The Failure Analysis and Troubleshooting System
1. 고장 분석의 연장으로서의 고장 원인 해결 기법 (Troubleshooting as an Extension of Failure Analysis)
2. 기계 고장의 원인 (Causes of Machinery Failures)
3. 기계고장의 근본원인 (Root Cause of Machine Failure)
- 고장원인 해결기법
Troubleshooting as an Extension of Failure Analysis
수년동안, “고장 분석”이란 말은 정적인 설비의 검사 일환으로 수행하는 파괴역학과 부식손상 해석과 관련하여 특별한 의미를 가져왔다. 그림 1-1은 재료의 기본적인 고장 분석 단계를 보인 것으로 기계의 고장 분석에 응용되는 기법들은 기본적으로 같지만, 금속적 조사에만 제한이 없다. 여기서, 고장 분석은 기계부품과 그의 가능성 있는 원인에 대한 고장 형태를 규명하는 것이다. 그림 1-2는 터빈 제작자가 생산 개발에 있어서 품질, 신뢰성, 안전과 관련한 기계요소의 고장형태 분석의 일반적 특징을 보인 것이다.
때로 기계 고장은 원인과 결과의 연쇄 반응으로 나타난다. 반응의 끝부분은 증상, 결함, 또는 단순히 “문제”를 언급하는 성능결함이다. 고장원인 해결은 연쇄 반응의 요소를 정의하기 위해 거슬러 조사하며, 현존 또는 잠재적 문제의 근본 원인에 대한 고장(현상)분석의 근거에 의해 가장 가능성 있는 잠재적 원인과 연결시킨다. 실제적으로는 고장 분석과 고장원인 해결은 뚜렷한 과정도 없이 서로 얽히는 경우가 많다.
후에 알겠지만, 문제의 원인을 찾는데 있어 단지 고장원인 해결 기법만으로 충분한 경우가 많은데 이것은 고장형태가 분명하지 않은 경우이다. 간헐적인 동작불량이나 결함이 일반적인 예이며 대부분 노련한 고장원인 해결사를 당혹케 한다. 이러한 경우 조사자가 시스템을 알고 있다면 고장원인 해결은 성공적이고, 부품간의 상호작용, 운전 또는 파손유형, 기능 특성에 익숙하지 않으면 노력은 허사가 된다.
기계 고장 분석과 고장원인 해결의 목적은 다음과 같다.
⑴ 향후의 고장사고 방지
⑵ 기계 수명 기간중 안전성, 신뢰성, 정비성 확보 :
a. 설계와 사양.
b. 기본 장비의 설계, 제작, 시험.
c. 선적과 저장.
d. 설치와 시운전.
e. 운전 및 정비.
f. 교체.
a항~f항에서 보면 고장 분석과 고장원인 해결은 상호 관계가 있음이 분명하다. 여러 부서가 참여하게되고 임무가 때로는 다르기 때문에 기계고장에 대한 체계적이고 일률적인 이해와 기술이 중요하다.
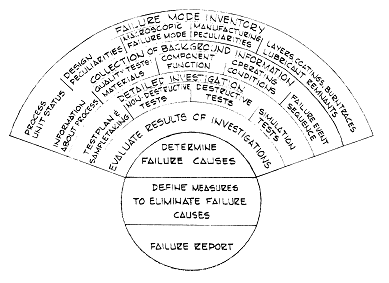
2. 기계고장의 원인
Causes of Machinery Failures
고장이란 기계부품이나 요소가 변형하여 제기능을 발휘 못하는 것이라 할 수 있으며 실제 최종적인 고장은 계속적으로 사용하기에 불안전하고 신뢰성이 없는 “초기 결함”, “초기 고장”, “열화”, “손상” 등이다.
사고원인의 분류 :
⑴ 설계 결함
⑵ 재료 결함
⑶ 공정과 생산 결함
⑷ 조립 불량
⑸ 설계 불량 또는 용역조건 미흡
⑹ 정비 결함
⑺ 운전 불량

기계의 고장 원인을 다루는 통계나 참고자료는 일반적으로 다음 분류법을 사용한다.
실제 고장 분석을 위해 다음 목록의 확장이 필요하다. 표 1-1은 기계 고장의 원인에 대한 대표적인 예이다. 고장 원인은 각기 해당 영역에 적용되어야 하나 그렇지 않을 경우, 앞에서 언급한 고장 분석의 목적에 맞지 않을 것이다.
고장 원인은 하나 이상의 특정 고장 형태와 관련시켜 규명하는 것이 고장 분석의 주요 개념이다. 표 1-2는 석유화학 공장의 99%의 기계 고장에서 나타난 기본 고장 형태를 나타낸 것이다.
다음 장에서 이 목록을 더욱 확장하여 일일 고장 분석에 사용하고 있다. 고장형태는 고장의 결과이므로 고장의 원인과 혼돈해서는 안된다. 고장 형태는 원인과 결과의 긴 연결고리의 결과일 수도 있어 결국 기능상 고장을 유발한다.
표 1-1 고장 원인


표 1-2 기계 고장 형태 분류

자주 쓰이는 다른 용어로는 “결함 종류”, “결함”, “고장 메커니즘” 등이며, “고장 메커니즘”이란 용어는 특정 고장형태로 구분되는 금속적, 화학적, 윤활과정으로 표현된다. 예로, 롤러 베어링의 Fretting 마멸이나, 펌프 임펠러의 공동현상, 치차 톱니면에서의 초기 Pitting에 대한 일련의 원인과 결과를 표현하고자 고장 메커니즘이 개발되었다. 기계요소와 부품의 고장 메커니즘의 기본 인자는 외력, 시간, 온도, 그리고 부식성 환경으로서 각기 표 1-3과 같이 세분된다.
이와 같이 정의된 고장 메커니즘은 고장 형태가 어떻게, 왜 화학적 또는 금속적으로 발생했는지는 말해주지만 고장의 근본 원인을 밝히지는 못한다.
표 1-3 기계 요소 및 부품의 고장 메커니즘 인자

3. 기계고장의 근본원인
Root Causes of Machinery Failure
앞장에서 주어진 고장에는 여러 가지 원인과 결과가 있음을 보여 주었고, 여기서 우리는 문제 해결에 기여하는 인자의 제거나 수정을 위해서는, 일련의 원인과 결과의 실제 문제에 들어가야 한다.
기어의 주 고장형태의 하나로써 융착 마멸(Scuffing)을 들 수 있는데, 그것은 고장 메커니즘의 심각한 형태 접착성 마멸이다. 만약, 충분히 두꺼운 유막이 치차 톱니 표면을 분리시키면 접착성 마멸은 발생하지 않는다. ‘접착성 마멸 고장 메커니즘에 가려진 원인과 결과의 관계가 있다하더라도 이 마지막 문장에서 근본 원인에 대한 단서‘를 보여줄 것이다. 그렇다면 근본 원인은 무엇인가? 융착마멸은 보통 시간에 따른 고장형태인 피팅과는 대조적으로 매우 갑자기 발생한다. 따라서, 특수한 기어셋트에서 사전에 융착마멸이 관찰되지 않으면, 윤활계의 설계나 윤활유 자체에서 근본 원인을 찾을 수 없다. 갑작스럽고 간헐적인 윤활 중단이 그 이유가 된다. 그것이 근본 이유인가? 물론 아니다. 융착마멸의 발생지속, 또는 재발을 방지하기 위해 제거 또는 수정할 요소를 찾을 필요성이 있다면 계속 찾아야 한다. 그 이유는 갑작스럽고 순간적인 윤활유 압력손실을 야기시키는 예비 윤활유 펌프를 주기적으로 시험하기 때문이다. 결국, 설계, 운전, 정비관례의 변경이 치차의 융착마멸을 멈추게 한다는 점에 귀결하게 된다.
기계 고장의 원인 제거는 설계나 운전-정비에서 해야한다. 전통적으로 후자는 고장 분석과 방지에서 자주 강조된다. 우리의 견해는 장기적 고장의 감소는 규격과 설계의 수정만으로 달성할 수 있다는 것이다. 이러한 작업은 어떻게 하는가? 고장 형태를 확인후, 고장난 기계요소가 그 손상에 더 견딜 수 있는지 규명한다. 이는 표 1-4에서 보는 바와 같이 가능한 수정을 위해서 설계 변수를 점검해야 한다. 양호한 해답이 구해진다면 근본 원인이 규명되어지고 재료, 요소, 어셈블리 또는 시스템의 취약성을 감소케하는 무엇이든 자세히 지적할 수 있다. 우리의 실행계획을 수립한 후에, 기계적 원리(격언)가 자명하고 사실인지를 확인해야 한다.
모든 가상 상황에서도 부품을 보다 강하게 한다고 해서 기계 손상에 좋은 영향을 미친다는 생각은 잘못임을 명심해야 한다. 유연성있게 설계된 요소는 때로 강체부분 보다 어떤 심한 운전조건에서도 잘 돌아간다. 표 1-5는 직접 원인이나 설계변수 결함과 관련한 기계 고장 형태를 요약한 것이다.

