Lubricated and Gear Couplings
4.1 潤滑 커플링 故障 分析 (Lubricated Coupling Failure Analysis)
4.2 기어 커플링의 故障 分析 (Gear-Coupling Failure Analysis)
4.3 기어 커플링의 손상 메커니즘 (Gear-Coupling Failure Mechanism)
4.1 윤활 커플링 고장분석 (Lubricated Coupling Failure Analysis)
정유화학공장에서 적용하는 축커플링은 일반적으로 2가지의 기본 형태가 있다. 즉 기계적으로 탄성인 커플링과 디스크와 다이어프램 커플링처럼 재료의 탄성에 좌우되는 커플링이다. 기계적으로 탄성인 커플링의 사용자와 설계자는 윤활에 의한 마모와 싸우게 된다. 그림 3-139는 석유화학 산업에서 보여주는 커플링의 기본 형태이다. 지금까지 가장 광범위하게 사용된 윤활 커플링은 기어 커플링이다. 1918년, 기어 커플링이 발명되었을 때 산업은 증기에서 전력으로 그리고 벨트 구동 기계에서 직접 구동 기계로 바뀌었다. 이러한 변화로 탄성 축커플링을 축에 직접연결이 가능하게 되었고, 기어 커플링은 이러한 변화에 중요한 역할을 하였다.
지난 10년동안 비윤활, 고속, 고 토오크 다이어프램 커플링은 좋은 반응을 얻었다. 이러한 발달에도 불구하고 많은 압축기에는 여전히 다양한 크기와 모양의 기어형태 축커플링이 설비되어 있다.
이의 기본 목적은 회전력을 구동기계에 전달하고, 연결축의 예상되는 미스얼라인먼트를 조정하고 또한 그로 인해 야기되는 구동 및 피구동 기계의 문제를 예방하는 것이다.
다른 모든 윤활 커플링에서와 같이 기어 커플링 손상의 75%는 윤활유의 부적절이나 불충분에 기인한다. 커플링 손상의 원인 분포도는 표 3-12와 같고 손상형태 분포는 표 3-13과 같다.
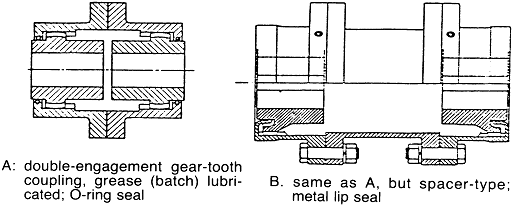
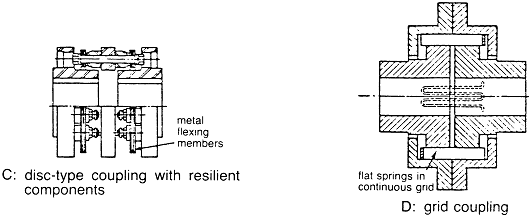
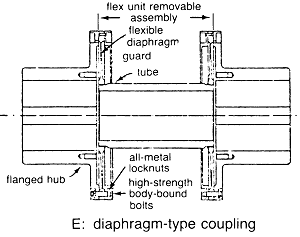
그림 3-139 공정 기계에 사용된 탄성 축 커플링
표 3-12 기계 커플링의 고장 원인
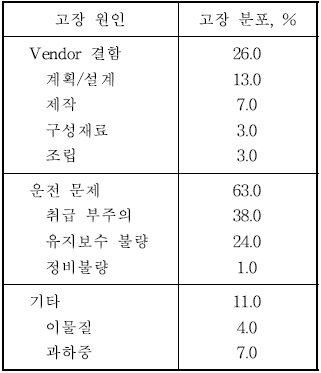
표 3-13 기계 커플링의 고장유형 분포
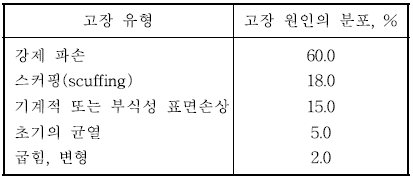
4.2 기어 커플링의 고장분석 (Gear-Coupling Failure Analysis)
기어 커플링에 대해 여러 기술서적에서 다루었었는데 이는 의심할 여지없이 관리 상태가 양호한 공장에서조차 윤활 커플링에서 빈번히 문제가 발생하기 때문이다. 취약 연결로 인해 신뢰성이 없고 손상이 일어나기 쉽기 때문에 주기적인 점검과 정비가 필요하다.
“결함”을 규정하기란 어렵다. 이러한 작업은 전문가조차 어려워한다는 것을 기어 커플링에 대한 경험에서 알 수 있다. “Worm Tracking의 존재”의 판단은 용이한 반면 “경미한 마멸”이나 “부식”의 판단은 어렵다. 종종 예비품의 비효용성이나 교체비용 때문에 기어 커플링의 점검후 조치에 대한 판단이 어렵게 된다. 기어 커플링의 주 손상 형태가 마멸임이 밝혀진 바 있다. 고속 커플링의 손상 분석에 관한 보고서에서 커플링의 일반적 손상 형태를 표 3-14와 같이 목록화 하였다. 간략히 말해서 기어 커플링의 다양한 마멸 등급 판단은 숙련된 기계문제 전문가에게도 어려운 과정이다.
표 3-14 기어 커플링 고장의 일반적
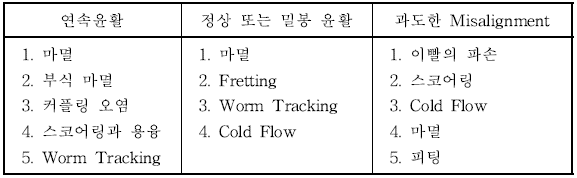
4.3 기어 커플링의 손상 매커니즘 (Gear-Coupling Failure Mechanism)
기어 형태의 커플링은 축의 미스얼라인먼트에 순응하려할 때 슬라이딩 운동이 기어의 맞물림 안쪽에서 발생하는데, 이것은 커플링 마멸과 손상의 주원인이 된다. 슬라이딩 운동은 축방향 진동 운동과 커플링이 미스얼라인될 때마다 생기는 록킹(Rocking)운동으로 구성된다. 진동운동 속도를 슬라이딩 속도라고 한다. 그림 3-140은 기어 한쪽이 Angular Misalignment된 기어 커플링을 나타낸다. 허브 안쪽에 발달한 치차 패스의 물결 모양은 과도한 미스얼라인먼트에 의한 커플링 손상 특징이다.
적절한 얼라인먼트 상태와 양호한 윤활하에서 기어 커플링은 수년동안 안전하게 기능을 다한다. 그러나 이런 조건이 불량해지면 손상 발생의 신호가 나타나는데, 이것은 실제로 커플링 손상이 발생하기 전에 기계에 좋지 않은 영향을 미친다. 이러한 손상 신호는 미세해서 알기 어렵지만 고장정지를 유발할 수 있다. 특히 미끄럼 마찰계수 증가와 조심하여 조립한 기계에서도 미스얼라인먼트는 항상 존재하므로 이때 생기는 굽힘 모멘트에 의해 축방향 힘이 발생한다. 미스얼라인먼트 영향은 다이어프램 커플링보다 기어 커플링에서 더욱 심각하고 다른 주요 기계 요소까지도 취약하게 한다.
기계문제 전문가는 규칙적인 커플링 점검으로 도움을 얻고, 기어 커플링에 관한 마멸 진행도를 탐지하기 위해 기록과 사진을 보관해야 한다. 이러한 활동을 손쉽게 하기 위해 메트릭스 형태로 표현한 표 3-15를 참조하라.
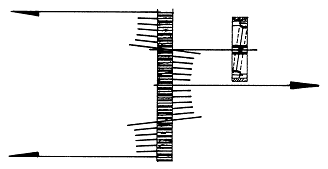
그림 3-140 Angular Misalign된 기어 커플링 한쪽 전개도
표 3-15 기어 커플링의 피로 및 고장 분석
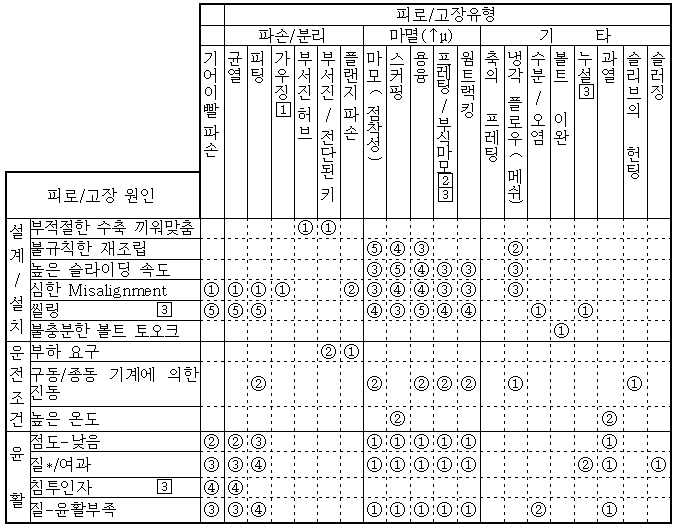
기계부품 손상의 분석 활동에 있어 관련 시스템과 부품의 기능상 특색과 설계에 대한 이해가 필요하다. 이것은 기어 커플링의 손상을 분석할 때 특히 필수적으로 다음의 예는 이를 증명할 것이다.
1972년 Petronta는 압축기의 높은 횡진동이 발생하여 8500 HP 프로필렌 압축기를 정지해야 했다. 고속 커플링의 점검중 허브 기어 이빨의 대부분이 파손된 것이 발견되었다. 그림 3-139의 Spacer 타입 B 커플링은 15년간 사용되었고, 2년 간격으로 재윤활과 병행하여 점검되어 왔다. 커플링의 손상이 매우 심하므로 실험실에서 손상을 분석하기로 결정되었다. 손상 분석 보고서는 다음과 같다 :
1.0 서론 (해설 생략)
2.0 연구 과정과 결과
2.1 육안검사
2.1.1 받은 제출물은 암수 스플라인 부품과 수 부품으로부터 분리된 다양한 스플라인 요소로 구성되었다. 몇몇 요소가 암 스플라인의 바닥에 고착되었는데, 그 요소를 용이하게 제거하려면 지지대 외곽 쪽에 구멍을 뚫어야 했다.
2.1.2 모든 표면은 경미하게 녹이 쓸었고 그리스 흔적이 없는 건조상태였고, 암 스플라인 바닥에 붉은 녹성분이 나타났다. 2가지 예외가 있는데, 허브와 일체로 남은 수 스플라인 요소의 파단면은 원주면의 안이나 스플라인 끝면과 예각을 이루고 있다.
원주 파단면이 생긴 곳은 거의 모든 스플라인이 사라지고, 표면은 부채살 모양이 되었고 극도로 Fretting되었다 (그림 3-141). 부채살 모양을 가진 모든 경우 각 이빨의 스플라인 끝면반경을 잘라내었다. 예각의 파단면은 취성이 지배적이고, 스플라인 루트 반경상에 하중을 받는 측면에서 발단하는 “Sunburst” 취성 파단 모양이 나타났다. 파단면의 채브론 마크 (Chevron Mark)로 대부분의 균열이 반회전 방향으로 발달했음을 알 수 있었다.
2.1.3 조각난 수 스플라인 파단면은 주변의 손상조각이나 허브와 일체로 남아있는 수 스플라인 파단면과 일치하지만, 두 가지 경우에 파단 직전 위치가 예리한 각도로, 지지되지 않은 반경/원주방향 스플라인 끝면 표면에서 나타난 조각들에서 Beach 모양의 표시가 관찰되었다. 이 조각들은 일체의 수 스플라인들과는 공통된 표면을 갖지 않았다. 많은 조각들은 부하를 받은 스플라인 측면 뿌리 원주에서 집중되는 “Sunburst” 파단 모양을 가졌다.
2.1.4 파단이나 눈에 뜨일 정도의 균열 스플라인이 없음을 커플링의 암 부품 실험을 통해 알았지만, 하중 베어링에 심각한 Fretting이 관찰되었다 (그림 3-142). Fretting 패턴은 수 스플라인과 접촉면에 대칭이 아니었다. 모든 경우 명확한 단계를 볼 수 있는데 각기 4개의 다른 깊이를 갖는 Fretting이 한 스플라인 나타났다. Fretting 깊이는 0.001 in에서 0.060 in로 다양하고, 전체적으로 볼 때 그 스플라인은 Fretting 깊이가 같은 영역에서 스플라인 전체에 걸쳐 명확히 진전하는 패턴을 나타내었다.
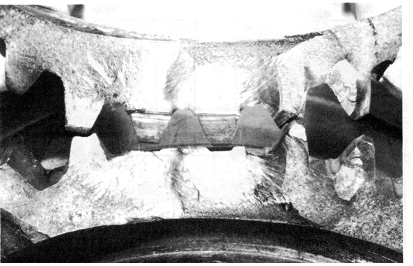
그림 3-141 심하게 Fretting된 부채살 모양의 파단과 “Sunburst” 파단
(1.4배 확대)을 보이는 다중 스플라인 요소 위의 마주하고 있는 부품의 파단면
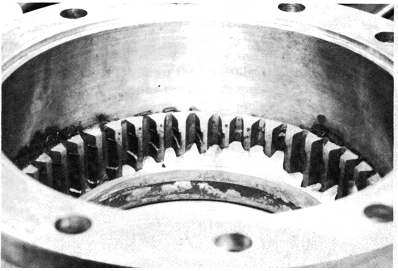
그림 3-142 암 스플라인상의 심각한 Fretting. 함몰된 수 스플라인 요소
(0.5배 확대)를 수반하는 패턴의 감소와 깊이가 일정함을 주시하라.
2.1.5 수 커플링 부품을 다시 조립할 때 각 수 스플라인은 이와 상대되는 암 스플라인과는 다르게 Fretting되었다. 스플라인은 가장 심한 Fretting(그림 3-143)을 나타낸 커플링과 일체인데도, 부러진 몇 조각에서는 Fretting이 거의 없었다. 재조립된 커플링의 암․수 부분 관찰을 통해 Fretting 마멸 패턴이 유사함을 알 수 있었다.
수 스플라인 조각은 그림 3-144의 A에서 T까지 알파벳 순서로 적혀있고 양요소의 패턴이 도면화 되었다. 이러한 실험을 통해, 각 수 스플라인 조각의 Fretting 마크의 깊이와 형상이 암 커플링상의 상대되는 영역과 정확히 일치하고, 파단된 수 커플링 특정부위와 접촉하는 암 커플링에서 힘을 받은 Fretting 마크 깊이는 스플라인 전체에 걸쳐 일정하다. 일반적으로, 깊이가 뚜렷한 Fretting이 4개 관찰된다 (그림 3-144).
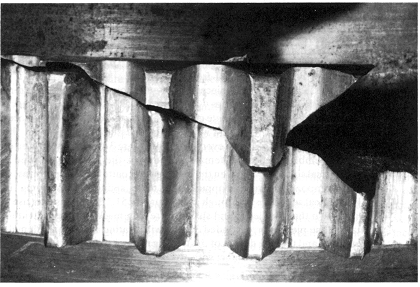
그림 3-143 Fretting(2배 확대)을 유발하는 변경된 치수를
보여주는 다중 스플라인 요소와 일체의 수 스플라인.
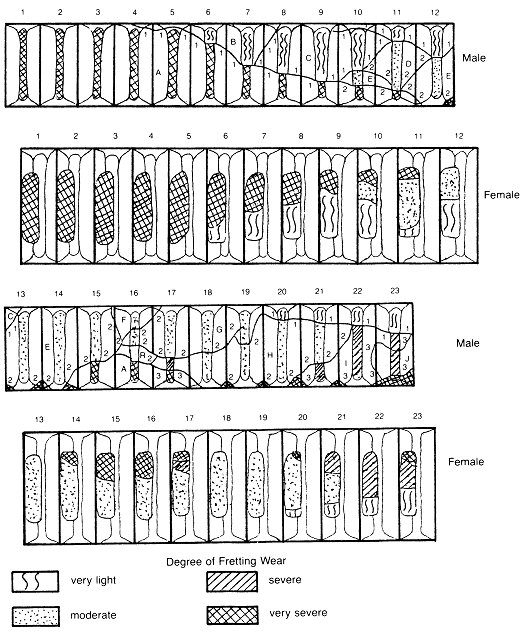
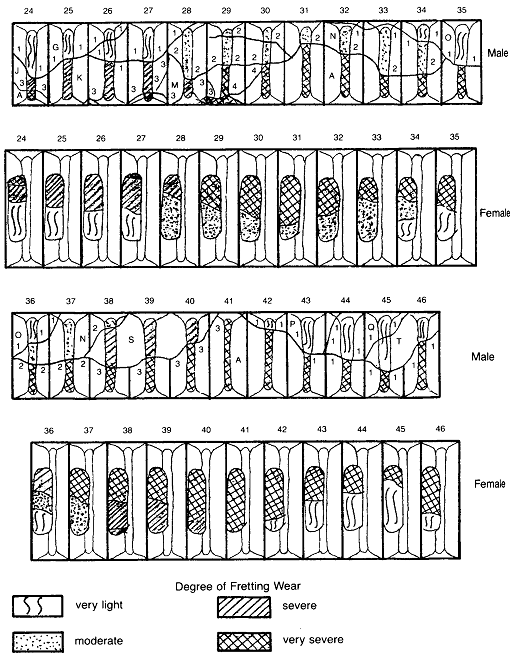
그림 3-144 수 스플라인의 파단 형태와 순서뿐만 아니라 이와 상응하는 암 스플라인의
마멸 형태를 보이는 다이아그램. 균열에 따른 숫자는 균열 발생중 파단상을 나타낸다.
2.1.6 수 스플라인 3조각(그림 3-144에서 R, S, T)은 없어졌지만, 암 커플링과 일치하는 위치에서 이들에 의해 힘을 받는 Fretting 깊이는 주요 4개 범주중 하나로 구분되었다.
2.2 금속조직 검사
2.2.1 금속 조직 검사 목적으로 커플링에서 손상 받은 수 부품의 스플라인 각 요소로부터 대표 단면이 준비되었다.
2.2.2 모든 단면의 구조는 두드러진 함유물질이 없는 대략 뜨임 처리한 마르텐사이트로 구성되어있다. 입자크기는 #4인 ASTM E112이다. 취성 입내 파단의 발달은 “Sunburst” 파단 쪽에서 관찰되었다. “Sunburst”가 집중된 곳에서는 핵을 형성하는 위치에 관한 어떠한 증거도 발견되지 않았다.
2.2.3 육안으로 Fretting이 분명한(그림 3-141에서 스플라인상의 부하 베어링 측면과 플렛팅된 부채살 모양을한 파단면) 표면에 인접 부위를 검사한 결과 심한 구조적 변형이 없음을 보여주었다. 0.0005 in의 균일 산화막이 부채살 모양의 표면에 나타났고 파단진전은 입내 메커니즘에 의해 진전했다.
2.3 경도 시험
2.3.1 경도시험은 횡방향의 수 스플라인 미립시편의 하나의 축을 따라 행해졌고 시작은 Crown부에서 마지막은 허브의 기준 단면에서 취했다. 측정치는 330 HV/313 BHN에서 309 HV/293 BHN 사이였다. 보다 낮은 수치는 보다 큰 기준 단면에서 발생하는 경향이 다소 있었다.
2.3.2 경도 변화를 알기 위하여 정상부위와 Fretting된 파단면 그리고 정상부위와 손상된 “Sunburst” 중심을 Tukon 미세경도계로 시험하였다.
2.4 화학 분석
2.4.1 수 커플링 허브의 드릴링(Drilling)한 것을 분광사진으로 분석하였다. 분석결과 금속은 SAE 4140 타입의 저 합금강이었다.
2.5 스캐닝 전자 현미경 실험
2.5.1 “Sunburst” 파단면, 부채살 모양을 한 부위 및 기준 “Beachmark” 형태의 진전 파손물이 S.E.M 실험과 분석을 위해 연구기관에 제출되었다. 결과는 파손 시기 때문에 신뢰성이 없었다. 고배율에서 정상으로 관찰된 취성, 연성, 피로파손 특징인 틈새, 홈 및 가는 홈이 쉽게 증명되지 않았다. 심하게 Fretting된 부채살 모양의 작은 부위에서 가는 홈 표시는 볼 수 있었지만, 이 표면의 산화층과 눈에 띄는 Fretting으로 볼 때 위에서 관찰된 유용성에 대해서는 확신할 수 없고, 2가지 경우 모두 실제 피로 흠을 감추기도 한다.
3.0 토의
3.1 육안 및 야금 실험으로 취성 파괴 메커니즘에 의해 주요 3, 4개 상(Phase)으로 스플라인 커플링이 손상됨을 알았다. 지배적으로 뚜렷한 4개의 Fretting 깊이중 가장 얇은 Fretting은 0.001 in이고, 가장 깊은 곳은 0.060 in이므로 그리스 주입 운전 이후에 상당한 간격을 두고 파손이 발생했음이 짐작된다. 일반적으로, Fretting 깊이는 수 부품에서 분리된 다중 스플라인 요소의 모든 스플라인에서 일정한 것으로 보아 손상이 급격히 진행된 것으로 보인다. 또한, 심각한 “Sunburst” 파손이 각 요소에 인접한 스플라인에서 발생하는데 이는 요소를 통해 전파하는 앞쪽의 단일 균열과는 대조적인 다중파손 시발점들인 것을 의미한다.
“Sunburst” 파손 형태는 고 에너지의 취성 균열이 주요 크기의 핵에서 외곽으로 퍼지는 특징이 있다. 스플라인의 Fretting된 베어링의 측면 상에 루트 반경에 인접한 핵들을 동반하면서 대다수 수 스플라인 파손면에 이러한 현상이 나타났다.
3.2 취성 분열 손상은 다음 3가지 조건 또는 인자의 조합과 관련이 있다.
a. Notch “Flaw” (중요함) b. 낮은 운전 온도 c. 급격한 변형률 변화
기어 커플링에서 조건 c는 압축기 기동시나 가변속도 유니트인 경우 속도 변환시 발생한다. 온도영향(조건 b)은 손상시간과 그때의 조건을 알 수 없다. Flaw(조건 a)는 기계적(예로 가공 흠, 눌린 자국 및 Fretting에 의한 Notch 등), 야금학적(예로 피로균열, 함유물 등), 화학적(예로 합금 편석, 부식 등) 등이 있다. 취성 “Sunburst” 파손의 핵은 Flaw를 확인하기 위하여 육안검사, 금속조직 사진 S.E.M과 경도 측정기술을 사용하여 정확히 조사된다. Fretting 손상은 Flaw로만 발견되고, 초기 파손후에 발생한다. 작은 피로균열처럼 야금학적 Flaw를 제시할 만한 증거는 없지만 Fretting에 의해 가려진 피로부위를 가진 피로로 시작한 취성 파괴 가능성은 있다. 커플링에 그리스가 전혀 없으면 Fretting을 가속시킨다. 2년마다의 재 그리스 주입은 꽤 충분하다고 증명되었으므로, 그리스가 전혀 없다는 것은 비정상 조건이었음을 나타낸다. 커플링의 미스얼라인먼트는 Fretting과 적용 변형율의 변화를 가속시킨다.
3.3 재료 SAE-4140 타입의 강은 요구되는 경도 범위 내에서 열처리되었지만, 금속조직에서 관찰된 비교적 거친 구조는 취성 파손을 진전시키는 경향이 있다.
4.0 결론
4.1 몇 단계에 걸쳐 취성 파손 메커니즘으로 스플라인의 커플링 손상이 발생했다.
4.2 최종 검사이후의 운전 조건은 비정상이었다.
4.3 재료의 질은 명시된 바와 같다.
커플링 손상의 근본 원인은 무엇인가? 해답은 그림 3-144에 있다. 즉 파동성 마멸패턴이 확실히 나타나 있다. “운전 조건”에 대한 손상 분석가의 설명은 그리스 주입의 단계적인 감소로 인한 심각한 Misalignment였다는 것이다.