였다. 같은 기계적 조건하에서 압축기 속도를 바꿔 가며 시험함으로써 정상 운전 조건중에 압축기를 시험할 수 있고, Stall 발생중에 가장 나쁜 진동 상태를 예측할 수 있다는 것을 알았다. 그러나 Thrust나 Drive End Radial Probe 때문에 같은 조건하에서 동일한 비교를 할 수가 없었다.
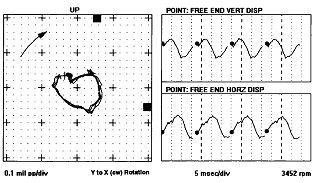
그림 7-33 정상 운전시 자유단에서의 Orbit 및 Timebase Plot
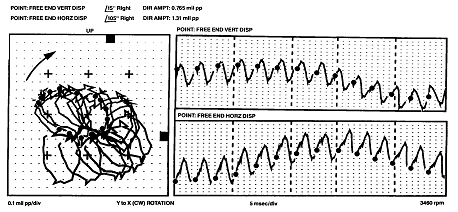
그림 7-34 Orbit 및 Timebase Plot은 회전하는 로터의 전체 움직임을 잘 나타내고
Keyphasor Dots는 Orbit 및 Timebase Plot에서 저주파 성분이 나타남을 보여준다.
가스 유량이 감소될 때 한 단에서 가스 밸브 조절에 따라 2~3초간 Stall이 발생되는 것이 관찰되었으며, 이와 같은 거동을 각단에서 여러 운전 속도에서 시험하였다. 마지막으로 Stall에서 벗어난 더 높은 유량 계수나 안정 영역으로 이동시켰다. 또한 불안정에 관해 압력과 관련된 Hysteresis Effect를 관찰하였다. 일단 몇몇 단에서 Stall이 발생하면 유동이 불안정하게 되는데 걸리는 시간보다는 안정한 상태로 복귀될 때 더 많은 시간이 걸린다.
임펠러나 디퓨져에서 Stall Flow의 변질성이 혼합된 영향을 압축기 성능 커브(그림 7-35)에 나타내었다. 여기서 각 단에서 감소된 출력을 반영하고 있는데 이것은 시험중에 Flow/Isotropic Head Data를 Plot하는 과정에서 발견하였다.
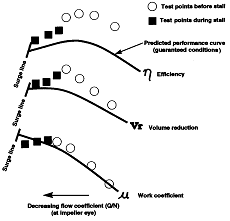
그림 7-35 압축기 성능 곡선
결 론
기계 제작자는 Stall 유량 범위, 기계적 형상, 진동 특성, Q/N의 관계를 면밀히 검토하였으며 이러한 정보는 최적 설계와 신뢰성을 향상시키는데 이용되고 있다. 임펠러나 디퓨져에서의 Stall의 구분은 다른 참고문헌에서는 물론 이 프로젝트 결과에서도 명확하게 정의하지 못하였다. 그러나 어떤 중요한 Rotating Stall은 Surge 발생에 앞서 일어난다는 것이며, 이것이 심해지면 압축기와 구동부품들을 손상시킬 수 있다는 것이다.
성능시험에서 유량의 감소에 따라 가스평균 속도와 유체입구 각도가 감소하는 것으로 나타났으며 이것은 레이놀드수, 운동에너지, 압력비, Surge Margin등을 상당히 변화시킨다. Stall 방(Cell)은 저주파 가진이 되는 특별한 위치에서 형성되는데 이는 운전속도의 7% 근방에서 일어나는 것을 알았다. 압축기 베어링의 형상에 따라 축과 씰 및 로터의 강성 특성이 변화될 수 있으며, 이것은 다른 차동기 진동요소에 가진을 유발시킬 수 있고 또한 안정성을 저하시키기 때문에 바람직하지 못하다.
Stall 발생중의 압력 측정값은 단(Stage) 압력과 진동변화에 따른 압축기 로터의 거동을 이해하는데 아주 중요하다. 압축기의 부품 변경에 대한 영향을 평가함으로써 Stall Zone의 특성을 더욱 잘 알 수 있었으며, 이에 따라 OEM은 Balance Piston, Labyrinth, Eye Seal을 개선하여 압축기의 성능을 향상시켰다.
진동 이외의 데이터는 여러 계측장치를 208 DAIU에 연결하여 ADRE에서 적절하게 Scale하여 수집하였다. 이것은 압력, 유량 등 여러 인자를 환산 Factor 없이 직접 구할 수 있게 해준다. ADRE for Windows Software는 보관된 ADRE 3 Database를 쉽게 검색, 정리 및 분석을 할 수 있어 여러 가지로 유용하게 해준다.
7. BFP 수력 강제진동 (Hydraulic Force Vibration in a Boiler Feed Pump)
7.1 背景 (Background)
화석연료를 사용하는 한 공장에서 각 기계에 대한 컴퓨터 베이스 진동 프로그램의 시행과 완성, 초기 기준 자료의 수집 및 기계 상태에 대한 기준 자료의 보고서 제출을 기술지원팀에 조사의뢰 하였다.
이 급수 펌프는 터빈 구동 가변속도 기계로 터빈, 펌프 모두에 슬리브 베어링이 장착되어 있고 각 베어링에서 측정한 최근(8월 16일) 진동값은 그림 7-36과 같다. 이중 몇 개는 경보치를 상회하고 있었다.
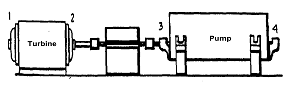

그림 7-36 보일러 급수펌프의 최근 진동 측정치
7.2 結果 (Results)
그림 7-37~7-40은 내측(위치 3) 및 외측(위치 4) 펌프 베어링에서 수평 및 수직 방향의 진동 스펙트럼이다. 각 진동 스펙트럼에 상당히 큰 진폭의 5×RPM 조화파가 실려 있음에 유의하라. 5×RPM 주파수는 그 당시에는 정확한 Impeller Blade 개수를 몰랐었지만 Blade 통과주파수(BPF)라고 믿었다. 그림 7-37, 7-38 및 7-40은 15×RPM(또는 3×BPF)인 100,350 cpm 주파수가 우월하였다. 그림 7-37과 7-38을 비교해보면 100,350 cpm에서 수직 방향의 값이 0.3 in/sec로 수평 방향의 값인 0.273 in/sec 보다 약간 높지만 거의 같다. 그러나 그림 7-39와 7-40을 비교해 보면 100,350 cpm에서 수직방향 진폭이 수평방향 진폭보다 수배 높은데 이는 100,350 cpm에 가까운 수직 방향의 고유 진동수가 외측 펌프 베어링에 존재하는 것을 암시하는 것이다.
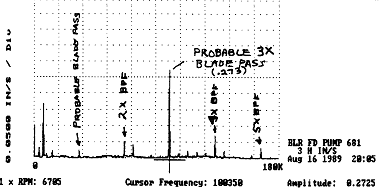
그림 7-37 위치 3H에서의 진동 스펙트럼
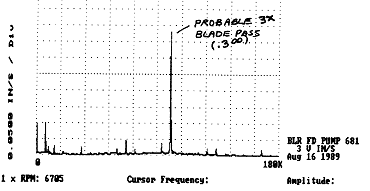
그림 7-38 위치 3V에서의 진동 스펙트럼
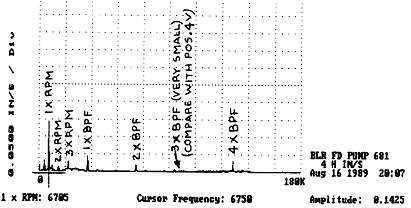
그림 7-39 위치 4H에서의 진동 스펙트럼
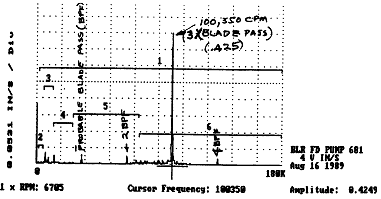
그림 7-40 위치 4V에서의 진동 스펙트럼
7.3 結論 (Conclusions)
① 임펠러가 5개의 베인을 가졌다면 유동과 관련된 문제점은 Blade 통과 주파수의 배수 고조파에 의한 것을 의미한다. 유동의 문제점은 유동의 억제(Elbow, 밸브, Reducer, 저항물체 등), 하우징 내에서 임펠러의 편심위치 및 회전 베인과 정지체인 디퓨져 베인간의 불균일한 간극 때문이다. 임펠러 베인의 개수를 확인할 필요가 있다.
② 100,350 cpm인 3×BPF에서 수직 방향의 고유 진동수는 외측 펌프 베어링(위치 4)에 존재했을 것이다. 시스템의 고유진동수도 Blade 통과주파수(BPF)나 고진동을 일으키는 BPF의 고조파와 때때로 일치한다.
7.4 勸告事項 (Recommendations)
① 임펠러 베인의 개수를 확인할 것.
② BPF 고조파와 모든 속도에서 예상한 고유진동수를 계속 추적할 것.
③ 터빈속도가 변할 때 15×RPM 주파수에서의 진폭을 추적할 것. 만일 100,350 cpm이나 그 부근에서 수직방향의 고유 진동수가 실제로 있다면, 특히 위치 4V에서 15×RPM의 심각한 진폭 변화가 있을 것이다.
8 냉각수 펌프 케비테이션
Cavitation Diagnosis within a Chilled Water Pump
8.1 背景 (Background)
냉각수 펌프들에서 여러 해 동안 케비테이션 문제점들이 있었다. 분명히 펌핑 시스템은 처음부터 설계가 잘못되었거나 펌핑 시스템에 유해한 영향을 미치는 변수가 있어 케비테이션을 일으킨 것이다. 이 조사의 목적은 실제 문제점의 근원을 확인하는 일과 권고 조치 사항을 제출하는 것이었다.
8.2 結果 (Results)
케비테이션을 일으키는 펌프에서 어려운 점은 그 상태가 실제로 펌프내부 부품을 손상시키는 케비테이션 문제인지 또는 보다 즉각적인 영향을 가지는 베어링 문제인지를 확인하는 일이다. 4호기 냉각수 펌프가 바로 이러한 경우이다. 펌프 베어링의 전체 Spike Energy 준위와 Velocity Band 경우가 경보치를 넘나들었는데 이는 구름 베어링의 문제점인 것으로 나타났던 것이 실제로는 케비테이션이었다.
그림 7-41은 4호기 냉각수 펌프 배열도이며, 기준값을 초과한 내측 펌프 베어링에서 취한 전형적인 진동 스펙트럼과 베어링 결함 주파수(또는 그 조화파) 또는 Blade 통과 주파수 일수 있는 몇 개의 Spike가 포함되어 있다. 그림 7-41에서 광대역 Energy가 14,000~44,000 cpm 사이에서 탁월한데 이는 케비테이션이거나 구름 베어링 수명의 최종 단계를 의미할 수 있음에 유의하라. 그림 7-42의 위 두 그림은 두 개의 펌프베어링(위치 3과 4)에서의 모든 방향의 진동 스펙트럼이고, 아래 그림은 Spike Energy 의 경향도 이다. 이 문제점이 케비테이션 때문이었는지 또는 베어링 마멸 때문이었는지를 결정하는데 이들 그림들은 도움이 되지 않았다.
도움이 된 것은 그림 7-43과 7-44의 Waterfall Velocity Spectrum 이었다. 각 점에서 Waterfall Spectrum은 최소한 1년 이상동안 동일한 모양을 가지고 있었다. 만일 문제점이 베어링 변형에 의한 것이라면 1년 이상 운전하였으면 손상이 발생했던지 적어도 더 악화되었을 것이다. 스펙트럼간에 실제적인 변화가 분명하지 않았기 때문에 케비테이션이 거의 문제점이었다.
도움이 될만한 또 다른 사실은 일반적으로 동일 축에 두 개의 베어링은 동시에 같은 비율로 손상이 발생하지 않는다. 이 경우에서도 마찬가지로 두 개의 베어링이 1년 이상이나 동일 변형상태로 있을 수가 없었을 것이다. 케비테이션을 의미하는 또 다른 강력한 실마리는 펌프의 소음이었다. 케비테이션은 기계가 깨끗한 액체 대신에 모래나 자갈을 펌핑하는 소음을 발생한다. 이 경우에 이러한 소음이 여러 번 발생했다는 사실을 진동 분석가가 서류화하여 제출하였다.
이러한 상황에서 있을법한 가능성 있는 문제는 윤활부족이다. Spike Energy 값은 윤활되지 않은 구름 베어링의 부품운동에 민감하다. 그러나 그것이 윤활 문제라면 펌프 베어링은 피로 손상없이 거의 2년 동안 계속해서 운전할 수 없었을 것이다.
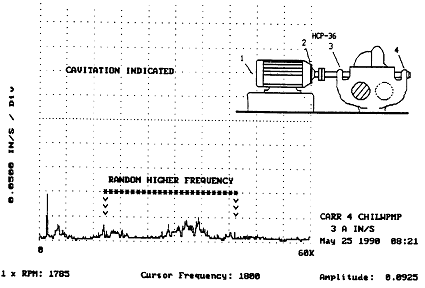
그림 7-41 4호기 냉각수 펌프의 진동 스펙트럼(위치 3)
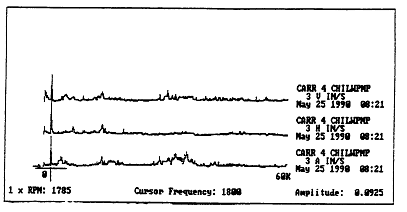
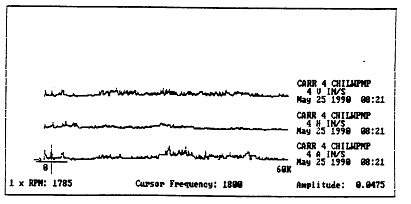
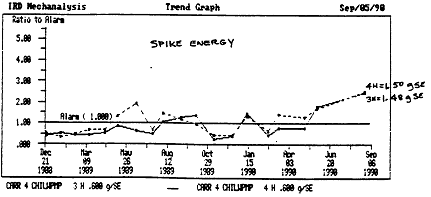
그림 7-42 펌프 베어링에서의 진동 스펙트럼(위치 3과 4)
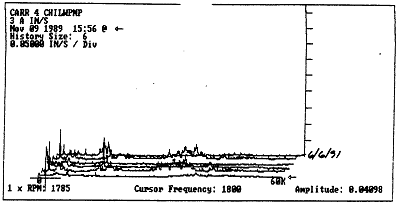
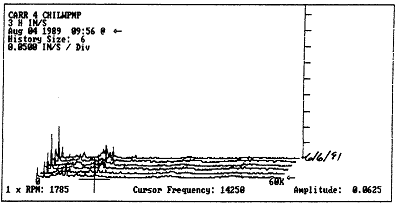
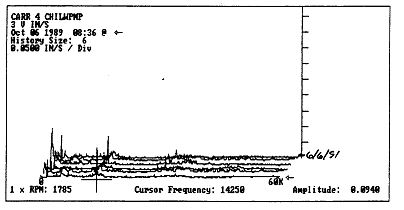
그림 7-43 위치 3에서의 Waterfall Plot
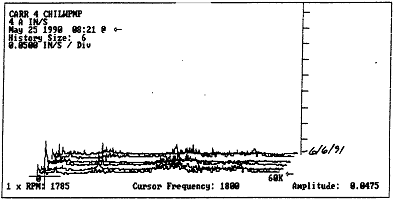
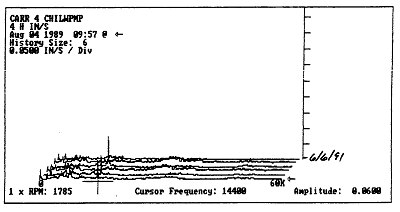
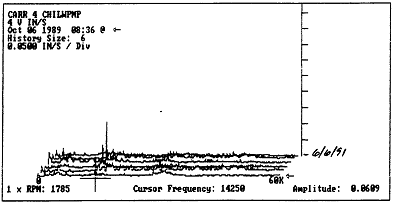
그림 7-44 위치 4에서의 Waterfall Plot
8.3 結論 (Conclusions)
① Velocity Band Alarm과 Spike Energy Alarm에 의해 검출된 문제점은 케비테이션에 의한 것으로 진단되었다.
② 교정되지 않은 그러한 케비테이션은 결국에는 펌프내부 부품과 심지어는 연결 배관에 큰 손상을 일으킨다.
8.4 勸告事項 (Recommendations)
계속되는 케비테이션 문제의 근원을 밝히고 이것을 제거하는 조치를 취할 것. 각종 밸브들이 적절하게 작용하고 있는가를, 흡입 배관에 방해물은 없는가를 확인할 것. 또한 펌프성능 한계를 넘어서 운전하고 있는가를 확인할 것.
9 터빈 베어링 Dry Oil Whip
Detection of High Vibration due to Dry Oil Whip at Turbine Bearing
9.1 運轉狀況 (Operating Status)
보령화력 발전소 6호기의 터빈 발전기(베어링 배열도 참조)는 건설 이후 첫 번째 Overhaul 작업을 수행하였는데, 주요 작업은 저압 터빈(#A)의 #3 베어링 교체와 터빈 발전기의 축정렬이었다. 한편 각 베어링에서는 Dual X, Y Probe가 설치되어 있어 축진동 및 케이싱 진동을 감시할 수 있으며, 베어링 메탈 온도 및 배유 온도도 감시할 수 있는 설비를 갖추고 있다.
터빈을 기동한 결과 약 40시간 운전후(‘95. 11. 8) 저압 터빈(#A) #3, 4 베어링 진동 진폭(Peak to Peak)이 각각 98 ㎛에서 138 ㎛로 또 45 ㎛에서 86 ㎛로 약 40 ㎛ 정도 상승하여 현장에서 베어링 유압 조정 및 운전 모드(부분분사 및 전주분사 방식) 변경 조치로 한시적으로 안정되는 듯 싶었으나 같은 현상이 계속 발생하였다.

그림 7-45 터빈 베어링 배열도
9.2 터빈 諸元 (Turbine Specifications)
• 터빈 출력 : 500 ㎿
• 터빈 형식 : 초임계압 충동 4류 재열 재생 복수 터빈
• 주증기 압력, 온도, 유량 : 246 ㎏/㎠, 538℃, 1,720 t/h
• 터빈단수 : HP-7, IP-5, LP-6 × 2
• 추기단수 : 8단
• 진공도 : 722 ㎜Hg
9.3 振動 特性 (Vibration Characteristics)
(1) 진동 현황
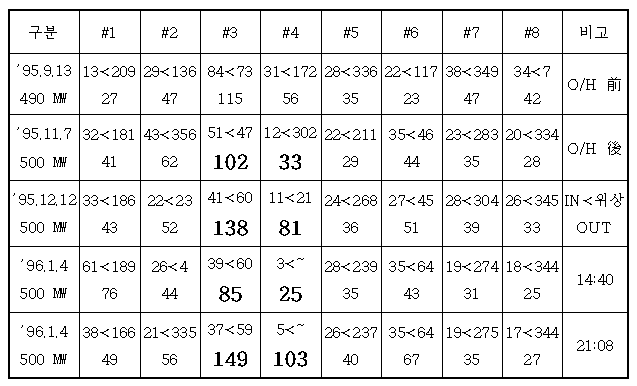
∙ 저압터빈(#A) #3, 4 베어링 외의 다른 베어링의 진동은 양호함.
∙ #3 베어링의 진동은 시간의 경과와 더불어 102 ㎛ → 138 ㎛ → 149 ㎛로,
#4 베어링의 진동은 33 ㎛ → 81 ㎛→ 103 ㎛로 급격히 악화됨.
∙ 동일 운전조건에서도 #3 베어링의 진동은 순간적으로 85 ㎛ ↔ 149 ㎛로,
#4 베어링의 진동은 25 ㎛ ↔ 103 ㎛로 변동됨.
(2) 베어링 금속 및 배유온도 현황
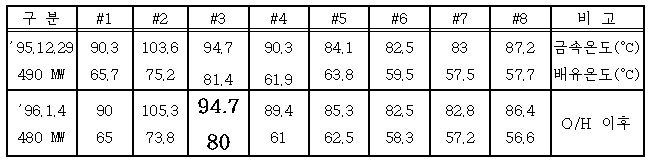
∙ #3 베어링의 금속 및 배유온도가 Overhaul 전보다 후에 5℃ 상승하였음.
(3) #3, 4 베어링의 진동 특징
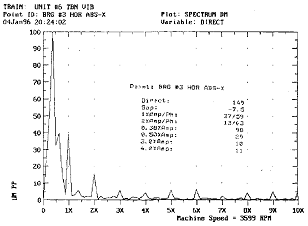
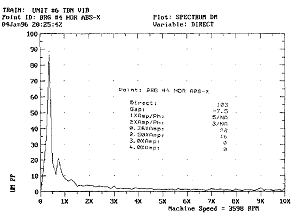
그림 7-46 #3(위), #4(아래) 베어링의 진동 스펙트럼
① 진동 주파수 성분
∙ Subsychronous 성분 (0.38×, 0.77×)이 아주 우세함.
∙ #3, 4 베어링 외의 다른 베어링 진동주파수 주성분은 Synchronous 성분 (1×RPM)임.
② 1× 성분의 Orbit 형태
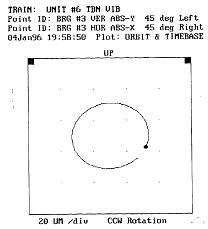

그림 7-47 전형적인 모양을 가진 #3(위), #4(아래) 베어링의 Orbit
③ 진동 Trend
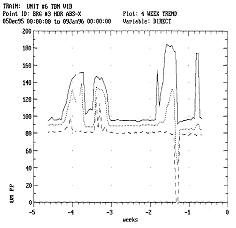
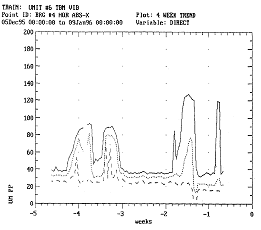
그림 7-48 #3(위), #4(아래) 베어링의 4주간의 진동 경향도
∙ 4주 Trend(’95. 12. 5~’96. 1. 9) : 운전조건의 큰 변화없이 #3 베어링은 최대값으로 100 ㎛에서 150~180 ㎛로, #4 베어링은 최대값으로 40 ㎛에서 90~120 ㎛로 증감 변동함.
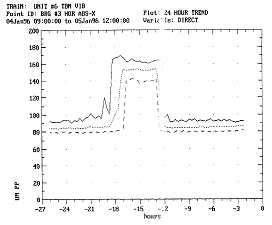

그림 7-49 #3(위), #4(아래) 베어링의 24시간 진동 경향도
∙ 24시간 Trend(’96. 1. 4. 09:00~’96. 1. 6. 12:00) : 운전조건의 큰 변화없이 #3 베어링은 최대값으로 100 ㎛에서 160 ㎛로, #4 베어링은 최대값으로 40 ㎛에서 110 ㎛로 증감 변동함.
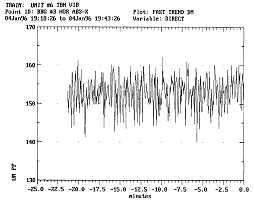
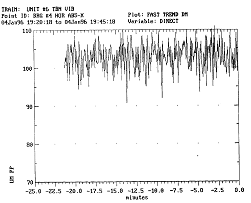
그림 7-49 #3(위), #4(아래) 베어링의 진동 변화 상태도
∙ Fast Trend(’96. 1. 4. 18:26~’96. 1. 4. 19:43) : 운전 조건의 큰 변화없이 #3 베어링은 최대 진동변동폭 15~20 ㎛로, #4 베어링은 최대 진동변동폭 10~15 ㎛로 Hunting함.
9.4 診斷 結果 (Diagnostic Results)
저압터빈(#A)의 불안정 진동의 원인은 베어링 온도 상승 및 우월 진동주파수 성분이 0.38×으로 보아 #3 베어링으로의 윤활유 공급 부족으로 인한 유체 불안정(Dry Oil Whip)에 기인한 것으로 판단되었다.
9.5 措置 結果 (Results of Corrective Actions)
(1) 임시 조치 및 결과
① 운전변수 조정
터빈 운전상태 하에서 베어링 메탈의 고온과 Oil Whip에 의한 고진동을 저감시키기 위해서는 윤활유의 압력 또는 온도 조정, 주증기 또는 재열 증기의 온도 조정 및 복수기의 진공도 조정에 의한 운전중의 Rotor Alignment 상태를 변화시켜 베어링 부하를 설계치에 가깝도록 유지시키는 것이다. 따라서 다음과 같이 운전변수를 조정하였더니 유체 불안정 현상이 소멸되었다.
∙ 재열 증기온도 하향조정 : 538℃ → 520℃
∙ 터빈 Hood온도 상승조정 : 34℃ → 40℃
② 임시 조치후 진동 현황
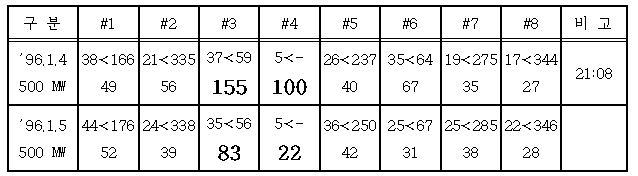
∙ 조치후 #3 베어링 진동은 155 ㎛ ↔ 83 ㎛로, #4 베어링의 진동은 100 ↔ 22 ㎛로 Step증감 반복되다가 Oil Whip 현상이 소멸되고 저압터빈의 진동이 낮은 값에서 안정화됨.
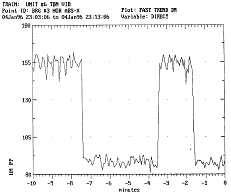
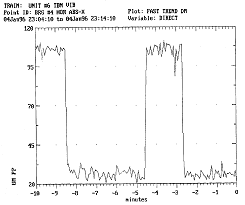
그림 7-50 Oil Whip의 발생과 소멸이 반복되고 있는 #3, 4 베어링의 진동 스펙트럼
③ 진동 주파수 성분 및 진동 변동폭
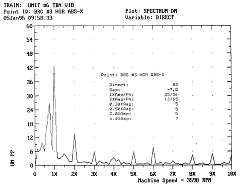
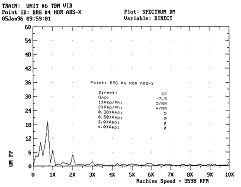
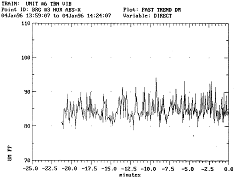
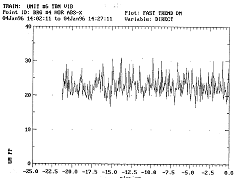
그림 7-51 0.38× 진동 주파수 성분이 소멸되고, 변동폭도 10 ㎛미만으로 다소 안정화된 진동 스펙트럼
(2) 근본조치
임시 조치로 운전해 오다가 설날 연휴기간(96. 2. 16~96. 2. 21)을 이용하여 #3 Tilting Pad 저널 베어링을 정밀 점검하여 근본 조치함.
① 점검결과
• Tilting Pad 베어링의 모서리부에서 접촉흔적이 있었음.
• 베어링 전 Pad(6 ea)의 Contact이 약 40%로 불량함(80%이상이면 양호)
• Tilting Pad 선단부 Rounding처리는 4.5R로 미흡(설계치는 9.5R임)
• 하부 좌측 Tilting Pad 고정핀 Hole이 편마모되고 고정핀이 절단됨.
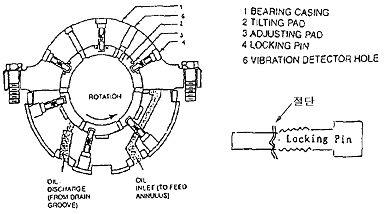
② 점검 결과로 본 진동의 원인 검토
Tilting Pad 저널 베어링은 Self-Align되는 가장 안정성이 좋은 베어링 형식으로 유체 불안정 진동이 발생되지 않는 장점이 있다. 그러나 Tilting Pad 저널 베어링인 #3 베어링의 유체 불안정 진동 원인은 Pad 선단부 Rounding처리가 4.5R로 미흡하게 되어 베어링 Pad로의 윤활유 공급 및 배유 부족으로 ,즉 #3 베어링으로 윤활유가 적게 공급되어 베어링 온도가 Overhaul 전보다 5℃ 높아지고, 이 윤활유 공급부족 및 베어링 Contact 불량으로 인해 Oil Whip현상이 발생되었다.
또한 Tilting Pad 형식인 #3 베어링이 원활히 Self-Align(Tilting)되지 못하여 최소 유막 두께부가 형성되는 하부 좌측 Tilting Pad의 고정핀 Hole이 고정핀에 의해 편마모되고, 또한 고정핀도 절단된 것으로 판단되었다.
③ 정비 내용
• 베어링 전 Pad의 Contact를 80%이상으로 수정함.
• 모든 Pad 선단부(즉 Pad로의 윤활유 입출구부)를 Rounding 개선 조치 하고(4.5R→9.5R) Locking Pin Hole이 손상된 하부 좌측 Pad 및 Locking Pin을 교체함.

④ 정비후 시운전 현황
진동현황
임시조치시 조정한 운전 변수들을 모두 정상으로 하고 기동한 결과 진동 상태가 다음과 같이 감소되었다.
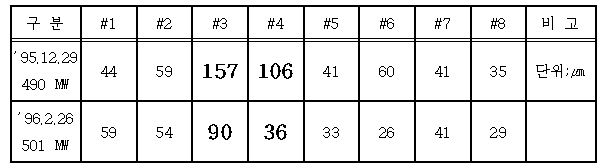
∙ #3 베어링의 진동은 157 ㎛→90 ㎛로, #4 베어링의 진동은 106→36 ㎛로 개선됨.
베어링 온도 현황
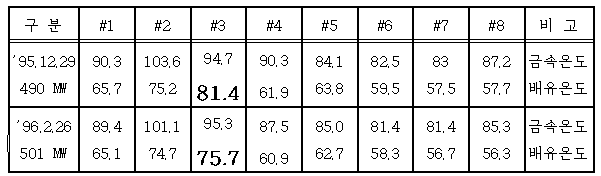
∙ #3 베어링의 금속온도는 거의 변화없으나 베어링의 배유온도는 81.4℃→75.7℃로 낮아짐.