Considerations for Moving Machinery in the Field
8.1 런아웃과 축정렬 공차 (Runout and Shaft Alignment Tolerance)
8.1.1 런아웃 (Runout)
Runout이란 용어는 회전기계 축상에 존재하는 진원도 및 수직도의 불량 상태를 나타내는 량이며, 축정렬을 하기전에 점검해야 할 사항중 하나이다. 모든 회전기계의 축, 커플링 허브, 임펠러 또는 축에 견고하게 부착되어 있는 다른 부품들도 어느정도의 Runout(작은 것은 1 ㎚로부터 큰 것은 3 ㎜까지)을 가지고 있다.
반경방향(Rim)의 Runout은 축의 회전중심선에 관하여 축에 견고하게 부착된 부품 또는 축의 외주 표면에서의 편심이다. Face Runout은 축의 끝부분이나 축에 견고하게 부착된 부품의 표면상에 존재하는 비 수직도의 량이다. Runout 상태는 통상 다이얼 인디케이터로 측정하며, 로터 길이 방향에 따라 몇몇 위치에서 점검해야 한다. Face Runout의 량은 회전 중심선으로부터의 거리에 따라 변할 수 있다. Couplng에서 Runout 문제가 원천적으로 발생하는 3가지 범주는 커플링 허브 내경의 중심이 어긋나게 가공된 경우, 커플링 허브 내경이 비스듬히 가공된 경우와 축이 휜 경우이다. 또한 Runout 문제가 조립시 발생하는 경우는 커플링 볼트 및 볼트 구멍의 표면 불량으로 Coupling Slip이 운전중 발생하기 때문이고 또 커플링 볼트의 체결력이 불균일하여 공심 및 중심 이탈이 발생하기 때문이다.
회전기계 축에 관하여 허용 Rim Runout 값의 지침으로는 표 2-10이 사용되며 Face Runout 값은 0.02 ㎜ 이하를 추천하고 있다. 한편 Runout 값 측정 기록시 주의할 사항은 최고점(High Spots)과 돌출부(Hills)는 같지 않으며 역시 최저점(Low Spots)과 오목부(Valleys)도 같지 않다는 것이다. 즉 최고점과 최저점은 180°떨어져 발생해야 하며, 돌출부와 오목부는 예를들면 커플링 허브의 외주 어느 곳에서도 발생할 수 있다. 따라서 이와 같은 돌출부와 오목부에서의 Runout 값은 제외시켜야 한다.
표 2-10 최대 Rim Runout 권고치
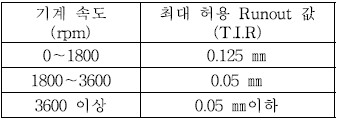
8.1.2 軸整列 公差 (Shaft Alignment Tolerance)
Flexible Coupling에서 축의 Misalignment란 기계가 정상운전 상태일 때 동력전달점에서 측정한 공동선형(Colinear) 회전축으로 부터의 상대적인 축위치의 편차(Offset)이다. 공동선형이란 동일선 또는 동일 축선을 의미한다. 두 축이 공동선형 상태일 때 두 축은 정렬 되어 있다고 볼 수 있다. 상대적인 축위치의 편차는 한 축의 회전 중심선과 상대축의 회전 중심선과의 차이를 측정하여 계산한다
그림 2-82의 Flexible Coupling의 경우 수직면(Side View)과 수평면(Top View) 각각의 동력 전달점에서의 편차가 4개 있다. 만일 이 4개의 편차중 최대치가 6 mils 이고 동력 전달점간의 거리가 4 inch 라면 최대 Misalignment 편차는 6 mils/4 inch=1.5 mils/inch 이다.
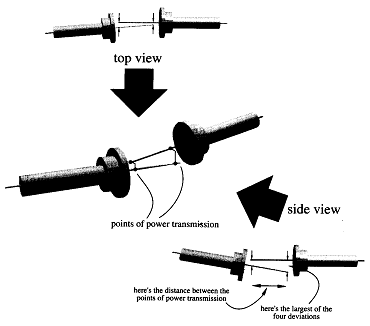
그림 2-82 Flexible Coupling에서 4개의 편차
Flexible Coupling을 가지는 기계에서 축정렬의 목표는 4곳의 편차가 어떠한 공차값 이하가 되도록 기계 케이싱을 위치 시키는 것이다. 그림 2-83은 회전기계의 속도, 동력 전달점에서의 최대 편차(Rim)와 각도(Face)간의 관계를 보여주며 또한 Flexible Coupling을 가지는 회전 기계의 허용 축정렬값의 지침으로 사용되고 있다.
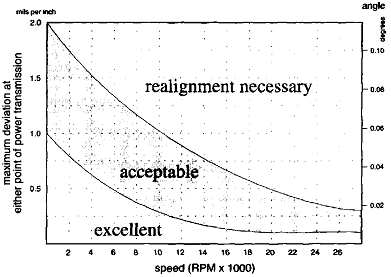
그림 2-83 축정렬 공차지침 (Flexible Coupling의 경우)
8.1.3 水平度 (Level)
수평도를 조정한다는 말은 정렬 작업을 한다는 말과 다른 의미이다. 수평도란 말은 지구의 중력과 관계가 있다. 어떤 물체가 수평상태에 있을 때나 물체의 길이 방향에 따라 여러 점들이 동일한 고도에 있을 때 그 물체는 수평(Level)을 이루고 있다고 한다. 다른 말로 표현하면 물체의 표면이 중력선에 수직인 경우 수평을 이루고 있다고 한다. 지구의 표면이 곡선이기 때문에 지역에 따라 수평상태의 회전기계 기초는 서로 평행 상태일 수는 없다.
비록 드문 일 이기는 하지만 구동기의 수평조정과 축정렬을 동시에 맞출 수는 있다. 또한 수평조정은 행하고 축정렬은 않되는 경우도 있고 반대로 축정렬은 행하고 수평조정은 안되는 경우도 있다. 축정렬 작업은 축의 회전 중심선들을 맞추는 것이기 때문에 중력선에 수직인 회전 중심선들을 가질 수도 있고 갖지 않을 수도 있다. 표 2-11은 수평방향으로 설치된 회전기계에 대한 추천된 수평도 범위이다.
표 2-11 수평 회전기계의 수평도 범위
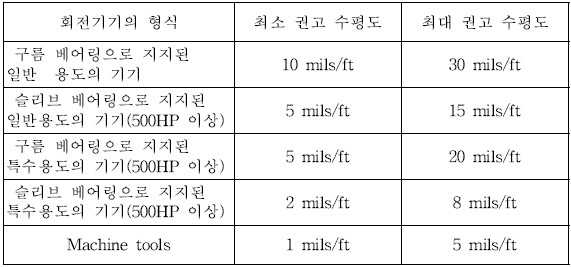
8.2 냉간 및 열간 축정렬 (Cold and Hot Shaft Alignment)
Cold Alignment는 운전조건이 아닌 정지 상태에서 2개 이상의 축을 원하는 축정렬 값으로 조정하는 기법이다. 이 냉간 축정렬 작업은 50℃ 이하의 순환유만을 공급하는 것이 관례이다. 이와같이 하는데는 2가지 장점이 있는데 그 하나는 베어링이 너무 뜨겁거나 찬 공정 과정중의 열이 없는 아주 안정된 대기 온도 상태로 하기 위한 것이고 또하나는 축정렬 측정치를 얻기 위해 축을 회전시키는데 편리하기 위하여 사전에 윤활을 하기 위한 것이다.
앞의 2~5항에서 기술한 축정렬의 측정, 작도 및 계산기법(예를들면 Rim 및 Face 기법, 역 다이얼 인디케이터 기법, Double Radial 인디케이터 기법, 축과 커플링 스플 기법 및 Face 와 Face 기법 등)은 모두 Cold Alignment 작업을 위한 기법들이다.
실제로 모든 회전체는 기동시와 운전 과정중에 위치가 변화하여 축정렬에 영향을 미친다. 축이 정상적인 운전조건 하에서도 동일 직선상에서 운전되기 위해서는 축의 이동량과 방향을 측정하여 이를 냉간 축정렬 과정에서 보상하는 것이 바람직하다.
현존하는 회전기계의 약 60%는 이동량이 미미하여 무시할 정도이나 나머지의 경우는 원활한 운전을 하는 기계도 있는 반면에 이로인해 문제가 되어 골치를 썩이는 기계도 있다.
일단 기계가 가동되면 기계를 이동하게 하는 여러 가지 인자들이 있다. 가장 일반적인 원인은 기계 자체의 온도변화(가스를 압축할때나 베어링에서 마찰로 인해 윤활유가 가열될 때) 때문이며, 따라서 이를 일반적으로 열적 이동(성장) 이라고 한다. 그외 기계를 움직이게 하는 원인들로는 고정 볼트의 이완, 옥외 설치된 기계에 미치는 기후조건 변화, 콘크리트 페데스탈의 가열 및 냉각, 무부하로부터 부하상태까지의 운전조건의 변화 및 로터 회전시 원심력에 대한 케이싱 및 지지구조물의 반작용 등을 들 수 있다.
기동정지가 빈번하거나 운전중 부하가 급변하는 기계에 대해서는 특별한 관심을 가져야 한다. 이와 같은 경우에는 특정 상태에서의 지속시간, 기계 이동량의 최대 및 최소치의 변화량 및 커플링과 Alignment의 공차 등과 같은 인자들에 가중치를 두고 절충 운전을 하여야 한다. 이러한 변화를 잘 관찰하고 기록하기 위해서는 주기적인 점검을 해야하며, 연속적인 축 위치도 감시하여야 한다.
정지상태로부터 운전상태로 변함에 따라 회전기계의 이동량을 관찰 한다는 것은 얼른 보기에는 대단히 복잡한 것 같이 보일지 모르지만 이 측정은 기계가 정지 상태일 때의 회전 중심선들의 위치와 운전상태 일때의 회전중심선들의 위치를 비교하는 것에 불과하다. 따라서 자료를 정지중일 때(냉간상태)와 운전중일때(열간상태) 취해야 한다.
기계가 정지 상태에서 정상 운전 상태까지의 축정렬 변화량을 측정할 수 있는 방법으로는 기계정지 직후 측정하는 법, Water Stand 사용법, Optical Eguipment 이용법, Laser Beam 이용법, Proximity Probe 이용법 등 다양하지만 각각 장단점을 가지고 있기 때문에 2개 이상의 방법으로 측정한 결과를 비교하여 선정하는 것이 바람직하다.
증기터빈, 가스터빈, 원심펌프, 왕복동기계 및 변속기 등은 단위 기계간의 유체 온도 차이로 인하여 좌우 및 축방향의 열팽창 뿐만 아니라 상하(수직)방향으로 Thermal Growth 차이로 인해 베어링간의 부하 안배가 균등하지 못하여 Oil Whip에 의한 고진동이 발생하게 된다. 재질에 따라 열팽창 계수가 다르지만 통상적으로 강의 열팽창량은 물체의 길이가 1 m일때 100℃를 올리면 이 물체는 1내지 1.1 ㎜늘어난다(1 ㎜/m/100°≈0.6 mils/inch/100°F). 이 팽창량을 감안하여 냉간 축정렬시 이를 보상 하므로써 정상운전(열간 축정렬 상태)중에 Smooth Alignment(Face 및 Rim 모두 Zero인 축정렬)가 되도록 하는 것이다.
8.3 기계이동 작업과 제한 (Machinery Movement and Restrictions in the Field)
현장에서 축정렬 하는데 7가지 기본 절차(① 안전조치 ② 사전 점검 ③ 축위치 측정 ④ 계산 ⑤ 이동량 결정 ⑥ 기계의 이동 ⑦ 운전과 점검)가 있다. 이런 절차중 현장에서 축정렬 하는데 가장 많이 시간이 소요되는 절차는 사전점검(커플링의 손상부품 확인, 기초 문제점의 확인, 베어링 간극 측정, Runout 및 Soft Foot 확인 등) 항목과 기계이동 및 측정 항목이다. 따라서 축정렬 작업을 단축 시키기 위해서는 값비싼 측정 장비를 구입 사용하는 것 보다 정확한 기계 이동을 위한 각종 Device를 설치하는 것이 바람직하다.
기계를 원하는 축정렬 위치로 옮기는 기술이야말로 중요한 기술이다. 아무리 0.01 ㎜ 정밀도로 측정하고 계산하여도 그렇게 정밀하게 이동할 수 있는 기술이 없다면 그것은 의미가 없는 일이다. 만약 그렇게 할 수 없다면 그 이전단계에 기울였던 모든 노력과 정성이 헛수고로 된다. 정확하게 기계를 이동 수정하는 기술이야말로 축정렬에서 노련미를 나타내는 척도이고 앞으로 개발하여야할 과제이다. 지금까지 땀흘리며, 온갖 정성을 기울여 작업하여 왔던 그 결과가 바로 여기에 좌우된다.
8.3.1 機械移動의 基本節次 (Machinery Positioning Basics)
(1) 축간 거리 (Axial Spacing)
구름 베어링으로 지지되는 로터의 경우 양 축사이의 거리는 정말 중요하다. 추력 베어링과 미끄럼 베어링으로 지지되는 로터의 경우는 로터의 실제 위치를 반드시 고려하여야한다. 예를 들어 슬리브 베어링에 의해 지지되는 전동기 회전자에 계자전류를 가하면 이 전자기장은 회전자를 고정자 계자장의 중심에 오도록 한다. 이 위치를 Magnetic Center라 하며, 전동기를 단독 운전하여 베어링실(Bearing Seal)과 같은 고정 기준점 근처에서 날카로운 Pen이나 Soap Stone으로 회전축상에 선을 긋는다. 이와 같은 전동기의 경우는 축간 거리를 결정하기 전에 Magnetic Center를 찾아 이를 보상(참고) 하여야 한다. 또한 원심 압축기, 터빈 등은 “Active” 추력 베어링과 접촉하여 운전하게 되므로 축간 거리를 설정할 때 “Active” 추력 베어링과 Thrust Collar가 접촉되도록 하여 측정해야 한다.
기계 제작자의 특별한 언급이 없는 한 축간 거리는 회전축 중심선에 가능한 가까운 곳에서 측정되어야 한다. 공차가 주어지지 않았다면 대충 +/-0.010″ 이내로 조립한다. 커플링의 잠금 현상은 이 Gap이 부적절하거나 과도한 축의 Misalignment가 있을 때 발생하므로 축간 거리의 중요성에 대하여 강조하지 않을 수 없다. 커플링의 목적은 회전력을 전달 하는 것이지 축사이의 추력을 전달하는 것이 아니다.
(2) 심 넣기 (Shim Stock)
기계의 상하 및 좌우 이동을 하는데 가장 일반적으로 사용하는 것이 바로 심이다. 심의 두께는 보통 1 mil에서 100 mils이며 100 mils 이상이 되면 스페이서(Spacer) 또는 플레이트(Plate)라고 부른다. 보통 심은 동, 탄소강, 스테인레스 등으로 만들지만 필요에 의해서 다른 금속으로도 만들 수 있다. 심 두께의 정확도는 통상 +/- 5%이다.
(3) 좌우 이동 (Lateral Movement)
나사 잭(Jackscrews)이나 다른 장비 등 어떤 것을 사용하던지 베이스 볼트를 풀고 조이는데 지장이 없도록 하여 가능한한 축정렬 목표값에 근접하도록 해야한다. 좌우 이동량을 확인하는데 사용되는 다이얼게이지의 부착위치는 나사 잭(Jackscrews)을 조이고 풀때 생기는 충격을 최소화하기 위해 움직이고자 하는 나사 잭(Jackscrews)의 반대 위치에 부착한다. 좌우로 움직일 때 베이스 볼트 한쪽을 고정점으로 하고 반대쪽을 움직인다. 한쪽을 목표 값만큼 충분히 이동시킨 후 베이스 볼트를 고정하고 반대쪽 볼트를 풀어 다시 목표 값으로 이동시킨다.
보통 기계를 측면 이동할 때 큰 실수를 범하기 쉽다. 대부분의 기계에서 한 지점을 고정하고 한쪽만 움직이는 것보다 양쪽을 똑 같이 수평으로 이동하는 경우가 더 많을 것이다. 예를 들어 Outboard를 움직일 때 Inboard가 움직이는 양을 감시하지 않으면 모르는 사이에 Inboard에서 변화가 생길지도 모른다. 따라서 문제점을 최소화하기 위하여 몇가지 제안을 한다.
• 기계의 Inboard와 Outboard 양쪽에 똑같이 인디게이터를 부착한다.
• 기계에 덕트나 파이프가 부착되어 있다면 볼트를 풀기전 인디게이트를 ‘0’로 조정한다 (만약 케이싱 볼트를 푼후 2 mils이상 움직인다면 “Soft Foot” 문제나 파이프 Stress문제를 수정하는 방안도 검토해 보아야 한다).
• 기계를 움직일때는 반드시 나사 잭을 사용한다
• 만약 나사잭을 사용하지 않는다면 베이스 볼트 하나를 고정점으로 하여 먼저 Outboard를 움직이고 다시 Inboard를 움직이는 방법을 택한다.
Inboard쪽 움직임을 확인하기 위하여 기계 케이싱의 한쪽에 다이얼게이지를 부착하거나 커플링에 부착한 다이얼게이지를 이용한다. 커플링 허브에 부착한 다이얼게이지를 한쪽 면에 고정하고 ‘0’으로 고정한 후 180°돌려서 나온 값을 읽는다. 커플링에 장착한 다이얼게이지의 값이 목표 값의 반이 될 때까지 Inboard쪽을 원하는 방향으로 움직인다. 다시 다이얼 게이지의 값을 ‘0’으로 고정하고 축을 반대로 180°돌려서 처음의 다이얼게이지의 값을 ‘0’으로 고정한 위치로 가서 그 값을 읽는다. 만약 그 값이 ‘0’이 나오지 않으면 Inboard쪽을 다시 미세 조정하여야 한다. 또한 각 베이스를 동시에 다이얼게이지와 나사 잭을 사용하여 움직여도 무방하다.
(4) 수직 이동 (Vertical Movement)
기계를 상하로 이동하는 것은 좌우로 움직이는 것보다 주변 여건상 훨씬 어렵다. 따라서 정확한 수직위치에 기계를 고정시키기 위하여 최소한의 기계만을 움직이고 수직 이동을 한후에 수평 이동을 하는 것이 바람직하며 시간도 절약된다.
8.3.2 移動 制限値 (Movement Restrictions)
축정렬 상태 측정, 이동량 계산 다음에는 실제로 기계를 이동하여 원하는 축정렬 상태로 조정해야 한다. 물론 허용공차 이내로 축정렬을 하게 되지만 로터가 고정자 내에서 완전히 정렬되어 고정자(케이싱)을 이동하는 경우와 터빈과 같이 케이싱 정렬이 이루어진 상태에서 로터를 케이싱 간극 내에서 축정렬을 하게 되는 경우가 있다.
케이싱을 이동하여 축정렬 하는 경우 상방향 이동은 대체로 큰 량도 가능하다. 하방향 이동은 이미 Foot 밑에있는 Shim Plate 두께 이상으로는 불가능하다. 이것이 상하방향 이동의 제한치 이다. 한편 좌우방향의 이동은 부착된 파이핑 시스템에 의한 이동제한과 기초볼트와 기초볼트 구멍간의 간격이 이동제한치 이다. 축정렬시 이동 제한치에 해당되면 한쪽 기계를 고정시키고 다른 기계를 이동시켜 축정렬 하려고 하지말고 두 기계를 동시에 이동시킨다면 이 제한치 내에서도 축정렬이 가능한 경우가 훨씬 많아진다.
케이싱 정렬 완료후 케이싱 내에서 허용공차 이내로 축정렬할 경우는 내부 간극이 작기 때문에 비록 축정렬은 잘되었어도 운전중 로터와 케이싱간에 Rubbing이 발생할 수 있다. 이러한 경우을 피하기 위해서는 모눈종이 위에 상하, 좌우 이동상태별로 각 부위마다 설계 간극 및 실제 간극을 표시하여 로터를 이동할 수 있는 간극을 알 수 있게 한다. 이를 Clearance Map이라고 하며 이를 근거로 하여 Rubbing 없이 축정렬 허용치 이내로 로터를 상하 또는 좌우 이동할 수 있다.
8.3.3 機械 移動時 留意 事項 (The Do’s and Don’ts of Moving Machinery)
• 기계 Foot 아래와 Base와의 접촉면은 먼지가 없고, 평면도를 유지하고 깨끗해야한다 (이때 필요하다면 “Soft Shim”을 사용한다). 수평 이동이 쉽도록 마찰면 사이에 윤활유를 얇게 발라도 무방하다.
• 기계아래 심을 넣고 뺄 때 손가락을 사용하지 말고 플라이어를 사용하라.
• 얇은 심이 여러장 들어 있다면 이를 제거하고 그에 대응하는 한 개의 두꺼운 철판으로 대신하라.
• 파이프가 설치되어 있는 경우 이것이 기계 이동에 어떠한 영향을 미치며 또 그 응력을 제거할 수 있는 방법을 고려하라.
• 수평이동 없이 하부에 심을 조정할 필요가 있을 때는 양쪽에 나사 잭을 고정시키고 작업을 하라. 만약 나사잭이 설치되지 않았다면 가능한 조정하지 않는 쪽은 볼트를 풀지말고 조정할쪽만 나사를 풀어 심을 수정하라.
• 하부 심을 수정한 후 볼트를 조일 때 다이얼 게이지를 부착하여 축정렬이 흩트러지지 않는가 확인하라. 흩트러진다면 교정되지 않은 Soft Foot 때문이다.
• 기계를 움직인 후에는 볼트를 꼭 잠갔는지 확인하라.
• 기계 축을 돌릴 때 커플링 볼트 사이에 파이프 렌치나 지렛대를 사용하지 말라. 체인 렌치나 특수공구를 제작하여 사용하라.
• 일반 탄소강 심을 사용하거나 페인트가 칠해진 심을 사용하지 말라.
• 얇은 심을 여러장 넣지 말라.
• 기계의 움직임을 알기 위하여 다이얼게이지를 설치하기전에는 볼트를 풀지말라.
• 베이스 볼트를 언더 컷(Under Cut)하지 말라.
• 기계와 베이스를 다우엘(Dowel) 핀으로 고정하지 말라.
8.3.4 軸 整列 問題點의 解決指針 (The Alignment Problems Troubleshooting Guide)
간혹 축정렬한 것이 도리어 더 나쁜 쪽으로 진행되는 경우도 있다. 또는 전체 축정렬 값은 어느 정도 잘 조정되었으나 허용공차를 벗어나는 경우도 있다. 같은 량의 심을 빼냈다가 다시 제자리에 넣은 경우 볼트를 조일 때 옆으로 움직이는 경우도 있다. 이렇게 난처하게 만든 것이 도대체 무엇이란 말인가 ?
① 잠시 멈추고 하던 일손을 놓아라. 큰 문제를 야기 시키는 원인은 조그만 일들 속에 있다. 다음 단계로 나가기 전에 지금까지 당연시해왔던 여러 일들을 다시 한번 생각하고 처음부터 확인해 보라.
② 1.6항(축정렬전 점검사항)에 특별한 주의를 기울여라. 축정렬에 문제가 있다면 반 이상이 바로 이부분에서 일어난다. 반복적으로 확인 작업을 하지 않았다면 다시한번 측정을 해보라. 만약 반복측정을 했다 하더라도 다시 한번 측정을 해보라. 만일 Runout 값이 과도하던지, Soft Foot이던가, 베어링 조립에 잘못이 있다던지, 베이스의 뒤틀림이나 기초대의 변형 또는 과도한 파이프의 응력이 있다면 그 문제점을 해결하라.
③ 지금까지 아무런 문제점을 발견하지 못했다면 좋은 징조이다. 자 이제 축정렬 측정시스템을 조사해보자. 만약 여러분이 다이얼게이지를 사용한다면 그것을 떼어내고 손으로 접촉면을 만저보아 튀어나온 점이 있는지 또 다이얼게이지 스템이 이동하는데 지장은 없는지 조사해 보라. 다이얼게이지의 스템이 부드럽게 움직이지 않으면 교체하라. 만약 여러분이 레이저 시스템이나 광학 장치를 사용하고 있다면 연결선의 상태가 양호한지 센서하고 연결은 잘되어있는지 확인하라. 배터리 상태도 확인하라. 축에 부착한 Clamp 상태도 확인하라. 축에 견고하게 부착되어 있는가 ? 레이저와 판독기가 브라켓에 잘 부착되어 있는가 ? 그리고 Clamp 장치의 처짐도 확인해 보라. 베이스 볼트의 Soft Foot 현상은 없는지 조사한다. 볼트를 여러번 풀고 조여서 그 변화값이 항상 일정한지 조사한다. 다이얼게이지의 값은 정확하게 읽었는지 의심이 나면 다시 한번 읽는 사람을 바꾸어가면서 확인한다. 그리고 읽은 값을 비교해 보라.
④ 축정렬 작도 기법을 사용한다면 정확히 작도하였는가를 점검한다. 만약 의심이 간다면 그 작업에 대하여 잘 아는 믿을만한 사람에게 다시 한번 해 보게 한후 그래프 2개를 비교해본다.
⑤ 지금까지 점검한 모든 결과가 만족하다고 느끼는가? 그럼 이젠 기계가 원하는 방향으로 정확하게 갔는가를 점검한다. 심을 삽입하기 전에 마이크로미터로 정확하게 심 두께를 측정하였는가? 심을 정확히 기계 밑에 설치하였는가? 심을 정확하게 양쪽 볼트 밑에 놓았는가? 새로운 심을 넣을 때 기존심을 빼내었는가? 새로운 심을 넣을 때 Soft Foot를 확인하였는가? 심 설치후 베이스 볼트를 정확하게 조립하였는가? 기계를 움직일 때 다이얼게이지를 부착하여 이동값을 확인했는가?
⑥ 움직임을 끝내고 다시 한번 축정렬 값을 측정해 보라. 만약 다이얼게이지를 사용했다면 축을 한바퀴 돌려도 항상 ‘0’값이 나왔는가? 그래프를 그릴때 원하는 Hot Alignment값을 고려하여 작성하였는가? 축정렬 허용공차를 알고 그 범위내에 조립하였는가? 정확한 축정렬을 위하여 심 조정값을 1 mil 단위로 조정하였는가를 확인해 보라.
⑦ 기계를 운전하고 난후 진동, 온도, 기타 운전변수를 측정했는가? 진동이 올라간다고 축정렬을 잘못하였다고 탓하는 이는 없는가? 만약 그렇다면 그들에게 이 책을 다시 읽어보라고 권해 보라.
해결 지침은 이상과 같이 단순하다. 만약 여러분이 축정렬을 잘하였다면 기초대는 안정적이고, “Soft Foot” 현상도 없고 파이프 응력도 없고 축정렬 작도는 완벽하게 한 것이고 운전중 기계의 거동상태도 잘 고려하여 완벽하게 작업을 한 것이다.