Shaft Crack Problems
2. 원자로 재순환 펌프 축 균열 (Reactor Recirculation Pump Shaft Crack)
3. 원자로 냉각수 펌프의 진동 진단 (Diagnosis of Problems on a Reactor Coolant Pump)
1. 보일러 급수 펌프 축균열 (Vibration Analysis Techniques used to Detect a Rotor Crack on a Boiler Feedwater Pump)
석유 화학 설비에서 운전중인 급수펌프의 축 균열 검출에 필요한 정보를 진동 분석 기술로 수집하여 운전중 축 파괴로 인한 정지 가능성을 피했다.
전체 진동값, 1× 진폭 및 1× Slow Roll 진동 데이터는 축 균열을 검출하고 진단하는데 가장 유익한 정보를 제공한다. 이 예에서는 축 균열을 검출하는데 사용된 진동 분석 기술을 설명하고자 한다.
공장내에는 동일한 중간 크기의 보일러 급수 펌프 3대가 있었다. 이 펌프중 두 대( #1과 #3)는 축 손상을 경험했으며 축 손상으로 펌프의 고정 및 회전 부품에 상당한 손상을 입었다.
진동진단 회사의 MES(Mechanical Engineering Services)는 #2 펌프 상태를 조사하도록 의뢰 받았는데 그 펌프는 축 균열 현상 발생은 없었으나 고진동 이력이 있었다.
과도상태 자료를 수집하기 위해 #2 펌프를 정지 및 재 기동하기로 하고 축 균열로 수리한 실적이 있는 #3 펌프를 재기동 하였으나 기동 후 얼마 되지 않아 #3 펌프에 비정상적인 진동이 나타났다.
비정상 진동 원인을 분석하기 위해 MES는 #3 펌프를 기동, 정지 및 부하 상태에서 진동 시험을 실시했다.
세 펌프는 토출 압력 18,300 ㎪, 43 ㎥/hr의 용량을 가진 14단 보일러 급수 펌프로서 구동 전동기는 1650 HP, 3560 rpm의 직접 연결식 유도 전동기이다.
펌프는 그림 13-1에 나타낸 바와 같은 방향으로 구동단(D.E.)과 비구동단(N.D.E.)에 축 변위 Probe가 설치되어 있고 하나의 와전류 변위 Probe가 축방향 위치를 측정하기 위해 비 구동단측에 설치 되어있다.
#3 펌프의 전체 진동값이 뚜렷이 증가하는 것을 데이터에서 보여준다.
진동 분석 시험에 앞서 #3 펌프 전체 진동 데이터를 40시간 동안 기록하였으며 축의 축방향 위치 측정은 수동으로 기록했다. 그 결과(그림 13-2) 진동 감시 기간 마지막에서 진동 변화율 증가와 더불어 전체 진동치가 급격하게 증가하는 현상이 구동단에서 나타났다.
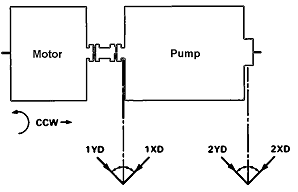
그림 13-1 축진동 Probe 설치방향을 나타내는 보일러 급수펌프 배열도
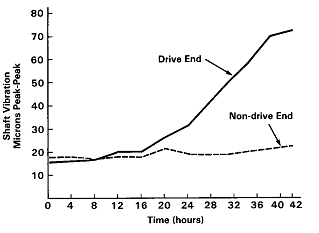
그림 13-2 급수 펌프의 진동 경향도
기동중 펌프 축의 급속한 가속 때문에 기동시의 과도상태의 1× 진폭과 위상 자료는 의미가 없어 정지시의 과도상태 자료를 기록하고 분석하였다.
그림 13-3, 13-4는 정지시 구동단과 비구동단에서의 상대 축진동의 Polar Plot이다.
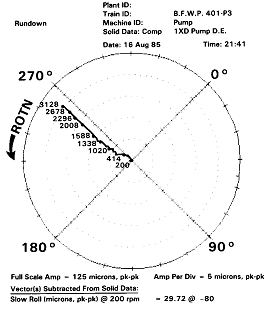
그림 13-3 정지시 구동단의 Probe(1XD)에서 취한 Polar Plot
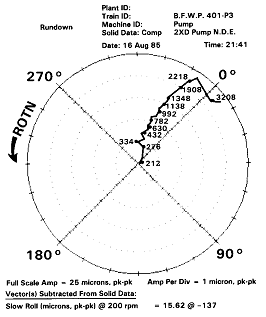
그림 13-4 정지시 비구동단의 Probe(2XD)에서 취한 Polar Plot
축이 휘고 Preload를 받고 있음을 Slow Roll 데이터에서 보여준다.
200 rpm시 구동단 X와 Y Probe에서 수집한 Slow Roll 진동값은 각각 248˚ 및 80˚에서 14.99 ㎛와 29.72 ㎛이었고, 비구동단 X와 Y Probe에서 수집된 Slow Roll 진동값은 각각 137˚ 및 295˚에서 15.62 ㎛와 9.27 ㎛이었다.
건설시 펌프에서의 전형적인 Slow Roll 벡터는 Probe가 지시하는 축 표면에서의 기계적 Runout와 축의 잔류 굽힘에 의해 약 5 ㎛ 정도이어야 한다. 그러나 측정된 진동 값은 15~20 ㎛ 이었으며 축의 기계적인 휨을 나타내는(그림 13-5) D.E.와 N.D.E.에서의 위상각은 거의 동상이었다. 또한 X와 Y Probe 방향에서의 진폭이 같지 않은 것은 Preload가 높은 것을 나타낸 것이었다.
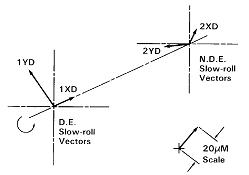
그림 13-5 2000 rpm에서 취한 Slow Roll Vector
펌프 정지시의 자료로는 확실한 결론에 도달할 수 없음.
정지시 진동 위상각 변화는 약 500 rpm 이상에서 D.E.와 N.D.E.측 모두에서 약간 발생했다.
그림 13-6의 예에서와 같은 Cascade Spectrum Plot은 정지시 정보로부터 수집된 것이며 비구동단에서의 진동 주성분은 1× 회전 주파수이었다.
약 2000 rpm에서 2× 성분이 약간 증가하는 현상이 구동단의 X, Y Probe에서 관찰되었으나 이 정보(그림 13-6) 만으로는 확실한 결론을 이끌어 낼 수가 없었다.
더 많은 정보를 얻기 위해 펌프를 재기동 함
보다 많은 정보를 수집하기 위해 펌프를 재기동 하였으며 정상 운전 속도에서 약 40분간 운전했다. 그림 13-7, 13-8의 Orbit과 Timebase Plot은 펌프 정지 직전까지 기록 됐다.
진동 진폭은 비구동단에서 보다 구동단에서 훨씬 높았다. 구동단에서의 필터 되지 않은 Orbit은 수평축 상에서 타원형이며 Orbit의 상부는 평평하게 나타났다.
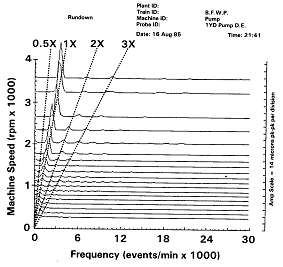
그림 13-6 Probe 1YD에서의 Cascade Spectrum Plot
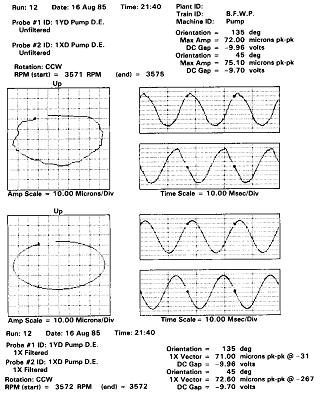
그림 13-7 구동측에서의 전체 및 1× Orbit 및 Waveform
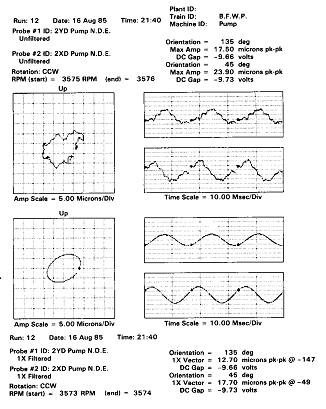
그림 13-8 비 구동측에서의 전체 및 1× Orbit 및 Waveform
1× 진동 진폭이 높고 증가함
Slow Roll 값을 보상한 후 구동단에서 기록된 실제 1× 진동 진폭은 각각 84.7과 102.5 ㎛이었다. 이 진동치는 이전에 측정된 값보다도 높고 허용치를 초과하였기 때문에 점검을 위해 펌프를 정지하기로 결정했다.
축 균열 진단 : 펌프 특성
대부분의 다단 펌프에서는 내측 단과 케이싱 끝 밀봉부를 통과하는 유체의 누설 때문에 댐핑이 높게 나타난다. 사실 펌프의 밀봉 장치는 축을 구속하고 지지해주는 베어링역할을 한다. 펌프 설계자는 적은 Seal 간극이라도 반드시 정상 운전중에 Rub를 일으키지 않음을 보증하기 위하여 Seal에 의한 “베어링 효과”를 고려하게된다.
긴 다단 펌프 축의 수력학적인 설계상 스핀들 직경이 제한되고 임펠러 축 방향 길이가 주어 주기 때문에 축은 아주 유연하다. 10단 이상인 펌프는 긴 탄성 축을 갖는 것이 필수적이다.
때때로 Seal은 차동기 진동을 일으키는 축의 불안정성의 원인이 될 수 있다. 이것은 Seal 내의 유체 막이 베어링 내에서와 같이 작용하기 때문에 일어날 수 있다.
1차 임계속도를 증가시키는 펌프의 Gland로부터의 전체적인 강성효과에 추가하여 임펠러 내에서 유체의 동적 영향으로 펌프 운전동안 로터의 강성을 증가시키거나 구속하려는 경향이 있다.
공기중에서 운전하는 펌프축은 운전속도 이하의 속도에서 1차 임계속도를 가지지만 지지대로 작용하는 Gland의 영향으로 1차 임계속도를 운전속도 훨씬 이상으로 증가시킨다.
그럼에도 불구하고 시스템 내의 감쇠치가 아주 높으면 1차 공진속도의 상부측이 운전 속도 범위까지 끌어올리게 된다. 달리 말하면 펌프 Gland는 상당히 낮은 속도까지 떨어트리는 펌프 축의 동역학적 특성에 중요한 영향을 준다. 그러나 시스템 내의 감쇠치가 높으면 질량 불평형 값이 적절한 경우 진동 응답이 적게 나타나게 된다 (그림13-9).
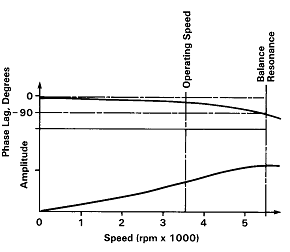
그림 13-9 운전속도 이상에서 발생하는 크게 감쇠된 임계속도를 나타내는 Bode Plot.
그러나 다단 펌프의 특성은 펌프가 구동기에 연결될 때는 변할 수 있다. 이러한 불확실한 특성은 통상적으로 펌프의 구동단에 큰 Overhung Mass에 의해 생긴다. Overhung Mass는 커플링에 큰 처짐을 주어 펌프축의 Bending Mode에 영향을 줄 수 있다. 이로 인해 Balance Sensitivity가 크게되고 구동단에서 허용될 수 없는 진동치를 갖게된다 (그림 13-10).
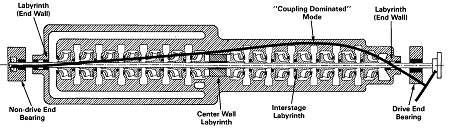
그림 13-10 펌프 축의 커플링 불평형 Mode
진동 가능 원인
펌프의 구동기에서 진동 문제의 원인이 될만한 가능성이 거론되었다. 그러나 이 문제는 정지중에 관측된 진폭과 위상 응답에서 어떠한 공진 응답도 나타나지 않았기 때문에 제외되었다. 정지중 3560 rpm~500 rpm에서의 위상 변화는 특히 적었다.
속도를 증가시켰을 때 D.E.와 N.D.E.단 끝에서 나타난 진동 진폭은 원심력에 대해 비공진 응답이 회전 속도의 자승에 비례하여 증가했다. 이러한 1× 진동 성분의 원인은 질량 불평형이나 축의 기계적인 휨으로 결론지었다. 앞의 2일 동안에 걸쳐 관찰한 진동의 급속한 증가(그림 13-2)는 질량 불평형의 급격한 증가가 원인이 아님을 암시했다. 대단히 크고 점진적인 진동 변화가 축에서 발생한다는 사실이 납득하기 어렵기 때문에 질량 불평형의 급격한 변화는 진동 상승의 원인에서 제외했다.
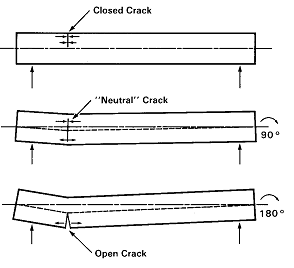
그림 13-11 1× 진동주파수를 가지는 축의 처짐의 변화를 일으키는“Shaft Crack”의 도해
관찰된 1×와 2× 성분의 진동 특성
질량 불평형을 진동 상승 원인에서 제외했기 때문에 큰 기계적 굽힘이 축에 발생하여 빠른 속도로 그 굽힘이 증가되고 있다고 결론 지었다. 관찰된 1× Slow Roll 진폭과 위상관계가 실제로 축이 휘었다는 사실을 확신시키는데 도움을 주었다 (그림 13-5).
두 대의 다른 펌프 축도 균열로 인해 이미 손상된바 있기 때문에 #3 펌프 로터는 진동 시험중에 균열이 급격하게 진전 됐다고 신속하게 결론을 내렸다. 축에서의 횡방향 및 반경 방향 균열의 영향은 비대칭 강성을 초래하여 중력을 발생시키고 축의 정적 처짐 곡선(그림 13-11)의 1회전당 1번 변화를 가져왔다. 이러한 변화는 축이 회전할 때 1× 성분을 가진시킬 수 있다. 비록 정보가 빈약하였지만 낮은 값의 2× 성분의 가진을 정지시 구동단의 Cascade Spectrum Plot(그림 13-6)에서 관찰할 수 있었다. 2× 진동 Peak 치는 2300과 1800 rpm 사이에서 발생되었음이 나타났다. 그 진폭은 2100 rpm에서 가장 높았지만 단지 10 ㎛(Peak-to-Peak)에 불과하였다.
1차 공진이 약 4400 rpm 부근에 있었고 균열에 의해 비대칭 강성 상태이었고 중력의 작용으로 축의 1차 공진이 다시 가진되어 2× 진동 성분이 더 높아졌을 가능성이 있다.
중요한 점은 2200 rpm의 실제 펌프 속도에 관련한 수력학적 강성 상태하에서는 1차 공진이 4400 rpm에서만 발생된다는 것이다. 3560 rpm의 운전 속도에서는 수력학적인 강성이 증가되어 1차 공진이 4400 rpm 훨씬 이상의 속도로 증가할 것으로 예상되었다. 정지시 비구동단에서의 Bode Plot(그림 13-12)을 살펴보면 3000과 3560 rpm 사이에서 위상 지연이 약간 증가하는 것이 나타난다. 이러한 증가는 축이 매우 높게 감쇠된 1차 공진 영역에 들어섰다는 것을 나타낸다.
축 균열 : 축 휨의 원인과 비슷함
여러 정보는 축이 확실히 휘었다는 것을 나타냈다. 횡방향 및 반경 방향 균열은 펌프 축에서의 기계적인 휨 발생과 매우 유사하다.
균열이 성장함에 따라 스핀들의 응력 감소로 스핀들이 휘게되고 균열 표면이 떨어지게 된다. 균열이 축의 정상상태 응력을 이길 만큼 충분히 크면 휨은 더욱 증가한다.
축 균열 확인
검사시 구동단 Gland 부싱(그림 13-13) 내에서 축 균열이 확인되었다. 실제로 축은 후에 제작사로 반출되는 동안 두 조각으로 깨어 졌다. 운전중 파괴되는 손상이 가까스로 면했다.
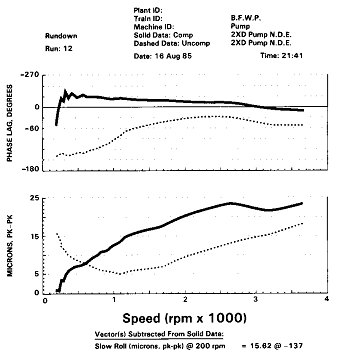
그림 13-12 정지시 비 구동측에서 Probe 2XD의 Bode Plot
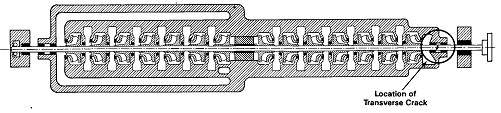
그림 13-13 구동측 Labyrinth에서 축의 횡방향 및 반경방향 균열 위치
피로, Misalignment가 주된 원인
균열 성장의 메커니즘은 주기적인 응력에 의한 피로임이 분명하였다. 펌프 조립과 설계에서 몇 가지 관련된 특징이 나타났는데 펌프 Seal과 베어링의 복합적인 Misalignment와 구동축과 펌프간의 외부적인 Misalignment가 이런 문제를 일으켰음을 나타내고 있다.
그러한 환경하에서는 펌프축은 가압된 케이싱(즉 케이싱 양 끝단 Seal 사이의 로터 Span) 내에서 매우 크게 구속된다. 그러나 구동측에서 Seal을 벗어난 축은 구속되지 않으며 Misalignment에 의한 힘에 의해 휘어질 수 있다.
결과적으로 굽힘 모멘트는 구동측 Seal의 내측에 집중되어 균열이 성장할 가능성이 있다.
또한 케이싱 비틀림에 대한 몇 가지 증거가 발견되었다. 이러한 비틀림은 내부Seal간의 Misalignment의 위험을 증가시키고 펌프 케이싱 내에서 축의 Preloading을 더욱 발생시킬 것이다.
2. 원자로 재순환 펌프 축균열 (Reactor Recirculation Pump Shaft Crack)
이 사례는 원자로 재순환 펌프 및 전동기를 중대한 위험에서 구한 기록이다. 1989년 5월 1일에서 11일 사이에 유체 베어링(Hydrostatic Bearing)의 전반적인 구역에서 펌프 축을 통하여 균열이 진전되었다. 740 마력의 전동기로 구동되는 각각의 원자로 재순환 펌프는 분당 170,325 리터의 물을 원자로의 노심으로 공급할 수 있다. 원자로 재순환 펌프는 Proximity Probe를 사용해 상대 축 변위, 축 방향 진동 그리고 축의 회전 속도를 측정 감시한다. 또 이 펌프들은 토출량, 베어링 온도 그리고 전동기 권선 온도를 감시한다.
5월 11일, Grand Gulf 원자력 발전소의 진동 엔지니어는 연속적으로 감시되는 모든 중요 회전기계에 대해 정기적인 모니터링과 진동 점검을 수행하였다. 이 정기적인 모니터링과 진동 점검을 하기 위해 진동 감시 설비에서 Unfiltered 및 Filtered Orbit과 전체 진동 진폭이 이용되었다. 모든 진폭은 유사한 운전 조건하에서 관찰된 2주전의 진동 데이터와 거의 똑 같았다.
그러나 반시간 뒤 #B 원자로 재순환 펌프에서 Orbit의 모양이 바뀌었다. 그리고 펌프 커플링에 설치된 Proximity Probe의 진폭이 330 ㎛ p-p에서 406 ㎛ p-p으로 증가했다. 30분 후에는 펌프 커플링에서 진동은 457 ㎛ p-p에 도달하였다. 전동기 Inboard/Outboard 베어링 및 축 방향에 설치된 모든 Proximity 변환기도 마찬가지로 진동이 상승한 것으로 나타났다. 이 기간 동안 진동 엔지니어는 진동 상승 원인이 운전 조건의 변화 때문에 생기는 진동인지를 확인하기 위하여 진동 주파수 스펙트럼 데이터와 운전과 관련된 진동 데이터를 수집하였다.
운전 데이터와 결부시킨 진동 스펙트럼 점검결과 진동 상승의 원인은 운전 조건 때문이 아니라는 것을 확인하였다. 펌프를 정지해야하는 긴박한 문제라고 확신한 진동 엔지니어는 진동 계측용 테이프 기록계에 양쪽 재순환 펌프의 진동 신호를 기록하기 시작했고 #B 재순환 펌프에서 높은 진동이 발생하고 있다는 것을 제어실의 운전원에게 통보하였다.
진동 벡터 데이터는 1×, 2× 주파수에서 진동이 심각한 위상각 변화와 함께 증가한 것으로 나타났다. 반시간 후 진동 레벨은 위험 설정치인 508 ㎛ p-p 이상 증가하였다. 운전원은 진동 상승 추세를 줄이기 위하여 유량 조절 밸브를 조정했다. 이러한 노력은 효과가 없었으며 진동은 762 ㎛ p-p으로 증가했다. 축 Orbit 변화가 시작된 세시간 후 저속에서 펌프는 안전한 상태가 되었고 펌프 커플링의 총 진동 진폭도 279 ㎛ p-p로 감소하였다. 진동 데이터를 재검토하고 더 수집하기 위한 시간을 벌기 위해 진동 감시와 이완 부분에 대한 감시를 계속하면서 펌프를 저속으로 운전하였다.
다음날 진동 데이터를 검토한 결과 펌프가 손상을 입은 것이 뚜렷했고 저속 운전일지라도 더 이상의 운전은 적절하지 못한 것으로 판단되었다. 펌프를 정지하고 진동, 이완 부분의 “소음” 그리고 운전 중 데이터를 주의 깊게 재검토했다. 진동 데이터를 검토한 결과 과도한 진동의 원인은 펌프의 축 균열이나 축 휨으로 판단되었다.
육안 점검결과 여러 가지가 드러났다. 첫째 임펠러가 부착된 바로 위 테이퍼진 부분의 원주방향 약 320˚ 부근에서 축 균열이 발견되었다. 둘째 유체 베어링 상부 360˚ 위치에서 마찰 흔적이 있었고 저널은 130˚ 위치에서 마모된 흔적이 있었으며 마지막으로 축은 축 중심선에 대하여 굽었다.
2.1 再循環 펌프의 配置 (Recirculation Pump Arrangement)
#A, B 원자로 재순환 펌프의 일반 배치도는 그림 13-14에 나타내고 있으며 임의의 0˚ 기준에 관하여 두 로터 시스템의 진동 변환기의 각도 위치를 나타내고 있다.
두 로터 시스템 각각에 다음과 같은 위치에 3 세트의 X, Y Proximity Probe가 있다.
① 전동기 상부 베어링(UMB Y 및 UMB X)
② 전동기 하부 베어링(LMB Y 및 LMB X)
③ 펌프 커플링 허브(PCH Y 및 PCH X)
각 펌프에는 하나의 축 방향 위치 변환기가 추가로 설치되어 있고 전동기 상부 베어링 부근에는 밸런스 링(Balance Ring)을 관찰하는 곳이 있으며 Keyphasor 변환기는 전동기 하부 베어링 부근에 위치한다 (그림 13-15). Keyphasor 변환기 신호는 이 글에서 나타난 모든 위상각 데이터의 기준 값으로 사용된다.
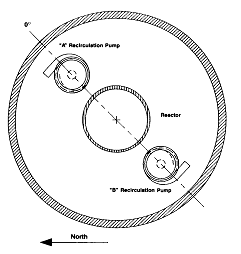
그림 13-14 진동 변환기의 방향을 보여주는 원자로 재순환 펌프
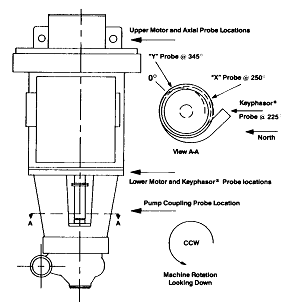
그림 13-15 Probe의 위치를 보여주는 원자로 재순환 펌프
2.2 診斷 接近方法 (Diagnostic Approach)
펌프를 저속으로 감속 운전하기 전에 축 균열 징후가 분명히 나타났는지를 평가하기 위해 테이프에 저장된 데이터 분석이 수행되었다. 분석은 다음의 축 균열 현상의 기초적인 해석에 근거를 두었다.
균열이 있는 축은 균열 면에서 강성이 저하되는 것을 경험으로 알고있다. 그러므로 반경 방향 힘을 받을 때 균열이 있는 축은 균열이 없는 축 보다 더 굽어질 것이다. 또한 균열이 있는 축은 정상 운전상태 및 과도 운전상태(기동/정지) 모두 다른 동적 응답을 나타낼 것이다. 수평기계의 경우에 정상적인 힘의 가장 일반적인 근원은 중력이다.
원자로 재순환 펌프 즉 원자로 냉각수 펌프에서 반경방향 측의 부하 그리고/또는 전동기와 펌프 축간의 가혹한 축의 Misalignment는 필연적으로 반경 방향의 힘을 가하게 된다. 균열이 발생하면 축은 굽은 상태가 되어 1× 응답의 변화로 나타나며 비대칭 축 강성으로 2× 응답이 발생한다. 그러므로 1×와 2× 진동 응답 벡터는 잠재적 균열을 나타내는 중요한 척도가 된다.
원자로 재순환 펌프의 데이터는 유량 조절 밸브를 6에서 12% 정도 열어 감속 운전하는 도중에 수집된 것이다. 이 상태에서 순수한 반경 방향 측 부하는 임펠러 주위에 존재하고 펌프의 흡입측으로부터 떨어진 쪽 즉, 동쪽으로 향하여 작용한다.
2.3 定常 運轉狀態 데이터 (Steady State Data)
그림 13-16~13-23는 5월 2일까지의 진동 진폭이나 위상각이 변하지 않은 Unfiltered, 1× 및 2× Filtered Shaft Orbit를 보여준다. 그러나 5월 11일 데이터는 현저한 진폭 및 위상각의 변화가 모든 Orbit 모양에서 명백히 나타났다.
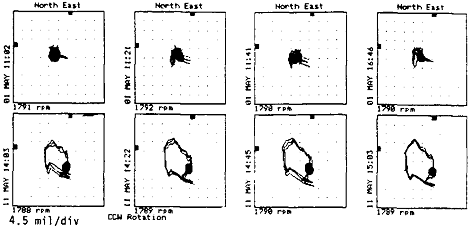
그림 13-16 전동기 하부에서의 Orbit
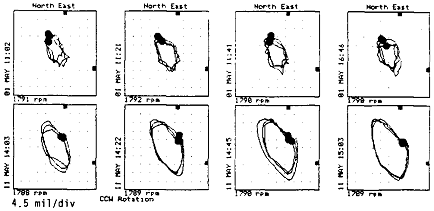
그림 13-17 펌프 커플링에서의 Orbit
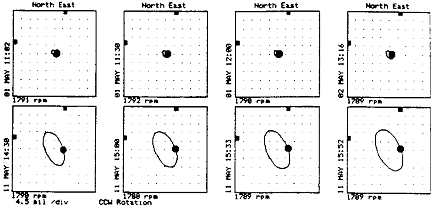
그림 13-18 전동기 하부에서의 Orbit
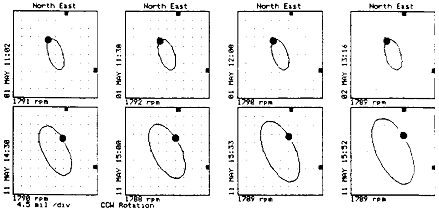
그림 13-19 펌프 커플링에서의 Orbit
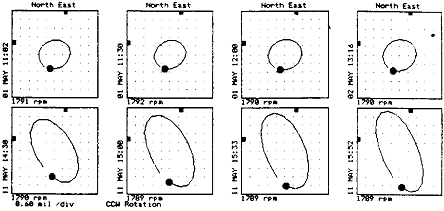
그림 13-20 전동기 하부에서의 Orbit
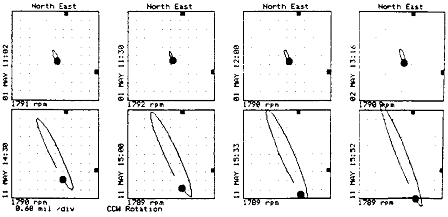
그림 13-21 펌프 커플링에서의 Orbit
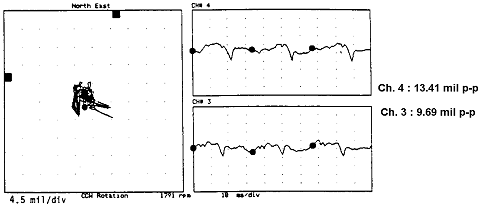
그림 13-22 최종 균열 발달 이전의 전동기 하부에서의 Orbit/Timebase 데이터(5월 1일)
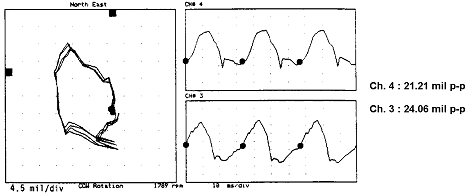
그림 13-23 최종 균열 진전 동안의 전동기 하부에서의 Orbit/Timebase Plot(5월11일)
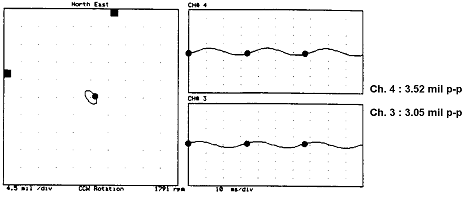
그림 13-24 최종 균열 진전 이전의 전동기 하부에서의 Orbit/Timebase Plot(5월 1일)
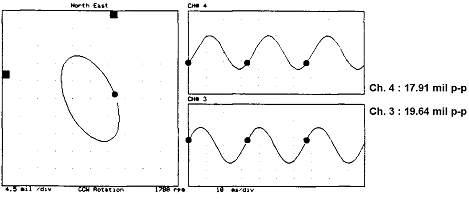
그림 13-25 최종 균열 진전 동안의 전동기 하부에서의 Orbit/Timebase Plot(5월11일)
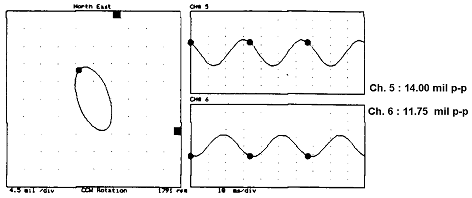
그림 13-26 최종 균열 진전 이전의 펌프 커플링에서의 Orbit/Timebase Plot(5월1일)
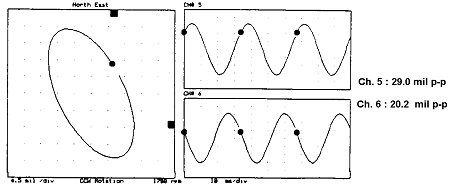
그림 13-27 최종 균열 진전 동안의 펌프 커플링에서의 Orbit/Timebase Plot(5월11일)
Shaft Orbit는 전동기 상부에서 북동쪽을 향하고 서서 펌프를 내려다보는 방향으로 모두 정해져 있다 (그림 13-14, 13-15). 이 문제를 염두에 두면 북동쪽은 0˚이고 북쪽은 45˚ 동쪽은 315˚이다. 경험상 #B 펌프의 흐름 상태에서 임펠러에 예상되는 반경 방향 예압(Preload)은 45˚ 방향 즉, 동쪽 방향의 벡터이다.
#B 펌프의 Shaft Orbit는 예압이 동서 면에 존재한다는 것을 나타낸다. 비록 Orbit가 예압의 방향을 지시하지는 않지만 Orbit의 타원 모양은 예압의 존재를 나타낸다.
그러나 5월 11일 펌프 커플링에서 Unfiltered Orbit를 보면 반경 방향 부하가 45˚에 작용한다는 결론을 내릴 수 있다. 최초로 Unfiltered Orbit가 타원형(그림 13-16, 13-17)으로 나타났으며 2시간이 지난 Orbit의 타원 모양은 동쪽이 잘려 나가기 시작했는데 이는 축이 그 방향에서 예압을 받고 있음을 의미한다.
그림 13-28~13-31까지는 1×, 2× 벡터의 진폭과 위상각 대 시간(APHT) Plot 이다.
모든 위치에서의 진폭과 위상 정보는 5월 1~2일, 26 시간 동안은 일정했다. 그러나 1×, 2× 두 벡터에서 심각하고도 연속적인 변화가 5월 11일 2시간 동안에 감지되었다.
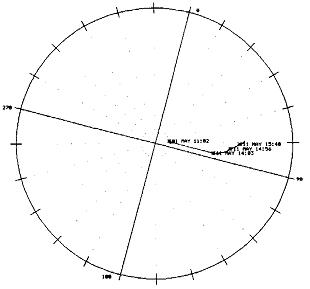
그림 13-28 전동기 하부에서의 1× 벡터의 진폭 및 위상각 대 시간 Plot (5월 1일)
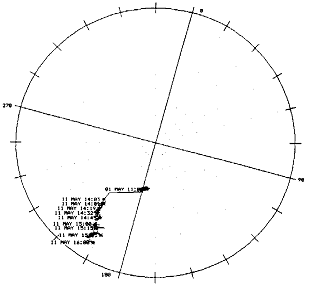
그림 13-29 전동기 하부에서의 2× 벡터의 진폭 및 위상각 대 시간 Plot (5월 1일)
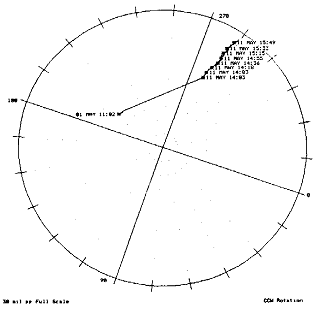
그림 13-30 펌프 커플링에서의 1× 벡터의 진폭 및 위상각 대 시간 Plot (5월 1일)
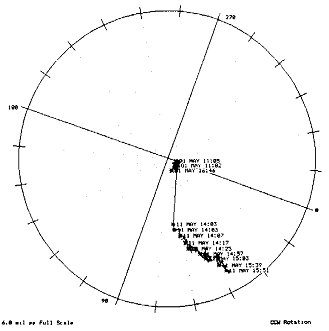
그림 13-31 펌프 커플링에서의 2× 벡터의 진폭 및 위상각 대 시간 Plot (5월 1일)
정상상태의 반경 방향 힘이 존재하면 균열은 축에 2 가지 영향을 미칠 것이다. 첫째 균열이 로터의 휨을 야기하는데 이는 1× 응답 변화로 나타난다. 둘째는 축의 강성을 비대칭적으로 만들고 이는 2× 응답 변화로 나타난다.
2× 성분은 각 축이 회전하는 동안 정상 운전상태의 반경방향 힘의 방향으로 축의 강성이 현저하게 2번 변화할 때 발생된다. 강성이 강한 단면이 반경 방향 힘 쪽으로 향할 때 축은 덜 휘고 강성이 약한 단면이 반경방향 힘 쪽으로 향할 때 축은 더 휜다.
그러므로 Bode Plot상에 정상적인 허용영역(Acceptance Region) 값을 설정하기 위해서 연속적으로 1×, 2× 진동의 정상 운전상태 벡터를 감시하는 것이 필요하다. 게다가 경보 기능은 진폭과 위상각이 정상적인 허용영역 바깥쪽으로 벗어나는 것을 사용자에게 경보해 주기 위해 필요하다. 1×든 2× 벡터든 설정된 허용영역 바깥쪽으로 움직일 때는 그 이상상태의 진단이 필요하게 된다. 1×, 2× 벡터(그림 13-28~13-31)의 연속적인 변화는 축 균열의 존재를 알리는 중요한 열쇠다.
다음 표는 5월 1일부터 5월 11일 까지 진폭의 상대적인 변화이다.
1 May | Location Unfiltered mils pp(㎛) |
1× Filtered mils pp(㎛) |
2× Filtered mils pp(㎛) |
UMB Y 5.69(144 ㎛) LMB Y 13.41(341 ㎛) LMB X 9.69(246 ㎛) PCH Y 17.52(445 ㎛) PCH X 16.92(430 ㎛) |
2.48(63 ㎛) at 259˚ 3.52(89 ㎛) at 125˚ 3.05(77 ㎛) at 67˚ 14.07(357 ㎛) at 323˚ 11.75(298 ㎛) at 199˚ |
0.36(9 ㎛) at 238˚ 2.19(56 ㎛) at 273˚ 2.10(53 ㎛) at 175˚ 0.62(16 ㎛) at 157˚ 0.51(13 ㎛) at 16˚ |
11 May | Location Unfiltered mils pp (㎛) |
1× Filtered mils pp (㎛) |
2× Filtered mils pp (㎛) |
UMB Y 7.77(197 ㎛) LMB Y 21.21(539 ㎛) LMB X 24.06(611 ㎛) PCH Y 31.50(800 ㎛) PCH X 30.60(777 ㎛) |
5.04(128 ㎛) at 244˚ 17.91(455 ㎛) at 130˚ 19.64(499 ㎛) at 74˚ 29.00(737 ㎛) at 49˚ 28.20(716 ㎛) at 284˚ |
0.36(9 ㎛) at 238˚ 4.31(109 ㎛) at 246˚ 5.20(132 ㎛) at 198˚ 6.10(155 ㎛) at 209˚ 5.10(130 ㎛) at 42˚ |
이 데이터의 Orbit/Timebase에 관한 사항은 그림 13-22~13-27을 참조
2.4 起動 데이터 (Startup Data)
5월 1일 수집한 기동 자료는 로터 시스템의 첫 번째 공진이 1360 cpm에서 발생하였고 추가로 2450, 3550 그리고 6550 cpm에서도 관찰되었다. 공진은 기동 기간 동안 1×, 2× 그리고 5× 진동 응답을 관찰함으로써 입증되었다. 그림 13-32는 2× 응답을 그림 13-33은 펌프 커플링에서 5× 응답을 나타내고 있다. 로터 공진이 어떤 주파수에서 관찰되는지 2×, 5× 성분의 공진 응답이 51 ㎛ p-p을 초과하고 어떤 경우에는 102 ㎛을 초과할 때 공진 응답은 모두 중요하다.
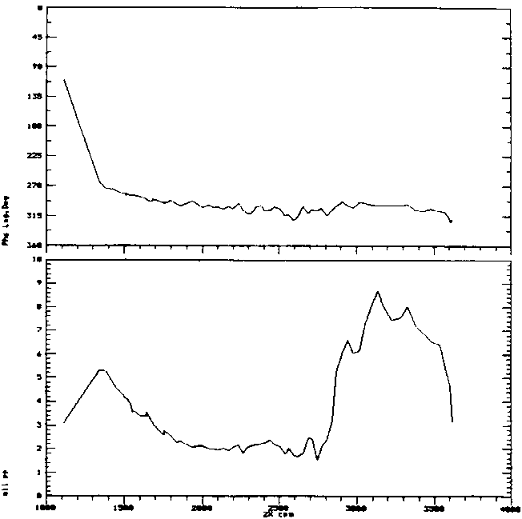
그림 13-32 전동기 상부에서의 2× 진동진폭 및 위상각 (5월 1일)
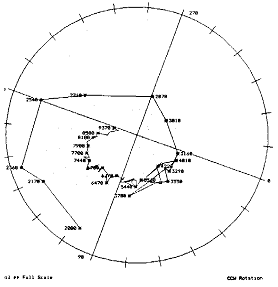
그림 13-33 펌프 커플링에서의 5× 진동 (5월 1일)
2.5 結論 (Conclusions)
로터의 과도 운전상태 응답은 공진 주파수를 구하기 위해서 기록되어야 한다. 공진 주파수의 감소는 시스템 강성의 감소 및 축 균열의 가능성을 나타낸다.
#B 펌프의 기동 데이터는 현저한 2×, 5× 성분의 공진 상태를 나타낸다. #B 펌프의 과도 운전상태의 2×, 5× 성분은 5월 1일 기동시 균열로 인한 축 강성 감소가 직접적인 결과이다.
축 균열에 대해 로터 시스템을 적절히 감시하기 위하여 전체 진동, 1× 진폭, 1× 위상각, 2× 진폭, 2× 위상각 데이터들 중의 하나 또는 결합된 데이터들이 경보를 울려줄 수 있도록 연속적으로 감시하고 진동 추이를 관리하는 것이 필요하다. Grand Gulf에서 이 데이터들에 대한 경향이 감시되었다면 양쪽 펌프 커플링의 Proximity Probe에서 측정된 이 다섯 가지의 데이터들이 5월 11일에 경보를 발생했을 것이다.
1989년 5월 2일부터 11일까지 정상 운전상태 응답에서의 변화는 로터 시스템에서 횡 방향 균열의 존재를 명백히 나타낸다. 5월 11일 펌프 커플링에서 약 76˚의 위상각 변동과 더불어 1× 진폭은 5월 2일의 값보다 35% 증가했다. 또한 펌프 커플링에서 Y와 X Probe의 2× 위상각이 각각 52˚와 37˚ 변동과 더불어 2× 진폭이 300 내지 400% 증가하는 2× 응답의 심각한 변화가 주목된다. 5월 11일 1792 rpm에서 펌프가 운전되었을 때 1× 진폭은 추가로 67% 증가했고 2× 진폭은 20% 증가했다. 2시간 후 펌프 커플링에서 전체 진폭은 약 813 ㎛ p-p로 나타났다.
3. RCP 진동 진단 (Diagnosis of Problems on a Reactor Coolant Pump)
이번 사례에서는 ADRE 3가 보유한 데이터 수집 및 표시(Display)기능을 이용하여 제작자의 문제 해결 부서가 문제를 처리해 가는 과정에 초점을 두고 있다. 이번 사례에서 특이하다고 할 만한 것은 문제를 해결하는 과정에서 이 장비를 미국에서 유럽으로 다시 유럽에서 미국으로 휴대하고 다녔다는 것이다. 즉, 이 장비는 높은 휴대성과 견고한 구조로 만들었기에 그러한 여행에도 이상적인 동반자가 된다.
다음은 유럽에서 가동중인 원자력 발전소의 한 가압 경수로 냉각수 펌프에서 발생한 문제에 대하여 보고한 내용이다. 그 펌프는 진동에 문제를 일으키고 있어 그곳의 근무자들이 Westinghouse(WH)에 도움을 청하게 되었다.
RCP는 수직으로 설치되어 있으며 1차측 냉각수를 원자로에서 증기 발생기로 순환시키는 역할을 하며 원심 펌프로써 1480 rpm/7000 HP의 전동기에 의해 구동되고 288℃/100 m의 수두에서 약 94,000 gpm의 냉각수를 순환시킨다. 전동기와 펌프간은 견고하게 연결되어 있는데 그 이유는 반경 방향 베어링 3개(2개는 유윤활 Pivot Pad형 전동기 베어링이고 1개는 L/D=1인 대형 수윤활 평면 저널 베어링)만으로 전동기와 펌프를 감당하고 있는 구조이기 때문이다. 펌프 베어링의 경우 Seal/Bearing부에 냉각수를 공급하고 있고 베어링 하부에 열 차폐용 열 교환기가 있어 그 내부 유체에 비해 낮은 온도를 유지하고 있다. 냉각수는 케이싱 하부에서 유입되어 접선 방향의 출구를 지나 배출된다. 반경방향 베어링들에 정적부하를 주기 위해 임펠러에 907~1361 ㎏의 반경방향 부하가 걸리도록(유체 온도에 따라 다름) 수력학적으로 설계되어 있다. 그림 13-34은 개략적인 배치도를 나타낸 것이다.
이 펌프에는 WH사가 RCP에 널리 사용하는 가장 일반적인 형태의 진동 감시 장치가 설치되어 있다. 배전반 모니터에는 2개의 Proximity Probe(펌프 커플링부에 설치)와 1개의 Keyphasor Probe 및 2개의 속도 센서에서 나오는 신호를 받는다. 변위 센서와 위상 변환기는 커플링을 바라보는 형태로 Seal Housing의 상부에 설치되어 있다. 속도 센서는 Motor Frame의 하부에 설치되어 있다. 그림 13-34를 보면 펌프측 수윤활 베어링과 전동기측 하부 베어링의 중간쯤에 Proximity Probe가 설치되어 있음을 알 것이다.
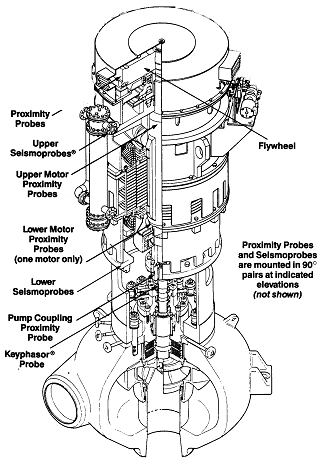
그림 13-34 원자로 냉각수 펌프
배전반 모니터에 나타난 신호를 볼 때 3개의 펌프 중 1대에서 전체 진동 크기가 150 ㎛ 범위 이상을 왔다갔다하고 있었으며 경보값인 254 ㎛ p-p을 넘고 있었다. 진동이 한번 등락하는데 소요되는 시간은 1~2분 정도였다. WH 기술자는 ADRE 3를 설치하여 진동 신호를 수집하고 아울러 고진동의 원인을 파악하는데 도움을 줄 다음과 같은 관련 사항을 기록하였다.
∙ 문제의 발생은 1988년 4월말 100% 전 출력 운전 중 예기치 않게 시작되었다.
∙ #1 Seal(펌프 베어링 바로 위에 설치되어 있음)로 부터의 Leak-off량이 맥동하는 시기는 진동 등락 현상 발생 시기와 일치하였다.
∙ 진동 크기 및 진동 등락 발생 시기는 열차폐벽에 흐르는 냉각수의 양이나 온도 또는 Seal 분무수의 양이나 온도와는 상관관계가 없었다.
∙ 처음에는 진동이 높지 않았으며 고진동의 발생과 소멸이 무작위적이었다. 그러나 고진동이 발생할 때마다 그 지속시간이 길어지는 듯 하였다.
3.1 初期 資料 取得 및 檢討 (Initial Data Acquisition and Review)
WH기술자는 108 DAIU를 사용하여 전부하에서의 정상상태 자료를 수집하고, Bode’, 축 중심선 및 Spectrum Plot들은 ADRE 3 소프트웨어를 이용하여 그렸다. 변위 센서에서 취한 데이터로부터 APHT Plot를 보면 진동은 등락을 반복하고 있으며 이에 비해 위상의 변화는 상대적으로 미소하게 나타났다 (그림 13-35). 스펙트럼 Plot (그림 13-39)을 보아도 진동은 등락을 거듭하고 있음을 보이고 있고, 또한 차동기 성분 및 조화 주파수들도 보이지만 진동이 등락하는 사이의 어느 특정 시간에서만 보이고 있다.
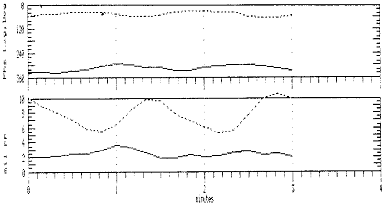
그림 13-35 APHT Plot [Ch. 1(X, 실선) 및 2(Y, 점선)]
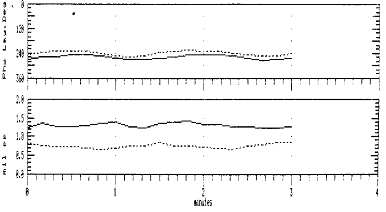
그림 13-36 APHT Plot [Ch. 3(X, 실선) 및 4(Y, 점선)]
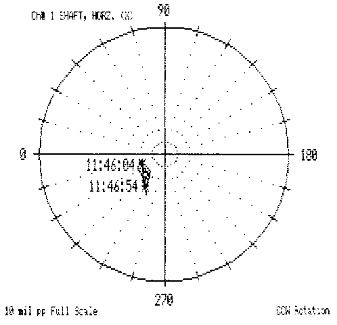
그림 13-37 축 중심선도(Ch. 1)
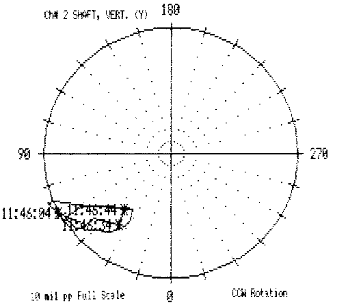
그림 13-38 축 중심선도(Ch. 2)
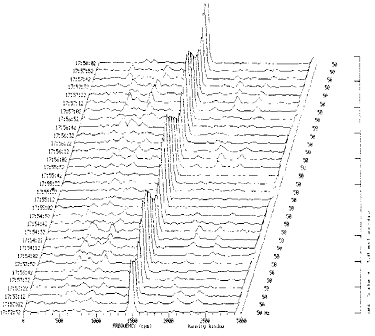
그림 13-39 Waterfall Plot (Ch. 2)
다른 그림들에서도 많은 사실을 알 수 있는데 정상 상태에서 축이 베어링 간극 내에서 반경 방향으로 움직이고 있음을 축 중심선 Plot(그림 13-40)에서 알 수 있다. 보다 중요한 사실은 축의 거동이 축의 회전 방향과는 반대인 시계방향 세차운동을 일으키고 있었다는 것이다. Motor Frame에 설치된 속도센서로부터는 문제 해결에 필요한 정보를 거의 얻을 수가 없었다.
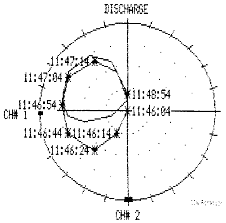
그림 13-40 축 중심선도(Ch. 1 및 2)
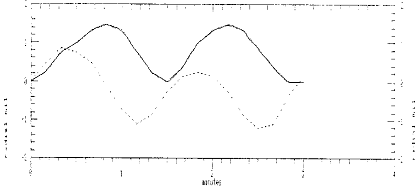
그림 13-41 진동파형 [Ch. 1(X, 실선) 및 2(Y, 점선)]
축 중심선이 역방향 세차운동을 하는 것으로 보아 Rub 상태가 아닌가 의심되었다. 비정상적인 형태의 차동기 성분들이 그런 가능성을 암시하고 있었다. 그러나 Keyphasor의 신호가 그리 불안하지 않고 진동값이 천천히 변하는 등의 모습은 Rub에서 보이는 일반적인 형태는 아니었다. 그렇다고 Rub가 없다고 하는 것은 아니다. WH기술자는 이러한 형태의 거동을 “Lubricated Dry Rub”로 비유하였다. 완전한 Dry Rub 상태라면 아주 높은 속도에서 역방향 세차운동을 하며 통상 급히 기계를 파손시킨다. 이러한 거동은 주로 축이 정방향 회전을 하며 축을 서서히 역방향 세차운동을 하게 하는 Rub에 의한 작은 비틀림 저항을 가진다.
현장에서 운전자 및 엔지니어들이 모여 그런 거동을 유발할 만한 다른 가능성에 대하여 토의를 하였고 이에는 전동기의 전기적 상평형 문제정도가 대두되었다. 하지만 최근 정비시 어떤 문제점들을 발견한 바 없어 분명한 불평형은 없었다. 따라서 현재의 문제를 설명할 수 있는 1차적인 가정으로는 역시 Rub가 우세하였다. ADRE 3의 데이터도 이러한 가정을 뒷받침하고 있었다.
3.2 첫 번째 問題 解決 試圖 (First Attempted Problem Correction)
데이터를 수집하는 동안에도 발전소는 100% 부하 운전중이어서 모든 RCP를 운전해야 했기에 즉각적인 수정 작업을 할 수가 없었다. WH 기술자는 차기 정지시에 하부 전동기 베어링부의 Labyrinth Seal에 Rub가 있는지 검사해보자고 권하였다. 그 펌프는 진동값이 정지 제한값보다 낮으며 상태가 안정적이고 반복적이었기 때문에 현재상태로 연속 운전할 수 있었다.
다른 모든 관찰 사항들이 진동 데이터와 어떻게 일치하는가를 설명하기 위하여 WH 기술자는 진동의 등락, 축의 느린 세차 운동 및 Seal 유량의 맥동간의 상관관계에 대하여 기초로써 ADRE 3의 데이터를 제시하였다(자세한 사항은 3. 5항 참조).
1988년 7월에 잠시 정지 작업기간이 있자 전동기의 하부 베어링과 Labyrinth Seal을 검사하였다. 시간이 많이 소요되는 분해 점검을 할 수 없어 직접적으로 확인할 수는 없었으나 문제의 Labyrinth는 Rubbing 되지 않았고 Labyrinth의 중심도 베어링의 중심과 잘 일치하는 것으로 보였다. 베어링에서는 7개의 Shoe중 1개의 간극이 권장치인 0.15~0.2 ㎜를 넘는 0.4 ㎜이었으나 이로 인하여 어떻게 Labyrinth가 Rubbing이 될 수 있으며 위에서 언급한 문제들이 생기는지 완전하게 설명하기에는 충분하지 않았다. Shoe를 교체하고 나서 전동기와 펌프 베어링간의 Alignment를 점검한 결과 허용치 내에 있음을 알았다.
3.3 두 번째 데이터 取得 및 檢討 (Second Data Acquisition Survey and Review)
냉각수 가열을 위해 펌프를 가동하자 마자 진동이 등락하는 현상이 다시 일어났다. 그러나 최초에 문제가 시작되었을 때와 마찬가지로 정상 운전중 짧은 기간이지만 등락 현상이 있었다.
WH 기술자는 정상운전 중에는 그 발전소에 있어 본 적이 없어 나중에 감시 장치의 기록계 출력 단자로부터 취한 표준 기록으로 이런 현상을 입증하였다. 그는 그 발전소가 다시 도움을 청해오자 진동 데이터를 좀더 수집하기 위해 ADRE 3을 가지고 갔다. 따라서 보다 나은 문제점의 규명을 위하여 펌프의 기동과 정지 때의 진동신호를 연구할 수 있었다.
축 중심선도를 검토한 결과 전기적인 원인으로 발생했을 가능성은 완전히 배제하게 되었다. 전자기적인 중심과 회전자의 기계적 중심이 서로 상당히 틀릴 경우 펌프의 전원을 차단시키면 축 중심선이 갑작스런 변화를 보이는데 이번 기동/정지시의 데이터에는 그런 변화가 없었던 것이다. 전동기 프레임에도 진동 점검을 실시하였지만 다른 기계적 문제점이 진동 감시를 하지 않고 있는 전동기 상부에 존재할 것이라는 가능성을 배제한다면 어떤 이상한 점을 나타내지 않았다.
새로 수집한 정보로써 Rub라는 가설을 단언하게 되었고 Seal 유량의 맥동 및 진동 등락 현상과 축 중심선의 위치가 관계 있다는 설명을 확증하게 되었다. 그림 13-42, 13-43, 13-44, 13-45는 ADRE 3로 2회의 정지시 데이터를 취한 것인데 마치 서로 다른 2대의 기계에서 수집한 것처럼 보인다. 이들 그림과 축 중심선들과의 상호관계를 보면 2회의 Coastdown은 축 중심선의 위치가 최대로 떨어진 지점에서 시작되었음을 알 수 있고 이때의 진동진폭은 거의 최대치에 있었다. 이러한 데이터로 보아 Dynamic Bearing의 상수들의 변화가 진동 진폭의 등락을 초래하였다는 것이 더욱 분명하였다.
역방향 세차 Orbit의 크기와 펌프 및 전동기에서의 베어링 간극을 검토한 결과 WH기술자는 펌프 축과 베어링 내면간의 Rub라는 가설과 일치하는 가능성 있는 손상 모드가 오직 하나 있다고 결론 지었다. 이러한 설명에 대한 단 한가지 문제점은 이러한 사례가 전에는 한 번도 없었다는 것이다. 베어링이 어떻게 고착될 수 있었는지 확신을 가지고 있는 사람은 하나도 없었다. 베어링은 0.076~0.2 ㎜정도의 반경 방향 간극을 가지고 있었다. Rub(이젠 Rub가 있다는 것은 기정사실화 되었다) 발생원으로의 이러한 설명을 받아들일 수밖에 없는 가장 큰 이유중 하나는 다른 가능성 있는 설명들은 펌프에서 나온 데이터로는 뒷받침되지 않았다는 것이다.
그러나 전력을 계속적으로 생산해야 했기에 펌프를 정지시켜 베어링을 확인해 볼 수는 없었다. 진동 크기가 안정적이어서 차기 정지시인 1989년 4월까지 계속 운전하기로 결정하였다.
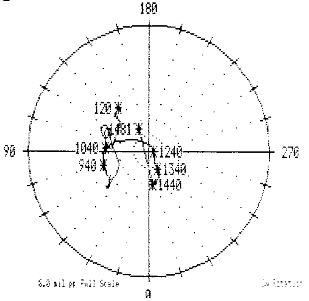
그림 13-42 1차 정지시의 축 중심선도
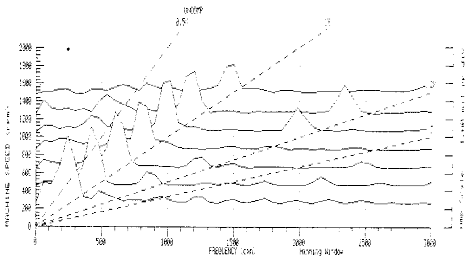
그림 13-43 1차 정지시의 Cascade Plot
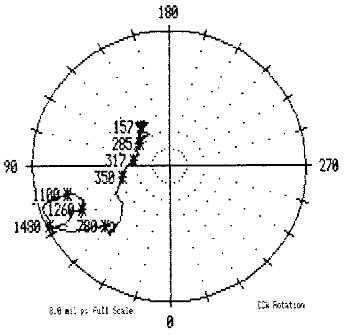
그림 13-44 2차 정지시의 축 중심선도
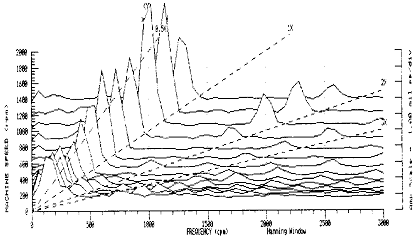
그림 13-45 2차 정지시의 Cascade Plot
3.4 세 번째 데이터 取得 및 檢討 (Third Data Acquisition Survey and Review)
차기 정비 시기가 가까워지자 그 펌프는 문제점과 전혀 관련이 없지만 일반적으로 펌프에서 관심이 되는 진동상승의 문제점이 발생했다. 또한 진동값도 서서히 상승하는 경향이 있었고 때로는 거의 정지 제한값까지 치솟는 경우도 생겼다. 다행히 이 제한값까지 도달하지는 않았다. 이 새로운 문제들을 다루고 1988년 8월~1989년 4월 사이에 다른 변화는 없었는지 알아보기 위해 WH기술자는 ADRE 3을 유럽으로 재차 가지고 갔다.
진동 진폭은 지난번 보다 조금 더 큰 범위로 등락하고 있었다. 축 중심선의 역방향 세차 주기는 조금 줄었다. 차동기 주파수들( 및 조화주파수)도 선형 주파수 및 Waterfall Plot상에서 거의 보이지 않게 되었다. Unfiltered Shaft Orbit을 보면 진동 진폭의 증가와 함께 보다 전형적인 Impact-Rebound형의 Orbit(그림 13-46 및 13-47)으로 진전되었다. 또한 Filtered Orbit을 보면 전에도 그랬듯이 심한 타원형(그림 13-48 및 13-49)인데 이는 어느 한쪽 방향으로의 움직임이 제한 받고 있음을 나타내는 것이다. 한 Waterfall Plot(그림 13-50)을 보면 1× 성분과 그 크기의 변화를 같이 하고 있는 2× 성분이 있음을 알 수 있다. 최근 다른 발전소의 RCP의 축 균열 사례가 있어서 염려가 되었는데 여기의 2× 성분은 안정적이며 지난번 검사시보다 아주 조금 커졌을 뿐이어서 축균열 가능성에 대한 검토를 할 필요는 없었다.
몇몇 사람들은 축균열 가능성으로 걱정하고 있었지만 더 많은 데이터로 인해 이러한 Rub에 대한 가설이 강화 되었고 발전소는 차기정비 시까지 계속 운전하게 되었다. 펌프는 4월부터 5월까지 잠시 정상적이었다가 정지전에 통상적인 Rub Mode로 되돌아 왔다.
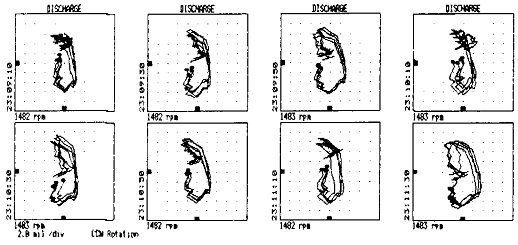
그림 13-46 Impact-Rebound형의 Unfiltered Orbit (23:09:10~23:11:30)
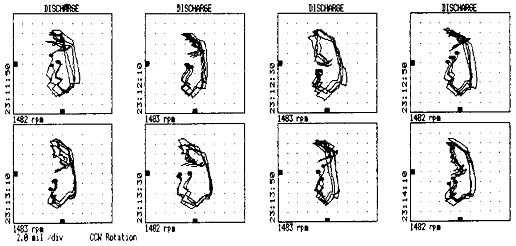
그림 13-47 Impact-Rebound형의 Unfiltered Orbit (23:11:50~23:14:10)
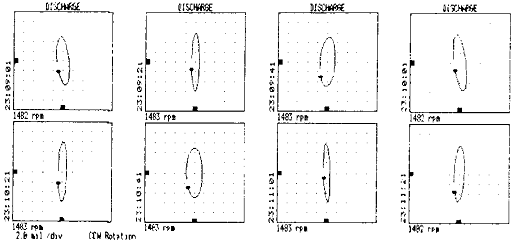
그림 13-48 Filtered Elliptical Orbit (23:09:01~23:11:21)
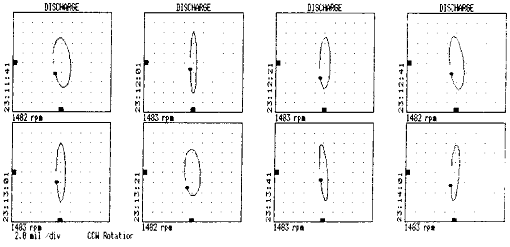
그림 13-49 Filtered Elliptical Orbit (23:11:41~23:14:01)
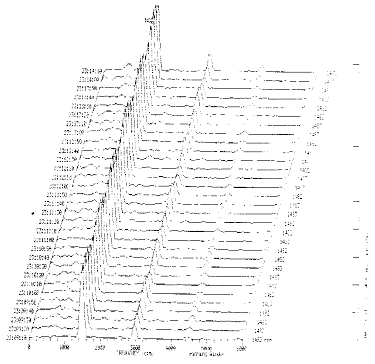
그림 13-50 Waterfall Plot
드디어 발전소를 정지하고 펌프 베어링을 검사하게 되었다. 그런데 뜨거운 Barrier Housing에서 베어링/Housing 전체를 뽑아내는 것은 대단히 어려웠다. 결국 그 부분을 뽑아내려고 새로운 기법(액화질소를 이용함)을 사용해야만 했다. 여기서의 결론은 뜨거운 Barrier Housing이 베어링 Housing을 꽉 잡아서 0.076~0.2 ㎜인 베어링 Housing 틈새를 더욱 죄었다는 것이다. 따라서 베어링이 자유롭게 Pivoting될 수 없어 그 끝단부에서 예상해 왔던 대로 심하게 Rubbing을 일으켰던 것이다. 가장 손쉬운 정비 방법은 펌프내부 부속품을 예비품으로 교체하고 빼낸 부품중 사용 가능한 것은 추후 사용토록 하는 것이었다.
RCP를 수리하고 발전소를 재기동하였는데 문제가 없었다. 단지 진동치를 원하는 수준까지 저감시키기 위한 의례적인 발란싱만 했을 뿐이다.
그 발전소의 RCP들은 Proximity Probe와 전동기 프레임에 설치된 진동 변환기에 의해 연속적인 감시가 이루어지고 있었다. 감시 장치는 배전반에 진동값을 연속적으로 보여주었다. 진동값을 배전반에서 계속 확인할 수 있음으로써 RCP에 문제가 있더라도 정지가 필요한 시점까지는 계속 운전할 수 있다. 이러한 감시 장치가 없으면 RCP의 상태나 문제의 진전을 알 도리가 없는 것이다. 이러한 진동 감시장치와 진단용 장비를 적절히 활용함으로써 이 펌프를 계속 운전해도 되겠다는 결정이 가능한 것이다.
이러한 사례로 볼 때 X, Y Proximity Probe Transducer를 설치하는 것이 이익이 된다는 것은 자명해진다. 2×와 3× 뿐만 아니라 차동기 주파수 성분들의 변화는 전형적으로 문제가 있음을 나타낸다. 그러나 일반적으로 그 문제의 원인까지 알려주지는 못하는 것이 보통이다. 이번 사례에서 축 중심선도(X, Y Probe에서 수집한 Gap Data)를 표현할 수 있어서 정상 상태에서의 축이 반경 방향으로 움직이고 있음을 즉각적으로 알 수 있었다. 또 Proximity Probe에서 취한 Orbit Plot을 보면 축이 무엇인가를 치고 있다는 것을 알 수 있었고 나아가 Rub 가능성도 확인할 수 있었다. 분명한 사실은 적절한 감시 장치가 설치된 기계에서는 기계의 상태를 알 수 있는 정확한 정보를 받아볼 수 있다는 것이다. 이러한 정보는 어떤 문제를 해결하고자 할 때 불확실한 많은 사실들을 일단 배제시킬 수 있게 해준다. 만약 전동기 베어링에도 X, Y Proximity Probe를 설치하였더라면 이 Probe의 신호로부터 전동기 베어링이나 그 근처에서는 Rubbing이 없음을 확인할 수 있었을 것이고 따라서 문제의 원인을 보다 빨리 알아낼 수 있었을 것이다.
3.5 RCP에 發生한 問題들의 相互關係 (How the RCP’s Problems Related to Each Other)
ADRE 3 시스템만으로는 이런 류의 문제들을 해결할 수는 없다. 그러나 데이터의 수집 기술과 사용자가 원하는 형태의 그림 또는 숫자로 표시함으로써 진동 진단자로 하여금 데이터를 마음껏 가공하여 사용할 수 있게 하였다. WH기술자는 지난날에는 약간의 데이터를 얻기 위해 많은 시간을 소비하였지만 이제는 그가 필요로 하는 모든 데이터를 가질 수 있다고 말했다. 그는 이제 다만 어느 그림이 문제점을 가장 잘 표현하고 있는지에만 시간을 쓰면 되는 것이다.
베어링 Dynamic Spring/Damping Constants측면에서 보면 진동 등락 현상과 축의 역방향 세차 운동은 서로 연관을 가지고 있다. WH의 모든 RCP는 유체 베어링을 사용한다. 따라서 베어링 상수는 베어링 내에서의 축의 편심에 크게 영향을 받는다. 축이 펌프 커플링에서 50 ㎛정도 움직이면 그 양은 알 수 없지만 모든 베어링에서도 움직이고 있을 것이 틀림없다. 회전축에 고정된 불평형량이 존재하면 이에 해당하는 운전속도 주파수의 진동진폭 변화만큼 베어링 상수의 변화에 대하여 축이 응답한다. 이것이 바로 데이터가 보여주는 내용이다.
Seal의 Leak-off량이 맥동하는 것은 #1 Seal의 유체역학적 특성 때문이다. 이는 Seal Ring과 Seal Runner의 중심의 상대적 변화에 따라 Leak-off 비율 변화만큼 응답한다. Runner(펌프 베어링의 바로 상부)는 축에 부착되어 있고 Seal Ring은 정지체인 Seal Housing에 반경 방향으로 또 축방향으로 Floating 하도록 고정되어 있다. 따라서 Seal Leak-off량은 축 중심선의 세차운동에 영향을 받아 맥동하게 된다. 축의 세차운동이 매우 저속이어서 Seal Leak-off 유량 측정은 이러한 변화 상황을 감지할 수가 있다. 축 회전 주파수에서의 진동은 너무 빨리 발생하여 Leak-off 유량 측정을 할 수가 없다. 그러므로 이 Seal의 설계상 Leak-off량에 미치는 축 진동의 영향은 거의 없다.