Mechanical Seals
5.1 靜止 씰 要素의 熱 龜裂 (Heat Checking of a Stationary Seal Element)
5.2 磨滅된 靜止 씰 要素 (Worn Stationary Seal Element)
5.3 골고루 磨滅된 面 (Matched Worn Faces)
5.4 뒤틀린 靜止 要素 (Distorted Stationary Element)
5.6 고무의 熱 損傷 (Heat-Damaged Rubber)
5.7 酸에 의해 損傷된 고무 (Acid-Damaged Rubber)
5.8 固形物로 코팅된 씰링 要素 (Sealing Elements Coated with Solids)
5.9 硏削劑로 損傷된 슬리브 (Abrasive-Damaged Sleeve)
5.10 軸과 靜止 要素간의 干涉 (Interference between Shaft and Stationary Element)
5.11 干涉에 의한 Seat 龜裂 (Seat Crack by Interference)
5.13 磨滅된 驅動 Lug (Worn Drive Lugs)
5.15 不適合한 씰링 環境의 影響 (Effects of Unsuitable Sealing Environment)
5.16 機械的 및 設置 問題 (Mechanical and Installation Problems)
5.17 씰의 設計와 材料의 選擇 (Seal Design and Material Selection)
화학 공장이나 대규모 정련소의 정비 경비중 적어도 30%는 펌프 수리에 소요된다. 한편 펌프 수리비중 60~70퍼센트가 기계적 씰에 할당되고 있다.
그러므로, 석유화학 산업에서 씰 손상 감소가 기계 기술직원에겐 최우선 과제이다. 만약 문제 해결과정이 조직적이고 철저하지 못하면 근본적인 손상원인을 밝힐 수 없고, 비용 손실을 계속하여 초래하게 된다. 분석내용이 전체적인 Pumping 회로, 운전조건 및 씰과 접촉하는 유체의 물리적 및 열역학적 특성을 포함하고 있는 경우에만 분석 기술자는 성공적 분석을 할 수 있다.
그렇지만, 손상된 씰의 조심스러운 검사는 그 문제점이 씰 선택이나 설치, 액체 환경이나 펌프운전 등에 있는지 밝히는데 도움을 준다. 조심스런 검사는 가능한 방해되지 않는 조건에서 씰 전체가 유용할때만 가능하다. 마멸, 부식, 침식, 결합(Binding), Fretting, 골링(Galling), 러빙(Rubbing), 과열 등의 부품검사는 씰문제 해결에 실마리를 제공한다. 표 3-16과 3-17은 가장 가능성 있는 손상 원인에 대한 지배적인 손상모드를 관련지을 수 있도록 해준다.
표 3-16 기계적 씰의 고장 분석
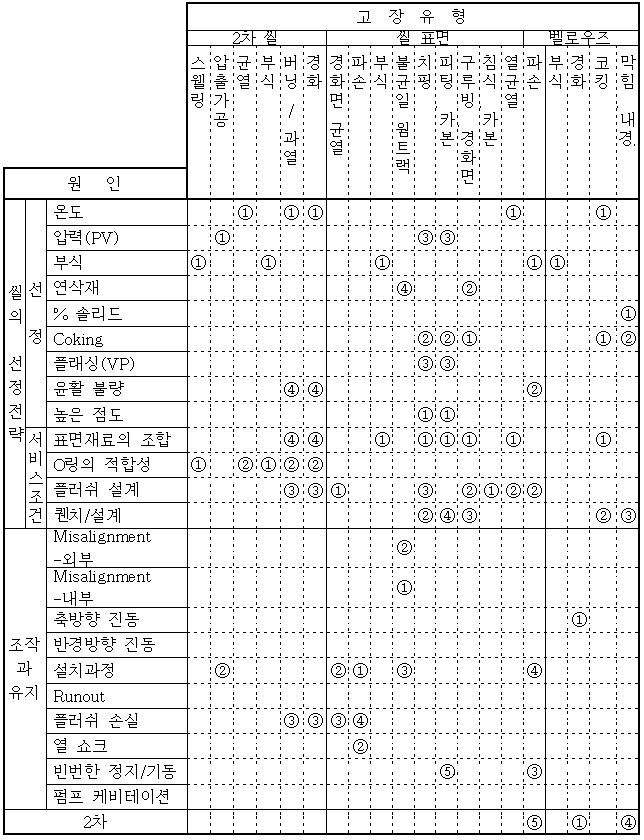
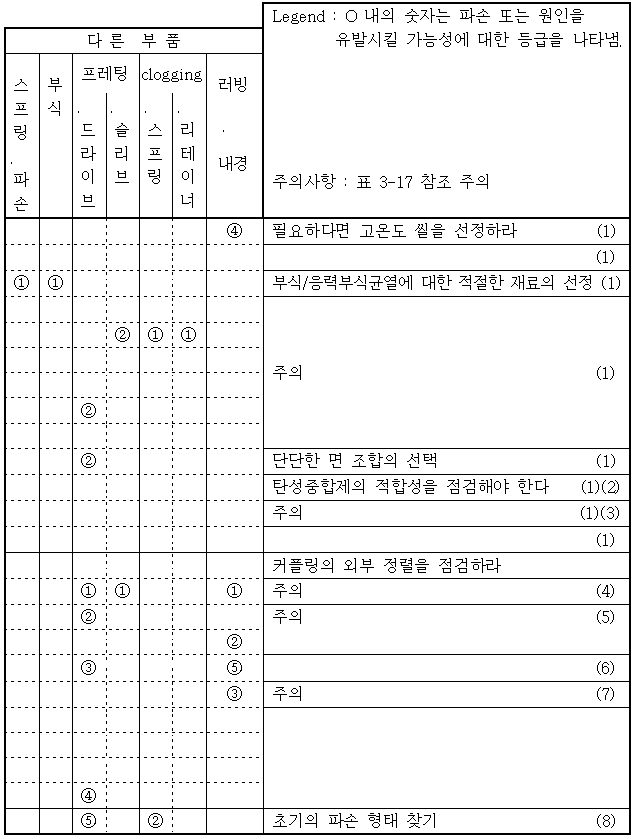
표 13-17 기계적 씰의 고장 분석시 주의 사항
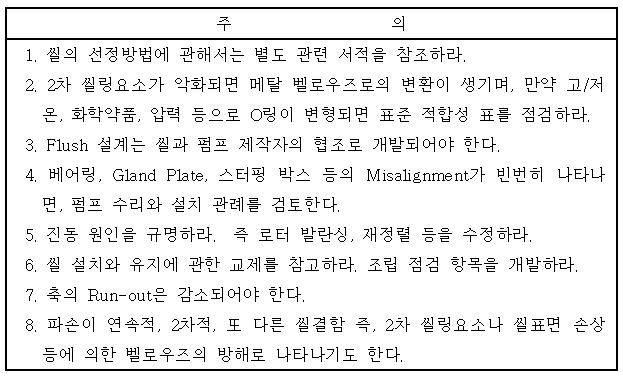
5.1 고정 씰 요소의 열 균열 (Heat Checking of a Stationary Seal Element)
그림 3-145는 비정상 운전시 경금속면에 발생한 내용을 설명하고 있다. 이 특정 조각은 가벼운 탄화수소를 취급하는 프로세서 펌프내의 주조 스텔라이트 씰이다. 이 조각에 대한 씰 운전의 회전요소는 카본이다.
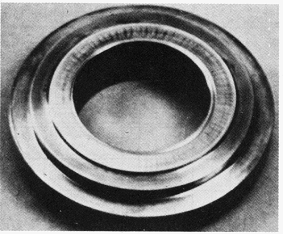
그림 3-145 씰 표면의 윤활막 파괴후 열집중으로 인한 응력 균열
응력균열은 극히 국부적인 상태를 나타내는 카본 회전요소와 직접 접촉한 표면으로 제한되었다는 사실이 중요하다. 다른 부위는 대기온도 상태에 있는데 반해 경금속 표면에 발생한 집중열에 의해 표면균열이 발생했다. 정지요소에 미친 열은 씰 표면간의 윤활막 결핍에 의한 것이 틀림없으며, 윤활막은 회전 및 정지 요소간의 접촉을 방지한다. 어떠한 이유로 윤활막이 파괴되는 순간 높은 열이 발생하며 거의 순간적으로 경금속의 표면이 균열된다.
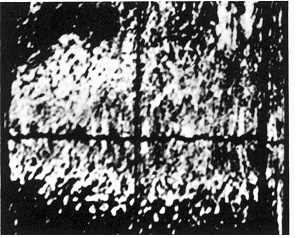
그림 3-146 44배 확대시 나타난 열 균열된 표면
높은 온도에서 금속표면은 팽창하려 하지만, 주위 온도상태에 있는 표면아래의 금속은 표면 금속의 팽창을 방해한다. 표면 금속의 팽창이 선형이 아닌 만큼 위쪽으로 휘게 된다. 실제로 탄성이 없기 때문에 균열이 발생한다. 정지 요소의 평평한 표면 위로 약간 올라온 균열의 모서리는 카본 회전요소 재료를 깎는다.
그림 3-146은 열 균열 상태를 44배 확대한 것이다. 균열 양쪽중 밝은 쪽이 정지요소의 평평한 표면 위로 올라온 쪽의 금속이고, 카본 회전요소로 연속 마모됨을 알 수 있다. 일반적으로, 첫 번째 문제 신호로 씰판 외곽 면에 커다란 카본 찌꺼기가 나타남을 알 수 있다.
경금속의 열 균열은 씰 표면에서 생성된 열 때문이므로, 씰 표면간의 윤활막 파괴를 무엇이 일으키는지 알아내야 한다. 만약 펌프가 저압에서 인화하는 가벼운 탄화수소를 취급한다면 씰의 적절한 플러싱을 위해 씰을 점검해야 한다.
양호한 씰 설치작업을 하려면 청결을 유지하기 위해서는 모든 배관과 씰 Chamber의 개구부를 점검해야 한다. 빈번히, 유체의 재순환을 최소화하거나 압력 감소를 위해 플러싱 라인 내에 오리피스가 설치된다. 오리피스가 사용되는 경우 막힘을 방지하기 위해 직경이 1/8 in 이하가 되어서는 안된다. 펌프의 흡입 손실은 씰 표면의 윤활막 손실을 반드시 일으킨다. 펌프에서 전유량이 흐르는 상태에서 작은 난류가 생길지라도 적절한 씰 윤활의 감소를 초래한다. 부정확한 조립으로 씰 표면에 기계적 과도하중이 가해져도 똑같은 현상이 발생할 수 있다.
무엇이 이같이 단단한 재료의 열 균열을 유발하는지를 밝히는 것은 씰 문제의 원인을 규정하는데 도움을 준다. 연속적인 열 균열에 대한 어떠한 원인도 발견되지 않을 때 대안은 단지 온도차와 조건에 대한 저항성 재료를 사용하는 것이다.
불행하게도, 이러한 조건에 대한 저항 재료는 부식에 대해 양호한 저항을 갖지 못하므로 사용이 제한된다.
5.2 고정 씰 마멸 (Worn Stationary Seal Element)
그림 3-147은 열 균열이 발생하지 않는 스텔라이트의 심한 마멸의 예이다. 여기서 알 수 있는 것은 씰의 윤활은 충분했지만, 펌핑된 액체는 연삭성 입자를 포함하거나 씰 표면사이에서 결정체화하는 경향이 있음을 알 수 있다.
단단한 정지 요소는 완전히 마멸되는 반면, 카본 회전요소는 통상적으로 심하게 마멸된다(때로 마멸이 나타나지 않기도 한다). 연삭 입자가 카본 회전요소 면에 박혀 있을 때 이러한 현상이 발생하기도 하고, 이것이 단단한 정지 요소에 대해 그라인딩 공구 작용을 한다. 결정체화 경향이 있는 액체를 취급할 때 그같은 현상이 발생할 수 있다. 보통, 연삭 결정체는 카본 면을 완벽히 코팅하므로써 정지요소는 마멸되는 반면 이것은 마멸로부터 보호된다.
이러한 현상을 해소시키기 위해서는 씰 표면에 침전 결정체나 연삭액을 다루는 방법중 하나로 씰 표면으로부터의 연삭제를 제외시켜야 함이 분명하다.
5.3 골고루 마멸된 면 (Matched Worn Faces)
그림 3-148은 심하게 홈이나 있고 마멸된 씰 표면이 어떻게 해서 씰링 유체 작업을 잘 수행하는지를 보여주고 있다.
이들 씰 표면의 마멸은 계속되었고 평평하지 않는데도 상당기간동안 만족스런 운전이 이루어졌다. 그런데 이 같은 조건에서 씰면이 만족스럽게 임무를 수행할 수 있었던 것은 오직 정확히 조립되었고 안정한 운전특성을 가졌기 때문이다. 축의 Runout은 표면의 일치를 방해하여 심한 누설을 일으키는 것을 쉽게 볼 수 있다. 정지요소 구조가 대칭이므로 반대측도 원래 설치시의 씰면으로 사용되어 동일한 마멸 형태가 발생하므로 이 부위는 2배 역할을 할 수 있다. 그림 3-148은 최상의 씰 수명을 위해 원활한 운전을 하는 장비를 가지는 장점을 나타낸다.
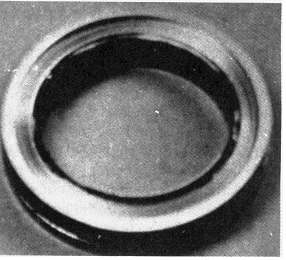
그림 3-147 연삭에 의한 스텔라이트 시트(Seat)의 심한 마모
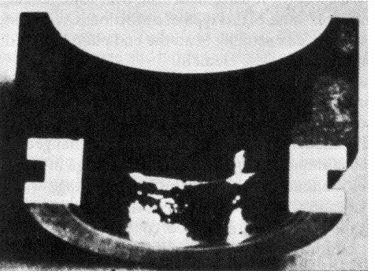
그림 3-148 안전하게 연속 운전하는 골고루 마멸된 씰면
5.4 뒤틀린 고정 요소 (Distorted Stationary Element)
그림 3-149는 운전중에 심하게 뒤틀린 정지요소 인데, 이것은 씰면간에 접촉이 중단된 형태로 나타났다. 유니트에 설치되기전 이 부품의 평평도에 관해서는 의심이 없었고, 이 유니트는 압력이 높은 배관에서 정제된 석유제품을 취급하는 다단계 펌프이다. 이 부품이 제작자에게 되돌아갔을때 운전중에는 뒤틀렸어도 평평한 상태임을 알았다. 즉 제거 후에는 원래의 평평한 상태가 되었다. 펌프 Stuffing Box에 체결된 씰판 Counterbore에 조립하는 연삭한 정지부의 뒤틀림은 설치중에 발생되었다.
소량의 유체가 누설하고 있던 교체 씰을 검사하기로 결정하였다. 이러한 뒤틀림의 통상 원인은 Gland 볼트의 과도한 조임이다. 몇몇의 경우 이런 작업은 실제로 End Plate를 휘게할 수 있어 연삭된 정지요소의 지지표면을 뒤틀리게 한다.
Seal Chamber의 고압은 End Plate의 지지표면에 순응하도록 연삭한 부품에 힘을 가하므로 더 이상 평평하지 않게 된다.
이러한 이유로 End Plate 볼트를 1/4 바퀴정도 풀어놓으면 갑자기 누설 양상이 변화된다. 이것은 연삭한 정지요소가 볼트 인장의 변화로 다시 작용하고 있음을 의미한다. 글랜드 볼트의 인장을 조심스럽게 조정하면 누설이 거의 0까지 감소된다. 볼트의 인장이 다시 증가되었을 때 씰은 갑자기 작은 량이 누설되었다. 글랜드 볼트에 가해지는 인장량으로 누설률이 용이하게 조절될 수 있다.
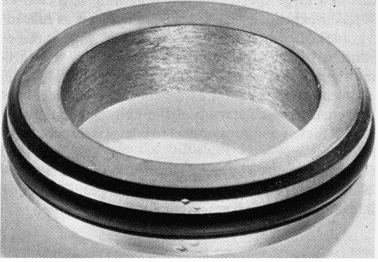
그림 3-149 심하게 뒤틀린 면에 의한 중단된 접촉 형태
5.5 카본 폭발 (Exploded Carbon) (Exploded Carbon)
그림 3-150은 찬 대기 중에 작동하는 큰 속도의 감속기 씰의 카본 회전요소의 면에 나타난 매우 비정상 상태를 보여주고 있다.
카본 회전요소 공급자는 이러한 손상모드를 표면의 열이 높기 때문이라고 설명했다. 수지(Resin) 필터를 갖는 어떤 카본 등급에서는 고열의 표면은 카본내 기공을 채우는데 사용된 수지의 순간 팽창을 유발한다. 이 갑작스런 팽창은 재료의 작은 단면을 분해시켜 카본 표면아래에서 작은 폭발을 유발한다. 유니트 기동시마다 카본의 몇개 입자만이 분해되어 이러한 상황이 진전되는 것이다. 연마한 표면을 지나 누설경로를 형성하도록 일련의 이러한 공간이 완전히 연결될 때까지는 씰의 손상은 실제로 발생하지 않는다.
표면의 고열은 씰의 윤활 부족에 기인한다. 유니트가 찬 대기 상태에서 기동되면 기어에 부착된 기어 케이스내의 중유의 높이는 축의 위치 아래로 낮아진다. 이러한 타입의 장비에서 실제 시험한 결과 순간적으로 오일의 높이가 축 위치 이하로 떨어져 적절한 씰 윤활을 위한 적정 위치까지 회복하는데 2~5분이 걸렸다. 이러한 문제점을 해소시키기 위해 개발한 수지가 없는 카본을 사용하여 이러한 문제를 교정하였다. 청동과 경화된 씰표면의 조합도 그와 같은 응용에 대해 좋은 결과로 이용된다.
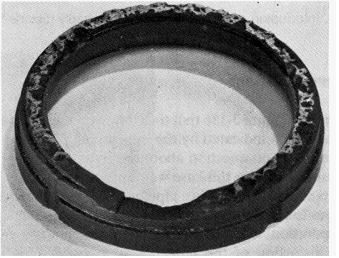
그림 3-150 표면의 고열에 의한 회전 카본 요소의 손상
5.6 고무의 열 손상 (Heat-Damaged Rubber)
그림 3-151의 오른쪽 단면은 펌프 몸체나 Seal Plate에 대해 세라믹을 밀봉하는 고무컵에 설치된 세라믹 정지요소를 보여준다. 고무컵은 더 이상 탄성의 씰링체로써 기능을 다할 수 없다. 불충분한 윤활상태로 씰을 운전하여 생성된 열이 이 부품에 전이되어 결국 고무의 경화와 균열을 초래하였다.
그림 3-151의 좌측의 위쪽 그림처럼 이와 동일한 조건은 고무 회전 씰 요소에서도 유사한 손상을 초래한다. 사진 아래쪽은 고무와 세라믹의 조립품에 대하여 회전하는 카본 회전 씰 와셔이다. 씰면의 생성열은 카본 와셔에 의해 고무 씰링 요소의 플랜지부분으로 전이된다. 고무 씰링요소면의 경화와 균열은 이것과 카본 와셔간의 Liquid-Tight Fit를 파괴한다. 부품조건은 합성고무 씰링 요소의 범위를 초과한 온도에서 사용하여 씰의 오적용이나 설치 잘못을 검출하는데 도움을 준다.
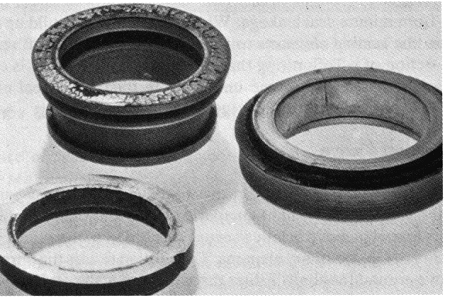
그림 3-151 운전중에 깨진 고무컵에 설치된 세라믹 정지요소
5.7 산에 의해 손상된 고무 (Acid-Damaged Rubber)
그림 3-152는 합성고무 씰의 황산 잔류분에 의한 영향을 나타낸다. 사용자가 씰 제작자에게 제공한 사용방법에 기초하면 고무맞춤 씰은 완벽하게 만족스러웠지만, 사용자는 얼마후 씰문제에 부닥쳤고 손상된 고무 요소의 검사를 위해서 씰 공급자에게 보냈다. 씰은 원래 사용하기로 되어있던 가벼운 탄화수소 이외의 다른 물체를 취급하고 있었던 것이 분명하였다.
시스템의 실제 상태를 재검토한 후, 유체 내에 H2SO4 흔적이 발견되었다. Teflon 씰링 요소를 갖는 씰을 이용하여 이 문제는 간단히 해결되었다.
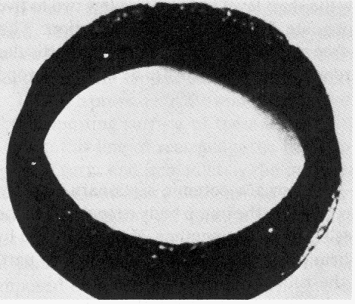
그림 3-152 합성고무 씰요소에서의 황산 흔적 영향
5.8 고형물로 코팅괸 씰링 요소 (Sealing Elements Coated with Solids)
앞서 언급된 바와 같이 증발로부터 침전물을 남기는 액체나 연삭액으로 인해 심각한 손상이 유발될 수 있다. 그림 3-153은 부유물 내의 연삭제를 가지는 액체 내에서 운전하던 카본 와셔와 Teflon으로된 쐐기형의 씰링이다.
양쪽 부품은 모두 초기의 씰손상을 유발하는 고운 연삭제로 코팅되었다. 이와 동일한 고형물질이 씰면의 바로 아래와 축위에서 보통 발견된다. 이 침전물이 축에 생성되면 축에 대해 씰링요소를 고정시키고 모든 씰의 탄성을 제거시킨다.
또한, 닦고난후 Teflon링 단면을 본 결과 Teflon 씰요소내에 연삭입자가 박혀있었고, 이것이 직접 축마모를 유발하기도 한다.
5.9 연삭제로 손상된 슬리브 (Abrasive-Damaged Sleeve)
그림 3-154는 씰링요소와 축간의 연삭입자의 영향을 보여주고 있다. 정지 씰요소가 약간 기울면 이를 보상하기 위해서 Teflon 쐐기는 축의 매 회전시 축방향으로 이동한다. 이러한 이동으로 연삭입자가 축주위의 홈을 마멸시킨다. 이리하여 축과 Teflon 쐐기간의 씰을 파괴하거나, 쐐기가 홈내에 고정되어 씰의 탄성을 파괴한다. 축의 홈은 가능한 축에 거의 직각으로 정지요소를 설치하는 것이 중요함을 나타내고 있다.
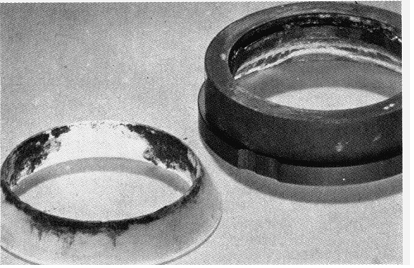
그림 3-153 급격한 마멸을 유발한 Teflon 씰요소에 박힌 연삭 코팅
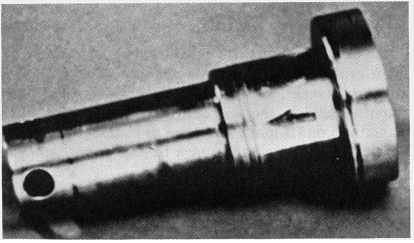
그림 3-154 마멸을 유발하는 축과 씰링 요소간에 적재된 연삭입자
5.10 축과 고정요소간의 간섭 (Interference between Shaft and Stationary Element)
씰 손상의 원인은 때로 정지 씰요소 검사로 쉽게 검출될 수 있다.
그림 3-155의 상태는 불충분한 Bore의 틈새, 축의 Runout 또는 축과 펌프 스터핑 상자간의 편심 등으로 초래된다. 금속간 접촉에 의한 열때문에 가연성의 액을 취급할 때는 이러한 씰 손상은 극도로 위험하다.
석유화학 공장의 그림 3-155와 같은 손상은 펌프 케이싱의 노즐하중을 유발하는 파이프의 설치 오류에 의한 것이다. 국부적인 휨은 축의 외경과 스터핑 박스 Bore간의 심한 미스얼라인먼트를 초래한다.
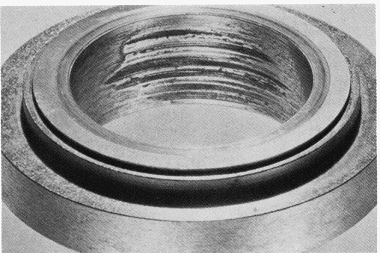
그림 3-155 시트 Bore의 상에서의 Rub를 일으킨 펌프 스터핑 박스 부품의 국부적인 손상
가연성 유체를 다루는 주요기계에서는 스파킹 없는 부싱이 사용되어야 한다. 이것은 정지 요소 보다 미세한 정도로 작은 내경을 가져야 하며, 이렇게 하므로써 축과 정지 요소간의 접촉을 방지할 수 있다. 씰의 설계가 어떻든 간에 End Plate의 부싱 내경과 축간 간극은 Feeler Gage로 정확히 점검하는 것이 중요하다. 간극은 접촉을 피할 정도로 충분해야 한다.
5.11 간섭에 의한 씰 균열 (Seat Crack by Interference)
그림 3-155의 부품은 매우 심한 손상으로 나타나지 않았지만, 그 손상은 정지요소의 연삭 면의 평평도를 흩트릴 만큼 충분하다. 그림 3-155는 심한 온도차를 견디는 니켈-철 합금으로 만들어진 부품이다. 한편, 그림 3-156은 실제 3조각으로 균열된 코발트-크롬 합금으로 만들어진 유사 부품이다.
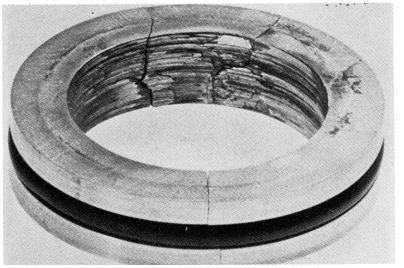
그림 3-156 정지 부품의 평평도를 망가트린 상승한 온도에서의 간섭 맞춤
5.12 가스켓 결함 (Faulty Gasket)
기계 씰에서 누설이 실제로는 다른 곳이 근원인 경우가 빈번히 발견된다. 가장 일반적인 예중의 하나는 마운팅된 씰의 슬리브와 펌프축 사이의 누설이다. 어떤 경우에는 개스킷을 빠트리고 설치한 경우가 있다.
축과 슬리브간의 부적절한 가스켓팅은 씰을 교체해도 일정한 누설을 야기한다. 만약, 씰 전체에서 누설이 있다면 시간이 경과함에 따라 누설정도가 변할 것이다. 한 예로, 알루미늄 개스킷이 슬리브를 축에 밀봉 할 때 사용되었다. 처음에 씰의 누설이 예상되었는데 분해결과 완전한 상태이었다. 누설의 원인을 더 찾아본 결과, 그림 3-157의 한 단면에서 알루미늄 개스킷이 거의 침식된 것이 발견되었다.
이는 고압에 적용되었고, 개스킷이나 이와 인접면상의 미세한 결함으로 소량의 누설을 일으켰으나 압력이 높은 액체에 의한 침식으로 더욱 증가하였다. 다른 경우 한 펌프에서 4, 5번의 씰교체 후에도 누설이 지속되었다. 씰이 설치된 청동 슬리브가 구멍이 나있었고 액체는 씰을 우회하여 흐르고 있음이 최종 발견되었다.
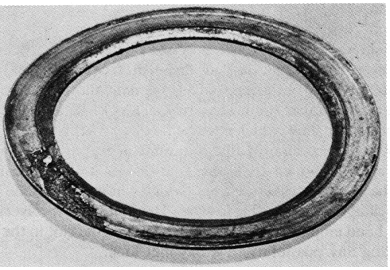
그림 3-157 결함있는 개스킷이 누설 통로를 생성시켜 씰의 변형을 초래하였다.
5.13 마멸된 구동 러그 (Worn Drive Lugs)
그림 3-158은 2개의 Interlocking Stamping을 통하여 씰면에서 생성된 토오크를 전달하는 마찰 구동 타입의 고무 씰의 회전체를 나타낸다. 부품이 맞물리는 점의 마멸은 두 부품을 Bayonet Lock과 유사한 방식으로 잠겨지는 것에 주의하라. 이러한 상태는 Outer Shell의 자유로운 이동을 못하게 하므로 씰면이 접촉하도록 유연성이 있어야 한다.
이러한 형태의 마멸은 잦은 기동과 정지하는 유니트에서 통상 발견되기도 하고 기어 구동 유니트에서도 나타난다. 한가지 예상되는 원인은 정지 씰요소의 모서리가 있어 Interlocking 부품간의 어떤 운동을 일으켜 마멸을 일으킨다. 이러한 상태는 특수 구동 Band를 가지는 Lug를 사용하고 Bayonet Lock와 같은 가능성을 제거하므로써 교정된다.
5.14 펌프내 이물질 (Debris in Pump)
흥미 있는 것은 고층 건물내에 제공되는 공기 정화장치의 고압 냉각수 펌프이다. 이 특정 펌프의 과도 진동이 씰의 성능에 영향을 주는 것을 알았다. 펌프 분해시 다양한 크기의 석조물 조각이 임펠러내에 적재된체 발견되었다. 몇몇 예는 그림 3-159와 같다(골프공은 크기 비교를 위한 것이다).
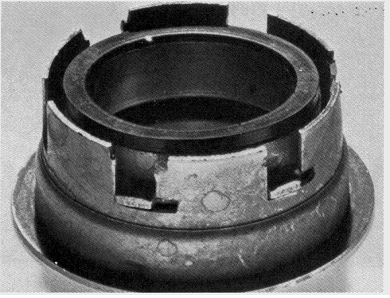
그림 3-158 씰 거동이 제한 받는 마멸된 구동 러그
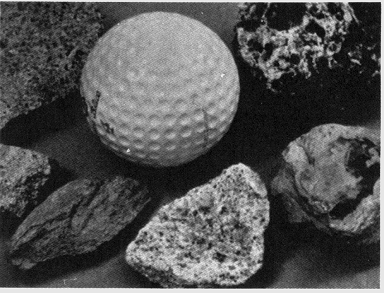
그림 3-159 펌프내 파편은 씰에 나쁜 영향을 준다.
5.15 부적합한 씰링 환경의 영향 (Effects of Unsuitable Sealing Environment)
“부적합한 환경”은 건식 운전으로부터 과도한 점성유체의 씰작동에 이르기까지 모두 포함한다. 이로 인한 손상을 설명하기 위한 몇 가지 전형적인 예를 보여준다.
그림 3-160은 오물처리 공장에서 제거된 씰이고, 씰의 재료는 천연 고무를 가진 카본을 변환한 실리콘-커버이드이다. 이 유니트는 건식 운전으로 손상되었고, 실리콘-커버이드 두께를 규정하는 링은 깨졌다.
그림 3-161과 같이 에지테이터 씰에 적용시, 1차 Ring과 상대 Ring은 텅스텐-커버이드로 이 손상은 저점성 유체에서 운전한 결과이다. 이러한 경우 씰 윤활제는 실리콘 오일이고, 씰의 수명은 11개월이었다. 1차 카본링은 씰 Nose에서 반경 내에서 마멸되었다. 상대링으로의 마멸은 1/8 in 정도였다. 이러한 상태는 씰 챔버의 윤활제 교체로 해결하였고 교체 유체로써 물을 사용하였다.
그림 3-162는 오일 안개 상태에서 속도 19,000 rpm으로 스텐레스 강에 경크롬 도금을 한 결과를 나타낸다. 씰면에 이렇다할 압력은 없었고, 씰의 수명은 불과 며칠이었다. 열로 인해 코팅 면의 경크롬 도금이 조각났다. 씰의 직경은 1 1/2 in 이다. 코팅 시트를 적용할 때는 사용 재료의 최대 PV(압력, 속도)값의 관찰이 필요하다. 경험상 코팅된 시트는 100,000 PV 이하로 하라.
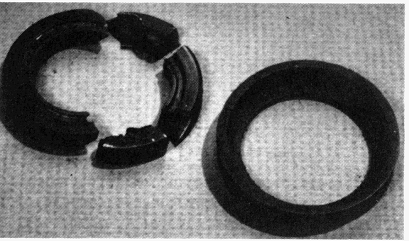
그림 3-160 건식 운전으로 손상된 실리콘-커버이드 씰
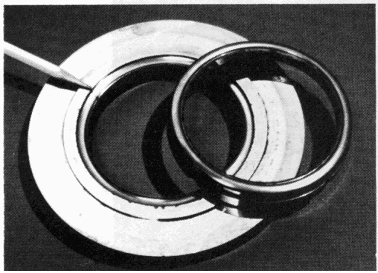
그림 3-161 씰링 유체의 불충분한 점성의 영향
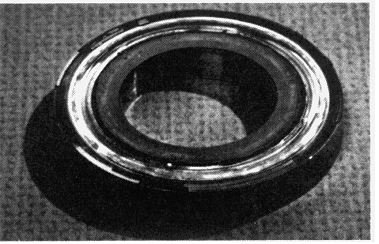
그림 3-162 경크롬 도금된 시트는 높은 Pv값을 견디지 못한다.
Seal Cavity내에서 유체의 증기가 발생하면 손상은 심해진다. 그림 3-163은 유체가 대기의 끓는 점 근처나 그 이상에서 운전되어온 금속 벨로우즈 씰이다. 1차 및 상대 Ring의 텅스텐-커버이드 표면에서의 심각한 마멸과 Seal Head 내경에서 금속 벨로우즈의 처음 회돌이가 갈라진 것에 주시하라. 고온에서 윤활 성능이 좋지 못한 윤활유를 사용할 때에는 끓는점에서 적어도 이하에서 운전하는 것이 좋다.
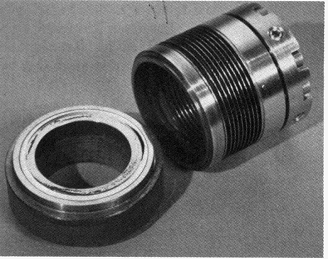
그림 3-163 Seal Cavity에서 유체의 증발은 금속 벨로우즈 씰의 손상을 유도한다.
5.16 기계적 및 설치 문제 (Mechanical and Installation Problems)
설치와 관계된 씰문제가 “변형”과 “간섭”항에서 앞서 언급했지만 아래 몇 가지의 부가 사진을 사용하여 재강조 한다.
그림 3-164는 고압의 씰에 사용하는 1차 카본링이다. 이 유니트는 배관상에서 운전중이었고, 연삭제가 내재되어 있어 Gland Plate와 상대 Ring의 변형된 것으로, 와이어 브러싱(Wire Brushing)이 씰면에 발생했다. 뒤틀림 원인을 확인 및 수정하므로써 이러한 현상은 제거된다.
그림 3-165의 씰은 오물을 취급하는데 사용되었다. 유니트는 누설이 발생하기전 잠시동안만 운전되었다. 니켈 저항 시트의 심각한 홈을 주시하라. 그것은 고형물 높이로 씰을 운전하므로써 생겼다. 리테이너 뒤쪽이 뒤틀렸음에 주시하라. 이는 누설을 가속시키는 설치의 결함을 의미한다.
그림 3-166은 처음으로 23개월 정도 운전되어온 씰이다. 조립시 앞의 어댑터를 분리하는 스플리트 벨로우즈 뿐만 아니라 텅스텐 씰면의 심각한 마멸을 주시하라. 이런 상태는 펌프의 기계적 상태에 관계한다. 동일한 씰을 설치할 때는 시간상의 문제에 부닥친다. 축방향 운동과 얼라인먼트 측면에서의 펌프의 운전 변수가 제작자의 허용 범위내에서 운전할 만큼 수정되지 않는 한 그 문제는 수정되지 않는다. 높은 온도에 적용할 때는 배관 변형이 펌프 케이싱에 전달되어 얼라인먼트 문제를 야기하는지를 확인하는 것이 좋다.
가혹한 기동과 정지는 2차적인 씰 문제를 야기한다. 그림 3-167의 Drive Notch에서 첫 번째 카본링과 스프링 및 금속성 디스크상의 마멸을 관찰하라. 리테이너 내면상의 접촉 패턴과 스프링 홈에서의 스프링 접촉 패턴을 주시하라. 기동과 정지운동 및 직각도가 아닌 결과로 인해 첫 번째 링의 내경에는 많은 재료가 쌓였다. 축을 따라 거동하는 쐐기(Wedge)때문에 Teflon 마멸이 발생했다. 이 경우에 씰면의 얼라인먼트를 개선하면 씰의 수명도 길어진다.
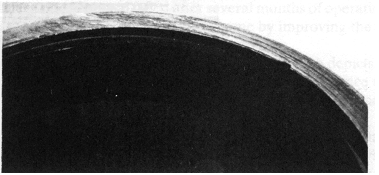
그림 3-164 Gland Plate대 상대 Ring의 변형에 의한 씰면에서의 Wire Brushing
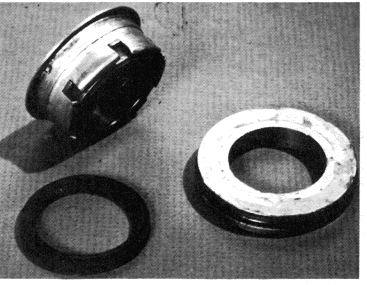
그림 3-165 설치 오류로 손상 받은 니켈 저항 씰 시트
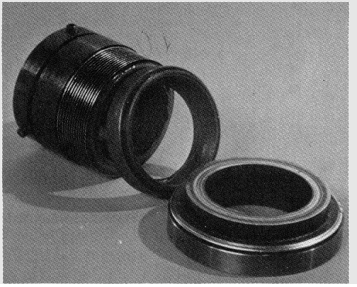
그림 3-166 씰의 손상을 일으키는 펌프의 기계적 문제
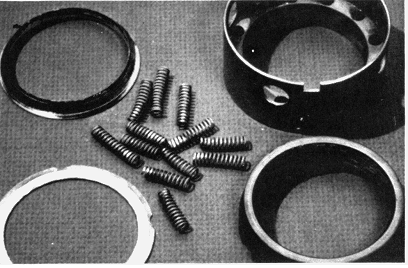
그림 3-167 마멸을 가속시킨 씰면의 미스얼라인먼트
5.17 씰의 설계와 재료의 선택 (Seal Design and Material Selection)
씰 설계의 특색, 조립 틈새와 재료 선택은 씰 제작자의 권리이다. 이러한 변수에 작용하는 씰의 결함은 2가지 그룹으로서, 사용상 정보 오류에 의한 구입자 결함과 생산자에 의한 기본적인 적용결함이나 설계상 오류이다.
그림 3-168은 탈 이온수에 노출된 공기 압축기의 씰이다. 카본이나 리테이너 쉘에 생성된 부식물을 주시하라. 조립품의 웨이브 스프링은 첫 번째 카본링 뒤편을 마멸 시켰다. 씰이 유연성을 잃었기 때문에 몇 개월의 운전후 손상되었고, 씰 설계시 간극 개선으로 극복되었다.
그림 3-169에서 씰 손상의 두 가지 형태는 배관 프로젝트에서의 씰이다. 첫째로, Gland와 접촉하는 면의 칼라 상태를 주시하라. 이 유니트는 그곳에 스페이서를 넣고 기동했는데 그곳에서 열 생성으로 어려움을 겪었다.
또한, 이 씰은 410 스텐레스강 슬리브에서 작동하는 청동 와셔의 부적합을 보인다. 부품간의 전기적 작용으로 인한 슬리브와 와셔간의 부식을 주시하라. 원유를 취급하므로써 생기는 연삭문제를 극복하기 위해 청동을 선택하였다. 부식 생성물로 연성을 잃어 씰이 손상되었다. 슬리브의 손상은 운전중에 발생한 극심한 피팅이며, 청동 와셔는 완전히 검게 변했다. 이 문제는 카본 재질을 변환한 실리콘 커버이드 사용으로 극복하였다.
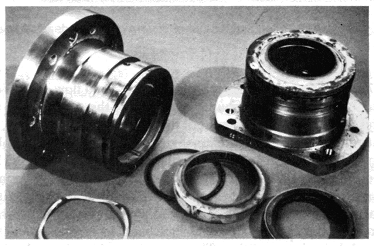
그림 3-168 씰의 연성을 잃게 한 부식물로 쓸모 없게 된다.
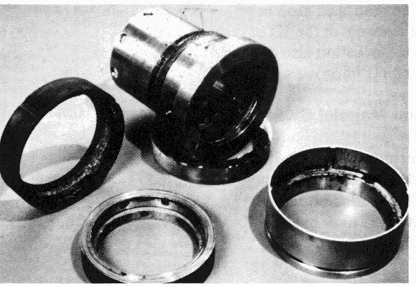
그림 3-169 재료 선택 오류에 의한 씰의 손상
그림 3-170은 정련소의 씰을 나타낸다. 시트 뒤쪽에서 Teflon의 저온소성 흐름이 상대 Ring의 직각 상태를 흩트려 파인 곳에서 큰 마멸을 일으키고 Retainer내의 스프링을 마멸시킨다. 이것은 또한 장비에서 상대링의 얼라인먼트나 직각도 문제로 예상되는 일상적인 것이다. 이와 같은 경우, 유니트는 유동하는 Teflon 시트의 최대 운전능력을 초과하여 사용되었다. 이것은 Viton O링의 사각 단면 텅스텐 커버이드 시트를 적용하여 수정되었다.
텅스텐 커버이드 상대링에 대해 회전한 실리콘 커버이드 제 1링은 그림 3-171과 같다. 이 씰은 극도로 취약한 윤활 품질을 가진 유체에서 사용되었다. 텅스텐 커버이드는 열균열 되었고, 실리콘 커버이드는 텅스텐 커버이드 몸체 내로 0.030 in 정도 마멸되었다. 밀봉된 유체는 1200 psi와 3600 rpm에서의 에탄이고, 마멸 패턴은 불량 윤활 상태를 나타낸다. 이 씰은 구성 재료에 추가의 윤활을 제공하지 않는 단단한 면을 갖는다. 이 문제는 텅스텐 커버이드 대신 카본으로된 Hydropad를 사용하여 해결하였다. 이러한 씰 부품은 근본적으로 적용 분류가 잘못되었다.
그림 3-172는 코발트-고착제 텅스텐 커버이드의 부식을 나타낸다. 만약, 그것이 적용상 적절히 선정되지 않았다면 니켈-결합 텅스텐 커버이드에도 발생했을 것이다. 화학적 부식은 단지 펌핑 물질에 노출된 면에서만 발생함을 주시하라. 고정된 시트의 개스킷 면에는 부식이 없다. 선택된 재료의 부식률은 년간 0.002 in 이하임을 항시 확인하라.
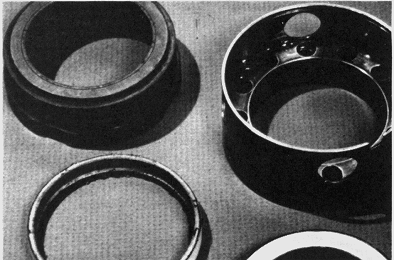
그림 3-170 Teflon의 저온 소성 흐름이 직각 상태를 흩트려 씰 손상을 유도한다.
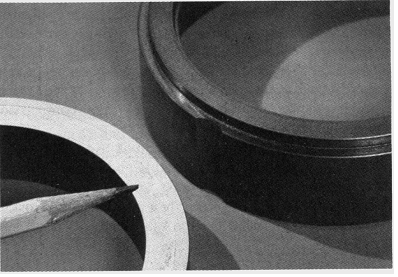
그림 3-171 부적합 부품을 파괴한 씰링 유체의 취약한 윤활
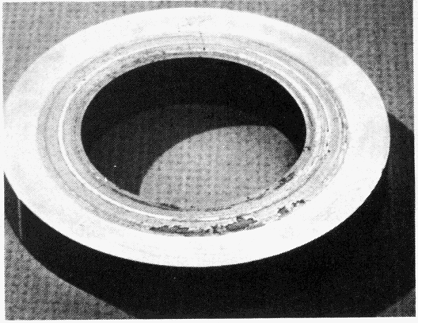
그림 3-172 부식에 의해 손상된 코발트-결합 텅스텐 커버이드
Control-Loop 설계결함에 의한 최종 결과는 그림 3-173과 같다. 이 결함으로 에지테이터 안쪽의 특수 고압씰의 손상이 발생하였다. 이중 Seal Chamber에서 압력을 잃을 때 와셔는 내부고압에 직면하여 그 압력이 카본와셔를 파괴시켜 금속 리테이너의 Ear를 휘게 하였다. 이 문제는 씰 외경쪽에 압력을 적절히 유지하도록 조절기능을 추가하여 해결하였다.
적절한 재료 선택의 중요성을 재강조 한다. 그림 3-174는 화학공장에서 경험한 금속 벨로우즈 씰 헤드이다. 어댑터 앞쪽이 벨로우즈에서 부러져 나가고 재료는 벨로우즈의 회선에 쌓였다. 이것은 원래 씰헤드에 사용된 구성재료에 영향을 주는 부식 문제이다.
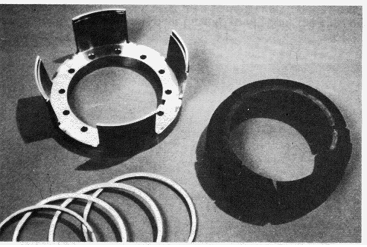
그림 3-173 고압으로 파괴된 카본 와셔
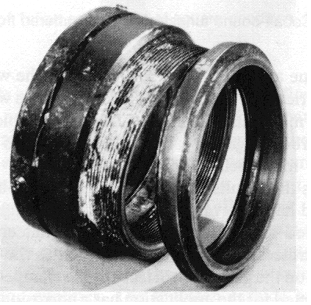
그림 3-174 부식된 금속 벨로우즈 씰
5.18 요약 (Summary)
언급한 문제의 원인은 다음과 같이 종합하여 표현할 수 있다. 열, 연삭, 미스얼라인먼트, 설치오류, 조건제원 오류, 재료선택 오류, 설계상 펌프운전의 오류 등이다. 이러한 모든 씰손상의 원인은 설계, 설치, 정비, 펌프 운전 등에 주의를 기울이면 제거되거나 해결될 수 있다. 씰문제를 해결하기 위해서는 문제 해결사나 분석가는 결함의 근원에 대한 실마리를 확인하기 위하여 검사해야 한다. 손상 징후를 관찰하는 것만으로도 도움을 받지만, 체계적인 접근 방법을 이용하여 단지 근본 원인을 다루는 방향으로만 정열을 쏟아야 한다.