Vibration Analyzers Used in the Field
9.1 Bently Nevada社의 機械 管理 시스템 (Machinery Management System of Bently Nevada Corporation)
9.2 Bru”el & Kjaer社의 機械 管理 시스템 (Machinery Management System of Bru”el & Kjaer)
9.3 EntekIRD社의 機械 管理 시스템 (Machinery Management System of EntekIRD International Corp.)
기계의 중요도에 따른 분류를 통해 상태 감시 및 관리 방식이 달라질 수는 있으나 용량 및 크기에 관계없이 기본적인 기계적 반응과 특성은 동일하게 나타난다. 다양한 종류의 센서와 장비를 이용하여 기계를 관리하는 주목적이 바로 기계의 상태를 정확히 이해하고 이를 통한 시기 적절하고 예측 가능한 정비 및 보완 조치를 결정함으로서 궁극적으로 설비 관리비용 절감을 기대하는 것이므로, 이를 위해서는 기본적인 관리 시스템의 구성이 필요하게 된다. 이러한 관리 시스템은 기계의 중요도와 구성 요소의 반응 특성을 고려하여 각기 가장 효과적이고 경제적인 체제로 구축하여야 하며, 조치 가능한 정보를 제공하여야 한다.
기계의 상태를 정확히 감시, 관리하기 위해서는 기계의 동적인 움직임에 의한 반응, 즉 진동을 고려하게 되며 이와 함께 다양한 기계의 운전 상황에 따른 각종 변수들을 조합하여 그 상관관계를 분석하게 된다. 진동이라 표현되는 기계의 동적 반응은 모든 변수 중에서 가장 민감하게 기계 상태 변화를 추종하게 되므로 가장 우선적으로 감시하는 대상이 된다. 따라서 센서 및 장비는 이러한 진동 변수를 정확히 측정하기 위해 선택되어야 하며 이는 곧 기계 타입과 베어링 종류에 따른 진동 특성을 이해하는 기준에서 감시 및 관리 시스템이 구축되어야 함을 의미한다. 크게 베어링 종류를 유체 유막 베어링과 구름 요소 베어링으로 구분 할 경우 다음과 같은 동적 특성을 고려하게 된다. 유체 베어링의 진동 특성은 진동의 근원지인 회전축에서 발생되는 진동이 유체 유막을 통해 감쇠 되어 외부 하우징으로 전달되게 되므로 축의 움직임을 직접 관측하는 것이 효과적이며, 진동 및 공정 변수의 상관 관계를 분석하여 이를 통해 기계의 상태 및 문제점의 조기 발견을 통한 예측 정비 구현을 목적으로 하게 된다. 구름 요소 베어링의 경우는 회전축에서 발생되는 진동이 구름 요소를 통해 대부분 하우징으로 전달되므로 베어링 하우징에서도 진동을 효과적으로 측정가능하며, 이러한 타입의 베어링을 사용하는 기계류의 진동 관리 목적은 유체 베어링의 경우와는 달리 마찰 부위의 피로 현상으로 인하여 초반부터 진행되는 해당 베어링의 마멸 진행 상태를 감시하고 최적의 시기에 이를 교체하고자 하는 것이다.
이미 언급한 바와 같이 기계 관리 시스템은 이러한 기계 종류 및 중요도, 특성에 기준하여 가장 효과적인 체제를 구축하여야 하며 관련 센서 및 장비, 그리고 분석 프로그램 역시 이러한 특성을 고려한 최적의 정보를 제공해야 한다. 이러한 관리 시스템으로 가장 널리 사용되고 있는 몇 가지 시스템을 통해 이를 구체적으로 검토해 보기로 한다.
9.1 Bently Nevada사의 기계관리 시스템
Machinery Management System of Bently Nevada LLC
9.1.1 Data ManagerⓇ 2000 for Windows NT System (DM2000) : System 1으로 통합
9.1.2 TrendmasterⓇ 2000 for WindowsTM (TM2000) : System 1으로 통합
9.1.3 Machine Condition ManagerTM 2000 (MCM2000) : System 1으로 통합
9.1.4 Performance ManagerTM 2000 (PM2000) : System 1으로 통합
9.1.5 ADREⓇ for Windows System : ADRE Sxp/408 DSPi
9.1.6 3300 모니터링 시스템 : 단종
9.1.8 System 1 Optimization and Diagnostics Software
9.1.8 Orbit 60 (New)
9.1.1 DM2000
Data Manager® 2000 for Windows NT System (DM2000)
(1) DM2000 System
중요 기계류의 진동 관리 시스템으로 전 세계적으로 가장 널리 사용되고 있는 Bently Nevada사의 대표적인 시스템으로, 주 적용 관리 대상은 일반적으로 중요 기계로 분류되는 터빈, 압축기, 대형 펌프, 왕복동 기계 등이 해당된다. 이러한 중요 기계류는 기본적으로 해당 기계에 문제 발생시 전 공정의 50% 이상에 영향을 끼칠 수 있는 기계류를 의미하며 대부분 유체 유막 베어링 타입을 적용하고 있고 기본적으로 그 중요도에 의거하여 기계 보호를 위한 감시 시스템이 이미 설치되어 있다. DM2000은 이러한 중요 기계류의 정상 상태 및 과도 상태에서의 기계 운전 조건과 상황에 대한 온라인 컴퓨터 감시 시스템으로서, 기계의 경향 관리, 상태 진단, 예지 정비 기능 구축에 필수적인 데이터를 제공하게 된다. 이러한 데이터를 개인용 컴퓨터를 근간으로 감시 시스템과 인터페이스하여 여러 가지 유형으로 데이터를 수집, 저장하고 디스플레이 하게된다.
(2) 시스템의 구성
DM2000 시스템은 다음과 같이 4가지의 필수적인 부분으로 구성되어 있다.
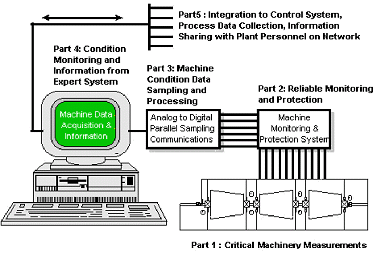
그림 6-39 DM2000 시스템의 구성
① 변환기와 감시 설비 : 현장에 영구적으로 설치되어 있는 각종 변환기(진동, 공정 변수 등)와 변환기로부터 온라인으로 계속적인 데이터를 받아들여서 이를 처리하고, 순시 값을 지시하게 하는 감시 설비이다. 일반적으로 감시 설비는 기계의 각종 변환기에서 입력되는 값과 현재 설정 값을 비교하여 초과할 경우 경보를 발생시키는 기능까지를 포함하고 있다. 기록계로 연결할 수 있는 기능 등을 부가적으로 포함하고 있으며, 기계 정지를 시킬 수 있는 설비와 연결되어 자동 정지가 가능하므로, 기계 보호 시스템으로 분류된다.
② Communication Processor (CP) : 앞서 언급된 감시설비에 연결되어 데이터의 처리를 실질적으로 관장하는 부분이다. 감시 설비와는 19 Pin과 25 Pin으로 구성된 한 쌍의 Cable로 연결되며, Keyphasor 신호는 별도로 연결되어 진다. 정상 운전 상태의 데이터만을 수집하여 처리할 수 있는 종류(DDI, Dynamic Data Interface)와 정상운전 상태뿐만 아니라 과도상태의 데이터도 처리할 수 있는 종류(TDIX, Transient Data Interface External)가 있다. 이들 CP들은 RS-232 혹은 RS-422 방식 등의 디지털 통신으로 서로 연결되어 DM2000 호스트 Computer에 연결되어 지는 것이 일반적이었으나, 근래에는 Networking을 통하여 DM2000 호스트 Computer에 연결되는 방식이 개발되어 주로 이용되고 있다. 기존의 디지털 통신에 비하여 Networking 방식은 전송속도면에서 약 10배 이상 빠르므로, 특히 과도상태 데이터를 처리할 경우 많은 장점이 있다. 또한 CP에서는 DM2000 호스트 Computer에 데이터를 보내는 동시에 Modbus나 Allen Bradley DF1 Protocol을 이용하여 공정용 Computer(DCS 혹은 PLC)에 데이터를 제공할 수 있다.
③ DM2000 호스트 컴퓨터 : DM2000 데이터 수집 프로그램이 내재된 컴퓨터로 CP의 데이터를 전송 받아서 기억 장소에 저장하고, 이들 데이터를 관리하여 Display 프로그램의 요청에 따라 필요 데이터를 지시하게 해주는 환경을 제공한다. 586 이상급의 Computer가 사용되며, Microsoft사의 Windows NT를 기본 Operating System으로 사용한다. 따라서 한글 사용이 가능하며, Windows NT의 표준적인 Networking 지원 기능을 이용하여 Display를 원거리에서 하는 것이 가능하다. 또한 현재 공정용 Computer System(DCS 혹은 PLC)의 Operating System 사용 추이가 Windows NT로 옮겨오는 추세임을 감안할 때 공정용 Computer와의 데이터 인터페이스 부분에서 많은 장점이 있다.
④ DM2000 프로그램 소프트웨어 : 데이터 수집용 프로그램(Data Acquisition Software), Display용 프로그램, 공정용 Computer와의 인터페이스용 프로그램(Process Correlation Modbus Interface)이 있다. 데이터 수집용 프로그램은 앞에서 언급된 호스트 컴퓨터에 설치되며, 데이터를 관리하며, Display 프로그램의 요청에 따라 필요 데이터를 연결하여 준다. Display 프로그램은 수집된 Data를 기계 관리 및 진단에 적합한 여러 가지 형태의 Plot으로 보여준다. Windows95 이상이 설치된 Computer System에 설치 가능하며, 다양한 형태의 Networking 방식(Networking, Dial-up Modem 등)으로 호스트 Computer에 연결할 수 있다. 공정용 Computer와의 인터페이스용 프로그램은 호스트 Computer에 설치되어 공정용 Computer의 데이터(운전 조건 데이터, Process Variable Data)를 DM2000 호스트 Computer에서 수집하여 관리되게 한다. 공정용 Computer와는 NetDDE 방식이나 Modbus 방식이 사용된다.
(3) 시스템 특징과 기능
기계 정보의 집합체로서 시스템 자체의 특징과 기능들 및 주변 시스템과의 인터페이스와 연계성에 관련한 특징 및 기능들로 구분할 수 있다.
① DM2000 소프트웨어 구조
Data Acquisition 및 Display Module 두개로 구성되어 있으며 Configuration Module은 이들 각각에 포함된 형태로 존재한다. Data Acquisition은 Monitor Rack과 CP에 접속된 컴퓨터와 공정 컴퓨터나 공정 제어 시스템과 접속하게 된다. Display Module은 데이터를 디스플레이할 모든 컴퓨터에 설치된다. Configuration Module은 Machine Train, 센서 및 Monitor System의 구성에 맞게 현장이나 원거리 어디서든지 Data Acquisition Package를 설치할 수 있다. Machine Train 번호, 센서의 타입과 설치 방향, 측정 단위, Keyphasor, Monitor Type 및 Full Scale Range, 디지털 접속에 의해 수집되는 공정 변수값에 대한 스케일링 변수 설정 등을 수행한다.
② DM2000 시스템 운영
정상 운전 상태에서 각 Monitor Rack에 연결된 CP들은 각 채널에서 입력되는 전체 측정값을 수집하고 이를 임시 메모리 버퍼에 저장한다. 또한 동적 데이터를 수집하기 위해 설정된 센서의 동적 신호 샘플을 수집하며 1× 및 2× 진폭과 위상각은 이로부터 계산된다. 데이터 수집 컴퓨터는 각 CP로부터 각 채널에 대한 최소, 최대 및 평균값을 받아들이고 이를 Historical Trend File에 저장한다.
③ Monitor Alarm Event
Monitor에 경보 상황 발생시 이와 관련된 모든 Monitor의 동적 데이터 버퍼에서 임시로 데이터를 저장하고 동시에 이 경보 상황이 데이터 수집 컴퓨터에 전달된다. 컴퓨터는 이 데이터를 자동으로 업로드하게 되며 Alarm Dynamic Data File에 저장된다.
④ Baseline/Conditional Baseline Data
정상 운전 상태에서 향후의 기준 값으로 사용하기 위해 수집되는 데이터를 Baseline Data라고 하며 이에 반해 특정 운전 상황에서의 기준 데이터로 저장하고자 할 경우 이를 Conditional Baseline Data라 한다. 이 데이터로는 Overall, Gap, 1× 진폭과 위상각, 2× 진폭과 위상각, 동적 파형 샘플 등이 포함되며 향후 문제점 발생 시 가장 기본적인 비교 기준 데이터로 활용 될 수 있다.
⑤ Plot Display Formats
과도 상태 및 정상 상태 데이터, 그리고 경보 상황 및 다양한 기준 데이터를 프로그램 내에서 선택 사용할 수 있다.
• Current Value
• Fast Trend and Trend Data
• Multivariable Trend
• Acceptance Region
• Orbit/Timebase
• Shaft Centerline
• Spectrum/Full Spectrum
• X and Y Plot
• Waterfall/Full Waterfall
• Bode Plot
• Polar Plot
• Cascade/Full Cascade
• Plus Orbit/Plus Spectrum
• Quickview
• Alarm List
• System List
• Bargraph and Machine Train Diagram
⑥ 타 시스템과의 연계 능력
• Ethernet과 Token Ring Network 기능 지원
• TCP/IP, SNA 및 IPX Network Protocol 지원
• 외부 Unix System에 X Windows Screen Display 기능
• Direct Digital Communication Link를 경유한 DCS, PLC의 공정 변수와의 상관관계
• Network상의 다수 사용자 디스플레이 기능
• Net DDE가 제공하는 개방형 구조 인터페이스 Protocol을 통한 데이터 이용
• 전통적인 원거리 통신 미디어를 이용한 원거리 사용
이외에도 온라인 진동 관리 시스템으로 필요한 기본적인 모든 기능 (FFT, Trend, Reference Data 수집 및 저장, Alarm 데이터 자동 수집, Orbit/Timebase Plot 등)을 두루 갖추고 있으며, Bently Nevada사의 진동 관리 System에 대한 경험을 바탕으로 기타 필요한 기능을 갖추고 있다. 또한 Windows NT를 운용 체제로 사용하므로 사용이 간편하며, Networking을 통한 정보의 공유가 손쉽게 이루어진다는 점이다. 또한 기계 제작업체나 진동 전문가 단체에서 Dial-up Modem을 통하여 원거리 접속이 손쉽게 이루어진다.
9.1.2 TM2000
Trendmaster® 2000 for WindowsTM
(1) TM2000 System
주로 전동기, Fan, 펌프, 블로워 등 산업체 다수의 일반 기계류를 관리하는 시스템으로서 중요 기계류와 같이 별도의 감시 시스템에 의한 기계 감시 시스템이 구축되어 있지 않고 대부분 Potable 진동 측정 장비에 의해 관리되는 기계류를 대상으로 하는 관리 시스템이다. 주로 볼 베어링 타입의 구름 요소 베어링을 사용하는 기계류가 그 대상이며, 기존의 Potable 측정기를 대체하고 경제적인 설치비용과 효과적인 관리를 위해 온라인 주기적 데이터 관리 방식(Periodic On-line)을 적용하는 시스템이다.
이 시스템이 적용되는 기계류의 특성은 일반적으로 중요 기계류에서 보이는 기계적 특성과 다소 차이를 보이게 된다. 대부분의 일반 기계에 해당하는 구름 요소 베어링의 특성에 따라 회전축과 베어링 요소의 기계적 피로 현상으로 인해 필수적으로 발생하게 되는 요소의 수명 제한과 동시에 적절치 못한 정비나 조립에 의한 급작스런 문제 발생은 지속적인 상태 감시를 통해서 관리 방식이 필요하게 된다. 따라서 온라인 방식을 적용하면서 시스템 설치 상태와 방식으로 간소화하는 시스템 구축 방식이 필요하게 되며 진동 특성에 기인한 분석 방식이 적용되어야 한다. TM2000은 이러한 일반 기계류의 진동 특성과 설비 방식을 고려하여 적용된 최초의 일반 기계류 관리 시스템으로 동 분야의 일반적인 관리 방식의 지침이 된 시스템이다.
(2) TM2000 System 하드웨어 구성
시스템은 현장 기계류에 설치되는 변환기류, 그리고 케이블과 데이터 처리기, TM2000 소프트웨어를 포함한 컴퓨터 시스템의 두 부분으로 구성되어 있다. 대부분의 구름 요소 베어링 부위에는 절대 진동을 측정하는 Seismic 변환기 타입이 적용되며 이러한 각각의 변환기들이 하나의 케이블 라인에 TIM (Transducer Interface Module)을 통해 접속되어 직렬 접속 방식으로 연결되게 된다. 이는 총 2040 포인트까지 하나의 시스템에 연결 가능하며 최종적으로 컴퓨터 시스템에 설치된 SPA (Signal Processing Adapter) 카드에 연결되어 신호 처리된다. 이러한 변환기 및 하드웨어 부분, 그리고 프로그램들은 기술력의 발달에 따라 지속적으로 업그레이드되고 있으며 신,구 제품과의 호환성이 계속 유지되고 있다. 적용 상황에 따라 유체 윤활 베어링 타입의 기계 역시 적용 가능하며 이 경우 변위 센서 적용과 함께 Keyphasor, 그리고 이를 처리하는 별도의 TIM이 적용되고 있다.
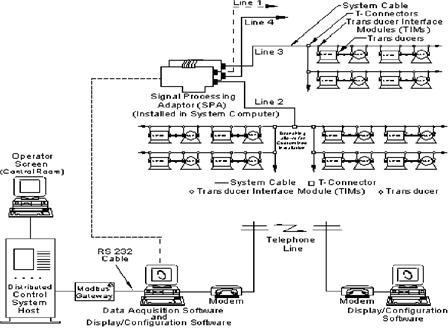
그림 6-40 TM2000 시스템의 하드웨어 구성
(3) TM2000 System 특성과 기능
DM2000과 마찬가지로 다양한 자체 기능과 타 시스템과의 연계 능력을 보유하고 있으며 하드웨어 점검 능력을 보유하고 있다.
① TM2000 시스템 구조
서버로 Windows NT를 사용하여 Standalone 방식뿐만 아니라 분산형 기계 정보 관리 시스템을 구성한다. 소프트웨어는 기본적으로 Data Acquisition Module과 Display/Configuration Module의 두 가지로 구성되며 추가로 DCS Interface Module이 적용될 수 있다. Data Acquisition 컴퓨터는 현장의 각종 센서에서 입력되는 정보를 수집하며 네트워크로 구성된 경우 네트워크 서버로 작동하게 된다. SPA Card를 내장하고 있으며 선택적으로 DCS Interface, Network, 외부 경보장치 또는 모뎀용 카드를 용도에 맞게 설치하여 운용할 수 있다. Display 소프트웨어는 어느 위치에서나 데이터 수집용 컴퓨터에서 수집한 내용을 디스플레이할 수 있고 환경 설정을 제어할 수 있다. 서버에 직접 설치될 수도 있으며 한 대 이상의 화면 표시용 컴퓨터에 Client로서 사용될 수도 있다. Configuration Module을 통해 다양한 소프트웨어 경보 상황 변수를 결정하고 적용할 수 있다.
② 외부 경보 능력
필요에 따라 외부 경보 릴레이 카드를 이용할 수 있으며 여기에는 Digital I/O Board, Cable and Relay Box가 포함된다. 각 릴레이는 시스템에서 제공되는 Not OK, No Data, Alarm1 및 Alarm2 상태를 지시하며 이를 Alarm Bell, Panel Light 또는 기타 경보 지시계에 와이어로 연결하여 기계 정보를 제공한다.
③ Plot & Point Display Formats
프로그램 영역 내에서 Group, Point 및 Plot영역으로 접근하며 관심 부분의 데이터 접근이 가능하다. 이를 통해 아래와 같은 데이터 종류를 이용한다.
• Overall/Direct 진폭
• Trend (Direct, Rotor, Prime)
• Orbit/Timebase
• Timebase
• Spectrum/Full Spectrum
• Acceptance Region
• Shaft Average Centerline
• Spectra vs Time (Waterfall)
• Full Spectrum vs Time
④ Test
시스템 테스트 프로그램으로 이를 이용하여 신호 처리기인 SPA Card의 정상 작동 여부, 모든 포인트의 스캔 및 상태 확인, 시스템 포인트 정상 여부 확인 등을 검토한다.
9.1.3 MCM2000
Machine Condition ManagerTM 2000
(1) MCM2000 System 개요
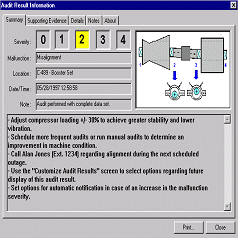
그림 6-41 MCM2000으로의 기계진단 결과
기계 감시 및 관리 체제 구축의 궁극적인 목표는 안정적인 기계보호 기능 구현 뿐 아니라 기계 운전 상태와 유지 보수에 소요되는 경비를 최소화하고 불시 정지와 같은 상황을 미연에 방지하여야 하며, 공장 정지 시간을 최소화하여 생산성을 향상시키는 것이다. 자산과 공정을 최적화 할 수 있도록 운전 가능한 정보를 확보하는 것이 필요하다. 이는 앞에서 설명한 DM2000/TM2000 등의 관리 시스템에서 수집, 관리되고 있는 각종 기계 상태 정보를 정확히 해석하고 이를 기반으로 적절한 조치를 취함으로서 가능하다. 그러나 현실적으로 이러한 데이터를 체계적으로 분석하고 현장에 수십 년간 축적된 다양한 정보를 취합하여 최적의 조치를 수행한다는 것에는 일정 수준이상의 전문 인력과 또는 관리 시스템 담당자, 그리고 다양한 경험 정보를 체계적으로 정리하여 이용하는 체제가 구축되어야 그 효과가 극대화된다. 이러한 문제는 대다수의 현장에서 인식되고 있는 것으로서 이러한 관리 방식과 체제의 차이로 인하여 양질의 관리 시스템을 구축하고서도 이에 준 하는 활용 효과를 얻는 것이 용이하지 않을 수도 있다. 이러한 문제점들에 대한 최적의 해결책의 하나로 인식되고 있는 것이 Bently Nevada사의 자동 진단 및 이를 통한 조치 제시 시스템인 MCM2000이다.
기계 상태 점검 및 유지 보수에 필요한 검사 및 분해 점검 일정을 줄이면서 제품 생산 운전 기간을 최대화하고 동시에 안전성, 신뢰성 및 장비 가용성은 향상 시켜야 하는 것이 현장에서 당면하고 있는 목표로서 이의 구현을 위해 사용되는 시스템이 MCM2000으로 인식된다. MCM2000 시스템은 기계의 상태를 24시간 연속적으로 진단하여 이상 유무를 판단하고, 적절한 조치를 권고하는 전문가 시스템이다.
(2) 시스템 구성
MCM2000은 기본적으로 중요 기계류 관리 시스템인 DM2000 시스템을 기반으로 하여 구성되는 시스템으로, DM2000에서 수집, 관리되고 있는 각종 상태의 데이터들에 대하여 지속적인 진단기능을 수행한다. 이를 통해 사용자가 설정한 기본 환경하에서 Bently Nevada사의 40여년에 걸친 회전 설비 분야의 경험이 축적된 Knowledge Base를 이용하여 분석과정을 거친 후 기계의 상태를 결정한다. 이러한 진단 작업이 끝나면, 결과는 사용자에게 디스플레이 되거나 사용자의 선택에 따라 통보되며 구체적인 내용으로는 각종 분석 내용에 대한 설명과 권고 조치 사항, 현장에서의 경험 조치사항, 그리고 필요시 관련자에게 직접 통보 가능한 연락 신호 송부도 가능하다.
MCM2000은 Data Extractor, Knowledge Base & Rules Processor, Display and Notification이라고 하는 네 개의 주요 소프트웨어로 구성되어 있다. 진단 과정이 끝나면 MCM2000 Display Icon (Bottom Tool Bar에 위치함)이 깜빡거리고 경고음을 울리거나, MCM2000 Display Message Box가 사용자의 스크린에 나타난다. 진단이 끝남을 알리는 이러한 두 가지 기능은 사용자가 선택 가능하다.
① Data Extractor
이 모듈은 각각 센서에서 수집된 정보를 DM2000으로부터 얻어내고 진단 과정에 이용하기 위해 이를 저장한다. 발췌되는 정보는 다음과 같다.
• Current Static Value Overall Amplitude, Gap Voltage, 1×, 2×, Not 1× 등.
• Waveform, Synchronous & Asynchronous Spectrum
• Trend File Data 일정 기간동안의 기계 상태 변화를 나타낸다. 이러한 정보는 문제의 진행 정도와 변화 추이를 평가하는데 이용된다.
• Machine Process Variable Data 진동 데이터와 현재 사용중인 기계의 관찰된 기계적 움직임이 서로 연계되어 사용된다. 이러한 데이터는 외부 시스템으로부터 NetDDE, Process Variable Monitor, TDIXconnX 혹은 Process Data Manager Communications Processor를 거쳐 DM 2000으로 수집된다.
• Monitor Point Status 감사를 마치는데 필요한 데이터의 유효기간을 결정한다. Knowledge Base와 Monitor OK Circuitry Level에서 모두 데이터 유효기간을 검증한다. 이러한 이중의 데이터 점검으로 부정확한 데이터가 기반이 된 감사를 최소화한다. 또한 시스템은 기계 진단을 위해 수동적인 데이터 입력을 요구하지 않기 때문에, 인간이 만들 수 있는 에러의 가능성을 제거한다. Data Extraction 공정상에서 나온 출력값은 후에 Rule Processing에서 이용될 Machine Attributes(기계 특성)이다.
② Knowledge Base & Rules Processor
Knowledge Base와 Rule Processor는 Extractor에서 나온 기계 특성들을 취합하여 이들을 Knowledge Base Rule-set과 함께 이용하기 위해 Machine Configuration 데이터와 결합시킨다. 기계 구성 데이터는 설계 규격과 Name Plate Rating이 있다. Knowledge Base Rule Set는 또한 User Defined Custom Rule을 포함하고 있다. 이러한 일련의 소프트웨어에서 얻어진 결과를 Malfunction Result라고 부르며, 이는 MCM2000 Data Base에 기록된다. 또, 이러한 진단 결과는 고장의 Severity Level(심각도 수준)을 나타낸다.
③ Malfunction Results Data Base
Malfunction Result Data Base는 진단 결과와 고장의 심각도를 나타내는 것뿐만 아니라 진단된 기계와 연결된 문서 파일을 포함하고 있다. 이러한 문서 파일은 Recommended Action을 포함하고 있거나 혹은 각 기계 고장에 대해 그 심각도에 따라 적절한 조치가 취해지도록 하는 내용을 포함한다. 진단 결과와 Recommended Action 문서 파일은 MCM2000 Client Display Software와 Notification Process로 보내진다.
④ MCM2000 Client Display
MCM2000 User Interface는 디스플레이를 거치게 되며 디스플레이의 주 스크린은 Audit Information Screen 혹은 Summary Screen이다.
(3) 시스템 특징과 기능
① DM2000과 데이터 호환
DM2000으로 기계 중요 공정변수와 동적 진동 데이터를 수집하고, 이들 데이터는 Bently Nevada 기계 진단 규칙(Rule Set)으로 처리하기 위해 MCM2000으로 추출된다. 기계로부터 발생하는 진동 및 공정에 대한 데이터는 기본적으로 DM2000에 의해 수집된다. 또한 DCS에 존재하는 다른 제어변수들도 수집이 가능하다. 이렇게 수집된 데이터는 MCM2000 시스템이 기계 상태를 판단하는 기초 데이터로 사용된다.
② 적용 가능한 정보 (Actionable Information)의 자동 통보 기능
MCM2000은 현장 또는 원격 디스플레이 기능, 회사의 LAN/WAN 통신망을 통한 E-mail, Paging/Beeper 시스템을 이용해 해당 담당자에게 특정한 기계의 비정상 상태 정보를 자동으로 알린다. 기계에 발생한 이상은 DM2000 시스템상의 데이터를 변화시킬 것이다. 이와 같은 변화는 많은 기계를 적은 수의 인원으로 관리하는 경우 매우 발견하기 어려울 수도 있고 정확한 진단을 수행하는 것도 힘든 일이다. DCS와 DM2000 시스템에서 제공하는 데이터라고 할지라도 수많은 데이터 중에서 유용한 정보를 추출하는 것은 매우 힘든 일이 될 수 있다. 이런 경우 MCM2000 시스템은 자동으로 데이터를 추출하고, 추출된 정보를 이용하여 유용한 정보를 구분하여 이미 정해진 진단 규칙을 통해 기계의 상태를 진단한다. 진단 결과를 토대로 즉각적인 조치가 요구되는 경우 각 공장에서 정해진 규칙에 따라 조치를 취해야 하는 사람에게 여러 가지 통신 수단을 통해 조치 내용을 통보하는 것이 가능하다. 적절한 시기에 기계의 이상 상태에 대해서 알게 되면 빠른 조치를 통하여 기계가 더 이상 손상되지 않도록 예방하는 효과가 있다. 만약, 전문가에 의해 진단을 수행하고 조치 사항을 결정하는 기간동안에도 기계는 운전될 것이므로 급속히 진전되는 기계 문제의 경우에는 치명적인 손상이 발생할 수도 있다.
③ 사용자의 환경구성 옵션
시스템은 기능적으로 융통성이 뛰어나기 때문에 사용자는 기계 감사 결과와 이들 결과 보고서에 적절한 조언내용을 첨부하는 능력을 별도로 구성할 수 있다. 이것은 사용자에게 특정 기계의 기계적 상태에 대한 운영절차 또는 방법론에 합당한 올바른 기능을 제공한다. 기계의 특성은 제조사별로 특성이 다르며 각 공장의 운영 조건에 따라 조치 방법이나 결정자가 다를 수도 있다. 이런 사용자들의 특성을 고려하여 MCM2000 시스템은 개별적인 조치 방법에 대한 구성을 수행할 수 있다.
④ 교육 기능
기계의 이상상태의 실체를 확인하는데 이용하는 추출 데이터와 더불어 자료화된 이상상태를 보기 위해 온라인 교육을 이용할 수 있다. 특정 사건에 대한 정보는 문서로 작성 보관되어 기업지식(Corporate Learning)을 끊임없이 개선한다. MCM2000 시스템이 제공하는 보고서 작성 기능은 최소의 시간을 투자하여 현재 기계가 겪고 있는 문제에 대한 조치 방법뿐만 아니라 이론적 배경에서부터 근거 데이터까지의 자료를 얻을 수 있다. 이와 같은 보고서를 통해 기계 관리자들은 다른 공장에서 발생한 문제에 대해서도 간접적인 경험을 통해 학습 효과를 얻을 수 있다.
⑤ Communication의 향상
MCM2000은 Windows NT의 Communication 능력을 이용한다. 향상된 Network와 원거리 접근 능력으로 Network Communication을 확장시키고 각 부서간의 의사결정을 향상시킨다. MCM2000은 Windows NT Remote Access Server(RAS)의 능력을 이용하여 고객이 모뎀을 통해 원거리에서도 효과적으로 통신할 수 있도록 한다. 이러한 기능은 무인 파이프라인 발전소에서 매우 유용하게 이용할 수 있다.
⑥ 하드웨어 비용 절약
MCM2000 Server와 Client Software Module은 DM2000 Server와 Client Module과 동일한 PC 상에 설치될 수 있다. 이는 하드웨어 비용을 절감시키고 사무실과 Control Room의 공간에 여유를 준다.
⑦ 다양한 진단 일정 선택 기능
진단 작업은 다음과 같은 세 가지 경우에서 실시될 수 있다.
• Hardware and Software Alarms : Machine Condition Manager 2000은 모니터 시스템의 하드웨어 알람 혹은 Data Manager 2000에서 나온 소프트웨어 경보를 감시하여 이와 관련된 기계를 즉각적으로 진단한다. 이러한 운전 모드는 정해진 진단기능을 통해 선행되며 언제든지 자동적으로 발생한다.
• Scheduled Audits : 이 모드는 기계가 특정한 시간 간격에서 분석되도록 사용자가 기계의 수를 정의할 수 있도록 한다. 기계 진단은 매 시간, 매일, 매주 단위로 이루어지도록 설정할 수 있다.
• Manual : 어떤 사용자라도 특정기계에 대해 즉각적인 진단을 진행 할 수 있다.
9.1.4 PM2000
Performance ManagerTM 2000
(1) PM2000 System 개요
설비 운영 부문에서의 비용 절감 문제는 공장 운영에서의 궁극적인 목표의 하나로 통계적으로 공장 운영을 위해 지출되는 비용 중 가장 큰 요소는 연료비이다. 성능 면에서 고찰시 운전 효율 증가시 큰 비용 절감 효과가 기대되며 세계적으로 각 발전소들은 경쟁사들보다 효율적인 운전을 통해 경쟁력을 제고해야 하는 것이 현실이다. 일반적인 Gas Turbine 운전에 소요되는 비용 분석 결과는 이러한 내용에 대한 좋은 보기로서, 전체 유지비용의 55% ~ 85%를 차지하는 것이 연료비이고 기계의 유지 보수비용은 2.4% ~ 3.5%에 지나지 않았다. 따라서 공장의 이윤을 극대화하기 위해서 가장 관심을 기울여야 하는 것의 하나가 연료비로 귀착된다.
성능에 관한 데이터는 기계 관리 지침에서도 매우 중요한 요소이다. 기계 관리는 손상을 방지하는 것뿐만 아니라 경보 설정치 이하로 기계를 운전하는 것처럼 기계를 완벽하게 이해하는 것이다. 이러한 목표를 성취하기 위해서는 진동에 대한 정보뿐만 아니라 다른 정보들도 요구되는데, 진동 데이터와 성능에 대한 데이터는 운전되고 있는 기계를 이해하는데 많은 도움을 주는 요소들이다. 이러한 정황을 근거하여 기계의 상태 감시 및 관리를 통한 기계 설비 관리의 최적화에 더불어 성능 감시를 추가하여 관리하고자 하는 것이 산업체의 추세이다. 본 내용은 이러한 성능 감시 시스템 중 Bently Nevada사의 PM2000을 대상으로 그 기능과 구성, 특징 등을 언급하고 있다. Bently Nevada 역시 성공적인 기계 관리 도구의 한가지로 PM2000을 출시하였고 이를 다른 관리시스템과 연계하여 최적의 설비 관리 시스템을 구축하고 있다.
PM2000은 열역학에 근거하고 있으며, 성능을 감시하여 운전중인 기계의 효율을 향상시킬 수 있도록 정보를 제공하는 제품이다. 기계의 상태를 프로세서와 진동 데이터를 서로 연관 지어 작업을 수행할 수 있는 환경을 제공함으로써 높은 효율과 좋은 기계의 상태를 유지하도록 지표를 제공한다. 또한 DM2000과 통합되어 향상된 기계 관리 체계를 구성한다. 성능 감시와 진동 감시를 조합함으로써 기계 문제를 진단하고 정비 활동 계획을 수립하는데 큰 지표가 된다
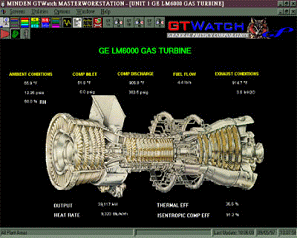
그림 6-42 가스터빈 성능을 감시하고 있는 PM2000 화면
(2) PM2000 System 구성
PM2000 프로그램은 원하는 기능을 제공하는 각각의 모듈로 구성되어 있다. 다음에 나오는 부분에서는 각 모듈에 대한 개관과 기술적인 시도에 대해 설명하였다. 장비 성능에 관한 ASME Performance Test Codes (PTCs)와 다른 규칙을 바탕으로 하는 계산 과정을 이용하여 연산이 수행된다. PM2000은 모든 타입의 발전소 장비와 공정에 관한 문제를 해결하고, 시험해 본 경험을 바탕으로 한다. 다음에 나오는 것은 시스템 모듈에 관한 설명이다.
① Data Point Configuration Module
Data Point Configuration Module은 현장에서 수집된 공정 데이터 입력값, 수동 입력값, 변수를 기본으로 하는 방정식과 스케줄 그리고 계산된 값 등 모든 시스템 데이터 포인트를 유지하는데 이용된다. 각각의 데이터 포인트는 Point ID, Point Description, Alarm Limits, Integrity Limits, Calibration Factors, Default Definitions, Initialization Information과 같은 정보와 연관되어 있다. 만일 데이터 포인트를 에러 없이 Data Manager 2000으로부터 받은 것이 확인되면, 그 값은 하나 혹은 그 이상의 독자적인 값을 바탕으로 하는 데이터 포인트의 무결성과 비교된다. 이 값이 이러한 범위 밖에 있다면, Smart Default 혹은 Fixed Default로 교체된다. Smart Default는 다른 Point ID(예, Gross Load, Compressor Discharge Pressure 등)에 따라 변하도록 설정 되어있다. 데이터 포인트 무결성은 Quality Status를 나타내도록 코드화 되어있는 색깔로 스크린 상에 나타난다. 데이터 포인트와 관련된 모든 계산된 값은 스크린 상에 그에 적합하게 코드화 되어있는 색깔로 나타난다.
② Historical Data Storage Module
데이터는 보통 다음의 네 가지 방식으로 저장된다: 1) Snap Shots, 일분 당 한번; 2) 매 시간 평균; 3) 변동 평균; 4) 매일 평균. Snap-Shot은 전 월(月)의 값과 당월의 값이 비교 가능하다. 매 시간 평균, 변동 평균, 매일 평균값은 전 년(年)의 것도 비교 가능하다. PM2000의 표준 저장 데이터 파일의 포맷은 Microsoft Access이다. 기록된 데이터는 Tape Drive 혹은 Optical Drive에 저장 할 수 있다. Optical Drive는 Performance Manager 2000s Historical Trend Recovery 특성을 이용하여 전 년도 데이터를 직접 이용할 수 있다. Tape Drive는 주기적인 시스템 Backup이 이루어지게 하기 위해 표준 Backup Software를 사용한다.
③ Database Report Writer Module
PM2000은 Database 보고 기능으로 Crystal Report를 사용한다. Crystal Report의 사본은 PM2000의 일환으로 제공된다. 표준 보고서 기능은 물론, 사용자는 Crystal Report Designer를 이용하여 사용자 정의의 보고서를 작성한다. Report Writer는 자동 보고서, On-Demand Test Logs, 연말 보고서 등을 포함한 광범위한 보고서 기능을 제공하며 사용자 정의로 구성된 보고서는 PM2000이 저장한 데이터베이스와 환경 설정 데이터 (예, Data Point Alarm Levels) 모두 이용 가능하다. Crystal Reports는 사용자가 보고서를 모두 디자인을 할 수 있도록 공식, 연산 기능, 분류 기능, Boolean Logic, Conversation 기능과 더불어 글꼴, 자동 현재 시간 표시 기능, 쪽 설정, 여백 등의 기능을 제공한다. 보고서가 작성되면 Custom Report는 사전에 정해진 시간에 자동적으로 혹은 요구에 따라 산출될 수 있다. 네트워크 환경에서 시스템 Report(표준과 사용자 정의 Report 모두)는 허가 받은 모든 사용자가 이용할 수 있다.
④ Screen Builder Module
Screen Builder Module은 스크린 디스플레이의 변경 및 작성하는데 이용되는 모듈인데 이는 암호를 이용한다. PM2000은 사용자 기계의 성능을 묘사하는 몇 가지의 실시간 그래픽 스크린을 제공한다. Screen Builder Module을 사용하여 이러한 스크린들은 수정될 수 있다. PM2000의 Screen Builder는 사용자 정의의 실시간 스크린 디스플레이를 작성하는데 이용될 수 있다. 종류에 상관없이 그래픽 소프트웨어 패키지를 이용하여 이미지를 작성하여 이를 Metafile(*.WMF) 혹은 Bitmap(*.BMP) 형식으로 저장한다. PM2000 Display Builder를 사용하여 그래픽 파일을 선택, 원하는 Point와 Label을 삽입하고 아이콘을 지정하며 새로운 스크린을 활성화시킨다. 새 아이콘이 컴퓨터 단말기에 디스플레이 되며 이는 모든 시스템 사용자가 이용 가능하다.
⑤ Configuration Maintenance Tools Module
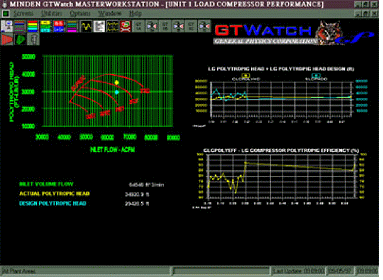
그림 6-43 PM2000에서 환경 구성 정보의 표시 예
PM2000의 주요한 특성은 다시 프로그래밍할 필요 없이 쉽게 유지할 수 있는 능력이 있다는 것이다. 시스템 환경 구성 유지에 필요한 도구들은 PM2000에 통합되어 환경 구성 데이터에 쉽고 빠르게 접근할 수 있다. 예를 들어, 스크린상에 나타난 값중의 하나를 두 번 클릭하면 즉각적으로 그 값의 환경 구성 정보(Configuration Information)를 볼 수 있으며 부가적 기능들은 편리함을 위해 단일의 스크린으로 모아지게 구성되었다. 환경 구성 데이터는 암호 처리 되어있으며 임의의 시간에 사용 권한이 있는 사람에 의해 갱신 될 수 있다. 네트워크 환경에서는, 환경 구성 변화는 주컴퓨터 단말기에 의해 이루어지며(암호 입력시) 모든 사용중인 컴퓨터 단말기에 의해 자동으로 감시된다. 암호는 변경 가능하며 소프트웨어 보존을 위해 사용자에 의해 조정된다.
⑥ Equipment Performance Modules
PM2000은 가스 터빈, 압축기, 펌프의 성능을 감시하도록 환경 구성된 형식에 따라 열역학적 계산과 방정식을 포함하도록 발전되어왔다. 이러한 정보를 이용하여 사용자 기계의 성능은 그래픽으로 디스플레이 되며 기계의 현재 성능과 기대 성능도 함께 디스플레이 된다. 기계 성능은 사용자 기계의 특정 설계 변수를 바탕으로 하고 이러한 기능을 통해 사용자는 실제 기계의 성능과 기대 되는 성능을 서로 비교해 볼 수 있다. 일반적으로 사용자 기계의 그래픽, 입출력 데이터, 실제 효율과 기대 효율 그리고 연관된 다른 데이터가 디스플레이 된다.
⑦ Gas Turbine Performance Module
Gas Turbine Module은 연속적으로 변화하는 상황하에서 기계 상태의 정확한 평가를 제공한다. 압축기 효율성, 전체적인 터빈의 효율성, 열 용량, 연소 공기량(Combustion Air Flow), 배기 온도와 같은 주요 성능 변수들이 감시된다. 설계 변수는 실제 성능을 직접 비교하기 위해 현장 상태 값과 비교된다. 이러한 비교를 통해 사용자는 저하된 기계 성능을 감시하는데 필요한 정보와 기계 운전과 유지 활동에 필요한 적절한 일정을 결정할 수 있다. 이러한 모듈을 지원하기 위해 다음과 같은 공정상의 데이터의 측정이 필요하다.
• Fuel Flow(S)
• Fuel Heating Value
• Ambient Temperature
• Ambient Pressure
• Relative Or Absolute Humidity
• Compressor Section Inlet Pressure
• Compressor Section Inlet Temperature
• Compressor Section Discharge Pressure
• Compressor Section Discharge Temperature
• GT Exhaust Temperatures
• Gross Generation(Kw) Or Shaft Speed And Torque
• Kvars (Generator Drive Applications)
⑧ Gas Compressor Performance Module
PM2000 Compressor 모듈은 기계 성능 저하로 인한 Off-Design 성능을 결정하는데 이용하는 특정 수단이다. Head, Flow, 속도와 효율, 설계 특성 치에 관한 각 압축기의 성능 Map은 참고자료로 사용하기 위해 Database에 저장되며 PM2000은 실제 운전 변수들을 계산하고 설계에 대한 그 값들을 비교한다. 설계 성능 Map의 그래픽이 디스플레이 되고 온라인 상에서 비교된 압축기의 실제 성능과 기대 성능이 압축기 Map에 나타난다. 저장된 특성들의 경향을 이용하여 실제 운전 데이터 대 설계 Plot이 수집되고 이는 담당자에 의해 진단될 수 있다. 이러한 모듈을 지원하기 위해 다음과 같은 공정상의 측정이 필요하다:
• Compressor Section Suction Pressure
• Compressor Section Suction Temperature
• Compressor Section Discharge Pressure
• Compressor Section Discharge Temperature
• Compressor Speed
• Gas Flow
• Driver Power (Motor Voltage & Current Or Shaft Speed And Torque)
• Gas Analysis
⑨ Pump Performance Module
PM2000은 펌프 기능 저하로 인한 Off-Design 성능을 결정하는데 매우 유용한 도구이다. Power, Head, Flow에 대한 각 펌프의 설계 성능 특성 치 곡선은 참고자료로 이용하기 위해 Database에 저장되며 Database는 설계와 비교하기 위해 실제 운전 펌프 Power, Flow, Head Pressure를 찾아낸다. Historical Trend Recovery를 이용하여 각 펌프에 대한 실제 운전 데이터 대 설계 Plot을 구할 수 있다. 이러한 모듈을 지원하기 위해 다음에 나온 공정 상의 측정이 필요하다.
• Pump Power (Motor Voltage And Current Or Shaft Speed And Torque)
• Pump Speed
• Pump Suction Pressure
• Pump Suction Temperature
• Pump Discharge Pressure
• Pump Discharge Temperature
• Pump Flow
(3) PM2000 System 특징과 기능
① 완벽한 네트워크 접속성
성능과 진동 정보의 통합은 매우 획기적인 시도로서 Bently Nevada사의 기계 진단 부문에서 적용하고 있는 방식이다. 성능과 진동 데이터를 연관하여 경향을 파악하는 기능을 가진 기계 진단 시스템의 구현은 보다 정확한 분석을 가능케 한다. 이는 PM2000과 DM2000 사이의 NetDDE Interface를 이용한 데이터 교환을 통해 이루어지며 PM2000은 DM2000으로부터 열역학적 성능 변수를 계산하는데 필요한 모든 공정 변수들을 수집한다. PM2000에 포함된 DDE Server는 오직 이러한 Communication Link 용으로만 발전된 것이며 다른 DM2000 DDE Server는 별도로 사용할 수 있다. 이는 DM2000과 사용자의 컴퓨터 시스템간의 DDE Communication 용으로 사용될 수 있다. DDE Server는 PM2000과 함께 작업 가능하며 NetDDE Interface를 통해 DM2000은 PM2000으로부터 성능 정보를 수집할 수 있다.
② 데이터 접근성
PM2000은 Server 및 디스플레이 소프트웨어와 사용이 가능하다. Server 소프트웨어는 환경 구성 기능, 데이터 수집 기능, 계산 및 디스플레이 기능을 포함한다. Server는 DDE를 거쳐 DM2000으로부터 데이터를 수집하는 소프트웨어로서 필수적인 것은 아니나 DM2000 데이터 수집 소프트웨어와 같이 동일 컴퓨터 상에 PM2000을 두는 것을 권고된다. 디스플레이 소프트웨어는 네트워크 상에 어떤 Node에서라도 Server 소프트웨어와 연결되며 디스플레이 컴퓨터는 모든 그래픽 디스플레이, 경향(Trend), 보고서를 사용할 수 있다. 이러한 모든 환경 구성상의 변화는 Server 컴퓨터에서 이루어진다. 원거리에 설치된 디스플레이 소프트웨어를 이용, 전화선이나 네트워크를 통해 Server에 접근하여 언제나 데이터를 볼 수 있다.
9.1.5 ADRE
ADRE® for Windows System
(1) 개요
현장에 설치되어 있는 중요 기계류의 경우 각종 변환기를 이용하여 24시간 데이터를 감시하고 이를 컴퓨터 시스템에 연결하여 관리하는 시스템 (Bently Nevada DM2000 System)이 널리 사용되고 있다. 또한 구름 요소 베어링을 사용하는 다수의 일반 설비류는 간단한 Portable 측정기나 온라인 방식으로 연결하여 주기적 전송 방식을 이용하여 경제적으로 시스템을 구성, 영구적으로 설치된 변환기로부터 전달되는 데이터를 관리하는 시스템 (Bently Nevada TM2000 System)이 적용된다.
이러한 시스템과는 별도로 기계 설비 분석 전문가들이 각종 현장에서 발생하는 설비 문제에 대해 고 품질의 분석 능력을 보유한 시스템을 활용하여 전문적인 분석을 가능하게 하는 시스템들이 현장에서 활용되고 있다. 이러한 시스템 중 대표적으로 가장 회전체 및 모든 기계류의 상태 분석에 적합하도록 고안되고 제작된 시스템이 Bently Nevada사의 “ADRE for Windows System”이다. ADRE for Windows (Automated Diagnostic for Rotating Equipment, 이하 ADRE) 시스템은 회전 기계류의 문제점을 해결하는데 있어 고도의 전문화된 생산적이며 정교한 도구로 최첨단 기술을 이용한 회전기계류 휴대용 진단장비이다.
(2) ADRE 시스템의 구성과 특징
이 시스템은 기본적으로 세 부분으로 구성되는 데 그 구성을 보면 각종 변환기 타입의 신호를 처리하고 이를 컴퓨터 시스템에 전달하는 208-P DAIU (Data Acquisition Interface Unit), 이를 각종 다양한 데이터 형태로 처리하고 실시간 디스플레이 및 저장 기능, 그리고 외부 장비와의 접속 기능을 가능하게 하는 기본 프로그램인 ADRE for Windows Software, 이러한 소프트웨어가 설치되어 이동 용이성을 기본으로 하는 일반 노트북 컴퓨터가 그 기본 구성이 된다. 자체적으로 오실로스코프(Oscilloscope), 스펙트럼 분석기(Spectrum Analyzer) 및 기록 장치 (Recording Instrument)의 특징과 기능을 가지고 있으며, 실시간 디스플레이(Real Time Display) 기능이 있어 데이터가 포착되는 동시에 이를 처리하여 볼 수 있다. ADRE는 User Interface가 Microsoft® Windows 그래픽 운영환경에 맞게 설계되어서 프로그램 사용이 매우 용이하다. Windows의 일반 기능을 활용하여 워드프로세서, 스프레드 쉬트, 그리고 그래픽 프로그램과 기타 윈도우즈 응용프로그램을 함께 사용할 수 있다. 이들 프로그램을 함께 사용하여 보고서 작성을 용이하게 할 수 있다. ADRE는 Steam 및 Gas Turbine, Electric Motor, Centrifugal And Screw Compressor, Vertical And Horizontal Pump, Turbogenerator Sets, Hydroturbine Generator Set, Turbo Expander, Ship Propulsion System, Aircraft Engine, Fan, Blower, Reciprocating Engine 및 Compressor 등 여러 가지 회전 기계로부터 데이터를 수집하여 분석 할 수 있다. 가볍고 크기가 소형인 노트북 컴퓨터를 사용하므로 Test Stand, Balancing Stand, Control Room, 그리고 시험실과 같은 현장에서 사용할 수 있다.
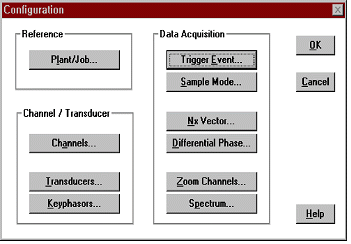
그림 6-44 ADRE 시스템의 구성
(3) ADRE 시스템 기능 및 이용 가능 데이터
일반 기계 관리 시스템과 마찬가지로 각종 기계 가동 상태를 통해 과도상태(Startup 또는 Coastdown) 및 정속 운전 상태 동안 16개 채널에서 동적(Dynamic) 진동 데이터를 동시에 샘플링하고 이를 DMA(Direct Memory Access) 방식을 통해 즉각 처리하게 된다. 이 기능들은 현장에서 분석 전문가가 필요로 하는 실시간 데이터 처리를 가능케 하는 것으로 매우 중요한 기능이 된다. ADRE® for Windows에서 구현 가능하며 각각의 운전 상태에서 데이터를 취득하여 진단 전문가에게 필요한 데이터를 얻을 수 있다. 진단 전문가가 데이터를 분석할 때 스펙트럼 해상도는 필요에 따라서 50, 100, 200 또는 400라인으로 선택 가능하며 고해상도가 필요한 경우에는 3200라인 해상도 구현이 가능하다. English 및 Metric 단위 등 자신에게 친숙한 단위를 사용하여서 데이터를 볼 수 있으며, peak-to-peak, zero-to-peak, rms, 그리고 적분기능이 있다. 동시에 1×, 2×, 그리고 n× 필터링된 벡터(진폭과 위상) 제공이 가능하다.
DAIU는 대부분의 일반 변환기의 동적 신호 출력으로부터의 입력값뿐만 아니라, 진동 변환기로부터 변위, 속도 그리고 가속도 진동값을 받아 들일 수 있다. 온도, 압력, 부하 등의 공정 데이터 값도 입력받아서 기계 문제를 분석하는데 이용할 수 있다. 8 또는 16 채널로 동시에 데이터 수집할 수 있으며 채널 당 1280개의 벡터 샘플 및 128개의 Waveform 샘플을 할 수 있다. 샘플링한 데이터를 이용, Orbit, Spectrum, Full Spectrum, Timebase, Cascade, Waterfall, Shaft Average Centerline, Bode, Polar, Trend, X-Y Plot 등의 다양한 데이터 형식을 이용하여 진단에 이용하게 된다.
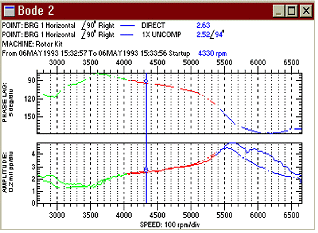
그림 6-45 ADRE 시스템에 나타난 Bode Plot
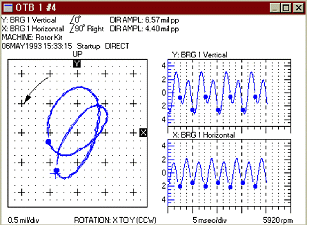
그림 6-46 ADRE 시스템에 나타난 Orbit과 Waveform
9.1.6 3300 시리즈 감시장치
3300 Series Monitoring System
(1) 개요
1989년에 발표되어 현재까지 사용되고 있는 중요 기계류의 온라인 진동 감시 시스템으로 가장 널리 사용되는 Bently Nevada사의 제품이다. 제품 발표이후에 큰 호응을 얻어서 상업적으로 상당히 큰 성공을 거둔 제품으로 현재까지도 많은 신규 프로젝트에서 가장 많이 설치되는 제품이다. 주된 적용 대상 기계는 일반적으로 중요 기계로 분류되는 터빈/발전기, 산업용 공기압축기, 대형 펌프, 왕복동형 기계류 등에 설치되는 경우가 많지만, 필수 기계로 분류되는 중대형 전동기나 중대형 펌프 등에도 이용된다.
3300 모니터링 시스템은 기존의 모니터링 시스템과 비교할 때 다음과 같은 특징을 가지고 있다.
• Microprocessor가 시스템 동작의 근간이 되는 타입으로 자체 진단 기능을 통하여 신뢰성을 향상시켰으며, 기존의 가동 코일형이 아닌 액정(LCD) 방식으로 지시치를 나타낸다.
• 많은 모니터링 옵션 사항을 Plug-in Jumper를 이용하여 현장에서 쉽게 변경, 재 설정할 수 있다. 현장에서 변경 가능한 옵션은 Monitor Full-scale, Transducer Type, Timed OK/Channel Defeat, Recorder Output, First Out, Alarm Time Delay, Danger Voting Logic, Common Relays, Normally Energized/De-Energized Relay Operation, Latching/Nonlatching Monitor Alarm Mode, Latching/Nonlatching OK Function, Upscale Towards/Away from Probe, Filter Options등이 있다. 예를 들면, 제품 구매 당시에 제품의 사양이 명확하지 않아서 Full-scale이 5 mils pp인 제품을 구매한 경우, 어떠한 이유로 Full-scale을 10 mils pp로 (예를 들면 Alarm 설정치가 7 mils pp인 경우) 바꾸어야 하는 상황이 발생한다면, 기존 제품은 신품을 다시 구매하여야만 하였으나, 이 제품은 현장에서 간단하게 Jumper를 조작하는 것으로 변경할 수 있다.
• API (American Petroleum Institute, 미국 석유 화학 협회) 670과 678 기준을 완전히 충족한다.
(2) 3300 모니터링 시스템 구성
3300 모니터링 시스템은 현장에 영구적으로 설치되어있는 각종 변환기 (진동, 위치 정보, 공정 변수 등)와 변환기로부터 전해지는 연속적인 데이터를 해당 모니터에 연결시켜주는 System Cable, 그리고 모니터링 환경을 제공하는 Rack, 전원 공급 장치(Power Supply), System Monitor와 각각의 목적에 적합한 모니터로 구성되어 있다. 아래는 Proximity Probe를 사용하는 경우의 대표적인 구성 형태이다.

그림 6-47 Bently Nevada 3300 Monitoring System
① 변환기 (Transducer) : 진동 또는 위치 등 측정하고자 하는 변수를 전기적인 신호로 변환하는 소자를 말한다. 일반적으로 진동의 변환기로는 변위 변환기 (Proximity Probe System), 속도 변환기 (Velocity Seismoprobe), 가속도 변환기 (Accelerometer)의 세 가지가 이용되나, 이외에도 온도 등 다른 변환기나, 변형된 형태의 다양한 변환기가 감시하고자 하는 변수에 따라 적용된다. 그림 6-48은 Turbine Generator에 설치되는 전형적인 구성이다.
② Field Wiring : 변환기 시스템과 모니터링 시스템을 연결하여 주는 케이블로 변환기의 종류에 따라 2 Wire나 3 Wire 케이블이 이용된다. 노이즈 방지를 위하여 차폐(Shield) 선이 있는 종류의 Cable 사용이 권고되며, 400V 이하의 Cable과 함께 포설 되어야 한다. 일반적인 최대 허용 길이는 300m이다.
③ 3300 모니터 시스템 : 3300 모니터 시스템은 전체적인 껍데기인 Rack, 전원 공급 장치 (Power Supply), System Monitor, 해당 감시 모니터로 구성된다. Rack은 4개의 모듈이 설치될 수 있는 것부터 14개의 모듈이 설치될 수 있는 종류가 있다. 전원 장치는 Rack의 가장 왼쪽에 설치되는 모듈이며, 외부 전원을 인가 받아 다른 모니터 모듈과 변환기 시스템에 필요한 전원을 공급한다. System Monitor는 전원 장치 다음 위치(왼쪽에서 두 번째)에 위치하며, 모니터 시스템이 공통적으로 하여야 할 작업을 진행한다. 즉 예를 들면, 시스템 Reset 기능을 제공하며, 전원 장치의 이상 여부를 감지한다. 이외에 경보 값의 조정 및 여러 작업을 진행하며, 공정용 컴퓨터 (DCS 혹은 PLC)에 상태 데이터를 제공할 수 있는 카드(SDI, Serial Data Interface)와 진동 관리 시스템 (예를 들면 DM2000 시스템)에 필요한 데이터를 제공하는 카드 (DDI, Dynamic Data Interface)가 옵션으로 설치될 수 있다. 그 이후의 Monitor는 감시 목적과 환경에 따라 다양하게 구성될 수 있으며, 3300 모니터 시스템의 경우 감시 목적에 따라 약 20 여개의 모듈 종류가 있다.
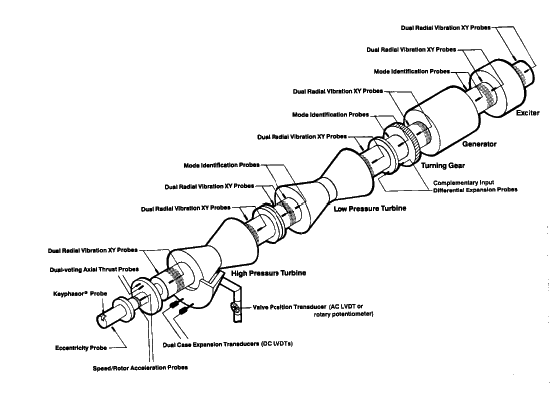
그림 6-48 터빈 발전기에 설치된 진동 변위 변환기
(3) 시스템의 특징과 기능
상업적으로 큰 성공을 거둔 제품이며, 목적과 시장 상황에 따라 다양한 제품이 존재한다. 대부분의 모니터링 시스템이 제공하는 현재 변수의 값 지시, 설정된 경보 치에 따른 경보 발생, 경보 발생에 따른 릴레이 구동, 레코더 Output 값 출력, 정밀 측정 장비와의 연계를 위한 Buffered Output 출력을 기본적으로 제공한다. 경보 릴레이는 기계를 정지시킬 수 있는 Trip Logic에 연결되어 특정한 기계 문제점의 발생 시에 기계의 파손이 심하지 않은 상태에서 안전하게 정지시킬 수 있도록 대부분 구성되어 진다.
국내에서 가장 많이 사용되고 있는 제품이므로, 신뢰성은 인정을 받았다고 볼 수 있다. 하지만, 제품의 옵션을 바꾸기 위하여 제품 Board를 만질 경우, 정전기에 의한 고장이 발생할 가능성이 있으므로 정전기 방지용 Kit의 착용이 반드시 요구된다. 기계적인 문제가 발생하였을 경우, 문제점의 원인에 대한 파악은 어려우므로, Computer를 근간으로 하는 데이터 수집 및 관리 시스템에 연결되는 것이 근래의 추세이다.
9.1.7 3500 시리즈 감시장치
3500 Series Monitoring System
(1) 개요
기존의 3300 모니터링 시스템을 대체하는 것이 아니라 디스플레이 방식과 모니터 설정 및 기능이 달라진 제품으로 위와 마찬가지로 90년대 중반 Bently Nevada사 에서 출시한 가장 최근의 감시 시스템이다.
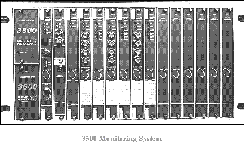
그림 6-49 3500 Monitoring System
시스템의 각종 기능들이 기존의 제품과 같이 하드웨어적인 설정이 아닌 소프트웨어를 이용하여 조절 가능하며, 하나의 모니터 모듈이 이러한 과정을 통해 최대 네 가지 종류의 다른 모니터 모듈 타입으로 설정되어 이용 가능하다.
마이크로프로세서 첨단 기술을 이용하여 설계한 3500 시스템은 기계를 보호하기 위한 충분한 기능을 갖춘 감시 시스템으로서, 아래와 같은 특징을 가지고 있다.
• 설치비와 유지 보수비 절감
• 개선된 운전자 정보
• 공장 제어 컴퓨터로의 통합 능력 개선
• 신뢰성 향상
(2) 3500 Monitoring System 구성
시스템은 현장 있는 각종 기계류에 설치되는 변환기 시스템, 그리고 이들 변환기로부터 얻어지는 데이터 신호를 받아들이는 3500 Monitor Rack이 있으며, 각 Monitor Rack에 대한 환경 설정(Configuration)과 디스플레이를 해줄 소프트웨어를 포함하는 컴퓨터 시스템으로 구성된다. 변환기로는 일반적으로 저널 베어링에 적용하는 변위 센서(Proximity Probe) 뿐만 아니라 볼 베어링 타입의 구름 요소 베어링에 적용하는 속도 센서, 가속도 센서 그리고 베어링의 온도를 검출하는 일반 온도 센서 모두를 포함한다. Monitor Rack을 구성하는 것으로는 이중 전원 공급 장치, 컴퓨터 시스템과의 인터페이스를 위한 모듈을 기본으로, 진동, 축의 위치, Over Speed Protection, 온도 등의 모듈이 있다.
3500 Monitoring System에서 이용할 수 있는 소프트웨어 패키지는 Data Acquisition, Rack Configuration, Operator Display가 있다. 모든 소프트웨어 모듈은 Windows 시스템을 근간으로 하고, Windows for Workgroup 또는 Windows95를 이용, 네트워크 상에서 운영할 수 있다. 그리고 전용 디스플레이 Monitor가 개발되어 사용되고 있다.
(3) 시스템의 특징과 기능
3500 시스템은 싱글, 멀티 커넥터를 사용해 진동 신호를 변환기 단자로부터 3500 Monitor까지 전달하므로 케이블 설치비용을 절감할 수 있고 기존의 Bently Nevada 제품과 호환이 가능하며, 사용이 용이하도록 그래픽 소프트웨어를 이용하여 환경 설정을 하도록 되어 있다. 유지 보수비용 면에서는 몇 가지 다른 기능을 하나의 모듈에서 할 수 있으므로 Spare Part 관련 비용을 절감할 수 있다. 모니터에 RS232/ RS422 방식을 통하여 직접 환경을 설정하거나 감시 기능 구현이 가능하며, 만일 공장 내에 자체 네트웍 망이 구축되어 있을 경우 이를 이용, 어디에서나 모니터링이 가능하도록 되어 있다. 또한 선택적으로 내부 Modem을 통하여 공장내에서 뿐만 아니라 그 밖의 어느 곳에서라도 Dial 접속이 가능한 경우 환경 설정 변경은 물론 데이터를 보는 것도 가능하다.
3500 시스템은 운전 정보(Operation Information)를 개선하고 그 정보를 운전자가 해석 용이하게 설계되었으며, 다음과 같은 특징이 있다.
• 전체 진폭(Overall Amplitude), Probe Gap Voltage, 1× 진폭과 위상 각, 2× 진폭과 위상각, Not 1× 진폭 등의 데이터 제공
• 3500 Operator Display Software : Microsoft® Windows를 기준으로 타 시스템과의 연계를 위한 Ethernet Network 가능. TCP/IP , FTP(File Transfer Protocol) 그리고 X-Windows Protocol를 지원하는 능력 보유.
• Server/Client의 구성
3500 시스템은 Modbus® 프로토콜을 지원하는 Communication Gateway를 사용해 공장 컴퓨터와 분산 제어 시스템(Distributed Control System : DCS)과 통신이 가능하다. 그리고 한 대의 3500 Rack은 다른 프로토콜을 이용하여 데이터를 DCS와 비용이 저렴한 원거리 디스플레이로 동시에 제공한다. 이를 통해 공정 변화를 기계 진동과 서로 관련시켜 기계 관리가 가능해진다.
이 시스템은 3500 Rack에 대한 이중 전원 공급 장치가 가능하여 갑작스런 전원 부분에 대한 문제 발생시에도 자동으로 다른 전원 장치로 대체하여 계속적으로 모니터링을 할 수가 있다. 중요 기계에 적용되는 진동 감시 시스템은 기계의 이상 진동 발생시에 기계를 보호하기 위하여 해당 Relay를 동작시켜 Alarm이나 기계를 자동적으로 정지시킬 수 있는 Trip 기능을 가지고 있으므로 시스템 동작에 대한 신뢰가 중요시된다. 따라서 3중화된 보완 단계(Triple Modular Redundant: TMR)를 걸쳐 최종적으로 Relay가 동작되도록 구성되어 있고 이는 해당 변환기에서부터 모니터, Relay까지 ‘Two out of Three’ 옵션을 통해 시스템 자체의 문제로 인한 오 동작으로 기계 Trip 현상이 발생하는 것을 방지하게 된다.
그밖에 Full Scale Range, Transducer Input, Recorder Output, Alarm Time Delay, Alarm Voting Logic, Relay Configuration 등과 같은 모든 모니터 옵션을 소프트웨어로 현장에서 조정할 수 있도록 되어 있다.
9.2 Bruel & Kjaer사의 기계관리 시스템
Machinery Management System of Brul & Kjaer
9.2.1 COMPASS (Computerized Prediction Analysis & Safety System)
소음 진동 계측기 분야에서 50여년의 기술력과 경험을 가진 Bruel & Kjaer사에서 설비 상태의 감시 및 설비 이상을 예방, 예측할 수 있는 Compass라는 시스템이 개발되었다.
이 시스템은 영구적으로 센서를 설치하여 설비를 감시하는 On-Line 시스템과, 휴대용 Data Collector를 이용하여 설비 감시를 수행하는 Off-Line 시스템을 통합하여 효율성과 경제성을 동시에 만족하도록 하였다. 특히 이 시스템은 설비의 여러 가지 운전 상태에 따라 적합한 감시 전략을 변화 시킬 수 있는 Adaptive Monitoring 능력을 갖추고 있으며, 더불어 첨단의 DSP(Digital Signal Processing)으로 시스템을 동작시키며, 여러 가지 설비 고장을 자동적으로 진단할 수 있는 인공 지능의 전문가 시스템을 구축하고 있다.
아울러 이 시스템은 최근 산업 현장에서 표준으로 사용하고 있는 Ethernet (TCP/IP), UNIX, X-Window, Mofit 그리고 Postscript 등과 같은 질 높은 산업 표준들을 사용하고 있다.
이 시스템의 최대 장점은 사용자가 현장의 특성이나, 설비의 특성에 맞는 적절한 SET-UP을 가변하여 설정할 수 있게 설계되어져 설비 감시 시스템으로써의 극대의 효과를 창출할 수 있게 하였다.
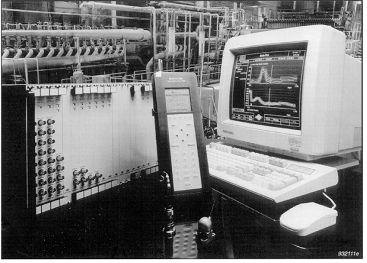
그림 6-50 Bruel & Kjaer사의 COMPASS 기계관리 시스템
(1) 특징
• Compass는 Critical 설비의 갑작스런 돌발 고장에 대하여 Shutdown Relay 동작 및 알람 경보 신호 등을 통한 보호 감시(Protection Monitoring) 기능을 수행한다.
• Compass는 진동 및 설비 Parameter 신호의 자동 측정 및 컴퓨터를 통한 데이터의 저장 및 분석을 자동으로 수행한다.
• Compass는 On-Line과 Off-Line, 연속 감시와 불연속 감시를 동일한 하드웨어와 소프트웨어로써 처리, 분석, Display한다.
• Compass는 기존에 설치된 감시시스템에 Upgrading하여 진보된 설비 감시시스템을 구현할 수 있다.
• Compass는 DCS(Distributed Control System) 등에 데이터를 제공함으로써 공장 자동화 및 설비 전산화에 체계화된 설비 감시 Parameter를 제공한다.
• Compass는 LAN(Ethernet) 통신을 이용한 Multi-User, Multi-Tasking을 수행함으로써 설비 감시에 관련된 여러 전문가들이 동시에 설비 상태의 분석 및 진단을 수행할 수 있는 데이터를 제공한다.
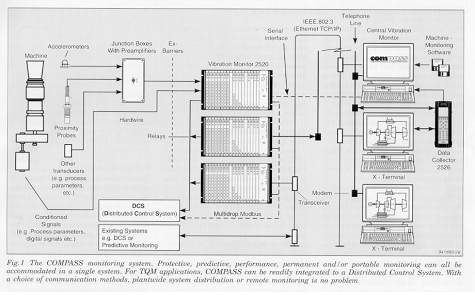
그림 6-51 COMPASS Monitoring System
• Compass는 먼거리에 여러 개의 공장을 가지고있는 User들이 데이터의 상호 교환 및 진단이 가능하도록 WAN(Wild Area Network) 통신으로 구축될 수 있다.
• Compass는 다음과 같이 전세계적으로 광범위하게 통용되는 산업 표준 및 국제 규약에 의하여 설계되었다.
– UNIX, Ethernet, TCP/IP, Motif, X-Window System, DSP
– API 670, CENELEC(CE), ISO 9001
(2) 하드웨어 기능
• 각 측정점의 개별적인 적용을 신축적으로 수행하기 위해, 아울러 쉽게 측정점의 확장을 위해 각각의 Processing Card는 Module화 되어 설계되었다.
• rpm의 증감에 따른 진동 및 Parameter의 기준 값을 설정하여 변화된 rpm에 따른 가변화된 경보값을 설정할 수 있게 설계되었다.
• 기계의 운전상태의 변화(Stop, Turning, Run-Up, Running, Coast-Down)에 따라 자동적으로 설비의 상태 감시에 적합한 감시 시스템이 운용되게 설계되었다.
• 진동값의 변화에 따른 진동 주파수 분석 데이터와 설비의 Parameter의 변화를 연동하여 설비에 가장 적합한 운전 상태 및 설비 효율을 밝혀낼 수 있게 설계되었다.
• Internal, External Trigger를 이용하여 불안정한 운전 상태에서의 진동 크기의 가변 요소에서 일정하게 유지되는 안정된 진동값 만을 Monitoring하여 설비 감시의 일관성을 유지할 수 있게 설계되었다.
• 첨단의 DSP(Digital Signal Processing) 기법을 제공하여 효율적인 감시시스템을 구축하였다.
• 감시 기계의 보호 및 User가 설비 상태의 인지를 쉽게 하기 위하여 Trip Relay, Alarm Relay 및 Machine State Relay를 자동적으로 조작되도록 설계되었다.
• 시스템 자체의 에러나 손상에서 시스템을 보호하기 위해 Self-Test, Overload Protection, Automatic Start-Up 등의 자기 진단 및 보호 시스템이 가동되도록 설계되었다.
• Data Collection, Field Balancing, Bandpass, Spectrum(CPB, FFT & SED) 그리고 Cepstrum 등의 기능을 갖춘 초경량, High Quality 휴대용 Data Collector를 Compass의 부분 시스템으로 사용할 수 있게 설계되어 On-Line과 Off-Line으로 구별하여 감시되야할 전 공장의 전 설비를 하나의 Compass 시스템으로 통합하여 관리할 수 있게 설계되었다.
• 모든 종류의 Proximity Probe, Accelerometer, Velocity Probe 등과 같은 진동을 측정하는 센서와 Pressure, Temperature Probe, Tachometer 및 모든 Process Parameter 신호들을 처리할 수 있도록 설계되었다.
(3) 소프트웨어 기능
• User가 설비의 상태를 인식하기 쉬운 신호등 색으로 설비 상태를 표시한다.
– 붉은색 : Danger 상태
– 노란색 : Alert 상태
– 초록색 : 정상 상태
– 파란색 : System Alarm
• Machine Group, Machine, Machine Part 그리고 Channel 등으로 측정 Point를 단계적으로 배열함으로써 사용자가 원하는 측정점을 찿아가는데 용이하다.
• Alarm Directory를 통해 설비 이상의 측정점, 설비 상태, 측정 Parameter, 경고 시간, 경고 Level, 그리고 User의 인식 여부 등을 알아볼 수 있다.
• 설비의 감시 Level에 따라 Basic Monitoring, General Purpose Monitoring, Rolling-Element & Gear Monitoring, Transient Monitoring, Shaft Monitoring, Machine Diagnosis Monitoring 그리고 Basic Performance Monitoring 소프트웨어로 단계적으로 적용할 수 있게 모듈화되어 있다.
• 진동의 FFT, CPB 주파수 분석을 통한 기계 고장의 분석 및 Cepstrum, Envelope Spectrum 분석을 통한 Gear 및 베어링의 상태 분석 및 진단을 용이하게 하였다.
• 설비 상태의 경향관리를 위해 진동의 Overall 값 및 Eccentricity, Thrust Position & Load, Valve Position, Casing Expansion, Differential Expansion 등과 같은 Scalar 값의 경향을 최소 0.1초에서 최대 30년까지 10단계로 분리하여 Display 및 저장함으로써 사용자가 쉽게 설비 상태의 경향을 확인할 수 있다.
• Turbine이나 Compressor 등과 같은 rpm의 변화에 따른 효과적인 설비 상태의 변화를 체계적으로 수행해야 하는 Critical 설비의 Run-Up & Coast-Down에서의 Polar Plot, Bode Plot, Waterfall Spectrum 등과 같은 Transient Monitoring 기능을 가지고 있다.
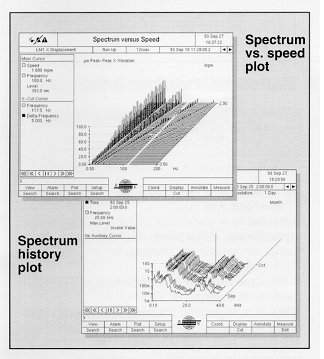
그림 6-52 Waterfall과 Cascade Plot
• Shaft의 감시가 필요한 Critical 기계에 대하여 Orbit Plot, Acceptable Zone 등과 같은 Shaft Monitoring 기능을 가지고 있다.
• 자동적으로 기계의 고장을 진단할 수 있는 Machine Diagnosis 소프트웨어를 채택함으로써 사용자로하여금 설비의 이상 판단을 확신할 수 있는 데이터를 제공하여 준다.
• 소프트웨어의 사용은 단계적으로 사용자를 제한할 수 있는 Protection Password를 제공함으로써 Set-Up의 변경 및 중요 데이터의 사용에 제한을 주고 있다.
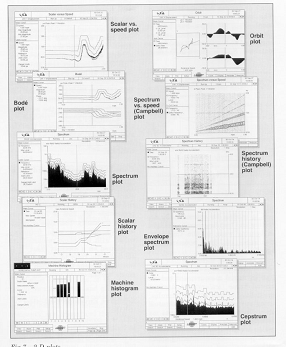
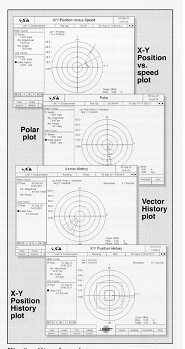
그림 6-53 각종 진동 Plot
9.3 Entek-IRD사의 기계관리 시스템
Machinery Management System of EntekIRD International Corp.
EntekIRD사는 플랜트의 부하 감소 또는 Shutdown을 일으킬 수 있는 Main Turbine, Generator, Boiler Feed Pump, Circulating Pump, Draft Fan 그리고 Pulverizer/Exhauster 등과 같은 중요하고 핵심적인 회전 기계 설비에서부터 각종 보조 기계 설비에 이르기까지 무수히 많은 종류의 다양한 회전 기계를 정확히 감시 측정 관리하는 휴대용 장비와 온라인 감시 시스템 및 Software를 제작 개발하였으며, 특히 Software의 개발은 하루하루가 다르게 변화하고 있는 세계적인 추세에 따라 개발 연구하고 있다. EntekIRD사는 CSI, SKF, Hewlett-Packard, Schenck, TEC 등과 같은 세계의 여러 대표적인 예측 정비 장비 회사들이 생산하고 있는 장비들과 호환성을 갖도록 Software를 개발해 왔으며, 특히 기계의 Oil 분석 장비 및 Thermography의 Data들을 진동 Data와 연계하여 종합 집합적인 관리가 가능한 PM Integrated Software를 개발하여 더욱 다양한 정보를 PM 실무자들에게 제공할 수 있게 되었다.
EntekIRD에서 생산하고 있는 종류들을 간단히 언급하면 휴대용 장비로는 진동 측정기(Model 810, Model 808….), 진동 분석기(Model 838, 870, 885), 진동 Data Collector/분석기 (dataline DSP, dataline IS, dataPAC 1250, 1500), 다채널 진동 분석 장비인 TURBOTEST이 있다. 온라인 장비로는 Machinery Protection 장비로 5800 Series의 Monitoring System, Two Wire System, 6600 Series의 Monitoring System, 그리고 IMP/VIMP System이 있고Computerized Monitoring System으로는M-Pulse System, EMONITOR On-Line System, 그리고 Turbomonitor System 등이 있으며, Software로는 EMONITOR for Window, EMONITOR Odyssey, ESHAPE, MOTORMONITOR, Explore-EX 등이 있다. 또한 여러 가지 크기의 Balancing Machine 등의 생산과 아울러 Displacement Transducer (Non Contact Pickups : Model 403 Series, Model 1900 Series), 여러 종류의Velocity Transducer, Accelerometer등과 같은 Vibration Sensor들 그리고 휴대용 장비와 사용하는 몇몇의 Temperature Transducer들을 제작 생산하고 있으며 Transducer제작 전문 회사인 Wilcoxon, IMI 등과 같은 회사에서 생산되는 Transducer를 사용할 수도 있다. 그리고 최근 2년 전에 Diagnetics라는 Oil 분석 장비를 생산하는 회사를 인수하였고, 조만 간에 Thermal Image 장비도 생산할 계획으로 세계 제일의 총체적인 PM장비 생산 회사로 발 돋음 하려 하고 있다.
앞에서 언급된 바와 같이 플랜트에 있는 많은 다양한 기계 설비들을 보호하고 그 수명을 최대한 연장하여 그 기계에 대한 경제성을 극대화하도록 하기 위해 기계에 따라 그 중요도를 나누고 온라인을 설치할 것과 휴대용 장비를 이용하여 관리할 것을 적당하게 분배를 하여 하나의 Software를 이용하여 개인용 컴퓨터로 Data를 관리하고, 뿐만 아니라 기계와 관련한 각종 정보 즉 Oil, Thermal Image, 온도, 압력, Flow등등의 Data를 수집 통합 관리할 수 있다.
다음에서 소개하고자 하는 내용은 앞에서 나열한 몇 가지의 휴대용 진동 장비와 온라인 장비 그리고 진동 Software에 대해서 간략하게 설명 하고자 한다.
9.3.1 dataline DSP
이 장비는 예지 정비와 기계 진동 진단을 위한 휴대용 Data Collector이다. 이것은 실무자로 하여금 주기적인 일정에 따라 Magnitude, Process, Spectrum, Time Waveform, 그리고 Phase Data를 플랜트에서 운전 중인 각종 회전 기계로부터 Data를 취득할 수 있도록 한다. 실무자들은 List에 정의되어 있는 위치에 대하여, 또는 List에 정의되어 있지 않은 위치에 대한 Data를 취득할 수 있다. 최근에 대부분의 진동 분석기들은 과거와는 달리 장비가 소형화, 경량화 그리고 다기능화 되어 가고 있으며, 특히 장비가 작고 가볍기 때문에 진동 분석기가 Data Collector 기능까지 함께 수행할 수 있도록 개발되었다.
(1) 특징
• 특허권이 있는 Pathfinder 기능 – 이것은 전 공장의 Database를 구축하고1998년 8월 10일서 측정을 할 때 일반적인 타 장비는 Database가 구축되어있는 순서로 Data를 취득해야만 그 Data를 보관, 관리할 수가 있다. 즉, 이 의미는 사용자가 현장을 상당히 많이 이동해야 한다는 점을 의미한다. 그러나 이 Pathfinder 기능은 Database 구축순이 아니라 사용자가 측정하고자 하는 기계들만 측정을 수행할 수 있게 하는 기능이다.
• Envelope Spectrum Processing (ESP) – Rolling Element Bearing들에서 고장을 정확하게 분석할 수 있는 매우 유용한 고도의 기술이다.
• Cold Cathode 형광 Backlit Display – 휴대용 장비를 위하여 매우 밝고 선명한 Display Technology 이다.
• Machine List, 취득 된 Data 그리고 Application Program들에 대한 최대한의 저장을 위해 ECARD PCMCIA Type II Card로 구성되어 있다.
• 방수성과 내구성의 기준이 되는 IP65로 제작되어져 있다.
• 현장에서 장비 작동 시간을 최대한 연장하기 위하여 최적의 조건으로 제작된 전원 소비 체계를 고려하여 Battery가 고안되어 졌다.
• 현장에서 용이하게 사용할 수 있게 하기 위하여 작은 크기, 가벼운 무게 그리고 양손을 사용할 수 있도록 설계되어 있다.
• 빠르고 간단한 Data 취득을 위하여 고속의 Processing과 Graphical User Interface가 내장되어 있다.
• EntekIRD사의 진동 관리 및 분석용 Software인 EMONITOR Series와 회전 기계의 Modal 분석을 위한 ESHAPE for Window 그리고 Motor를 정밀 분석할 수 있도록 정보를 제공하는 MOTORMONITOR라는Software와 연계하여 사용할 수 있도록 설계 제작되었다.
나. 기능
① Data Collector Diagram과 기능
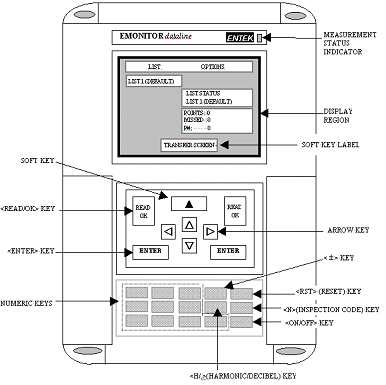
그림 6-54 Data Collector Diagram
Measurement Status Indicator | Data를 취득하는 동안에 측정되는 상태를 적색, 주황색, 녹색으로 나타난다. |
Soft Key Label | Soft Key를 위한 정의를 나타내고, Soft Key의 역할은 dataline의 현 상태에 의거하여 변경된다. |
Data Collector Hardware Connector | Serial Port Connector, Power Connector, E-Card Slot, EXT TRIG Connector, Input Connector가 Dataline 상단 부위에 위치해 있다. |
• 입력 가능한 Sensor Type으로는 ICP Accelerometer, 3방향 Accelerometer, 2중 출력 가속도/속도 Transducer, 속도 Transducer, 변위 Transducer, 적외선 온도 Sensor, 기 설치된 진동 감시 장치, 수동 Keypad 입력, 위상 Reference TTL/CMOS Trigger or Analog Trigger, Trigger Reference로부터 rpm 측정
• 측정 가능한 운전변수로는 가속도, 속도, 변위, Envelope Signal Processing (ESP), 위상, 회전수, 온도, 압력, 유속, 선형 변위, Count and Count Rate, 전압, 전류, 정적, 동적 사용자가 정의한 측정 단위 형태가 가능하다.
• Trigger 입력에 있어 그 Source로는 Internal 또는 External이 가능하며, 입력 가능한Type으로는 TTL 또는 Analog Level이 있다.
• 측정 가능한 Type으로는 Overall값, Time Waveform, Spectrum (FFT Spectrum), 위상값, Spectrum Bands (10), 그리고 Order Normalized Spectrum등이 측정 가능하다.
9.3.2 dataPAC 1500 (Portable Analyzer/Balancer/Data Collector)
dataPAC1500은 발전소, 석유 화학 공장, 펄프/제지 공장, 제철 공장과 같은 많은 공정을 필요로 하는 산업에서 설비의 상태를 파악할 수 있도록 작고 가볍게 고안한 완벽한 기능을 갖춘 장비이다. 일반적으로 고가의 장비에서 볼 수 있는 True Zoom기능을 가지고 있으며 사용하기 매우 용이하게 설계된 장비이다. 타 장비에 비해 상당히 넓은 주파수 범위(10 cpm~4,518,000 cpm)를 갖추고 있고, 또한 Screen Capture기능이 있어 화면에 있는 그림을 Print가 가능하다.
장비 Data 수집 및 진동 분석뿐만 아니라 자체에 Balancing Program을 내장하고 있어 임의의 Data를 입력하면 자동적으로 계산하여 Balancing을 수행할 수 있도록 Data를 제공하여 준다. 이 장비는 Data Collector로서 보다는 진동 분석을 수행함에 있어 보다 다양한 기능을 갖도록 함으로써 진동 신호를 다양한 정보로 만들어 실무자에게 전달할 수 있다.
즉, Data 수집보다는 현장에서 이상 징후의 기계류에 대해 다양한 분석 기능들을 사용하여 어떠한 원인으로 기계들의 문제점이 발생하였는지 여부를 판단할 수 있는 분석 기능들을 사용자에게 제공하며, Frequency Response Function기능을 추가하므로 하여 Impact Hammer를 이용한 갖가지 실험을 통하여 기계에 대해 여러 가지 상황을 파악 할 수 있다.
Data Collector의 기능으로써도 타 장비에 비해 전혀 손색이 없고 오히려 Data 취득 및 PCMCIA Card를 이용함으로써 저장 능력 또한 뛰어나다. 그리고 휴대 장비를 이용한 이러한 System 체계는 매우 효율적일 수 있으므로 실무자나 예산 입안자는 고려해 볼 만하다. 플랜트의 수많은 기계들에 Transducer를 영구적으로 설치하여 온라인화 한다는 것은 매우 많은 비용이 소요되므로 하나의 System 체계에서 온라인과 Data Collector와 같은 휴대 장비를 이용하여 하나의 Software로 관리를 한다면 몇 십분의 일에 불과 하는 최소한의 비용으로 수천 Point 이상을 관리할 수 있을 것이다.
온라인 Help 기능으로 장비 체계가 운용됨으로써 최소한의 교육으로 쉽게 장비의 모든 기능을 사용할 수 있고, VGA-Resolution 화면으로 되어 있어 화면에 나오는 모든 정보를 읽기 편하다.
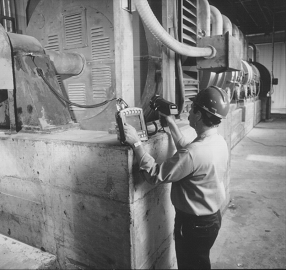
그림 6-55 dataPAC 1500 사용 모습
(1) dataPAC 1500의 특징
• 광범위한 주파수 대역의 분석과 True Zoom 측정은 10 cpm~4,518,000 cpm의 주파수 범위를 12,800 line의 표준 FFT 그리고 3,600,000 cpm까지의 범위를 True Zoom을 할 수가 있다.
• Startup/Coast Down의 기능으로 인한 Transient 조건하에서도 Data 수집이 가능하다.
• 현장에서 Strobe Light 또는 PhotoTach(또는 LaserTach)라는 Accessory를 이용하여 Field에서 One 또는 Two-plane Balancing이 가능하다.
• 18 Bit A/D Converter를 사용함으로써 분해능이 상당히 탁월하다.
• 6가지의 High Pass Filter를 선택할 수 있는 Spike Energy Spectrum™은 플랜트에서 고주파 성분을 갖는 각종 기계의Gear나 Rolling Element Bearing의 문제점들을 용이하게 파악 할 수 있는 기능을 가지고 있다.
• Frequency Response Function(FRF) 기능은 진동 분석에 대하여 정확도 및 정밀성을 한층 더 높이기 위하여 회전 기계의 고유 주파수를 결정할 수 있도록 하는 기능이다.
• 각종 Analysis 기능
– Time/Spectrum Display
Dual Display Format의 기능을 이용하여 Time/ Spectrum Data를 실제 진동 Signal을 그대로 처리 진행함으로써 진동에 따라 Data의 변함 정도가 실제적으로 변화되고 있는 상황을 볼 수 있다.
– True Zoom Spectrum
– Phase/Magnitude/Speed Display
Phase, Magnitude 그리고 Speed Data에 대한 매우 신속하게 처리되는 Polar Display
– Strobe 기능을 이용하여 다음과 같은 내용을 할 수 있다.
․ Speed 측정, Slow Motion에 관한 관찰, Balancing
․ Phase에 대한 관찰
․ Tuned filter, Synchronous studies
– Buried Shaft Triggering
․ Ratio에 근거한 Internal Shaft에서 External Shaft까지 Trigger Pulse를 지원한다.
․ Powerful Gearbox Analysis Tool 지원
– Startup/Coastdown 분석
․ Critical Speeds 판단
․ Resonance에서 반응에 대한 측정
․ Speed Changes 측정
나. dataPAC 1500의 기능
dataPAC 1500에서 입력 가능한 Sensor Type은 Accelerometer, Velocity Sensor, Displacement Probe, Temperature Probe, Photocells, Electromagnetic Transducer, Lasertach 등등 매우 다양하며 Transducer들의 Bias Voltage Check 및 Calibration Check 등을 통하여 Self-Test가 가능하다.
Data를 분석할 때 Spectrum의 해상도는 전자 부품 및 Software의 혁신적인 발전으로 인하여 이를 장비에 도입함으로써 12,800 Line의 고해상도를 선택할 수 있으며, GSE Corner Frequency는 각각 100, 200, 500, 1000, 2000, 5000 Hz를 선택할 수 있을 뿐만 아니라 18-bit A/D Converter는 Solid 96 dB Dynamic Range에 대하여 편입되어 있다. English 또는 Metric 또는 Decibel중에 원하는 단위를 선택할 수 있고, Amplitude 단위로는 RMS, Peak, Peak-Peak, 그리고 DC Meter Type들과 Linear, Exponential, RMS, 그리고 Peak-hold averaging의 Average Type이 있다.
주파수의 단위로는 Hertz, CPM, Orders, 10 Orders가 있어 이들 중에 선택을 할 수가 있고, Window의 종류로는 Hanning, Hamming, Kaiser-Bessel, Flat Top, Rectangular Windows가 있다. 그리고 앞의 특징에서 언급된 Spectrum기능은 단순한 Spectrum이 아닌 하나의 Spectrum을 취득하여 어느 특정 주파수를 확대하여 볼 수도 있을 뿐만 아니라 Amplitude Cursor, Frequency Cursor, Dual Cursor (Amplitude & Frequency, Band RSS Frequency, Delta Frequency, Mag), Harmonic Cursor (Frequency, Set Machine Speed), Sideband Cursor들을 이용하여 Spectrum을 정밀하게 기계에서 발생된 진동 신호를 분석할 수 있도록 하고 Spectrum이 화면에 있는 상태로 간단히 Soft Key를 눌러 그 Spectrum에 대한Time Waveform으로 변경하여 또한 여러 가지 기능들을 이용하여 진단에 필요한 정보를 얻어낼 수 있고 이러한 화면들을 Screen Capture 기능을 이용하여 Printer로 출력할 수가 있다.
True-Zoom Measurement기능을 선택하게 되면 dataPAC™1500은 마치 Spectra를 확대한 것 같은 Graphic이 나타내지만, 실제로는 사용자가 특정하게 설정한 주파수 범위에 초점을 맞추어 최대한 상세하게 많은 Data를 취득하여 나타냄으로 일반적인 Spectrum Graphic보다는 훨씬 많은 Spectra가 나타나 있음으로 하여 알 수 없었던 주파수의 Signal을 찾을 수 있다.
Coastdown/Startup기능에는 FFT/Waterfall과 Bode/Nyquist 그리고 Speed Profile의 기능이 있다.
이 밖에도 많은 응용 기능들이 있어 진동 진단 전문가가 보다 정확하게 기계 고장 원인을 분석하고 진단하게 할 수 있도록 하며 dataPAC™1500 또한 dataline Series의 장비와 마찬가지로 EMONITOR for Window, EMONITOR Odyssey, ESHAPE for Window, MOTORMONITOR 등과 같은 여러 가지의 Software와 사용 가능하고 뿐만 아니라 EMONITOR Odyssey 온라인 Version과도 자유롭게 사용 가능하므로 하나의 Software로 온라인/휴대용 장비를 동시에 사용함으로 경제적인 활용을 극대화 할 수 있다.
9.3.3 TURBOTEST
EntekIRD사의 TURBOTEST는 Turbine Generator, Compressor, Large Transfer Pump, Reactor Coolant Pump 그리고 Boiler Feed Pump 등과 같은 Critical Machinery의 운전에 대한 유용성을 증가하고 안전에 관련한 갑작스러운 손실을 감소시키기 위한 가장 강력한 System중의 하나로 온라인 CMS System을 Portable로 변형한 것으로 온라인 System에서 사용할 수 있는 모든 기능을 그대로 활용할 수 있는 진단 전문가용이라고 할 수 있다.
강력한 Data Acquisition과 그 처리 방법은 진동 전문가가 필요로 하는 정보가 있을 때, 필수적인 기계 상태에 대한 정보를 책임지고 지원한다. Data Acquisition은 기계들에 관한 모든 측정 Point에서 동시에 이루어진다. 이 장비는 사용하기에 매우 용이하며, 대부분 기능은 사용자가 만든 Soft-Key를 통하여 접속할 수 있다.
(1) 특징
• TURBOTEST은 최대 64 Channel까지 모든 진동 Channel에 대하여 동시에 Data를 취득하고 감시할 수 있다.
• X-Window/Motif Graphical User Interface는 사용이 용이하며, 다양한 User Interface는 여러 범주의 User들을 수용 할 수 있는 기능이 있다.
System Unit은 VXI-based UNIX Computer HP9000 V743/100, HP-VXI Bus Data Acquisition Instrumentation 그리고 ENTEK IRD’s TURBOAnalyzer software 이들 세 가지 주요 성분으로 구성된다.
(2) 시스템 하드웨어 구성(SYSTEM HARDWARE ARCHITECTURE)
TURBOTEST System은 데이터의 습득에서부터 저장 및 데이터 처리, Network 등 일괄 시스템으로 한 개의 Cabinet에 집약되어 있는 진동 전문 장비이다.
TURBOTEST System이 도입하고 있는 VXI Bus는 현재 전세계적으로 널리 사용 도입되어 있는 장비로서, 향후 플랜트의 표준 장비로서 가치를 더 할 것이다.
(3) DATA ACQUISITION
TURBOTEST는 사용자의 용도 따라 하드웨어를 구성 할 수 있으며, 그 용도에 맞추어 데이터 습득을 일시에 받아 드릴 수 있는 멀티 플렉스 모드 또는 연속 모드 형식으로 기능을 다양화 할 수 있으며, System Software는 측정 설비나 측정 포인트에 제한이 없다.
1 ~ 64 Channel 범위에서 한 개의 블럭 또는 다중 Channel 블럭으로 어떠한 형태의 Channel 구성이 가능하며 데이터 습득에 있어 연속적인 방법이나, 동기/비동기 형식으로 데이터 습득이 가능하다.
측정 설비의 특성을 고려하지 않고 일괄하여 조정함으로서 생기는 폐단을 제거 할 수 있는 블럭 구성은 측정 설비들의 특성에 맞게 데이터 측정 간격을 블록에 따라 조정 설정함으로서 데이터의 효율성을 한층 높일 수 있다.
TURBOTEST System은 다양한 진동뿐만 아니라 온도, 압력 등 다양한 Parameter들에 대한 데이터 Collecting 및 처리가 가능 한데 특히 Static과 Dynamic Data Collection, Transient Data Collection은 아래와 같다.
• Static Data Collection
Turbotest System은 전체의 Band 또는 어느 임의의 Sub-Band Vector Filtered Magnitude [(N × X) : N은 기계의 Running Speed (X)의 배수이다.], Vector Filtered Phase (N Phase), Overall or Filtered Signal에 대한 RMS Value, Signal에 대한 Gap Voltage 또는 Offset Voltage, Direct Phase 또는 rpm Inputs, Time Waveform 또는 FFT Conditioning 된 Signal부터 이끌어진 rpm, 그리고 Orders 또는 Frequencies Harmonics의 어느 임의의 Range에 대한 Harmonic Sum과 같은 Static Data에 대한 취득이 가능하다.
• Dynamic Data Collection
Turbotest System은 Time Waveform, Spectrum, Cascaded Spectrum, Orbits, XY, Polar / Vector Acceptance Region, 그리고 Shaft Centerline등과 같은 Dynamic Data에 대한 취득이 가능하다.
• Transient Data Collection
Bode (N × X) Plot, NX Phase/Amplitude 그리고 Shaft Centerline에 대한 정보가 포함된 Polar Plot, Cascaded Spectrum, X vs. Y, Waterfall Spectrum그리고 Tabular List와 같은 Transient Data 취득을 할 수 있다.
(4) SIGNAL PROCESSING
습득한 데이터 즉, Signal은 다음과 같은 기능에 의해 처리될 수 있으므로 다양한 형태의 데이터로 나타낸다.
• Math Functions
Mathematics 기능으로는 FFT, Transfer Function, Integration, Double Integration /Differentiation, DC Blocking, Addition, Subtraction, Multiplication 그리고 Division등과 같은 기능을 이용할 수 있다.
• Trigonometric Functions
Trigonometrics 기능으로는 Sine, Cosine, Tangent기능을 이용할 수 있다.
• Logarithmic Functions
Logarithmic 기능으로 Natural Log와 Base 10 Log 기능을 이용할 수 있다.
• Exponential Functions
Exponential 기능으로는 Exponent 및 Square Root가 있다.
• Statistical Functions
Statistical 기능으로는 Minimum, Maximum, Sum, Average, Median, Variance 그리고 Standard Deviation등과 같은 것들이 있다.
• Curve Fitting Functions
Curve Fitting 기능으로는 First to Third Order Polynomials이라는 기능을 활용할 수가 있다.
• Filtering
Filters 종류는 Low Pass, High Pass, Band Pass and Band Stop Filter가 있으며, 이들 Filter들은 FFT와 Time Format으로 적용 할 수 있다.
• Data Plot Formats
Data Plot Format에는 Digital Meter, Analog Meter, Bar Chart, XY, Trend (User Configurable Duration), Spectra (Synchronous 또는 Asynchronous, 28 ~ 7360 line까지 설정 가능), Time Trace, Polar, Orbit (N×X), Cascaded Spectrum, Current Value, Tabular List, Acceptance Region (사용자가 정의한 상태에 관한 어느 임의의 수)
(5) GRAPHICAL USER INTERFACE (GUI)
GUI는 X-window Compliant DCS, Control Systems, Windows and Windows 95 PC’s, HP-UX, Unix Workstations 등을 포함하여 다른 System과 같이 사용이 가능하다.
(6) REMOTE ACCESS
Software의 별도 추가 없이 원격 Network 또는 전화 모뎀을 통하여 원격 Processing (Control)이 가능하다.
9.3.4 Software
진동 Software의 등장은 진동 분석기에 비해서는 무척 짧은 역사를 가지고 있지만 현장에서 많은 회전 기계들을 효율적이고 효과적으로 관리하기 위해서는 진동 Software의 탄생은 불가피 하게 되었다. 예전에는 Hardware가 주가 되어 개발 발전되면 Software는 이를 뒷받침하는 종의 역할을 하여 왔는데 최근 몇 년 전 Window 체계가 확산되면서 Window의 편리함에 Computer의 사용 인구가 급격히 증가하면서 이제는 누구나 쉽게 Computer를 접하게 되고 그리고 각종 Software를 개발하는 회사들은 앞을 다투어 더욱 쉽게 사용하면서 더욱 더 많은 정보를 제공하도록 함으로써 향 후 어디가 끝이 될지를 아무도 모르는 지금은 Software를 잘 만드는 것이 관건이 되고 있다.
이러한 추세에 따라 진동 및 PM에 관련한 Software의 개발도 매우 빠른 속도로 발전하여 왔으나, Hardware를 보면 10년 전이나, 5년 전이나 지금이나 그렇게 크게 변한 것이 없다. 단지 Battery/전자 부품의 경량화 및 축소화에 따라 장비들이 과거 보다 가볍고 크기가 작아졌으며, 반도체의 발전으로 Data처리 속도가 빠르고 Data 저장 용량이 약간 커졌다는 것이고 그 이외에는 10년 전 Transducer, Cable 등등 거의 변화된 것이 없다고 해도 과언이 아니다.
그러나 최근 진동 Software의 동향을 보면 하나의 Software로 모든 PM과 관련한 각종 진동Data, Oil Data, Thermal Image Data, Temperature와 같은 Process Data 등등의 것과 같은 Parameter들을 통합 관리하려고 하고 있고, 현재 이러한 통합 관리가 가능한 Software가 생산되기 시작했고, Version을 향상시키려 많은 인력을 투입하여 회사의 운명을 Software에 걸고 경쟁사와의 승부를 하고 있다. 과거에는 온라인 Software와 휴대 장비 전용의 Software와 별개로 사용하고 판매를 하여 왔는데 98년 하반기부터 판매되는 EntekIRD사의 EMONITOR Odyssey라는 Software는 이것조차도 구분이 없이 약간의 비용만 추가하면 휴대 장비용 Software를 구매하여 사용하다 온라인 겸용의 용도로 사용할 수가 있도록 개발되어 시장에 나왔다. 그리고 더 나아가 앞으로는 User가 기존에 타사의 Data Collector를 가지고 있고, 현장에 있는 진동 감시 체계가 타사의 것이라 해도 약간의 비용만 더 추가하여 일부 Hardware를 교체하고 Software만 구입을 하면 적은 비용으로 플랜트를 Computer로 완전히 관리할 수 있게 된다. 지금은 Computer의 용량이 허락해 준다면, 온라인과 Data Collector를 사용하여 어느 한 임의의 플랜트의 진동을 관리한다면 On-line으로 할 수 없는 수백에서 수 천, 그 이상 Point까지도 얼마든지 관리가 가능하다. 이제는 한가지 정보만을 가지고 고장 및 예방 진단 정비를 하는 것이 아니라 모든 것이 통합 집약적인 정보를 이용 관리하는 것이 오늘날의 추세를 감안한다면 EntekIRD사의 EMONITOR Software는 이러한 요구를 충족 시켜 주는 Software라 할 수 있다. 편리하고 경제적이면서도 사용하기에 매우 편리한 그리고 빠른 진동 신호 처리 장비들이 매년 시장에 나옴으로써 이제는 거의 실제 일어나는 신호를 처리하여 이를 Software에서 Data화하여 User에게 제공하게 되었다. 기계를 분석하고 진단하는데 과거보다 훨씬 짧은 시간이 소요되며, 또한 요즈음 통신의 발달로 인해 모든 업무에 있어 시간/공간을 초월 할 수 있도록 WAN, LAN등의 방법을 통해 모든 Data를 주고받을 수 있는 것은 기본이 되었다.
EntekIRD사는 이러한 점을 예전에 파악을 하여 많은 인원/자본을 Software개발에 투자하고 PM에 관련한 모든 Data를 한 Software에서 관리하는 통합 관리 체계를 위해 힘을 쏟고 있으며, EntekIRD사는 이미 Microsoft사에서 개발한 Window 98의 운용 체계와 연계하여 사용할 수 있는 EMONITOR Odyssey라는 Software를 개발하여 얼마 전에 시장에 나왔고, Millennium BUG 문제에 대해서는 이미 2년 전부터 준비를 하여 오래된 Model을 제외하고 모든 Model에 대하여 해결이 되어 있다.
EntekIRD사의 Software로는 EMONITOR Odyssey, EMONITOR Odyssey On-line Version, EMONITOR for Window Series, ESHAPE for Windows, MOTORMONITOR, Explore-EX, Turbomonitor (이 Software의 기본 운용 Software가 UNIX X-Window로 사용되나 Window NT, Window 95이상에서도 사용 가능함.)등이 있으며, Single User 방식에서 Multi-User, LAN, WAN등의 방식으로 Up Grade가 가능하다.
앞에서 언급한 여러 가지 Software들 중에서 EMONITOR Odyssey에 대하여 그 특징과 가능을 기술하고자 한다.
(1) 특징
• 휴대용 Data Collector, On-line Surveillance 감시 체계 그리고 Continuous Protection 감시 체계(American Petroleum Institute, API 670)로부터 부분, 요소의Data를 완전히 통합 관리하는 완벽한 기계 상태 감시 체계이다.
• 진동 Data, Oil 분석 Data, Thermal Image, 그리고 다른 Condition Monitoring과 Process Data를 하나의 공통 Database로 통합할 수 있다.
• Open Architecture, Client/Server에 근거한 방식은 효과적인 Plant-Wide Communication-Single User, LAN(Local Area Network), WAN(Wide Area Network)에 대하여 완벽한 Networking 기능을 지원한다.
• 완전한 Window 체계로 설계됨으로 Plant IT Infrastructure로 용이하게 통합될 수 있고, DCS(Distributed Control System)과 CMMS(Computerized Maintenance Management System)로 고 부가의 기계 상태 정보를 지원할 수 있다.
• EMONITOR Odyssey는 Database를 설정하기에 빠르고, 쉬운 방법을 지원한다.
(2) 기능
• Window 95, Window 98 그리고 Window NT 4.0 체제하의 32-Bit Model에서 실행하는 EMONITOR Odyssey는 Button, Menu 그리고 Icon으로 모든 전체의 Window와 User Interface하는 특징을 갖는다. EMONITOR Odyssey는 Single-User, LAN, 그리고 EAN 구성에 대하여 SQL Client/Server Architecture를 사용하고, 대부분 플랜트 Information System에 대하여 충분히 능력을 갖추기 위하여 Multiple-Server 지원(ORACLE7™, Centura SQL Base™, SYBASE System 10™)을 제공한다.
EMONITOR Odyssey는 사용자를 위하여 미리 Formating된 Database View, Plot 그리고 Report에 대하여 Pane과 Window를 Modify할 수 있도록 User에게 그 방법을 개방해 놓았다. EMONITOR Odyssey는 다른 플랜트 Information System과 충분한 접속을 위하여 MIMOSA File 입력 그리고 출력 기능을 지원한다.
• Database 기능 :
EMONITOR Odyssey는 보다 효과적인 Database 관리를 위하여 다양한 Condition Monitoring 기술들로부터 Data를 통합한다. EMONITOR Odyssey는 사용자가 명명하는 Hierarchy Level을 6단계까지 지원하며, Icon과 중요한 Indicator로 이 Hierarchy를 나타낸다.
• Data Collection 기능
– 휴대용 장비 (Portable Instrument) : 일간 운용 업무는 Load/Unload Icon을 사용함에 있어 도식적인 유도에 따라 진행 할 수 있고, 수집된 Data로부터 자동적으로 Report가 작성될 수 있는 기능이 있다. EMONITOR Odyssey는 대부분의 다른 주요 제작사의 장비들뿐만 아니라 EntekIRD사의 모든 휴대용 장비들을 지원한다.
– 온라인 감시 설비 (On-Line Monitoring System) : EMONITOR Odyssey On-line은 자동적인 Data Collection 기능을 지원한다. Data Acquisition은 User의 간섭 없이 짜여진 Program에 따라 자동적으로 이루어진다. Manual Acquire Function은 사용자가 어느 임의의 시간에 Data Acquisition을 할 수 있도록 제공한다.
• List 기능 :
EMONITOR Odyssey List기능은 최적의 Data Collection, Plotting 그리고 Reporting을 하기 위한 강력한 도구이다. EMONITOR Odyssey는 Database로부터 Hierarchy View 또는 Automatic Selection에 상호 작용하는 Tagging을 통하여 List를 설정한다. Alarm Severity에 의한 선정은 분석 과 추적을 위해 보다 중요한 List를 지원할 수 있다.
• Plotting 기능 :
EMONITOR Odyssey Plot들은 기계 상태에 대한 분석을 위하여 가장 완벽한 기능으로 진동 진단 및 관리자에게 지원을 할 것이다. 이들 Plot들의 기능은 확장 가능하고 상호 작용하는 다음과 같은 기능들로 Plot을 조종할 수 있다.
– Rubber Band Zoom – Grids
– Auto Scaling – Linear 또는 Log X Scaling
– Multiple Cursor Types – Linear, Log, 또는 Decibel Y Scaling
• Report 기능 :
포괄적인 Report는 신속하고 효과적인 기계들에 대한 정보이다. EMONITOR Odyssey는 30가지의 표준 Report 뿐만 아니라 사용자 Report Generator를 지원한다. 요구되는 Data에 대한 Plot은 기계 상태에 대한 완벽한 도식들에 관하여 EMONITOR Odyssey Report에 삽입할 수 있게 될 것이다.