Turbine Supervisory Instrumentation
2. 축 및 케이싱 진동 (Shaft and Casing Vibration)
3. 로터의 축방향 및 반경 방향 위치 (Rotor Position-Axial and Radial)
4. 편심과 편심 위치 (Eccentricity and Eccentricity Position)
5. 케이싱 팽창과 차동팽창 (Casing Expansion/Differential Expansion)
6. 캠(밸브) 위치 [Cam(Valve) Position]
9. 베어링 온도 감시 (Bearing Temperature Monitoring)
10. 비접촉 변환기의 활용 (Uses of Non-Contacting Transducers)
1. 측정항목 (What to Measure)
무엇을 측정할 것인가에 대한 결정은 어느 정도는 기계 자체에 달려 있다. 육중하고 견고한 케이싱(그림 4-1a)내에서 상당히 가벼운 회전체가 운전될 때 회전체에 의해 발생된 대부분의 힘은 축과 베어링 사이의 상대 운동으로 방산된다. 케이싱과 회전체의 무게의 비가 약 30:1인 고압 원심압축기와 같은 형식의 기계에 있어서는 비접촉 Probe로 측정된 축과 베어링 사이의 상대변위가 회전체 상태를 나타내는 최고의 척도이다.
정반대의 구성으로, 탄성 구조물(그림 4-1b) 상에서 지지되는 견고한 베어링 내에서 회전하는 육중한 회전체인 경우는 회전체에 의해 발생된 힘의 대부분은 구조적 운동으로 방산 된다. 이러한 기계류 (즉, Fan이나 가스터빈, 구름 베어링으로 조립된 기계류)에서는 가속도계로 측정된 Casing 진동측정이 가장 좋은 상태 측정 방법이다.
a. 축진동 측정시:
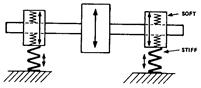
b. 케이싱 진동 측정시:
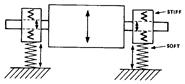
그림 4-1 기계의 구조와 베어링의 형식은 최적의 진동측정 형식을 결정한다.
최대의 효과를 위해서는 상태를 나타내는 측정은 기계 상태의 변화에 대한 응답에 따라 가장 큰 변화를 나타내야 한다. 예로써 추력 베어링에 대한 부하와 기계상태에 관련된 세 가지 측정대상 즉, 축방향 위치, 추력 베어링의 배유 온도 및 금속 온도를 조사해 보자. 이 세 가지 측정대상 중에서 베어링 금속 온도는 부하 변화에 대하여 가장 민감하다. 축방향 위치와 배유 온도는 무부하에서 전부하까지 각각 2~3 mils (50~75 ㎛)와 5 ℉(3 ℃)정도만 변화하는데 반해 베어링의 금속 온도는 100 ℉(55 ℃)의 증가를 보이는 것이 보통이다. 그러므로 고려 대상이 과부하만 이라면 금속 온도가 필요하고 또한 유일한 최상의 측정항목이다.
그러나 일반적으로 터보 기계류의 상태 측정은 이와 같이 단순하지 않고 또한 단 하나의 측정 위치에서 단 하나의 측정변수만으로 보호 계통이 보장되지 않는다. 추력 베어링의 상태 측정에 있어서 가장 좋고 보편적인 접근법은 축의 축방향 위치 변화를 감지하여 경보를 발생시키기 위한 축방향 위치 측정방법과 베어링이 받고 있는 부하를 나타내는 금속온도 측정방법을 조합하는 것이다. 정전하(Electrostatic Discharge)로 인한 Etching이나 윤활유 내의 불순물에 의한 Wiping과 같은 요인과 추력 베어링 문제의 원인이 될 수 있는 터빈 날개의 손상은 베어링 온도와 축방향 위치 측정을 조합하여 판명해야 할 것이다.
상태의 완전한 상황을 파악하기 위하여 감시되어야만 하는 주파수의 범위는 변환기와 측정할 최적 변수의 선택에 큰 영향을 가지고 있다. 어떤 경우에는 전 범위 적용을 위해 변환기들의 조합이 필요하다 (그림 3-1). 한 예로서 기어와 구름 베어링을 가진 기계의 효과적인 감시를 위해서는 회전 주파수의 80~100배에 이르는 넓은 주파수 범위에 걸친 감시를 필요로 한다. 이러한 형식의 적용에 있어, 진동 가속도계가 필요한 모든 정보를 제공해 주는데, 제지 기계나 소형 펌프, 공작 기계 등이 그 예이다. 고속 기어와 산업용 가스터빈과 같은 또 다른 적용에서 전통적인 관례는 고주파수 감시는 가속도계, 저주파수 감시는 축변위 검출기에 의존한다.
제 3장(진동 변환기)에서 기술한 바와 같이 설비운전 조건에 맞는 변환기나 진동 측정 방법을 선택하기 위해서는 기계 구조, 응답 특성, 측정 형식, 상태변화에 대한 응답 특성, 상대 측정이냐 절대 측정이냐, 관심 주파수 영역 등과 같은 기계 상태를 최적으로 나타내기 위한 많은 요소들이 고려되어야 한다.
증기터빈 발전기는 의심할 여지없이 가장 크고 고가이며, 로터 무게만도 150 Ton이 넘는 아주 중요한 회전기계이다. 물론 이 기계에서는 성능이나 임박한 문제점에 대한 경고를 반영하는 중요 인자들의 측정 및 감시가 절대적으로 필요한 것이다. 터빈 감시기구(Turbine Supervisory Instrumentation, TSI) 시스템은 중요 인자들의 측정 및 감시를 위하여 여러 가지 검출기와 기구를 사용하고 있으며, 다음 항부터는 이들 성능 매개변수들의 각각을 측정하는데 사용되는 기본 기구와 기술에 대하여 설명한다.
2. 축 및 케이싱 진동 (Shaft and Casing Vibration)
터빈 발전기 세트는 고압터빈, 중압터빈, 1~3개의 저압터빈, 발전기 및 여자기로 구성되어 있고 발전소에서 가장 중요한 회전기계이다. 이들 단위 기계의 축은 서로 커플링으로 연결되어 구동되고 있으며 이 축들은 각기 하나 또는 두개의 저널 베어링에 의해 지지되고 있다.
터빈 발전기 세트의 진동 상태감시를 위해서 1950년대 초까지는 속도 Pickup을 케이싱(베어링)에 설치하여 케이싱의 절대 진동만을 측정하였고, 1960년대 초에는 터빈 발전기 세트의 용량 증대와 복잡화함에 따라 감도가 증가된 동일한 진동 변환기를 사용한 Shaft-Rider가 개발되어 한 방향의 축진동을 측정할 수 있게 되었다.
오늘날에는 신형 대형 터빈 발전기 세트의 경우 각 베어링마다 서로 90°떨어진 2개의 비접촉식 X-Y Probe를 설치하여(그림 4-2) 베어링과 축간의 상대 축진동을 검출할 수 있다.
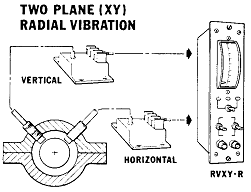
그림 4-2 전형적인 X-Y Probe
한편 X-Y 각각의 Probe로부터 발생한 정현파 진동 파형을 화면에서 보면(그림 4-3) 수평면(X-Probe)의 상대진동은 3 mils이고, 수직면(Y-Probe)의 상대진동은 2 mils임을 알 수 있다.
특히 탄성 지지대를 갖은 기계나 높은 케이싱 진동이 일어나기 쉬운 기계에서는 축의 절대 진동측정이 대단히 중요하다. 그림 4-4에서와 같이 지진계식 속도 변환기를 설치하여 케이싱의 절대 진동을 측정한 후 이 값에서 축의 상대진동을 벡터적으로 더하면 축의 절대진동이 구해진다. 이와 같이 축의 절대 및 상대 축진동을 동시에 측정할 수 있는 변환기를 Dual Probe라 한다.
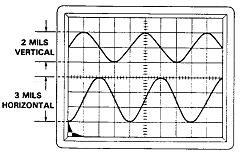
그림 4-3 X-Y 각 Probe에서의 상대 진동치
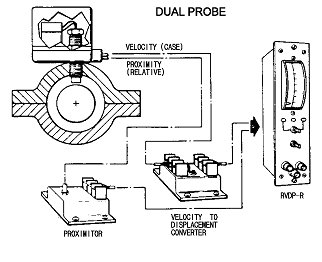
그림 4-4 축의 절대 및 상대진동을 동시에 측정할 수 있는 Dual Probe
축변위 감지기는 시스템의 이용을 용이하게 하기 위하여 각 베어링마다 같은 위치가 되도록 설치되어야 한다. 시간영역 상에서 정확한 Orbit을 얻기 위해서는 수평 Probe가 축회전 방향에 상관없이 구동측에서 보아 수직 중심선의 오른쪽에 위치해야 한다. 이러한 규칙은 오실로스코프나 진동 분석기상에서 X-Y Probe에 대응하는 축운동과 동일한 운동을 발생시킨다.
베어링과 케이싱의 수평 분할에 의한 간섭으로 종종 수평면에 변위 Probe를 설치하는 것이 불가능하기 때문에 API Standard 670은 수직 중심선의 45°상방향으로 각 Probe를 설치할 것을 요구한다. 이러한 구성에서도 축회전 방향과 관계없이 구동측에서 보아 오른쪽에 있는 Probe는 수평 Probe라하고 정확한 Orbit 회전 방향을 설정하기 위한 시간 영역 표시에서 X축이 되며 이때 Display되는 것은 실제의 축운동으로부터 45°기울어진다.
만일 변위 Probe를 이용하여 기계 상태를 나타내려면 변위 Probe 자체가 축상의 적절한 곳에 위치해야 한다. Probe가 진동이 없거나 극히 작은 부분인 Nodal Point나 또는 그 가까이 위치되지 않도록 하기 위해 측정점에서의 축의 휨 모드와 응답이 회전체 역학적 계산에 의해 평가되어야 한다.
Probe 위치가 Nodal Point로부터 멀어지면 회전체 축의 휜 정도는 일정한데도 불구하고 변위가 커진다. 추천된 진동 한계치를 유지하기 위해서는 기본적으로 베어링에 바로 인접하여 반경 방향 축변위 Probe를 설치해야 한다 (API 670은 반경 방향 Probe는 베어링으로부터 3 인치(75 ㎜)안에 설치되어야 하는 것을 요구한다). 그러나 추력 베어링과 같은 기계구성 요소로부터의 간섭으로 인해 이와 같은 위치에 설치하지 못하는 경우가 종종 있다. 이러한 경우에는 부득이하게 Probe를 축진폭이 훨씬 높아질 수 있는 위치인 베어링으로부터 멀리 떨어진 곳에 설치해야 한다. 하지만 이런 경우는 가능한 한 피해야 한다.
보통 반경방향 축변위 Probe는 Gap 전압이 선형 범위의 중간 정도에 있도록 조정된다. API 670은 반경 방향 Probe의 Gap 전압을 -10 VDC±.2 V로 추천하고 있다.
Probe에 의해 관찰되는 축표면은 베어링 저널과 동심이어야 하고 Scratch와 같은 어떤 기계적인 결함도 없어야 한다. API 670에 축의 표면 조도는 호닝이나 버니싱에 의해 16~32 마이크로 인치(0.4~0.8 ㎛ rms)로 명시되어 있다. 또한 API 670은 Probe와 마주보는 축표면은 기계적 및 전기적 총 Runout이 최대 허용 진폭의 25%, 즉 0.25 mils를 초과하지 않도록 탈자되어야 하는 것을 명시하고 있다. Probe면의 가우스(Gauss) 레벨은 1 가우스보다 더 적은 변화를 가지고 ±2 Gauss를 초과하지 않아야 한다.
Casing 진동을 측정하는데 있어서 중요한 주의 사항은 변환기의 설치가 견고해야 하고 감시해야 할 주파수 범위 안에 고유 진동수를 가지지 않도록 하는 것이다. 이완된 변환기나 기계 상태와 무관하고 설치대 자체의 공진으로 인한 잘못된 케이싱 진동측정이 많이 있었다.
기계의 케이싱에 직접 볼트로 고정 설치하는 방법이 선호된다. Faced and Tapped Head를 가지거나 Single-Point Block Mount를 가지는 볼트는 비싸지 않고 측정결과도 대단히 양호하다. 기계의 부착면이 평평하다면 전자석 고정 방법 또한 효과적이다. 일반적으로 외팔보식 고정 방법은 피해야 한다.
상태감시를 위해 사용되어지는 케이싱 진동 변환기는 가능한한 가장 견고한 베어링부에 부착되어야 한다. 여기서 다시 고유 진동수는 중요한 관심사이다. 케이싱 진동 변환기는 점검창이나 과도한 가진이 고유 진동수에서 일어날 수도 있는 가벼운 구조 부재 등에 설치되지 않아야 한다.
주의할 사항은 가진이 시험 주파수 범위밖에 있을지라도 큰 가진은 이 스펙트럼밖에 있는 신호를 찌그러뜨리도록 시스템에서 비선형성을 발생시킬 수 있다는 것이다. 그러므로 측정 시스템을 찌그러뜨리거나 혹사하는 일이 관심 주파수 안에서나 밖에 아무 것도 없는지 항상 확인하라.
임피던스가 큰 케이블은 독립된 변환 전자장치가 있는 가속도계로 케이싱을 측정할 때 어느 정도 움직이지 않아야 한다. 그렇지 않으면 케이블이 신호를 발생시켜 변환기로부터 얻어진 진동 신호에 더해진다. 일체의 전자장치를 가진 가속도계로부터의 케이블은 유도 잡음 운동에 다소 덜 민감하지만, 케이블의 운동으로 인해 가속도계 Case에 응력이 가해지지 않도록 케이블을 견고하게 묶어야 한다.
3. 로터 축방향 및 반경방향 위치 (Rotor Position-Axial and Radial)
3.1 軸方向 位置 (Axial Position)
축의 축방향 위치 감시의 목적은 축과 고정체간의 간극 변화를 측정하는 것이다. 측정은 추력 베어링의 Pad 간격에 대하여 로터의 위치변화를 구한다. 이것은 증기터빈과 원심 압축기에서 감시되는 가장 중요한 매개변수이다.
로터와 고정체간의 축방향 Rub에 대해 보호를 하는 축방향 위치 측정 시스템은 그림 4-5와 같이 Proximity Probe, Proximitor, 케이블 및 감시기로 구성되어 있다.
통상 Dual Channel Monitor가 사용되도록 추천되고 있으며 이러한 중복 감시 시스템 설치로 부품 손상으로 인한 잘못된 정지를 막을 수 있다. 어떤 Channel도 경계경보(Alert)와 위험경보(Danger)를 발생할 수 있지만 경계 경보는 “OR” 논리 회로를 통하여, 위험 경보는 “AND” 논리 회로를 통하여 동작한다.

그림 4-5 축방향 위치 측정 시스템
최선의 측정 결과를 얻기 위하여 축방향 위치 Probe는 온도 변화의 영향을 최소화하도록 가능한 추력 베어링 가까이 설치되어야 한다 [API 670에 의해 명시된 추력 베어링으로부터 Probe까지의 최대 거리는 12 인치 (300 ㎜)이다]. 축방향 위치 Probe는 열적인 과도 현상에 영향을 받지 않는 기계의 견고한 부분에 설치되어야 하며 축 또는 축과 일체인 추력 Collar를 감시해야 한다.
Noncontact Eddy-Current Probe로 측정하기 위해서는 Collar 표면이 매끈해야 하고, Collar 자체가 뒤틀려져 있지 않는 한 Collar Runout 측정은 축의 휨을 측정하는 가장 좋은 척도이다. 비일체(Non-integral) 추력 Collar로 만들어진 축의 축방향 위치 측정에 있어서 Collar가 이완되거나 축으로부터 이탈되어진다면 그 측정치가 회전자의 실제 움직임을 보여주지 않는다는 것을 인식하는 것이 중요하다. 추력 Collar가 이완될 경우에 축의 움직임을 경고하기 위해 또 다른 축방향 위치감시 Probe는 축의 일체인 부분 즉 축의 끝이나 단이진 부분을 관찰해야 한다. 이런 식으로 구성되었을시 주의해야할 사항은 축방향 위치 감시가 Dual Voting 로직으로 구성되었다면 추력 Collar의 이완으로 수반된 축방향 움직임은 위험 경보나 자동 정지를 일으키지 않을 것이다.
축방향 위치 측정이 축 끝에서 취해질 때 추력 Collar와 축의 끝 사이에서 일어나는 축의 열적 팽창은 측정에 영향을 줄 것이다. 이러한 열적 팽창은 대기 온도에서 운전온도까지 사이의 위치 변화를 평가하는 경우에 고려되어야 한다.
축방향 위치 Probe의 정확한 위치 설정에 상관없이 축방향 진동측정은 Misalignment나 커플링 잠금 같은 문제들을 분석하는데 아주 중요하다. 그러므로 축방향 위치 Probe와 마주보는 표면은 반경 방향 Probe에서 요구되는 것과 같은 표면조도와 Runout 공차를 가져야 한다.
3.2 半徑 方向 位置 (Radial Position)
반경 방향의 위치는 베어링 금속의 점진적인 손상을 판단하는 가장 중요한 척도이다. 또한 축의 안정성(편심)과 축정렬 관련 부하 상태를 평가하는데 사용되어진다. 축 변위 Probe로부터 DC Gap 전압으로 측정된 반경 방향 위치의 경향을 관리하는 것은 기계 상태의 총체적인 평가를 위해서 아주 중요하다. 대부분의 수력학적 베어링의 고장은 진동에 의하거나, 진동의 동반으로 일어나지만 별다른 진동 변화 없이 일어나서 반경 방향 Gap 전압의 변화에 의해 인지된 점진적인 고장의 경우도 있었다.
또한 반경 방향 위치 감시는 아주 가치 있으며 윤활유 공급 중단에 따른 재기동시의 큰 손실을 방지해 왔다. 이러한 상황에서 반경 방향의 위치는 베어링 손상이 일어나고 있는지 아닌지에 대한 정확한 평가를 제공해 준다.
X-Y Proximity Probe를 사용하는 많은 사람들은 기계가 운전중일 때는 DC Output이 유용하다는 사실을 모르고 있다. DC Output은 Radial 베어링 간극에 대하여 축의 평균위치를 나타낸다. 따라서 정상적인 Preload가 존재할 때에도 정상적인 축의 반경방향 위치를 예상할 수 있고 기동중, 정지중, Slow Roll중 및 정상 운전중에 축 중심선의 위치 변화는 기계의 힘이나 기계상태의 변화에 의한 것임을 알 수 있다 (그림 4-6).
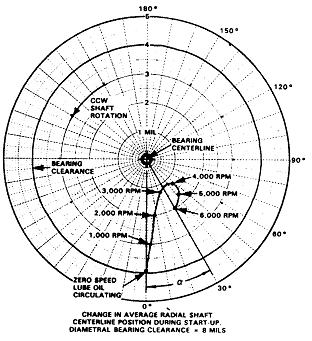
그림 4-6 축 중심선 위치변화
그림 4-7은 증기터빈의 기동시부터의 축 중심선의 평균 반경방향 위치를 나타낸 것이다. 기동전에는 축이 베어링 간극 내에서 하부 중심에 있었을 것이다. 기동후에는 이 위치로부터 비록 진동 진폭은 경보치 이하로 아주 낮았었지만 점차로 이동하여 축의 평균 반경방향 위치가 정상적인 베어링 간극밖에 있음을 보여주고 있다. 이 경우 기계 정지후 점검결과 Tilting Pad 베어링의 2개의 Pad가 마멸되었음이 드러났다.
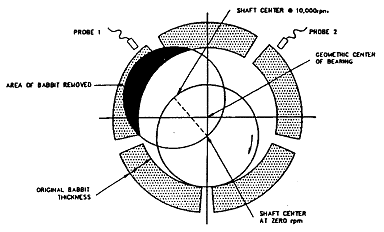
Shaft Movement Vector = 8.38 mils∠139°
Bearing Clearance = 6.5 mils
rpm | Time | DC Valuts (Volts) | ||
Probe #1 | Probe #2 | |||
1 | 0 | 1,100 | – 12.40 | – 9.28 |
2 | 10,000 | 1,115 | – 10.73 | – 9.42 |
그림 4-7 축 중심선 반경방향 위치에 의한 Pad 손상사례 발견
4. 편심과 편심 위치 (Eccentricity and Eccentricity Position)
발전소의 대형 증기터빈 및 가스터빈에서 편심을 나타내는 설비를 갖추는 것이 대단히 바람직하다. 편심은 정지시 Rotor의 휨(Bow)량이다. 이 휨량은 로터가 Turning Gear로 운전될 때 Proximitor로부터 천천히 변하는 D.C Peak-to-Peak 측정치로써 알 수 있다. Peak-to-Peak 진폭이 허용되는 낮은 값일 때는 휨 또는 그와 상응하는 Unbalance에 의해 원인이 되는 Seal 또는 Rotor Rub와 같은 손상은 염려하지 않고 기동할 수 있다. 편심 측정 Probe는 첫 번째 터빈 베어링으로부터 바깥쪽으로 가능한한 멀리 Front Pedestal내에 위치시켜 편심량을 측정한다.
대형 증기터빈에서는 Turning Gear 운전중이거나 Warm Up 운전중 운전원이 축의 휨량 및 진폭의 감소율을 눈으로 볼 수 있도록 편심이 Strip Chart Recorder로 기록되기도 하고 Multi Point Type Recorder에 나타낼 수도 있다.
편심위치란 저널 베어링 내에서 축의 정상상태의 위치량이다. 축에 내적 또는 외적 Preload가 없는 정상운전하에서 대부분 기계의 축은 설계상 Oil Pressure Dam이 있는 곳에 놓이게 될 것이다. 그러나 기계가 외적 또는 내적 Preload(정상상태의 힘)를 받으면 곧 저널 베어링 내에서 축의 편심위치는 어느 곳이든 이동될 수 있다. 편심위치 측정으로 베어링 마멸 및 Misalignment와 같은 Heavy Preload를 알 수 있다 (그림 4-8).
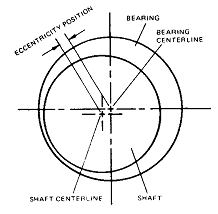
그림 4-8 편심위치
터빈 기동중에 축이 베어링 하부로부터 베어링 중심을 향하여 어떤 위치로 들어올려져 편심 위치가 변한다. 축밑에서 흐르는 Oil이 베어링내에서 축을 들어올리기 때문에 유막의 두께는 약 1 mil (0.254 ㎜)이며, 많은 베어링에 관하여 관찰해 보면 그것은 축이 Preload를 받는 방향으로 베어링 간극의 약 1/3이 되는 경우가 많음을 알 수 있다.
편심위치 측정치는 베어링에서 반경방향 진동 Probe와 종합된 Proximitor의 D.C Output을 감시함으로써 구해진다.
편심위치는 터빈의 부하, Alignment 등의 조건이 변화하는 상태하에서 변하기 때문에 Proximity Probe Transducer 시스템은 편심위치 변화가 Proximity Probe의 선형 범위 밖으로 이동함이 없이 발생하도록 충분히 긴 선형범위를 가지고 있는 것이 중요하며, 특히 큰 베어링 간극을 가지는 대형기계에서 더욱 그렇다. 편심위치의 주기적인 점검은 예지정비에 도움을 준다. 특히 Misalignment나 다른 Preload 상태가 가능성 있는 오기능 상태로 여겨지는 곳에서는 편심위치는 아주 면밀히 감시되어야 한다. 냉간 편심위치와 열간 편심위치를 서류화하여 훗날 편심위치의 비교를 위해 평가 기준계(Frame of Reference)로 수립하는 것이 중요하다.
5. 케이싱 팽창과 차동팽창 (Casing Expansion / Differential Expansion)
증기터빈이 승속할 때 로터와 케이싱은 온도에 따라 팽창한다. 케이싱 팽창은 바닥이나 기초에 대한 터빈 케이싱의 위치 측정으로써 LVDT (Linear Variable Differential Transformer)를 사용하여 측정한다. 케이싱 팽창 그 자체는 아주 중요하지 않으므로 TSI 시스템 내에 경보 설정이 없지만 케이싱 팽창과 차동팽창을 비교하면 운전원은 터빈이 기동중에 적절하게 열적 팽창을 하고 있는지 알 수 있다. 케이싱 팽창측정 설비가 터빈 좌우 양쪽에 설치된 경우는 케이싱 좌우의 부등 팽창량을 감지하므로써 케이싱의 Sliding Feet 부위에서 고착 여부를 알 수 있다.
진동과 더불어 차동팽창은 매우 중요한 측정항목으로 특히 터빈 기동중에는 주의 깊게 관찰해야 하는 사항이다. 차동팽창이란 케이싱에 대한 로터의 축방향 위치 측정이다.
증기터빈과 같은 대형기계에서는 기동중에 케이싱과 로터는 거의 같은 방향으로 또 같은 량으로 팽창하여야 한다. 만일 Unit를 너무 빨리 기동하면 로터가 케이싱보다 더 많이 팽창할 수 있다. 차동팽창이 크면 축방향으로 Rub가 발생하여 큰 손상이 발생하므로 터빈 전후 양쪽방향의 차동팽창을 Proximity Probe로 감시한다.
6. 캠/밸프 위치 (Cam/Valve Position)
캠 또는 밸브 위치는 증기밸브 개도(0~100%까지 증기가 얼마만큼 터빈 내부로 유입되고 있는가의 척도)의 측정이다. 이 밸브 개도의 검출은 통상 Rotary Potentiometer로 측정하지만 가장 좋은 방법은 회전하는 캠의 위치와 선형성을 갖는 LVDT를 사용하는 것이다 (그림 4-9). 캠이 회전하면서 상하 운동함에 따라 LVDT의 Plunger가 캠위치 감시기에 신호를 주도록 들락날락 한다.
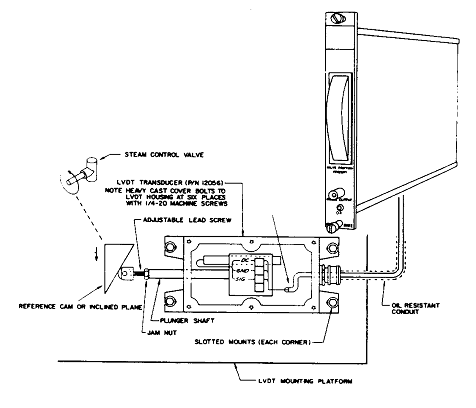
그림 4-9 LVDT로 캠위치 감시
7. 스피드 감시 (Speed Monitoring)
터빈, 발전기 세트의 속도지시는 전력 계통에 병입시 중요한 요소이다. 예전의 TSI 시스템에서의 속도감시는 아날로그 형식의 Tachometer 이었고 Front Pedestal에서 축에 부착시킨 영구 설비였다. 새롭고 신뢰성 있는 (±1 rpm) 디지털 회로의 출현으로 그림 4-10에서와 같이 기어 이빨이나 Keyway를 관찰하는 Proximity Probe와 더불어 디지털 Tachometer가 속도 측정용으로 보편화되었다. 정확한 디지털 속도 측정은 특히 터빈 발전기 세트를 전력계통에 수동 병입 시킬 때 유용하다. 정확한 속도를 알면 계통병입 하기가 보다 쉽다.
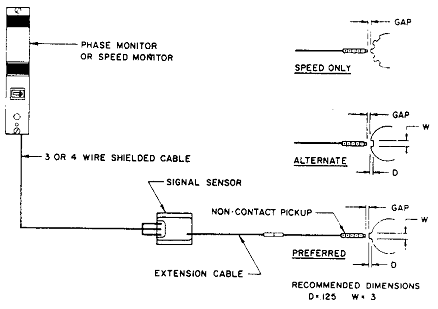
그림 4-10 Speed Monitor
8. 위상 감시 (Phase Monitoring)
위상각이란 축상의 고정 기준점에 대한 각 베어링에서 축의 상대적 위치이다. 제 2장 위상각 항에서 설명한 바와 같이 축상에 Keyway(Notch), Projection 또는 구멍을 뚫어 Once-Per-Revolution 마크(Keyphasor, Kø)를 만들고, 이 마크를 관찰하도록 위상 기준변위 Probe(Keyphasor Transducer)를 설치한다.
이 마크의 폭은 적어도 변환기 직경의 1.5배 이상이어야 하고 최소 1.5 ㎜의 깊이를 가져야 한다. 축이 1회전할 때마다 Keyphasor Transducer는 Keyway나 Projection과 1회 마주치게 되며 이때 Voltage Pulse(Keyphasor Signal)가 발생하는데 마크가 Keyway나 구멍인 경우는 Negative-Going Pulse를, Projection인 경우는 Positive- Going Pulse가 발생한다 (그림 4-11).
베어링 내에서 축이 회전하는 동안 축이 진동변환기에 가장 가까울 때 진동이 최대치(Peak)가 되며 이점을 Positive Peak라 한다. 그림 4-12와 같이 Keyphasor Signal과 진동 신호를 연합시켰을 때 Voltage Pulse가 발생하는 시점으로부터 진동 신호의 Positive Peak까지의 거리 또는 시간을 그 베어링에서의 위상각이라 한다. 이때 주파수는 서로 같아야 한다.
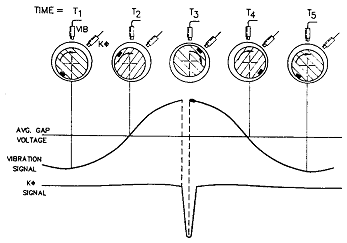
그림 4-11 축이 1회전시 마다 1회의 KΦ Signal이 발생
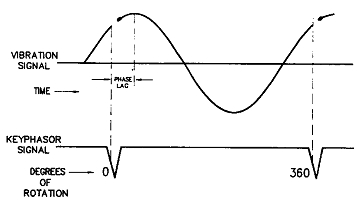
그림 4-12 위상각 측정
위상 측정의 용도로는
① Rotor Balancing
② 축의 Alignment
③ 축과 구조물의 공진 검출
④ 로터의 휨 위치
⑤ 균열축의 검출
⑥ 구조물의 Mode Shape
⑦ Rub 검출
⑧ 고정된 회전부품의 이완
⑨ ODS(Operating Deflection Shape)
⑩ Nodal Point의 위치 검출
등 다양하다.
위상각의 측정방법으로는 Keyphasor(Proximity Probe) 이외에 Optical Pickup, Strobe Light 및 Magnetic Pickup을 사용하는 방법이 있다.
Keyphasor의 기능으로는 위상각 측정 이외에 회전수 측정, 주파수 측정, Shaft Precession 방향 확인 및 기계의 오기능 구분 등이 있다.
9. 베어링 온도감시 (Bearing Temperature Monitoring)
9.1 베어링 溫度 測定의 利用 (Use of Bearing Temperature Measurements)
베어링의 하중과 성능을 나타내는 측정 매개변수 중에서 온도는 측정하고 이용하기에 가장 쉬운 것이다. 오래 동안 배유 온도는 베어링 상태의 외적인 지시를 제공할 것으로 기대되어 왔으나 배유 온도의 변화는 베어링 자체에 무엇이 일어나고 있는지에 대한 정확한 지시가 아닐 수도 있다는 것이 여러 시험에서 나타났다. 이전의 예를 인용하면 추력 패드에 묻혀 있는 열전대로 측정한 베어링의 금속 온도가 과부하로부터 고장에 이르는 동안 100 ℉(56 ℃) 상승했다. 그 때에 배유 온도와 축방향 로터 위치는 각각 5 ℉(3 ℃)와 0.002 인치(0.05 ㎜)만 변화했다. 그러므로 무엇인가 일어나고 있다는 것을 제대로 나타낸 것은 3개의 측정 매개변수 중에서 추력 베어링의 금속 온도뿐이었다.
베어링에 묻혀진 온도 변환기(열전대나 RTD)로 측정한 금속온도는 베어링 상태와 성능에 대한 정확한 정보를 제공하는 응답이 빠르고 측정이 쉬운 매개변수임이 증명되었다.
특히 기동․정지시와 같이 변화가 일어나기 쉬운 때에는 최적의 결과를 얻기 위해서 베어링의 온도가 기록 및 경향 관리되어져야 한다. 추력온도의 변화는 아마도 잠긴 커플링의 최적 표시중 하나로써 추력 베어링에 부하를 많이 지우고 기계의 추력균형을 변경시키는 비정상 운전 상태를 경고할 수 있다. 저널 베어링의 온도가 Wiping이 일어날 때 가끔 스파크를 일으킬 수 있다. 그러나 그 상태는 온도가 연속적으로 기록되지 않는다면 관찰되지 않을지도 모르게 아주 일시적일 수 있다 (가끔은 몇 분간 지속될 수도 있음). 베어링의 Wiping은 전형적으로 갑작스런 온도 상승을 수반하여 일어난다.
9.2 推力베어링의 溫度 (Thrust Bearing Temperature)
추력 베어링의 금속 온도 측정은 열전대나 RTD가 추력 베어링의 금속 접속선으로부터 약 0.030 인치(0.75 ㎜) 정도로 추력 패드에 박힌 두 개 또는 그 이상의 온도 변환기로 이루어진다. 보통 온도 변환기는 그림 4-13과 같이 추력 패드 폭과 회전방향으로의 원주상 75%에 위치되어 있다. 이 75-75 위치는 대략 베어링 부하의 중심에 접근하고 패드의 가장자리로부터 충분히 멀리 떨어져 있어 패드와 베어링 주위에서 순환하는 공급 윤활유와의 온도 구배에 의해 영향을 받지 않는다.
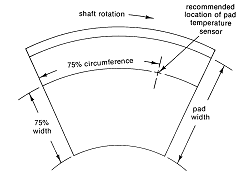
그림 4-13 베어링 온도 센서를 위한 추천된 75%-75%의
위치를 보여주는 추력 베어링의 Pad
과부하에 의한 추력 패드(그림 4-14)에서 가장 높은 온도 부분이 측정되어야 한다면 박힌 온도 센서의 위치 이동의 필요성을 나타낸다. 이 특정 패드에서의 가장 큰 하중을 받는 점은 검게된 면적으로 보이는 부분으로 폭으로 52% 정도에, 회전 방향으로 원주상 76% 부근에 중심이 있다. 추천된 온도센서 위치와 이 특정 패드의 실제 최대 하중점 사이의 약간의 폭의 편차에도 불구하고 추천된 위치에 설치된 센서는 검게 된 부분 안에 만족스럽게 있어 과부하 상태를 조기에 경보할 수 있도록 베어링 최대 부하점에 접근되어 있다.
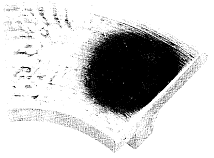
그림 4-14 최대 하중점을 나타내는 변색된 추력 Pad
최선의 보호를 위하여 3~4개의 온도 변환기가 추력 베어링의 Active측 Tilting Pad에 같은 간격으로 설치되어야 한다. Inactive 측에는 1~2개 온도 변환기가 참조 기준으로 사용되고 만일 기계에 Inactive 추력이 작용될 때를 위해서도 유용하다. 만일 2개의 온도 변환기만 설치된다면, 추력 베어링이 약간 기울어져 부등 부하분포가 되는 경우에는 90°떨어져 설치해야 한다.
추력 베어링 금속 온도는 일반적으로 부하와 더불어 직접적으로 변화한다. 대부분의 제작자들은 베어링 금속 온도 경보치는 250 ℉(120 ℃), 비상 정지치는 270 ℉(130 ℃)로 규정하고 있다. 실제로 경보 및 정지치 들은 베어링 제작사로부터 얻어져야 하고 허가 없이 초과시키지 말아야 한다. 보통 추력 베어링의 온도가 200~210 ℉(90~100 ℃)에 이르면 주의를 해야 한다. 부하를 받는 Active측에서 20~30 ℉(10~15 ℃)의 차이는 종종 관찰 확인된다. 또한 1~2개의 패드가 나머지 패드보다 약간 높은 온도 편차는 온도 변환기 깊이의 차이에 기인할 수 있다.
온도 감지 와이어는 다소 타이트한 간극 영역에 있는 베어링 주위로 루트가 정해져야 되기 때문에 케이싱 바깥으로 인도하는데 주의를 해야 한다.
9.3 Thrust Gap 電壓 調節 (Setting Thrust Gap Voltage)
축방향 위치 Probe의 Gap 전압 조절에는 많은 주의를 해야 한다. 추천된 방법이 비록 많이 있지만 그 기본적인 목적은 로터가 추력 베어링 간극의 중앙에 있을 때 Probe가 선형 범위의 중앙 가까이 있는지 확인하는 것이다.
그림 4-15에서 총 추력 움직임이 0.018 인치이고 Probe의 선형 범위는 -3 V DC에서 -19 V DC까지 0.080 인치이라고 가정하고 정(+) 추력방향을 Probe 안쪽으로 가정하자.
이 예에서는 선형 범위의 중앙은 축이 전후 양측으로 0.009 인치 움직일 수 있도록 -11 V DC이다. 200 mV/mil인 Probe라면 0.009 인치는 1.8 V 움직임과 같다. 일반적으로 추력 베어링에 상대하여 추력의 정(+)방향으로 축방향 Probe를 조절하는 것이 최선이다. 이런 다음 축방향 Probe Gap 전압을 -9.2 V DC [-11-(-1.8)]과 같게 조절하라. 마지막 확인 사항은 거리로 변환되는 조절 Gap 전압과 선형 범위의 끝 사이의 차는 작은 Wiping으로 인해 Probe가 선형 범위를 벗어나지 않도록 추력 베어링의 금속 두께보다 더 커야 한다. 이 예에서 Probe가 선형 범위를 벗어나기 전에 0.031 인치가 Active 방향으로 남는다. 이것은 적절하다. 만일 적절하지 않다면 Probe Gap은 약간 증가되어야 한다.
추력 간극이 큰 경우에는 회전자가 정(+)의 추력방향으로 최고로 움직였을 때 남게 되는 선형 범위는 적어도 0.015에서 0.020 인치(0.4에서 0.5 ㎜) 있는 것을 확인하라. 남아 있는 선형 범위는 추력 베어링의 문제 발생 동안, 추력 베어링의 문제 즉, 고장이 정(+)의 추력 방향으로 있더라도 Probe가 계속 작동되는 것을 보장해 준다.
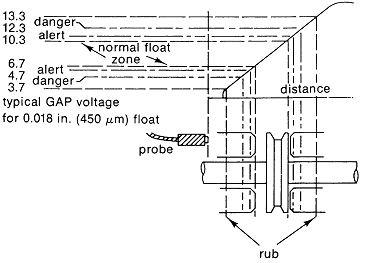
그림 4-15 축방향 위치 측정 – 전형적인 Gap과 경보 조정
대부분의 축방향 위치 감시 시스템은 조정 가능한 중앙 영점에 대한 축방향 위치를 감시한다. 선호되는 방법은 감시기의 중앙 영점을 추력 움직임의 한가운데에 회전자가 일치하도록 조절하는 것이다. 그러므로 이전 예에서는 Probe가 일단 적절히 조절된다면 추력 감시 시스템의 영점 제어는 추력 베어링의 Active 즉 정(+)의 방향측에 축이 있기 어렵도록 0.009 인치 더해진(+) 측정된 값이 되도록 조정된다. 이러한 추력위치 감시 시스템 방법으로 움직임과 경보의 Threshold는 중앙 영점을 중심으로 대칭이다. 이 시스템은 결코 계기 고장을 나타내는 값인 영점을 읽지 않는다.
9.4 저널 베어링 溫度 (Journal Bearing Temperature)
저널 베어링의 금속 온도는 종종 Misalignment 상태를 나타낸다. 베어링에 박힌 온도 변환기로 측정된 금속 온도는 베어링 성능은 물론 하중을 나타내는 쉽게 측정되고 응답이 빠른 매개변수이다.
온도 변환기는 최대 하중 영역이 있는 하부 베어링에 설치되어야 한다. 이것은 일반적으로 수직 중심선상에서 회전 방향으로 약 20°벗어나 있다. 여러 베어링 형식에 대한 상세 추천 사항은 API 670 규격에 포함되어 있다. 추력 금속 온도 측정을 위하여 앞부분에서 언급한 것과 같은 설치 방법의 고려 사항과 온도 제한이 저널 베어링 온도 측정에도 적용된다.
10. 비접촉 변환기의 활용 (Uses of Non-Contacting Transducers)
비접촉식 와류 진동 변환기를 사용하면 앞에서 언급한 모든 회전기계와 왕복동 기계의 동적운동, 위치측정, 속도 및 발란싱용 위상각 측정 외에도 다음과 같은 항목도 측정할 수 있다.
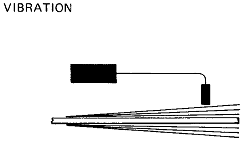
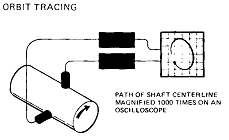
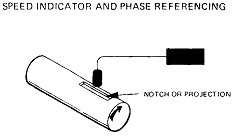
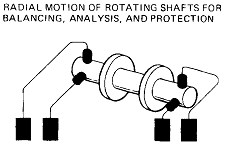
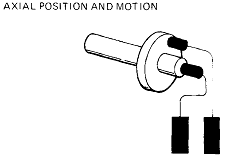
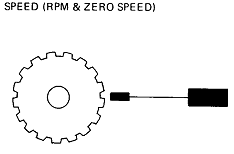
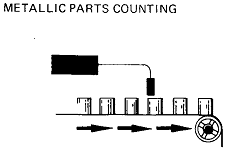
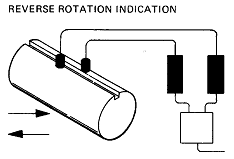
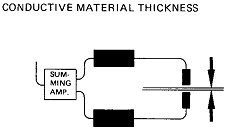
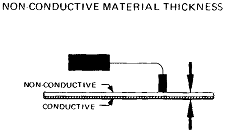
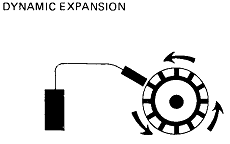
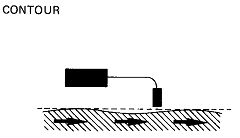
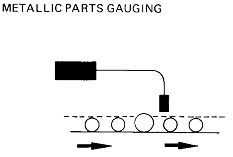