Glitch (Runout)
공장에서는 회전체의 진동진폭을 측정하기 위한 표준 계측기로써 Proximity Probe나 Eddy Current Probe를 채용해 왔다. 불행하게도 계측기는 축재료의 물리적 및 기계적 결함에 의해 원인이 된 틀린 값과 실제 진동간의 구별이 불가능하다. 이 틀린 값을 통틀어서 Glitch라고 하며 이는 기계적 및 전기적 Runout의 조합이다.
여기서 논의할 바는 Glitch의 원인을 확인하고, 그 성분의 측정방법을 보여주고, Glitch의 제거방법을 논의하고 제작설비에 적용을 위한 표준방법의 제안이다.
10.13.1 비접촉 변위센서 (Proximity Probe)
Proximity Probe란 기본적으로 Holder 끝에 있는 Ceramic Tip내에 심어 놓은 작은 Coil 선이다. 이 Coil은 Probe Tip으로부터 발산하는 자장을 생성하는 고주파수 전압이 공급된다. 이 자장 내에 놓여 있는 어떤 도체 표면도 이 힘을 다소간 흡수하며 Tip에 가까울수록 흡수하는 힘은 더 커진다. Coil로의 RF(Radio Frequency)신호는 Proximitor에 의해 공급되며, Proximitor는 자계의 강도를 전압으로 변환시켜 지시계로 되돌려 보내는 2차적인 기능을 가지고 있다.
Proximitor와 Probe는 지시전압과 목표와의 거리간의 선형관계를 주도록 교정된다. 이 선형관계의 범위는 Probe 형태 및 공급전압에 따라 다르지만 80 mils 정도이다.
이론적으로는 Gap이 50 mils이면 항상 동일한 전압 출력을 나타내야 하는데 불행하게도 그렇지 않으며 재질이 다르면 크게 다른 전압 출력치를 나타낸다(예를 들면 50 mils Gap에서 4140 Steel은 7 Volt를, Brass인 경우는 거의 11 Volt를 나타낸다). 동일한 재질이라도 주어진 거리에 대하여 다소 다른 전압출력을 나타낼 수 있는데 이를 전기적인 Runout이라 하며, 이는 잔류자기, 표면경도, 도자성, 미시적 구조, 및 화학적 성분의 편차에 의해 원인이 된다.
반경방향으로 설치된 Probe로부터 취한 지시치는 축 재질로부터 Probe까지의 최소 및 최대 거리간을 전기적으로 측정한 차이이다(Peak to Peak 진폭). 이것은 진동, 전기적 Runout 및 기계적 Runout으로 이루어진 것이다. 진동과 전기적 Runout이 없다면 축이 회전하면서 Probe로부터 기록되는 변화량은 편심, 축의 휨 또는 표면가공에 따른 불규칙한 것에 의한 것이다.
10.13.2 기계적 측정오차 (Mechanical Runout)
10.13.2.1 非同心의 表面/휨 (Nonconcentric Surfaces/Bows)
불량 가공된 (계란 모양 또는 비동심)축의 표면은 회전체의 회전속도와 일치하는 주파수를 가지는 정현 모양의 동적 운동을 지시하게 된다. 이와 동일한 모양의 동적 운동 조건을 생기게 하는 회전체에서의 또 다른 조건은 회전체가 물리적으로 휘었을 때이다.
표면이 불량 가공된 근원은 보통 최종 기계 가공시나 Grinding시 중고품 기계에서 마멸되었거나 결함 있는 베어링에서 또는 마멸된 선반의 중심을 가지는 선반에서 비롯된다. 회전체의 휨은 제작 과정 중에 로터의 취급 불량으로 통상 발생한다. 이것은 갑작스런 또는 부조화한 힘이 가해진 결과이거나 불량한 지지대를 가진 상태로 로터를 장기간 저장하므로써 발생된다. 부적절하게 지지된 로터는 중력에 의해 영구 처짐 즉, 휘게 된다.
어느 경우든 Runout 상태를 확인하는 가장 간단한 방법은 Proximity Probe 측정 면에서 Runout 모양을 관찰하기 위해 정밀한 Dial Gage를 사용하는 것이다. Dial Gage는 Proximity Probe로 관찰한 바와 같은 기계적인 Runout 유무를 확인하게 된다.
그 근원이 휜 로터에 의한 것인지 단지 비동심의 표면인지를 확인하기 위해서는 추가 점검이 요구된다.
비동심 로터인 경우 로터를 재가공하여 허용 동심도값 이내에 들도록 해야 한다. Rotor가 휜 경우는 기계적, 열적 또는 양자의 복합적인 방법으로 교정 절차에 따라 펴야 한다.
10.13.2.2 表面의 不規則 또는 缺陷 (Surface Irregularities or Imperfections)
표면이 불규칙하거나 결함이 있으면 Proximity Transducer로 관찰한 바와 같은 Runout 상태가 된다. 여기서 언급한 결함이란 Scratch, Dent, Burr 등의 형태를 말한다. 이런 결함은 분명한 기계적 Runout의 문제가 되지만 변형을 주지 않는 충격은 그 부위를 경화시킬 수 있으며 전기적 Runout의 원인이 된다.
Oscilloscope 상에서 이런 형태의 Runout을 보면 파형 위에 다소 높은 주파수의 Voltage Spike가 중첩된 정현 형태의 동적 운동파형이 나타난다. Voltage Spike의 극성은 축 표면의 결함 특성에 따라 (+) 또는 (-)가 된다.
일반적으로 표면의 불규칙은 Rotor 제작 과정중 취급 부주의에 의해 생긴다. 동적 운동을 측정하는데 사용되는 축 표면은 잘 보호되어야 한다. 또한 로터 저장을 위한 지지대는 표면의 Scratch, Dent 등이 발생하지 않도록 조심해야 한다. 때때로 축 표면의 불규칙은 기계 절삭공구에 의해서도 생긴다. 만일 공구가 무디거나 절삭 속도가 너무 빠르면 공구의 떨림이 생겨 축 표면에 작은 물결 무늬가 생길 수 있다.
교정조치로는 축 표면을 재가공하여 진원으로 만들어야 한다. 만일 표면의 불규칙이 대단히 미미하면 Oil을 적신 Emery Cloth로 표면을 재연마하면 표면의 불규칙을 제거할 수 있다.
10.13.3 전기적 측정오차 (Electrical Runout)
10.13.3.1 殘留 磁氣 (Residual Magnetism)
일반적으로 Proximity Transducer는 자계가 균일하거나 대칭적이면, 자장이 있는 곳에서도 만족스럽게 동작한다. 축 표면의 특정 부위에서 자장이 크고, 잔여 표면에서는 자장이 없거나 아주 작으면 전기적 Runout 상태에 있게 된다. 이것은 Proximity Transducer로부터 가해진 자장으로 인해 축 표면에 미치는 감도가 변화하기 때문이다.
Oscilloscope 상에서 이러한 Runout 상태를 관찰해 보면 정현적인 운동이 나타난다. 그러나 정현파는 찌그러지고 4각 파형이 되려고 한다. 잔류자기에 대한 최종점검은 소형 휴대용 자기 강도계측기를 사용하면 된다. 축 표면 위에 이러한 계기를 고정하고 로터를 손으로 돌리면 자장의 변화 유무를 확인할 수 있다.
잔류자기로 인한 Runout 문제가 발생하는 경우는 드물다. 그러나 제작 과정중에 적용된 여러 가지 물리적인 검사 기술로 인하여 잔류자기 문제를 일으킬 수 있다. 잔류자기가 생성 될 수 있는 가장 일반적인 검사 기술은 Casting, 또는 용접부 또는 다른 제작 과정 이후에 균열을 점검하기 위한 자분탐상 검사이다. 이러한 검사를 하는 중에 로터에 유기된 자장은 검사 과정이 완료된 후에 중성화되어야 한다. 이렇게 하기 위해서는 극성을 바꾸고 검사시 사용되었던 바와 같은 크기의 전압 전류를 통과시켜야 한다. 이 절차로 로터의 자기특성을 중성화시켜야 한다. 어떤 경우에는 극성의 반전이 이루어지지 않는다. 즉, 잔류자기가 남는다.
교정 조치로는 잔류자기 시험을 하여 전기적 Runout을 생기게 할만큼 충분한 크기가 있음이 발견되면 로터를 탈자시킨다.
10.13.3.2 金屬의 偏析 (Metallurgical Segregation)
전형적으로 축 재질로써의 합금강은 여러 가지 합금재료를 포함하고 있다. 일반적으로 이들 합금의 최종적인 금속학적 성분은 균질의 혼합물이다. 어떤 회전체에서는 합금강의 미시적인 편석이 일어 날수 있다. Proximity Transducer는 특정 금속에 따라 다른 전압 출력으로 응답하기 때문에 축의 원주 주위에 균질의 금속학적 성분이 결여되면 전기적인 출력이 변화하게 된다.
이런 모양의 Runout을 Oscilloscope에서 관찰하면 전형적으로 높은 전압과 파형상에 고주파수 Spike가 중첩된 다소의 정현파형을 나타낸다.
교정조치로써는 금속학적 근원으로부터 Runout을 제거할 수 있는 몇 가지 표면 처리 기술이 있다. 이에 관해서는 다음 항목에서 언급할 것이다.
10.13.3.3 殘留 應力 集中 (Residual Stress Concentrations)
통상적인 Rotor 제작 과정중에 다양한 기계가공 및 표면 처리로 인해 소량의 국부적인 응력 집중이 생길 수 있다. 응력부위가 Rotor의 기계적 특성에 나쁜 영향을 미치지는 않지만 Proximity Transducer로부터 전기적인 Runout을 일으킬 수 있다. Transducer로부터 전압 출력에 영향을 끼치는 변수 중의 하나는 관찰한 축 표면의 저항성이기 때문에 축 원주 주위의 저항의 어떠한 편차도 전압 변화를 생기게 할 수 있다.
Oscilloscope상에서 이러한 Runout 형태를 살펴보면 파형상에 고주파수 Spike가 중첩되고 높은 전압을 가지는 정현파형을 불수 있다.
교정조치로써는 이런 근원으로부터 생기는 Runout을 제거할 수 있는 몇 가지 표면처리 기술이 있다. 이에 관해서는 다음 항목에서 언급할 것이다.
10.13.3.4 鍛造한 軸 (Forged Shafts)
단조한 축은 잠재적인 전기적 Runout 문제를 나타낼 수 있다. 또 원자재의 질과 단조과정도 중요하다. 열간 단조의 취급도 Glitch 성능에 영향을 미칠 수 있다. Probe 부위의 뜨거운 축을 들어올리는 관례는 부분적으로 축을 급냉 시킴으로써 Glitch를 생기게 할 수 있다. 2중 Tempering한(증기터빈에서 사용된 바와 같은) 단조한 축은 Glitch가 생길 가능성이 더욱 낮다. 이것은 아마도 강의 보다 균일한 Tempering 때문일 것이다. 축은 야금학적 균일성을 확실히 하는 “초음파 검사”와 같은 규정이나 시험 절차는 Glitch 성능을 개선하게 할 것이다.
축의 균일한 열처리는 Glitch를 개선할 수 있으나 비균일한 열처리는 Glitch를 야기 시킬 수 있다. Glitch를 최소화하기 위해서는 Tempering이 균일하게 되어야 한다. 이러한 관점에서 열처리하는 동안 축을 회전하면 도움이 된다. 어떤 경우에는 경화기술이 Glitch를 야기 시킨다.
10.13.3.5 精削 節次 (Finishing Procedures)
축 반경의 최종 10 mils(250 ㎛)에 대한 정삭절차는 전기적 Runout에 큰 영향을 미칠 수 있다. 황삭가공후 동심도 확보를 위한 습식 연마는 어려움이 거의 없을 것으로 생각된다. 특히 최종 5 mils(125 ㎛)를 정삭하는 동안은 Hotspot이나 Chattering이 생기지 않도록 정삭 이송거리와 냉각 속도가 충분히 제어되는가를 확인한다. 이 가공 절차가 완료되면 25~35 microinch 정삭가공 상태가 된다. 이 단계에서 몇 가지 최종 정삭가공 절차중 하나가 사용되는데 이중에는 “Micro” 또는 “Super” Grinding, Honing 또는 Burnishing 등이 있다. Microgrinding은 Glitch를 유발시킨다. Honing은 일반적으로 보다 좋은 방법이다. Burnishing 특히 Diamond Burnishing은 모든 경우에 있어 실질적으로 기존의 Glitch를 감소시킨다. 기계 가공후 탈자 시키는 것은 Glitch를 감소시키는 방법으로 알려져 왔으며 일반적으로 Grinding 이후는 이것이 필요하다.
10.13.4 측정오차 측정 절차 (Measurement Procedure of Glitch)
① 축 Probe 부위에 잔류 자기가 있는가 점검한다. 2.5 gauss 이상이면 5,000 Ampere Turns 이하의 Coil을 사용하여 탈자 시켜야 한다.
② 베어링 저널부에 Vee Block이나 Roller 사이에 축을 설치한다. 축 양쪽에 Stopper(또는 Dial Gauge)를 설치하여 축 방향 이동을 방지한다.
③ 측정한 부위가 Probe에 의해 실제로 감시되는가를 확인하기 위하여 도면이나 베어링 하우징으로부터 Probe 위치를 정한다.
④ Probe 중심선으로부터 약 0.5 inch 떨어져 Probe 부위의 원주로 띠를 띄운다. 축 직경이 4.5 inch 이하인 경우는 띠에 10˚ 간격으로 표시를 하고 축 직경이 4.5 inch 이상인 경우는 5˚ 간격으로 표시를 한다. 띠에 영점은 Thrust Collar Keyway와 나란하도록 한다.
⑤ 축을 돌려 영점이 Test Probe 위치와 나란하도록 하고, 3 ft의 긴 끈의 한쪽 끝을 축의 하부에 접착 Tape로 붙여 고정시킨다. 이 끈은 측정하는 동안에 연속되는 회전으로 축에 감기게 되며, 끈을 풀기 위해 역회전하면 초기 시작점을 알 수 있게 된다. 이 간단한 절차가 Roller 내에서의 실수를 제한하게 된다.
⑥ Dial Gauge를 사용하여 기계적 Runout을 2회 측정한다. 측정은 Probe 중심선 양쪽의 ¼ inch(½ inch 떨어짐)에서 취한다. 36(또는 72)의 각 측정점에서 값을 계측기 눈금으로 읽을 수 있는 한 정밀하게 기록한다. 각 위치에서 2회의 값의 평균을 계산하고, 이들 2개의 평균값중 가장 큰 차이를 가지는 것을 구한다.
⑦ 이 최대 차이가 기계적 Runout이며 0.2 mils 또는 최대 허용진동의 25%중 큰 것으로 제한하고 있다.
⑧ Proximity Probe를 Probe 부위로부터 약 50 mils 떨어지게 설치한다. Proximitor로부터 RF(Radio Frequency) 신호를 Probe에 보내고, 송신전압을 Digital Voltmeter에 보낸다. 축을 회전시켜 Probe Tip과 영점위치와 나란히 정열 시키고, Voltmeter의 값이 약 7.5 Volt가 되도록 Gap을 조정한다. 축을 돌려 각 위치에서 소수점 2자리 수까지 그 값을 기록한다. 원래 영점으로 축을 되돌려 영점 조정을 다시 한다. 각 위치에서의 평균전압에서 영점에서의 평균전압을 제하여 그 값 앞에 (+), (-)기호를 기입한다. Volt 단위의 Glitch Runout은 이들 2개의 값들중 최대 차이를 가지는 것으로 하며 이의 인수 한계치는 0.04 Volt 이다.
⑨ Probe의 교정은 200 mV=1 mil 이기 때문에 전압 차이에 5배하면 Glitch 값(mil)이된다. 이 Glitch Runout의 인수 한계치는 0.2 mils 이다.
⑩ 전기적 Runout은 Glitch Runout (단위 mils)으로부터 각 위치에서 기계적 Runout을 제한 것이다. 이들 두 값을 기록하는데 사용되는 부호규약에 따라
전기적 Runout = Glitch – 기계적 Runout
⑪ Glitch Runout이 인수 한계치를 초과하면 Probe부위를 Micropeening 또는 Electro Plating으로 처리해야 한다. 처리후에 기계적 및 Glitch Runout 값을 이상의 ⑥~⑨항을 반복하여 기록한다.⑫ 최종 기록을 수집한 후에는 Probe 부위를 부식 및 기계적 손상으로부터 보호해야 한다.
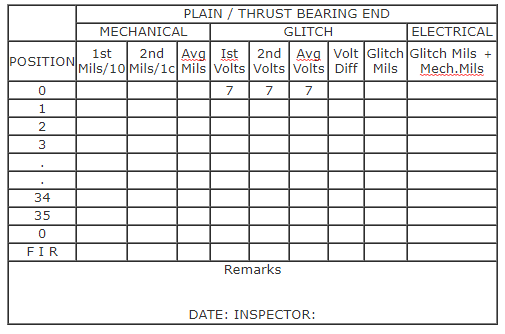
기계적 및 전기적 Runout 검사 보고서
주)
① Thrust Key 위치인 영점으로부터 10˚ 마다 값을 취한다.
② 기계적 Runout의 첫째 및 둘째란은 mil/10 단위로 기록한다. 측정은 Probe 중심선에서 양쪽으로 약 0.2 inch 떨어져 시행한다.
③ 기계적 Runout의 (+)는 축이 Probe쪽으로 움직이는 것을 의미한다.
④ Glitch의 (+)는 축이 Probe로부터 멀어지는 것을 의미한다.
⑤ 전기적, 기계적 Runout의 조합 영향이 Glitch이다. 이것은 5배의 전압차이며 단위는 mil이다(1 mil=200 mV).
⑥ 전기적 Runout은 기계적 및 Glitch Runout의 합으로 계산된다. 이것은 3, 4항에서 사용된 부호규약 때문에 의한 것이다.
⑦ (-)값을 가감할 때 수학적인 규약을 지키는 것에 주의를 기울여야 한다.
⑧ Glitch 전압차는 각 위치에서 마다 영점에서의 전압을 제하면 된다.
⑨ FIR는 각 란에서의 두 값간의 최대 차이다.
10.13.5 측정오차 취급법 (Methods of Dealing With Glitch)
Glitch를 제거하기 위한 전자적인 신호 처리를 전자적 Runout 보상 또는 Runout 공제라고 한다. 그것은 축이 Slow Roll Speed로 회전하는 상태에서 1회전마다 한 번의 Keyphasor Timing Pulse를 기준한 Glitch 형태를 전자적으로 기억하는 것을 포함하고 있다. 이 신호는 보다 높은 속도에서 변환되고 혼합(진동에 Glitch가 추가)신호에 추가된다. 이 절차로써 그 속도에서 전체 신호로부터 Glitch 신호를 유효하게 공제하여 실제 진동만을 나타내는 신호를 가지게 된다.
전자적 Runout 보상은 얼른 봐서는 Glitch에 대하여서는 만병통치약처럼 보인다. 그러나 이 기술의 효과를 완전히 이해하기 위하여 몇 가지 잠재적인 문제점들을 고려해야 한다.
일반적으로 전자적인 Runout 보상을 할 때 만일 (a) Glitch 모양이 Slow Roll로부터 더 높은 속도에 이르기까지 변화하거나 (b) Slow Roll 모양이 완전히 실제 Glitch(예를 들면 일시적인 Rotor Bow, 저속 진동)에 기인하지 않는다면 두 가지 잘못을 초래한다. ① 그 속도에서 실제 Glitch 신호 성분은 더 이상 보상되지 않으며 또, ② 보상회로는 실제 진동 신호 일부를 공제하게 된다.
이들 잘못은 실제 진동 크기 보다 더 높거나 더 낮은 진동진폭을 나타나게 할 수 있다. 기타 잠재적인 문제점들에는 다음과 같은 것들이 있다.
① 일시적 축의 휨
열적 또는 중력적인 휨으로 인한 신호를 Glitch로 잘못 판단하기 쉽다. 이들 일시적인 휨은 Glitch와는 분명히 다른 현상이다. 일시적인 휨을 Glitch로 잘못 알고 전체 신호로부터 공제하면 측정의 오류를 가져온다. 이들 휨은 Rotor 거동에 영향을 끼쳐 진동 신호로 나타난다. 또한 기동시나 부하 변화시와 같이 일시적인 휨상태가 변화할 때 만일 원래의 휨량이 공제되었다면 잘못된 결과를 초래하게 된다. Rubbing에 의한 어떤 형태의 열적인 휨은 또한 위상의 변화를 가져올 수 있다. 이것도 공제된 틀린 Glitch 신호의 원인이 된다.
② 축방향 위치 변화
Probe에 관하여 축의 축방향 위치가 크게 변화하면 Probe는 축의 새로운 부위를 관찰하게 된다. 새로운 Runout 신호가 기억된 원래 신호와 다르면 심각한 오류를 범하게 된다. 축의 열팽창에 의한 축방향 위치 변화는 0.25~25 ㎜ 변할 수 있다.
③ 축의 변화
예비 로터를 설치할 때 새로운 Glitch 모양을 기억해야 한다. Runout 기억으로 이전의 모양을 보유하고 있으면 틀림없이 큰 오류를 초래하게 된다.
④ 결선 잘못
진동 변환기의 결선이 잘못되면(예를 들면 수직 및 수평 신호의 바뀜) 틀린 Glitch 신호가 두 개의 변환기로부터 공제된다. 이로 인하여 큰 오류를 범하게 된다. 다른 속도로 회전하는 기계열에서 부적합한 Keyphasor 신호를 사용하여도 오류를 범하게 된다.
⑤ 시간에 따른 Glitch 모양의 변화
특히 자기적으로 유도된 어떤 형태의 Glitch는 시간에 따라 변한다. 전도성 변화에 의한 Glitch는 Proximity Probe Gap 거리의 함수에 따라 변화한다. 이들 변화는 보상된 신호의 오류를 가져온다.
⑥ 기준 각도의 변화
커플링 분리시 기준 각도 표시를 잊어버리면 공제된 신호의 위상각은 틀리게 된다. BNC 회사의 Digital Runout Compensator에서는 축 1회전을 256개 Segment로 나누어 각 Segment는 1.4˚씩이다.
⑦ 과도적인 속도 상황
로터의 회전수가 급속히 변화하면(예를 들면 전기 전동기의 기동중) Compensator의 Tracking(Slew) Rate가 초과되지 않는가를 확인해야 한다. Time Expansion Technique (예를 들면 다속 Tape Recorder의 사용)은 보상의 오류를 피하기 위해 필요하다.
⑧ 계측기 신뢰도
전기적 Runout 보상은 신호 통로에 전기회로를 추가한다. 이 전기회로의 고장은 그 Transducer로부터 보상된 신호의 손실이나 찌그러짐의 원인이 되고, 또한 Keyphasor 신호 손실은 이것과 연결된 모든 Channel이 찌그러지거나 기능이 저하된다(Runout을 보상하는 각 Channel은 연속적으로 작용하는 Keyphasor가 필요하다). Wobulator로 Monitor 교정을 하기 위해서는 “Black Box” Runout 보상기가 교정신호에 무슨 역할을 하는지에 대한 지식이 필요하다. 신뢰도 문제가 가장 중요한 이유는 전기적 Runout 보상이 기계 진단용으로는 바람직하지만 연속 감시용으로는 추천되지 않기 때문이다.
⑨ 운전원의 신뢰도
어떤 계측기에 대한 운전원의 신뢰는 그 계측기 기능에 대한 지식이나 시범에 달려 있다. 신호 통로에 “Black Box”가 많을수록 이해와 믿음은 더욱 어렵다. 이상의 조건들중 어떠한 것도 오지시하거나 불필요한 Monitor 경보가 발생하면 그 계측기에 대한 운전원의 신뢰도는 영향을 받을 것이다.
10.13.6 벡터의 무료화 대 측정오차 보상 (Vector Nulling VS. Runout Compensation)
회전체 상에 나타난 Runout 즉, “Glitch” 값을 제거하는데 이용하는 3가지 기술이 있다. 가장 기본적인 방법은 기계적 또는 전기적 Runout의 근원을 제거하기 위하여 축의 표면을 처리하는 것이다. 다른 2가지 방법은 축상의 Runout 값을 보상하는 전기적 회로를 채용하는 것이다. 분명히 Runout 근원을 제거하기 위한 축의 처리 방법이 가장 바람직하다. 왜냐하면 이 방법이 행해지면 진동 신호에서 Runout을 보상해야 할 아무런 이유가 없기 때문이다.
때로는 어떤 축재질 또는 단조품은 표준 축의 처리에 잘 응답하지 않는데 이는 축이 영구적인 휜 상태이거나 축 표면 처리가 불가능하거나 비현실적인 경우이다. 축의 표면 처리나 축의 휜 상태를 제거하는 것이 비현실적이라면 2가지 전기적 방법중 하나를 사용한다. 그러나 이 2가지 방법은 사용한 전기회로 측면에서 또 처리된 진동신호의 응용 측면에서 완전히 다르다. 다음은 2가지 방법에 대한 설명과 각각의 정상적인 응용에 관한 설명이다.
10.13.6.1 벡터 無効化 (Vector Nulling) … Digital Vector Filter
이 시스템은 Digital Vector Filter의 필수적인 부분이다. 이것은 Slow-Roll Vector 즉, 각기의 공진상태 이후 잔류 불평형으로부터 초래되는 Vector를 무효화하는 수단이 있다. 무효화 작업은 실제 Vector의 공제(위상과 진폭)이지 단순히 전압 억제 회로가 아니다. 무효화 회로는 Filtered 진동 파형에서 작용한다. DVF2에 채용된 Filter는 Rotor의 회전 주파수(1×RPM)로 조정되었기 때문에 무효화 회로는 회전 주파수와 일치하는 Shaft Runout 부위를 제거한다. 이것은 전형적으로 Probe로 측정하는 면에서 축의 휨이나 비동심(겨란 모양을 한) 축의 상태를 제거하는데 사용한다. 아주 큰 Runout(Scratch, 야금의 불규칙 등)도 DVF2의 Filter 작용을 통하여 제거된다.
무효화 될 수 있는 신호의 전체량은 DVF2상에 진동 범위가 어떻게 선정되었느냐에 달려 있다. 2가지 범위가 사용되는데 1~5 mils 그리고 1~50 mils 이다. 무효화 작업은 각 범위에 대하여 Full Scale의 20%로 제한된다. 따라서 최대 무효 신호는 낮은 범위에서는 1 mils 높은 범위에서는 10 mils 이다.
일단 초기 Slow-Roll Vector가 무효화되면 이것은 다음에 오는 모든 동적 신호로부터 자동적으로 공제된다. 이 시스템은 운전속도 범위에 걸쳐서 시스템의 기계적 응답과 Impedance, 공진(임계속도) 및 증폭계수를 정확히 실행하는 수단을 제공한다. 또한 Vector의 무효화는 공진 이후에 잔류 불평형 벡터를 보상하기도 한다.
10.13.6.2 Runout 補償 (Runout Compensation)…Digital Runout Compensator
Digital Runout 보상기는 Slow-Roll 동적 파형을 디지털로 기억하는 능력을 가지고 있다. 이 계측기는 128 Line, 9-bit, Digital Processing System이다. 초기 Slow-Roll 파형이 일단 기억되면 이것은 다음에 오는 모든 동적 파형으로부터 공제된다. Filter를 사용하지 않거나 파형의 사전 조정 작업은 기억기능 이전에 행해지기 때문에 Digital Runout Compensator는 복잡한 형태의 동적 운동 신호를 생산한다. 이 운전으로 전체 동적 신호를 관찰하게 된다.
10.13.6.3 綜合
2가지 보상 방법중 하나를 선정함에 있어 출력 신호의 최종 응용이 주 고려 대상이어야 한다. 어떤 형태의 Runout 보상기를 사용하는가에 대한 생각은 하나의 “중요한 규칙”을 고수할 것을 요한다. 「Slow-Roll 속도에서 측정한 Runout 형상이나 Vector는 시간, 축의 속도, 로터의 축 방향 위치, 온도(팽창차) 또는 기계의 운전조건들의 함수로 변화시켜서는 안된다.」
대형 기계에서는 운전속도까지 공칭상의 축방향 위치 변화와 차동팽창이 발생하면 진동 Probe가 “새로운” 축의 축방향 위치를 관찰하도록 하고 있다. 총 Runout 형태를 고려할 때 이 “새로운”축의 위치는 Slow-Roll에서 관찰한 총 형태와는 전혀 다르다. Slow-Roll에서 Program되어야 하는 Digital Runout 보상 회로는 축방향 변화는 발생하지 않는다는 것을 가정한다.
그러나 Vector 무효화는 시스템내의 Filter는 오직 1×Runout Vector만 고려되기 때문에 총 Runout 형태는 다루지 않는다. 1회전에 1회의 Runout Vector는 Slow-Roll로부터 운전속도 및 온도까지 거의 변화하지 않는다. 이런 관점에서 Vector 무효화는 Digital Runout 보상에 분명한 장점을 준다. Vector 무효화는 또한 Bode Plot이 작성될 때 다음 고차의 공진 작용을 관찰하기 위하여 공진속도역을 통과한 후 축 운동의 잔류 Vector를 무효화하는 능력도 제공한다.
따라서 Runout 보상 방법을 선정할 때 훌륭한 기술적 판단이 이용되어야 한다. 정상적인 기계의 운전 특성 및 출력 진동 신호의 의도적인 사용에 의한 잠재적인 오류의 근원에 주의를 기울여야 한다.
10.13.7 측정오차 감소 (Glitch Reduction)
Glitch를 감소시키는 방법은 여러 가지가 있고 성공적으로 수행되어 왔다. 각 방법이 소기의 결과를 얻을 수 있기 때문에 어느 방법이 최선이라고 할 수는 없다. 그러나 비용 및 시간을 기준으로 할 때 어느 방법을 선택할 것인가는 말할 수 있다.
① 추가 기계가공
Glitch 측정을 위해 Probe 부위를 점검한 결과 가용 한계치를 초과하면 Probe 부위를 진원 가공할 수 있지만 이것은 더욱 수용 불가의 결과를 초래 할 수 있는 잘못된 방법이다.
② Polishing 또는 Stoning
①항과 유사한 방법이지만 아주 무지스럽지는 않다. 그러나 사태를 더욱 악화시킬 문제점은 계속 안고 있다.
③ Sleeving
축에 슬리브를 강제압입 방법이 사용되어 왔지만 이것은 앞의 ①, ②항과 같이 예견할 수 없는 결과를 초래하는 비용이 많이 드는 방법이다. 이들 2항보다 더 많은 처리가 요구된다.
④ Rolling 또는 Burnishing
이 방법은 Glitch를 허용 한계치 이내로 감소시키는 높은 성공률을 가진다. Probe 부위를 경화시킨 Roller 사이에서 10시간 이상 부하를 준 상태로 Rolling한다. 실제로는 이 절차는 추가적인 처리가 필요 없는 균일한 경화표면을 갖게 된다. 이 방법은 가장 쉽고 기능도 크게 요구되지 않으나 Probe 부위마다 10시간 이상의 시간이 소요된다.
⑤ Micropeening
표면재료가 경화된다는 점에서는 ④와 유사하다. 그러나 표면경화는 그 정도가 경미하고 재료의 변화를 많이 일으키지 않는다. 따라서 Probe 출력전압의 증가가 요구되는 Probe 주위 위치에서 선별적으로 수행된다. 조작을 잘하고 측정치들이 일정하면 Glitch를 허용 한계치 이내로 줄일 수 있다. 이 작업은 시간이 소요되고 오류를 범하기 쉽지만 경험 있는 조작자는 일관된 좋은 결과를 얻을 수 있다.
Micropeening의 절차는 다음과 같다.
(a) 13.4 항에서 상술한 바와 같이 Glitch 전압치를 Micropeening Worksheet상에 기입한다. 각 위치에서의 전압으로부터 최고 전압을 제한 전압차를 구하고, 이것은 (-)량이 된다.
(b) Micropeening 계기를 최소 Stroke로 설정하고 최대 전압차를 가지는 위치와 나란히 축 방향으로 1″길이를 한 줄로 Peening한다. 이 위치에서 전압치 변화량이 첫 번째 값에 비하여 (+)0.04 Volt 인가를 점검한다(이 전압 변화량은 조작자와 Peening 계기에 따라 다르다. 만일 0.04와 다르면 0.04 대신에 다음 설명에서 얻어진 값을 쓴다).
(c) 전압 차가 0.06 이상인 다른 모든 위치에 Peening한다.
(d) 다른 일련의 Glitch 전압을 기록하고 그 차를 계산한다.
(e) 전압 차가 0.04 이상인 모든 다른 위치에 Peening한다.
(f) 기록을 반복하고 최대 차가 0.04 이하일 때까지 Peening한다.
(g) 13.4 항의 8~9번에서 설명한 바와 같이 최종값들을 기록한다.
⑥ Electroplating
Micropeening 기술의 실험 결과에 의하면 선택된 위치에서 Probe 출력전압을 감소시키는 방법은(Micropeening과는 반대 효과) 가장 이점이 큰 것으로 판명되었다. 선택적인 Electroplating 방법은 바람직한 효과를 가지고 있다는 것이 확인되었다. 따라서 소기의 출력전압을 주도록 Probe 주변의 선택한 위치에 금속의 Flash Coat를 적용할 수 있다. 또한 이 절차는 조작자의 높은 숙련도와 많은 시간의 소요가 요구된다.
⑦ Micropeening과 Electroplating의 조합
방법 ⑤와 ⑥을 조합하는 방법은 각기 나름대로의 방법보다는 보다 신속하다. 평균 Glitch 전압을 선정하여 평균보다 큰 전압을 가지는 곳에는 Electroplating을, 반면에 평균보다 낮은 전압을 가지는 곳에는 Micropeening을 시행한다. 허용되는 결과를 얻기 위해서는 극소 위치만을 Plating이나 Peening해야 한다.
이 조합 방법은 또한 요구되는 바와 같이 Peening 위에 Plating을 하거나 Plating 위에 Peening을 함으로써 조작자의 실수도 허용된다.
조합 방법의 절차는 다음과 같다.
(a) 13.4 항에서 상술한 바와 같이 Glitch 전압치를 Micropeening Worksheet상에 기입한다. 모든 전압이 0.02 이내에 오도록 계산 또는 어림하여 평균전압을 정한다.
(b) 평균전압이 0.02를 초과하는 모든 위치에는 Plating을 해야 한다. 공급된 액체로 이 부위를 청소 및 Etching하고, 접착 Tape으로 Probe 부위를 바르되 선정한 표시와 나란히 축 방향으로 길이 1 inch 폭 1/8 inch 만큼의 부위는 노출시킨다.
(c) 최고 전압 위치를 선정하고, 10~18 Volt, 0.5~0.9 Amp로 10초 동안 Nickel Alkaline 수용액으로 이 곳을 Plating한다. 경험상 이것은 그 부위에서 0.1 Volt만큼 Glitch 전압을 감소시켜야 한다. 실제 전압 변화를 점검하고 Plating Time(예를 들면 0.01 Volt 변화에 1초)을 조정한다.
(d) 이 Timing을 이용하여 다른 모든 선정한 부위를 Plating한다.
(e) Glitch 전압을 다시 취하고 소기의 평균전압을 얻도록 필요에 따라 다시 Plating한다.
(f) Masking Tape을 제거한다.
(g) 앞의 ⑤항에서 상술한 바와 같이 Micropeening을 한다.
* 과도하게 Peening된 부위는 Plating으로 소기의 전압이 회복될 수 있다.
* 과도하게 Plating된 부위는 Peening이나 Emery Cloth로 가볍게 문질러 소기의 전압이 회복될 수 있다.
⑧ Degaussing
균열 부위의 자분탐상을 하거나 자장내에서 작동하므로써 생긴 축의 잔류 자기는 상당히 큰 전기적 Runout을 일으킬 수 있다. 따라서 Glitch 제거를 하기 전에 모든 축의 Probe 부위의 잔류자기를 측정하는 것이 중요하다. Bently Nevada에서는 자장의 강도가 5Gauss인 잔류자기는 0.5 mil정도의 전기적 Runout을 준다고 말하고 있다. 따라서 2.5Gauss를 초과하는 잔류자기를 나타내는 모든 축은 탈자시켜야 한다. 이것은 Glitch를 완전히 제거하는 과정은 아니지만 운전 중에 잔류자기를 잃는 축 때문에 Glitch 값이 변하지 않는가를 확인하는데 도움이 된다.
10.13.8 비접촉 변위센서 측정 부위의 보호 (Protection of Probe Areas)
앞서 언급한 조치중 하나나 또는 조합으로 Glitch를 제거하는 것은 진동 관리하는데 중요하다. Probe 부위를 처리할 때 부식손상 및 긁힘이 생기지 않도록 보호하는 것이 중요하다.
인수시험과 현장 운전하는 사이에는 많은 주위를 기울이지 않을 수도 있다. 이 경우에 녹, 긁힘 또는 눌린 자국에 의해 Probe 부위가 손상되었다는 현장 보고서가 많다. Stoning이나 Polishing으로 손상을 제거하면 소기의 외형은 가질 수 있으나 원래의 Glitch 값은 완전히 바뀔 것이며 틀림없이 허용 한계치를 초과할 것이다. 그리고 Glitch 제거는 선택적인 Micropeening으로 현장에서 수행해야 하며 불리한 조건을 감안하면 그 결과는 공장에서 얻을 수 있는 값보다 항상 못하다. 따라서 공장에서 Glitch 처리를 하고 그 값을 취한 후에는 Probe 부위를 Epoxy Resin으로 Coating을 고려해야 한다. 이 Coating은 기계 수명 동안 남아 있으며 Probe 값에 영향을 주지 않을 뿐더러 부식 및 모든 미미한 기계적 손상으로부터도 Probe 부위를 보호한다.
10.13.9 결언 (Conclusions)
① Proximity Probe는 기계 진동 감시를 위한 공업 표준 설비로 받아 들여 왔다. 불행히도 이들은 반경방향의 참 진동과 회전체에 내재된 Glitch를 구별 할 수 없다.
② 따라서 Glitch를 제거하거나 허용 한계치 이내로 감소시키는 것이 관심사이다.
③ 축의 잔류자기에 의한 Glitch는 다른 조치를 취하기전에 제거되어야 한다.
④ 기계적 Runout이 허용치 이내에 있으면 이것이 Glitch에 미치는 영향은 전기적 Runout을 변화시킴으로써 극복 될 수 있다.
⑤ 전기적 Runout은 Burnishing(Rolling) 또는 Micropeening으로 Probe 부위를 경화시켜 Glitch를 허용치 이내로 오도록 유효하게 변경될 수 있다.
⑥ 이곳에서 Burnishing 작업이 시도된 바는 없으나 결과치가 일정하고 더 이상의 조치가 필요하지 않으면 Burnishing 작업이 아주 경제적이다.
⑦ Burnishing이 증명되고 적용될 때까지는 Micropeening이나 Micropeening과 Electroplating의 조합방법을 공장 및 현장용으로 이용해야 한다.
⑧ Glitch 제거를 완료한 후에는 즉시 Epoxy Coating을 Probe 부위에 적용하도록 공장의 관례를 바꿔야 한다. 이렇게 하면 장기간 표면이 보호되고 최소의 Glitch 값이 유지된다.